Manufacturing smart products without smart people?
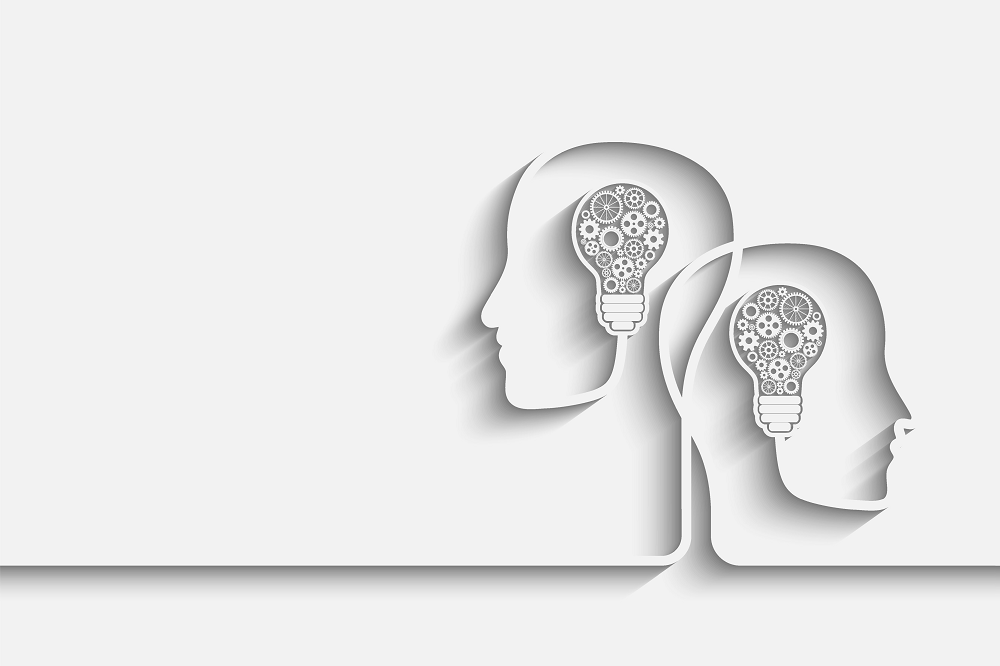
By: Josh Ray and Alex Allison
Everyone wants to be on teams that break new ground, like the teams at Zipline, a company that builds pilotless aircraft that are used to deliver vital supplies, such as medicine, to locations that previously were inaccessible. Zipline’s founders say its business model requires modern technology that enables them to design and build the drones with limited resources, which keeps costs down so buyers, such as the country of Rwanda, can afford them.
Choosing the right technology is a key part of breaking new ground like this, not only for the capabilities the technology provides, but also for efficiency and speed of process. Innovation has complicated manufacturing jobs, but it also has made manufacturing one of the most exciting places to work.
Unfortunately, not enough people agree.
Manufacturing continues to suffer from a worker shortage. Producing the same amount of goods today takes a lot fewer people than it did 20 years ago, but manufacturers still struggle to find enough people just to fill current demand, let alone build a pipeline of future leaders.
A big part of the problem is a need to reverse perception that manufacturing is dirty and antiquated. According to a Deloitte Insights Report:
“(Highly advanced operations) typically are characterized by work cells composed of numerous computer-controlled, but operator-managed, machines and robots where one worker ensures that software, hardware, tooling, and materials all work together and to detailed specifications. Unfortunately, many young people do not recognize this evolution. As a result, manufacturing has an image problem that further exacerbates the skills gap.”
The world is full of highly advanced manufacturers making innovative products, but not all manufacturers are as innovative as they could be. A big barrier holding back innovation is a need to invest in modern manufacturing technology.
For instance, these things must happen for a manufacturer to take advantage of all that the Internet of Things (IoT) offers in terms of product and service development, as well as process innovation:
• Software engineers must be able to collaborate with electrical engineers and also with mechanical systems designers.
• Production planners need to collaborate with product designers to ensure cost-effective manufacturability and capacity planning for those new products.
• Customers need to be able to send specifications and orders in their preferred file formats without friction or delays.
• On the shop floor, product data must merge with machine data for digital simulation of processes, automated (robotic) production, analytics-driven process control—and finally—into a data feedback loop within the connected processes so adjustments can be made quickly to iterate and improve.
In the most modern and innovative manufacturing plants, unified software platforms enable digital representation of what’s happening in the physical world using a digital twin. Everyone can reference the most up-to-date data simultaneously, as well as test the impact of proposed changes to manufacturing in a low-cost, low-risk environment—an essential capability for ongoing innovation.
On the plant floor, the digital and the physical worlds are colliding as machinery, mobile devices and web-based interfaces are starting to talk to one another in real time through the IoT. Connectivity is seamless, so much of what used to be done manually is now automated in “lights-out” factories. Operators are using software to move materials, assemble products and even test for quality.
Essentially, the digitalization of products and processes provides every professional the knowledge they need to be innovative; that is, make fast decisions in daily work, as well as improve on and add to existing product knowledge.
This is impossible to do when product information is analog, disconnected and missing.
When the next generation of workers are considering new workplaces, they will be looking for three important outcomes of the technology they will have access to:
• Will I have the capabilities to contribute to new ideas, and will I be able to innovate?
• Does it create a stable, scalable and reliable system on which we can create and build on new ideas?
• Is the technology intuitive and easy to use?
Assess your technology based on these questions, and then ask, “Where can we as manufacturers improve within our technology ecosystem to become more innovative and, thus, more attractive to the future generation of leaders?”
This concludes part two of our series on the future of manufacturing. In part three, we discuss how to choose technology for building innovative culture.
About the authors
Josh Ray is an account development executive for Siemens PLM Software. He began his career in the manufacturing software organization. Josh is passionate about people and technology, and his current role is to support business development in the industrial machinery and medical device industries. Josh works with companies to increase awareness and adoption of technologies across their innovation and product lifecycle. He regularly engages with C-level executives in this role, which inspires his drive to gain a deeper understanding of industry trends and the obstacles companies currently face.
Alex Allison is an account orchestrator with Siemens PLM Software and has been with the company since 2013. In his current role, he is responsible for maintaining relationships with electronics and high-tech companies on the Eastern seaboard. Alex began his career in the semiconductor industry, specializing in manufacturing systems. He has experience around OCM, managing complex enterprise system architecture, and ensuring customers have the right solutions and processes that will result in transformational efficiencies throughout their business.