How MES manufacturing can advance medical device technology
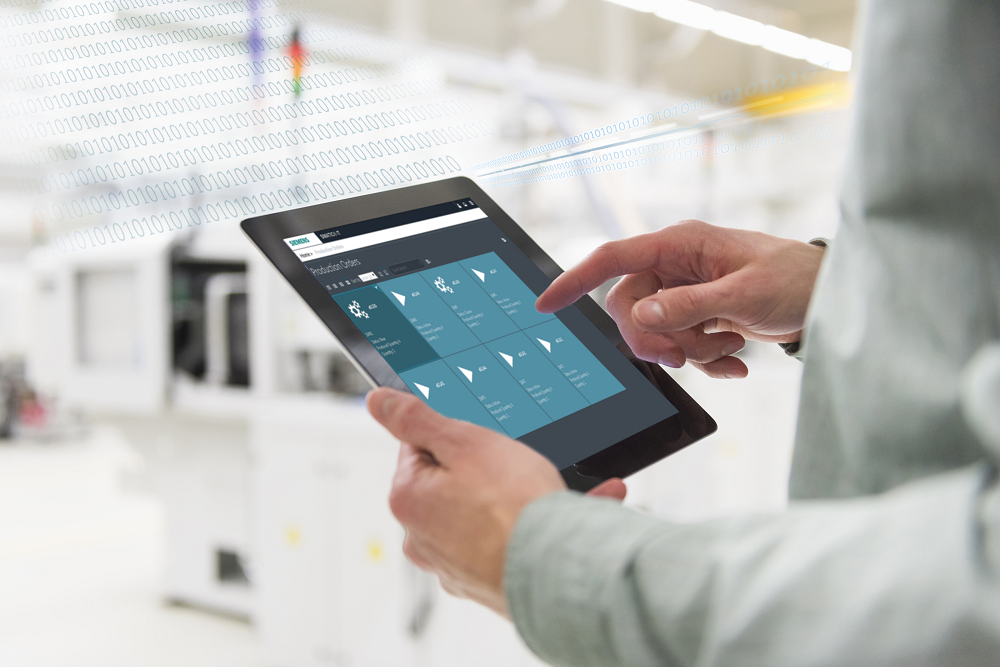
In June 2009, Belgian soccer player Anthony Van Loo’s heart stopped in the middle of a match. He collapsed immediately.
In a matter of seconds, thanks to an implanted defibrillator, his body literally jolted back to life and his heart started beating again. He was taken to the hospital after his collapse and resuscitation, and checked out fine. He continued playing soccer for another nine years.
“The miraculous part is that it works so fast, that there is no damage to the brain or any other organs,” said Professor Pedro Brugada, cardiologist and head of the Heart Rhythm Management Centre at University Hospital in Brussels.
As cutting edge as Micro Systems Engineering Inc. (MSEI) was in medical technology, the company still used paper-based manufacturing processes that kept it from growing. To become more competitive, innovative and churn out life-saving products faster, they transitioned from paper-based processes to a comprehensive, digitalized manufacturing execution system (MES).
Defining MES manufacturing
On its basic level, MES tracks production on the shop floor. After a part is designed and specified, production is scheduled. The MES manages the steps of the production process, informs operators, validates business rules and records all actions in an audit trail. This ensures a product is built consistently as designed.
The MES guides operators through a series of steps to perform, handles any non-conformances, accepts data collected from a number of sources to be linked to steps of the process, and verifies that the correct materials, tools, and equipment are used at each step. Operators are receiving better instructions leading to less stress as they work with automation.
Manufacturers can then better prevent errors by ensuring data is properly collected and is within acceptable values, verify equipment maintenance has been performed and validate employee training.
MES’s importance is realized in the medical device industry where new product introductions must be quick, growth is critical and innovation is key.
