Additive manufacturing technology transforms product development
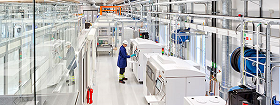
Imagine you head the aircraft intermediate maintenance department and are responsible for the readiness of jet fighter planes on a United States Navy aircraft carrier in the Indian Ocean. Your ship’s commanding officer needs to send an F-18 on a critical mission, but the F-18 needs a part.
If you have adopted additive manufacturing technology, and have a 3D printer and the appropriate materials onboard, your supplier can send a digital file and you can print the part.
But how can you be sure the file data is authentic and reliable?
That is one of the topics James Regenor, director of transformative technologies for Moog Inc., and a retired colonel in the United State Air Force, explored in his presentation on additive manufacturing at the recent Digital Twin Summit at the Digital Manufacturing and Design Innovation Institute (DMDII) in Chicago, Illinois.
Moog is a global firm that uses Siemens PLM Software solutions to design, manufacture and integrate precision control components and systems. It produced the gimbaled thrust system for the Mars lander, and worked on the X-47B unmanned combat air vehicle. Moog is also active in NASCAR.
Additive manufacturing technology is changing the way products are made. New machines and processes are swiftly moving additive manufacturing from creating prototypes to the production floor. Manufacturers are producing innovative designs that were impossible to make using traditional methods. Additive production methods can provide many benefits, including weight savings, superior performance, simplified assemblies and more material options.
Some of Regenor’s other observations included:
• Additive manufacturing technology enables more digital, more connected and leaner workflows. In the future, it will focus on increasing speed, developing in situ inspections and reducing postprocessing.
• It is important for companies to create an environment in which they can monetize intellectual property many times, sell digital supply items and leverage second- and third-order effects. Digital supply chains are the future.
• In the additive manufacturing space, one new technology by itself can provide a linear growth curve for your company. However, when you are able to converge technologies you can potentially create an exponential growth curve. It is important to look at multiple technologies around the additive space.
• You can create an environment in which you’re able to buy and sell digital supply items and the customer has the option of where and when he or she converts them to a physical item. This enables you to drive the nonvalue-added steps out of the supply chain. You don’t have to maintain a warehouse and inventory because you can make it when you need it. You don’t have to pay for all the things in between the end points, such as deliveries and customs charges. As a result, this takes the margin pressure off of you and the cost pressure off the customer.
We hope you enjoy this video on additive manufacturing technology.
In upcoming summit talks, you will learn about the synergies that exist between the automotive and aerospace industries and how digital twin technology weaves them together with the digital thread; autonomous/electrification issues from the perspective of an automotive and aerospace customer as well as an industry thought leader, and next-generation/additive manufacturing issues from the perspective of an automotive customer as well as an industry thought leader. You will also be able to watch a 45-minute question-and-answer (Q&A) session with the speakers. Keep an eye on this blog in the coming weeks as we provide links to them.
About the author
Indrakanti “Chaks” Chakravarthy is the Marketing Programs Director working in the Americas zone at Siemens PLM Software, where he is responsible for marketing programs covering the aerospace, defense, federal and marine industries. Chaks has spent the last 30 years working for a number of companies in presales technical, sales and marketing areas of the PLM portfolio in India, Japan and the United States. He has a mechanical engineering degree from Jawaharlal Nehru Technological University in India.
VIDEO TRANSCRIPT
TOM MAURER: OK. Continuing on our manufacturing journey, we have Colonel James Regenor, director of additive manufacturing, innovation and – I forgot the other one; additive manufacturing, innovation; I thought we’re very cool! So, colonel.
JAMES REGENOR: Thank you, thank you. Up to about a few minutes ago, I didn’t know exactly how I was going to put all this together and what I was going to talk about, so you guys got to bear with me a little bit. I’ll bring it all together at the end so you’ll be able to see clearly what the vision is.
A little bit about myself and a little bit about MOOG. I just changed my duty title; I’m the director of transformative technologies, and that’ll be important as we talk about some of these things today.
