Production systems engineering in future digital factories
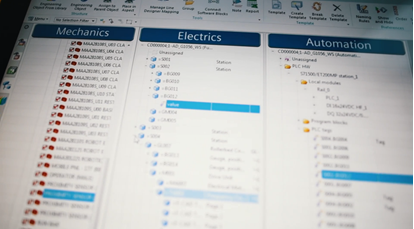
By: Wolfgang Schloegl and Christian Heck
We’re now at a similar turning point like we were in 2000 when the first digital factory projects began. Now, the full potential of digitalization is within reach through a digital twin that’s not only a planning tool, but acts as the master for the production in terms of efficient engineering, optimization, safeguards and predictability.
All of this comes together in production systems engineering, which integrates all involved domains – planning, mechatronics engineering, simulation, and validation – into one holistic concept. Production systems engineering can provide you with answers to the actual values and benefits of a factory design, and it provides use cases and workflows, data-modeling and tools that can be used to bring production scenarios to life throughout the plant’s lifecycle.
The concept of a production’s holistic digital twin is not simply done with implementing new software tools. It can also adopt the planning and engineering workflows, and it can change them according to the possibilities a mechatronics digital twin can offer when it’s always up-to-date.
The digital twin, with its mechatronics contents, serves as the master for change management between the engineering domains. It can be used for detailed virtual commissioning studies, not only before the start-of-production, but also during production to execute studies or test the integration of factory expansions.
Finally, it can become the master for factory execution when all decisions are based on foresighted analysis validated in the digital twin.
Siemens is in a unique position to complete the digital smart factory. We can provide an always-updated digital twin of the production for a plant’s planning, engineering and optimization – not only for the planning phase, but throughout the plant’s entire lifecycle.
Siemens has massively invested in this new era of digital planning in production systems engineering. We want to provide a foundation that will unleash the full potential of digitalizing a factory, integrating existing technologies for production planning and simulation with newly developed methodologies and technologies. This allows you to build a complete digital representation of production, along with the sophisticated methodologies and tools to use it.
Siemens is supporting digital factory enhancement so it becomes mechatronic to include the needed mechanical, electrical and automation data to serve all relevant engineering domains. This also includes functionalities for reusable mechatronic elements libraries containing proven solutions of customers-specific standards including their know-how.
Based on the mechatronics data model, new possibilities arise for automated engineering and automating once-manual engineering tasks, which would help manufacturers see faster, higher quality results based on their specific production standards. This can happen because the systems contain mechanisms to interpret connections of all reusable elements and to automatically generate the needed engineering results, for example, in terms of wiring diagrams or fully functional PLC code, to create fully automated engineering.
Siemens offers authoring tools for all major planning, engineering and simulation tasks, and these tools can integrate into a suite with change management and one common data backbone. The changes made in one tool are available for all partner’s work, regardless of whether they work in the planning, engineering or simulation department. The same information is available for all of them because there are synchronization and notification mechanisms between the digital models stored in the single data-backbone.
Production systems engineering is not only about data and tools, but is also about new ways of working and interacting with the partners in a project. It enables all users to fulfill their work based on up-to-date data, the workflows don’t have gaps in data, and the benefits of digital engineering can be gained by every domain, in every point in time, in a factory’s or machine’s lifecycle.
With these capabilities, the digital factory will no longer be outdated when production begins: this data will be the basis for the smart factory of the future. New smart factories will be built according to new guidelines and standards stemming from Industry 4.0 or the Internet of Things. These new factories will need this kind of foundation to serve as the planning and optimization backbone during their lifecycle.
This concludes our introduction to production systems engineering.
About the authors
Dr. Wolfgang Schloegl leads the Digital Engineering department in the Siemens Digital Factory division and is amongst others responsible for the software Automation Designer. He also works on providing integrated solutions of Siemens PLM Software with Siemens automation systems. He has been with Siemens since 2003 and previously worked in planning and digital manufacturing for automotive production. Wolfgang was formerly with Daimler in Sindelfingen, Germany, where he worked on knowledge management for production planning, and later, in project management for assembly planning. He studied production engineering at the University of Erlangen-Nuremberg in Germany, where he earned his doctorate in the area of simulation for discrete production.
Christian Heck is a Production Systems Engineering Solution Manager for Siemens PLM Software, a business unit of Siemens Digital Factory Division. He has more than 14 years of experience in automation engineering and commissioning, as well as developing cloud-based industry applications. Heck gained much of his experience working for Siemens Oil and Gas Offshore in Norway, where he worked as System Responsible for several major oil and gas projects. His previous experience with Siemens includes leading a Service Line for optimizing production plant performance based on data analytics applications. Heck holds a Bachelor of Science degree in automation engineering from the University of Cooperative Education in Karlsruhe, Germany.