Large-scale additive manufacturing benefits for industrial OEMs
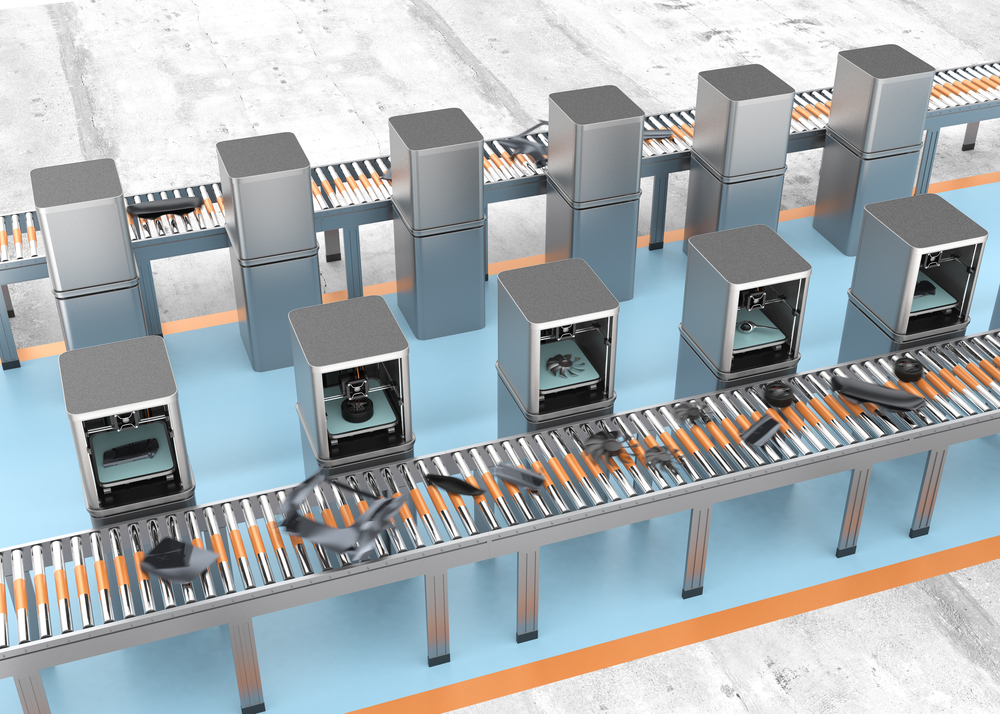
Companies and individual inventors have done amazing things with 3D printing. But what’s not happening is large-scale production of high-quality industrial parts used in machinery, automobiles and complex aircraft systems.
In many ways, this is the Holy Grail of 3D printing. It flips the normal production model from a subtractive effort—batches of raw material broken down or formed into parts—into an entirely digital additive effort, where engineered material is precisely layered according to specifications to create parts with less wasted materials and without specialized tools or molds.
Additive manufacturing (AM) is a more innovative, digitally driven method that can be used to create unique product features and operate at a faster, more agile pace; and as demand for large-volume industrials parts grow, the affordability of AM will decline.
According to the BCG report Get Ready for Industrialized Additive Manufacturing, “AM enables manufacturers to digitize the entire production process—down to the level of powder particles. Indeed, AM technologies are critical to realizing the vision of the factory of the future, in which manufacturers improve production by applying new design principles, implementing digital technologies, and integrating processes across the value chain.”
The advantages of additive manufacturing sound great, but the reality is that industrial manufacturers have been slow to expand AM beyond rapid prototyping and small-scale production in “projects” rather than everyday production.
A 2017 survey by printing services provider Sculpteo found that 67 percent of 3D printers are being used for prototyping, proof of concept and to make marketing samples; and, the two business functions most likely to use 3D printing are R&D and product design.
A new way to start or expand additive manufacturing
Lots of factors have held back large-scale AM parts production, but a major obstacle is lack of access to the quickly evolving knowledge and techniques in the marketplace.
This is entirely new territory for manufacturers, who are reluctant to make big investments without assurances that they will be able to control processes for quality, compliance and profitability—as they currently do with subtractive methods.