We talked earlier today about the Mars Lander. The gimbal thrusters on there were made by MOOG, so when you only have one shot at a landing, you want to make sure we do the parts for you.
There was talk about the UAS landing on the carrier. The X47, we made the flight controls for that, so when you’re going to land on that same spot, it’s because we made the flight controls that put you there.
When they show the video of the NASCAR garage, there was a MOOG logo in there. We do NASCAR, Formula One type of parts, too.
We are a company [with] $2.6 billion annually in sales, $1.1 billion in aircraft. Out of that, that’s the group I work in. We’re in 28 countries and 100 locations. We have about 11,000 employees, 4,000 of them are engineers; I’m not an engineer, I’m a geographer. So you understand when we start getting really technical how I stay at the very high level, and I’ll stay out of that.
I want to talk to you today a little bit about additive, and I think Hersh, you set this up perfectly for me today because what you created in your blood distribution network, was you created a point of use, time of need distribution network, right?
You start thinking, is that possible in the industrial space? Can you create a point of use, time of need supply chain? What then would be the enablers for that type of thing? These are kind of the questions we started asking ourselves at MOOG as we started getting into additive manufacturing.
This was a 3D printed part that we make – very complex part – but you cannot make this on a CNC machine. We started thinking as we bought an additive business in Livonia, out of New York, in the Detroit area – what could we use additive for?
What we found pretty quickly was, any one of these new technologies by themselves is kind of a linear type of growth curve. When you can have a convergence of technologies – in our case, we’re going to talk about additive and Blockchain and then platform-based business models – when you can get a convergence of technologies, you can then get an exponential growth curve. That’s what we’re after: exponential growth curves.
The ability to buy and sell IP [intellectual property], think of it as IP, and to remunerate and monetize IP multiple times – if you’re a sub-tier supplier, it’s available on this platformed network, and that’s pretty exciting.
Think of Netflix for aircraft parts, or an Amazon for aircraft parts. How do you make that happen? How do you create an environment so that you sell digital supply items to the customer, and the customer decides where he can convert that digital supply then into a physical item?
So we’re looking at technologies around our additive space, the future. We’re using artificial intelligence for melt pool monitoring to look at whether or not we’ve got a good part so we don’t have to CT scan every part that comes off. We’re using blended reality. Some of our design features, we’re using additive manufacturing. We’re using Blockchain for providence, which I’ll talk about here, to create that supply chain. On top of that, we’ve built a business model around a platform-based business.
So you could sell – at MOOG, we could sell an actuator to Lufthansa in Frankfurt and they have a plane broken in Auckland, New Zealand, and they want to send that digital file down to Auckland. They can send it down there. They can print the part Auckland and then put it on the airplane.
Here you have additive manufacturing, facilitated with this distribution network that you can send something, somewhere where it needs to be made. How do you do that?
Well, we started thinking that at MOOG, when we bought the additive manufacturing business, what are the second and third order effects that’ll be caused by additive manufacturing? Additive manufacturing, from our perspective, was going to be rapidly commoditized if you made bowling trophies. If you made high-end precision parts like we make: not going to be commoditized, but a chasm would exist between those two regions.
What we decided was, let’s focus on the left-hand side. As the standards come out, that’ll deepen the chasm. The folks on the right-hand side are making bowling trophies and bobbleheads. There’ll be a business for them, but they won’t need the standards, they won’t need the repeatability, they won’t need the control processes that are going to be required for aircraft actuation.
We started to kind of examine this. What we did was we use a tool called Scenario-Based Planning. We came up with some scenarios, and out of those scenarios, we did this left-to-right methodology to decide where we had gaps in our domain expertise.
The first scenario we did in November 2015 was, you’re on an aircraft carrier in the Indian Ocean and the sea state level 3. You’ve got an F-18. It has to fly a critical mission. You’ve got a 3D printer onboard. How do you send a file out to the aircraft carrier so they can print the part, look at it, know that it’s a real part, that there’s data integrity and nobody’s messed with the file? It’s the part that’s supposed to be there.
