IP protection in high-volume printed parts production
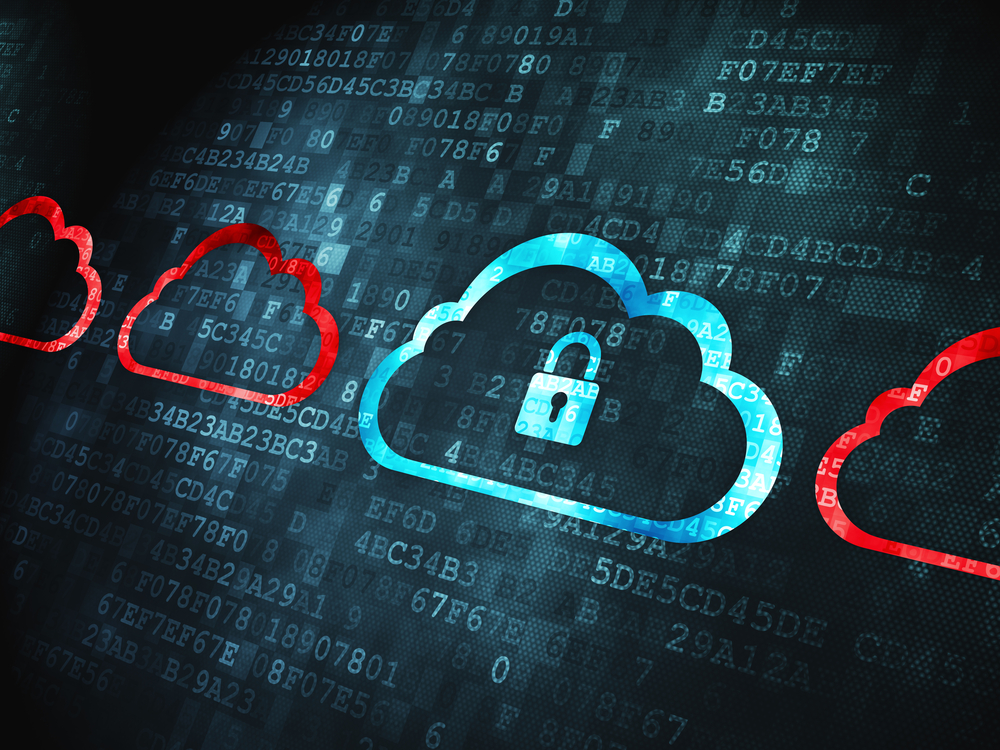
In any description of the factory of the future or Industry 4.0, data is the most valuable asset.
Materials shortages and mechanical failures used to be the biggest threats to fulfilling demand, but those have now been surpassed by missing or inaccurate data. Nothing happens in a modern supply chain or factory without information, and this has led to continued efforts to democratize data through digitalization.
At the same time, digitalization and digitization have made private information more vulnerable, and this includes vital intellectual property (IP) for manufacturers in highly competitive sectors such as aerospace, automotive and machinery/equipment.
Hackers that target services companies usually want customer data: at industrial companies, they want the trade secrets. In 2017, Manufacturing Business Technology indicated that 1 in 5 manufacturers reported a loss of IP from a cyberattack.
Protecting IP is on many manufacturing leaders’ minds as their companies consider adopting new or expanded digital capabilities, and as their markets evolve and respond to technology-driven changes.
The role of data in large-scale additive manufacturing
Specialized printed parts is one way industrial manufacturers are using new digital capabilities to become more competitive. GE Aviation, BMW and Siemens all use additive manufacturing (AM) to produce unique, differentiated parts for a limited number of engines, car bodies and turbines.
However, demand for large-volume printed parts beyond these, and a few other early programs, is rare in industrial manufacturing.
The biggest barrier holding back demand is a lack of access to a collective democratized data; that is, access to publically available information on the marketplace of providers as well as proven business models. AM at this scale is nothing like traditional manufacturing, and only a handful of companies have resources that allow them to tolerate risks and apply knowledge as needed to design and execute an entirely new production model.
The aforementioned pioneering companies had to start from scratch; this is not possible for most manufacturers. Yet, the very antidote to low demand is for producers to learn by doing, as AM leaders have done.
Siemens studied this dilemma and has introduced a platform-based AM service in which industrial manufacturers can work with AM service providers to identify opportunities, build business cases and connect with providers in a transparent, private network.
The Siemens Additive Manufacturing Network addresses both sides of the data/knowledge balance in modernized, digitally driven production. The platform aims to collect data and convert it to a consumable knowledge.
At the same time, participants—parts buyers as well as product and service providers—can also protect 3D printer design files and machines and materials IP.
• Knowledge sharing: The cloud-based platform supports an AM ecosystem in which parts buyers, printing service bureaus, equipment and materials suppliers, apps developers, and engineers and consultants can connect with one another and share knowledge as they work together to plan order-to-delivery models. As demand for printed parts grows, the knowledge base within the network grows, thus paving the way for more demand.
• Securing IP: Large-volume AM requires sharing digital files outside of a company’s protected systems, often with many entities, in different locations and among multiple devices. Securing IP in those files is paramount, and app developers are responding with new tools.
For example, in the Siemens AMN ecosystem, Identify3D technology provides a secure digital container to move and modify data through the digital workflow. The Identify3D Protect applications create the secure container, while Identify3D Manage enables distribution and licensing policies to be created for data usage within the container. These agreements and the data usage are transparent and traceable within the platform, which provides additive manufacturing security tools for all participants, whether they are buyers or vendors.
Stepping into the factory of the future with confidence
How soon will large-volume AM production be a regular part of everyday manufacturing?
BCG and others estimate that it could be at least a decade away, and even then, it will be a relatively small part of overall parts production. But if companies want to advance their operations, as well as their products, now is the time to start learning and experimenting with AM parts production.
Digitalization has been disrupting PLM for decades, and manufacturers have benefited. For instance, digital twins have eliminated the need for physical simulations in many cases. Manufacturers benefit from faster and less expensive product development, and they can either recover those costs or reinvest the new capacity in expanded R&D.
AM is an important part of this beneficial disruption of PLM. It’s a natural extension of value derived from Industry 4.0 technologies, such as the Internet of Things and intelligent process automation.
For manufacturers ready to try or expand their AM efforts, the first decision is where to start, and that takes knowledge.
The best source for that knowledge right now is the AM industry, and that’s why Siemens is bringing practitioners to manufacturers through the Additive Manufacturing Network. With knowledgeable experts to help, it’s a platform that enables industrial producers to take a step forward into the factory of the future with confidence.
This concludes our introduction to large-scale additive manufacturing.
About the author
Robert Meshel is the director of the Siemens’ Additive Manufacturing Network initiative, a new online collaborative platform designed to accelerate the use of additive manufacturing in the global manufacturing industry. This initiative was born under his previous role, as the director of strategy for the manufacturing engineering software unit. Driven by the passion for technology and business innovation, Robert is relentlessly pursuing new strategic opportunities developed within the organization or by external partners that are seeking to mark a significant impact of the future of humanity. Prior to that Robert, was the cofounder and the CEO of Synvertech, a technological startup that addresses major hurdles in mass adoption of renewable energy. He was also the vice president of business development at ETV Energy, a technological startup that develops novel Li-ion battery cells for the transportation market. Robert earned a bachelor’s degree in mechanical engineering from the Tel-Aviv University and an Executive MBA from the Kellogg- Recanati International program. He is also a graduate of the Singularity University executive program.