However, a new service from Siemens—the first of its kind in the AM marketplace—can make it easier and safer for industrial manufacturers to start or expand large-scale manufacturing of parts alongside their current processes. It connects the cumulative knowledge, tools and services in the AM value chain with each other and with parts buyers.
The Siemens Additive Manufacturing Network is a cloud-based platform that brings together:
• Part buyers (industrial OEMs) that want to adopt AM as a mainstream production method
• Print service bureaus that serve customers who want limited AM production, functional prototypes or serial parts production
• AM machine OEMs that are industry leaders who have knowledge and want to share it with the wider AM ecosystem while promoting their technology
• App developers that have innovative software ideas and want access to the wider market to execute with partners
• Engineering and consulting professionals who are offering their expertise in design for additive, production and quality management, business case development and other needs
• Material providers that want to promote and sell their advanced materials and process IP
The major unique thing about starting or expanding AM through the Siemens AMN compared with other ways is that participants can build knowledge together through a private network as they experiment with evolving AM technology, new materials and new part types.
This can happen as they use platform tools to actually execute the required transactions to try new vendors, processes and ideas, and have these transactions be traceable and transparent.
3 additive manufacturing use cases for industrial OEMs
Large-scale AM production is not an all-or-nothing endeavor. Additive and subtractive manufacturing can exist together. When manufacturers have access to vetted vendors and trusted partners, they can rely on vendors and partners to identify the best use cases for AM within their product portfolios.
Here are three ways industrial manufacturers could benefit from using AM.
Design for additive manufacturing (DfAM): Increasing the number of parts specifically designed for AM could yield differentiating product features, such as lightness, energy savings, temperature resistance or tensile strength, as well as overall high quality. AM also makes it affordable to produce personalized products, which—as with any higher quality product—can command higher prices.
Scaling production: For companies that already have some AM of parts and/or prototypes in place, the SMN can make the move to larger-scale production easier. Tools to manage orders, print jobs and monitor machines provide transparency. Additionally, product-related data is transmitted in a consistent, traceable manner among a private group. This reduces the risk of valuable intellectual property being copied.
Replacing physical inventories with digital inventories: AM can be used for fast, on-demand spare parts production. With an ecosystem of vetted partners in place, an order can be placed from one side of the world to have the parts printed on the other side of the world near their point of use. This could eliminate inventory-associated costs and shipping costs. It would also increase flexibility through global access to AM suppliers, and it removes the need for time-consuming, expensive vendor vetting and supplier certifications.
The major unique thing about starting or expanding AM through the Siemens AMN compared with other ways is that participants can build knowledge together through a private network as they experiment with evolving AM technology, new materials and new part types.
The platform facilitates interaction among members. It also enables providers to deliver and promote their proprietary knowledge, tools and services via APIs, applications, reports, research and a host of other methods.
For industrial manufacturers, this ecosystem can be ground zero for their new AM efforts. A good place manufacturers to start is considering the three use cases and ask, “Which of these aligns with our strategic goals as a company?”
This concludes part two of our series about large-scale additive manufacturing and the role the Siemens Additive Manufacturing Network will play in helping make these large-scale processes a reality. In part three, we discuss how the protection of IP plays a part in high-volume AM production.
About the author
Robert Meshel is the director of the Siemens’ Additive Manufacturing Network initiative, a new online collaborative platform designed to accelerate the use of additive manufacturing in the global manufacturing industry. This initiative was born under his previous role, as the director of strategy for the manufacturing engineering software unit. Driven by the passion for technology and business innovation, Robert is relentlessly pursuing new strategic opportunities developed within the organization or by external partners that are seeking to mark a significant impact of the future of humanity. Prior to that Robert, was the cofounder and the CEO of Synvertech, a technological startup that addresses major hurdles in mass adoption of renewable energy. He was also the vice president of business development at ETV Energy, a technological startup that develops novel Li-ion battery cells for the transportation market. Robert earned a bachelor’s degree in mechanical engineering from the Tel-Aviv University and an Executive MBA from the Kellogg- Recanati International program. He is also a graduate of the Singularity University executive program.