Then, you can look at the part providence – the pedigree of the part, so to speak – and see that it was made according to the design specifications.
We looked at a couple of different methods. We finally settled on Blockchain. Who here’s familiar with Blockchain? Trading cryptocurrency, or any of that stuff? Blockchain’s the foundation to Bitcoin and all these other things you hear about. It’s up 2, by the way; it was down 400 this morning, if you got and if you’re in it like I am – I was nervous. Feeling a little bit better after lunch!
How do you put that trust in? What we did is, we kind of started on the carrier, and we look backwards. We said, what do we need? Blockchain then became the solution, and we needed the additive manufacturing.
We came up this scenario, we came up with Blockchain. Then we started really kind of peeling that back. We said hey, what does that really give us? Because the reality was, it gave us more than just being able to send a part out there: it allowed us to start thinking in terms of what will the advances of additive manufacturing do? What can we look in the forward? Where are the other convergences for additive manufacturing?
From our perspective, the things that will change in additive, the future additive, will be things we’ll be able to make faster. There’ll be multi-laser machines. There’ll be production rates that will increase, and you’ll be able to get to these automotive type of production rates that don’t exist today. We think that’s inevitable.
The other thing is, you need to be able to do is in situ inspection. You need to be able to pull a part off a machine and realize that the part is good. You can’t CT scan every single part. That process is going to get better. That’s the future.
How can you do that?
I flew airplanes in the Air Force for 25 years. I flew KC-135, which is as old as the B-52. I never flew a plane that was built after I was born.
But everything that happens inside the fence at an airfield happens based on trust. When I walk out to an airplane, I open up the forms. There’s a 781 in there. I look and see that’s signed, and if it’s signed, I don’t open panels and look and verify the inspections. It’s trust. I know that guy did what he said he did because he signed the paper.
How can I stand on the aircraft carrier, look backwards into my supply chain and go, how do I have trust?
The other is, you need to reduce the amount of post-processing required for metal additive manufacturing, because right now, there’s quite a bit of post-processing. To think that you have a point of use, time of need supply chain, that’s good; but there’s still – you can take it off the printer and stuff to do some post. If you’re working in polymers, you can take off the printer and put it right to work. You don’t have to worry about post-processing, necessarily.
In the metal world, those are the things where the future is.
If you want to look at who’s kind of moving in the future, MOOG is moving in the future. From our perspective, that’s what the changes are, that are going to take place.
What do those changes facilitate? Well, if you can go back to what the supply chain may look like in a digital space, you now create an environment that if you’re able to buy and sell digital supply items, and the customer has the option of where he converts them to a physical item, you can drive the non-value-added steps out of supply chain.
You don’t have to maintain a warehouse. You don’t have to maintain inventory, because you can make it when you need it. You don’t have to pay for customs brokerages. You don’t have to pay for all the other things in between the end points, from where you drop it off in the dock to where the customer picks it up on his dock. You can you can eliminate a good portion of that.
Obviously, then you take margin pressure off of me, cost pressure off the customer, and create an environment that then will facilitate what Hersh is doing; it’s now the blood for the aircraft, or whatever industry.
What do you do with Blockchain, and what do you get with Blockchain? In our case, we have a patent pending on a process called Veripart. We can take our part back to this trust scenario. That artisan on the airplane can take our part, can scan it with his phone and it’ll light up say, yep, that’s a MOOG part. Then he can swipe through his phone, like you do on a lot of apps, to the left, and it’ll show every single transaction that’s happened to that part.
It doesn’t stop when he puts it on the airplane. He can now put that on the airplane, and through the full lifecycle when it goes off wing, comes back for MRO – that’s for Randy – when it comes back for MRO [maintenance, repair and overhaul], it still is living in that Blockchain, all the way through condemnation.
The previous speaker talked about traceability: there’s your traceability. From our perspective, it gives you a couple things. Counterfeit mitigation.
