How is collaborative manufacturing transforming agriculture?
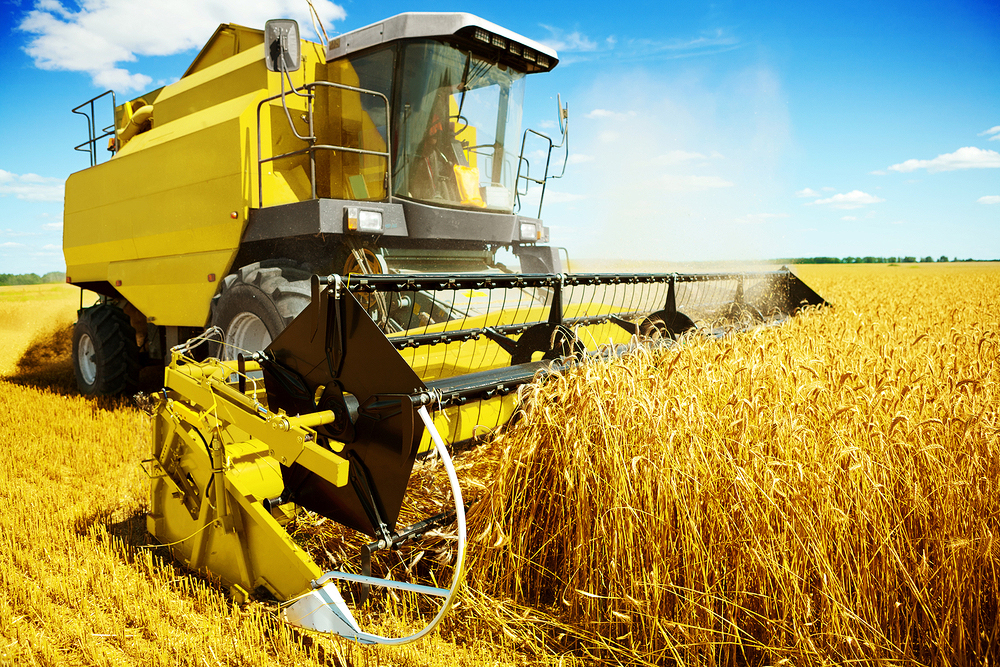
Efficient farming is a global necessity. Billions of people around the world already depend on fresh produce—and the numbers keep growing.
The world’s population will swell to 9.1 billion by 2050, and it’s estimated that food production will need to increase by 70 percent to feed everyone.
But heavy equipment manufacturers face many challenges that could impact their ability to meet global agricultural needs. This includes rising material costs related to numerous global economic factors, including tariffs on steel on aluminum. Pricing pressures impact both large and small agricultural equipment producers.
For example, Shield Agricultural Equipment will have to pay 25 percent more on certain products the Hutchinson, Kansas, company imports from Canada and elsewhere. And Caterpillar will raise prices to offset a $100 million – $200 million increase in tariff-related material costs in the second half.
Fortunately, manufacturers can still meet modern crop production demands using collaborative manufacturing tools. A movement toward collaborative manufacturing is helping agricultural equipment manufacturers bring highly automated, intelligent farm equipment to market without increasing labor or lead times.
Often referred to as “precision farming,” high-tech agricultural equipment can help farmers improve yields and efficiencies. For example, some equipment manufacturers, such as John Deere, are building machines with sensing and GPS technologies that help farmers determine the appropriate number of seeds or nutrients to disperse over a given area with a higher level of accuracy.
According to a Deloitte report, technologies such as the Internet of Things could boost agricultural productivity by 70 percent by 2050.
Collaboration holds the key to precision farming
Agricultural equipment manufacturer AGCO Corp. is another example of a company that’s transforming crop production with high-tech solutions. The Netherlands-based company has developed a number of intelligent features for its crop sprayers to reduce operator fatigue, improve application accuracy and increase productivity.
AGCO designed automated and cab-controlled adjustments to accommodate for varying field terrain and crop heights. The company also developed sprayers that can travel 19 miles per hour and boom arms of up to 118 feet to operate across vast fields.
These advancements would not have been possible without collaborative manufacturing. Collaborative manufacturing eliminates data silos that typically exist across organizations. It allows them to bring products to market faster using sensor-generated data that can be fed into digital product and process twins.
Build consistent designs from anywhere
One of the key attributes of collaborative manufacturing is the ability to easily replicate design changes across multiple plant locations without discrepancies between the engineering bill of materials and the manufacturing bill of materials.
AGCO wanted the ability to respond faster to market needs from any location. The company has plants throughout the world and distributes products in more than 140 countries. AGCO couldn’t have achieved its “design anywhere, build anywhere” strategy without the help of collaborative engineering and manufacturing.
In this environment, the engineers across the organization share and reuse data on a common global platform. The company can react quickly to changes in the market because it can plan real-world processes quickly using the digital twin.
“In the case of design anywhere, build anywhere, all of our new product introductions are going to be platform-oriented and will reuse data,” says Gary D’Souza, manufacturing engineering lead of global manufacturing PLM at AGCO. “In our design engineering, we’re trying to standardize the part numbers and the designs of parts so we can reuse them from platform to platform, from module to module, and from region to region.”
This type of consistent data and design information gives agricultural equipment manufacturers the knowledge and flexibility they need to make precision farming a reality even in an uncertain economic climate. As the global population continues to grow and raw material costs increase, collaborative manufacturing will become an essential strategy in the effort to increase crop quality and yields.
This concludes our series on collaborative manufacturing.
About the author
Rahul Garg is the vice president for industrial machinery and heavy equipment industry at Siemens PLM Software, responsible for global business development. He and his team are responsible for identifying and delivering strategic initiatives and developing solutions for the industry, working closely with industry-leading customers and providing thought leadership on new, emerging issues facing the machinery industry. Rahul’s experience and insights are derived from a 25 year career of delivering software-based solutions for product engineering and manufacturing innovation for the global manufacturing industry. He has held leadership positions in multiple areas, including research and development, program management, sales and P&L management, having focused exclusively on the industrial machinery and heavy equipment industry since 2007.