Consider that a new consumables part is introduced every 15 hours in the medical device industry, and the typical lifespan of a part is less than two years before it is updated or obsolete. On top of that, thousands of engineering change orders are processed annually. Batch records, which detail descriptions of processes, can commonly exceed six inches of paper per day, literally reaching miles of paperwork per product.
People like Van Loo depend on lifesaving equipment to work at the exact point it’s needed or risk organ failure, brain damage or death. Implementing an MES in the medical industry means data flows back and forth with other systems seamlessly and with greater traceability, leading to fewer defects, more rapid and accurate safety recall notices, better performance and more innovation delivered faster – all at a lower price.
Van Loo was diagnosed with a heart condition in 2008 and had been outfitted with a BIOTRONIK implantable defibrillator, a product of MSEI.
“They (defibrillators) are invisible, but they’re working 24/7, and they have to run and be reliable for years,” says Juergen Lindner, general manager of MSEI.
With each iteration and new product in development having increased complexity, MSEI found focusing more on automation, integration and digital data exchange allowed employees to complete more with greater accuracy and better implementation. Before costly, physical prototypes are created, companies like MSEI have the ability to answer “what-if” questions in the virtual environment before committing to physical iterations.
It’s easy to assume that the businesses employing MES solutions are the ones receiving the benefit of its use, but benefits reach far beyond that for people who rely on their devices every day, and all day, to keep them alive.
Employing MES for medical device technology
“The pace of change is so fast; you can’t grow by just adding people,” said Tom Rosso, vice president of global consumables operations at Illumina.
Medical device manufacturers like San Diego-based Illumina discovered they couldn’t grow without implementing a strategy that allowed for the level of rapid integration, growth and quality they required.
Illumina’s processes required endless coding and testing. As a result, product transfer times were high and they needed a massive amount of people to keep it running. They even struggled with automation finding it challenging to integrate data as they developed and manufactured their products.
Integration is a key part of digitalization, but there are plenty of challenges that come with implementation. With different systems come different developers, data structures, terminology and domains. Here are four challenges that frequently arise.
1. Coming up with one size fits all. You should have a configurable system that provides a single supported software platform to be used in virtually infinite situations. Fulfilling unique customer requirements might involve extending the system.
2. Implementation might take a lot of silos having to come together. Bringing in all the teams at once can feel overwhelming. Gradually bringing in teams might be a slower transition, but can often help find where bugs are in the system and issues can be managed easier. Companies can use new technology while the technology itself is under observation and refinement. It has the advantage of constantly being updated in an actual manufacturing environment.
3. Hooking everything up is more challenging than it seems. Integration between the shop floor and the MES is key to realizing maximum value. The equipment communicates with MES, which does not permit transactions to occur until the floor equipment is ready to proceed. Tight integration between MES and other software and systems, such as manufacturing operations management, product lifecycle management and enterprise resource planning, must be set up for interoperability.
4. Shortage of qualified labor. Without a qualified workforce, manufacturing with minimum resources might delay full implementation. Companies must consider better automation and MES to combat the current skills gap.
Regardless of the challenges of manufacturing with MES, there are plenty of benefits that minimize costs and increase efficiency.
• Smaller lot sizes with virtually infinite combinations possible. Increasing automation between shop floor and MES can support smaller lot sizes, improve quality and reduce labor costs.
• Faster feedback from the shop floor to stakeholders. When production problems occur, engineering support is available faster decreasing time-to-market and allowing more frequent new product introduction.
• Greater level of traceability. In regulated industries, it is necessary to have full traceability throughout the supply chain and manufacturing process. A full history of every operation, tool, employee, and specification used is accurately time stamped and maintained.
MES adoption will be critical for businesses in competitive industries. Along with faster time-to-market and shortened concept to production timelines, MES manufacturing brings more standardized interfaces and exchange formats across products and the supply chain. Unlike software integration today, which tends to exist as separate products, a well-integrated suite of MES software will be able to merge and function as a single product.