Additive manufacturing lends itself to the ability for somebody to replicate a part, and we make a distinction between a replication and a copy. A replica is a scan to print type of setup. I’ve got parts that I can put on a scanner, CT scan it right into a computer and print it. In fact, we’re so good at it. I did a cover on F-15; it had a little bit of a scratch on it. When I scanned it and printed it, the scratch showed up on the printed part.
Now, all of a sudden, you’re the artisan, you’re pulling something off the shelf on the ship and you’re going, well how do I know what’s real? I scan it, and it says hey, this is not a MOOG part. Or I scan two parts that have the same number, because people say well they’ll just print your number.
Two numbers is what’s called a byzantine spent. You pull it out, we have a way to tell which is ours. We have a patent-pending way that we fingerprint the part at the grain structure to be able to tell you which is a good part, which one’s not. Each part’s got kind of its own unique fingerprint.
Now you’re able to do that. You can do counterfeit mitigations. You can do the full traceability that I showed you as we just went through. Then you can do kind of a track, so you can keep track of where that part is in inventory.
Well then that lends yourself to think, well if I can track parts in and out of inventory, do I need an ERP [enterprise resource planning] system?
Nobody’s going to get their ERP system because they have it today. You’ve spent money on it, but if you’re a new company, do you need ERP? I don’t know, but if you’re using Blockchain, you might not. If you’re using additive manufacturing in the process we talked about, you may be able to cover yourself with the processes.
Where are those convergences leading us to? I mentioned before, you’ve got to get to an area where you can, inside the machine when the part comes out, decide that you’ve got a good build.
The future, when we look at additive manufacturing, is those convergences. Those are where MOOG is focused, where we think the exponential growth curves are and those are the areas that I think will kind of lend themselves to that next iteration in additive manufacturing.
Additive manufacturing has been around since 1987. We’ve been doing it at MOOG. We acquired a company that started in 2003 doing metal. We’ve done 100,000 plus parts.
The thing that’s missing is an accelerant to the FAA for aircraft parts, and that accelerant is the process we talked about today. We’re going to create a platform-based business that will allow people to exchange IP – in our case, the IP initially on it.
If you think of iTunes, the back catalog that we’re building is material properties: A-basis, B-basis S-basis data.
Right now, when the FAA approves a part, it’s a point approval. They approve that part. We want families of parts. The way to get families that parts approved is to have data available.
We’re developing data for an alloy right now; it cost us a $1.5 million to do that data. We can’t do the 20 or 30 alloys that are prominent in the aviation business at $1.5 million each: we need somebody to help pay for it.
We’ve brought on two partners, in our case, two competitors. We’re developing the data. We’re going to offer that data up on the platform for others through a subscription or license to be able to access that. That platform then will seed other people to do the same thing. We’ve created a three-sided platform: consumers, producers and the service provider.
If you’re just a guy who wants to print, you would work the service provider. If you want to up convert to 2D paper to 3D models, you could do that. If you’re a consumer, you could produce IP. You can make PMA [parts manufacturer approval] parts, put them up there and sell them. We created that platform environment.
The last step to this platform, and the last thing that you need, is you need a distributed network. You need a system that MOOG can print a MOOG part on a Siemens machine, and I can extend my liability and warranty because Siemens is in this certified network that we’ve created standards for.
Siemens has got the printer in Auckland, and I’m going to send, or Lufthansa’s going to send, to that printer there. You say, hey MOOG, I’m sending it to one of your network printers, it’s a Siemens printer. I’m like, yeah, cool, Siemens is in the network. We’ll extend the warranty liability.
Let’s say there’s not one there, and Lufthansa calls me up and says hey, we’re going to send your part to Auckland. There’s nobody down there in your network; we’re going to print the part. I go, it’s all yours. I’m not going to extend the warranty or anything.
In the follow on state, you create an environment that allows you to remunerate IP. You create an environment that allows you to sell digital supply items. Then you create, finally, that network that allows you to do that point of use, time of need digital supply chain.
That’s where I think the future is. The future is more than just the machine: it’s how you can use the second, third order effects and what that network and that ecosystem has created.