Address obsolete parts production with the digital twin
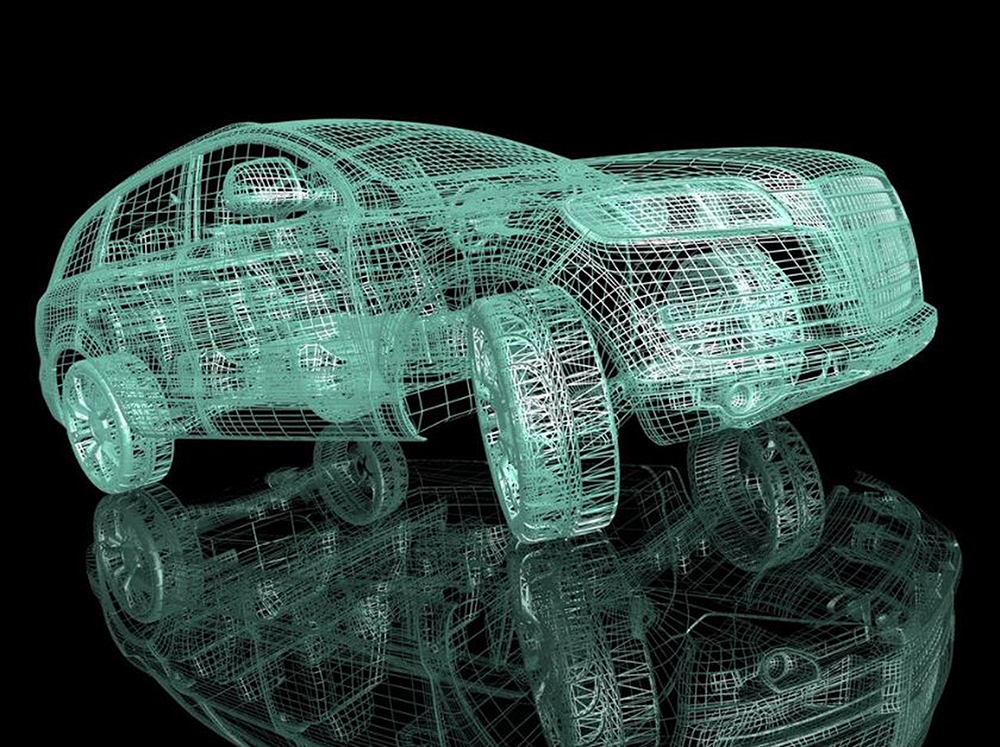
There’s more to a manufactured part than what’s visible. Every component contains a wealth of historical information about its design and the manufacturing processes that went into creating the part. Unfortunately, much of that information gets lost when organizations sell a product, end its production or when workers retire.
The problem becomes more apparent when demand increases for once-obsolete parts or products. Think about all the changes happening in the auto industry. An average of 3,000 or more parts per car model will become obsolete each year.
What happens when car enthusiasts want to bring an old Chevy truck back to life? Once mass production stops, parts become hard to find or manufacturers must stockpile inventory, which results in higher costs for obsolete parts. This is known as a “long-tail problem.”
So how do you address the long-tail for mass-produced obsolete parts? 3D scanning serves as insurance for manufacturing tooling and design data, so manufacturers can create a digital twin of that antique or obsolete part and make it available when needed.
Securing spare parts: A digital insurance policy
3D scanners provide manufacturers with the ability to make digital copies of parts to ensure they have backups of qualified tooling surfaces. This means they can bring old products back to life for new revenue opportunities or quickly reproduce quality parts when a component fails. The aftermarket auto industry is just one of many examples of ways manufacturers can use 3D scanning to reintroduce old product lines. The ability to make a digital copy of a tool before shelving it for retirement allows manufacturers to reintroduce the product faster than competitors.
Advancements to 3D scanning software are also helping manufacturers quickly verify product compliance. For instance, the aerospace and defense industry must address frequent regulatory changes, which can create challenges for products that have been in existence for decades. Think about Boeing’s B-52 bombers built between 1952 and 1962; 76 of them remain in active service.
Each time a regulatory change occurs, parts must be recertified. Modern 3D scanning software helps streamline the verification process. For instance, advanced 3D scanning software allows designers to create a trace link between a requirement and a product structure. This feature removes a great deal of complexity, time and potential errors from commonly practiced verification processes.
They also can correct quality issues with minimal downtime. For example, Siemens recently worked with a manufacturer that encountered a quality problem with an injection mold for a rubber gasket. The customer scanned the mold and came back with nominal dimensions to make a quality tool again.
The customer did this without any original records or drawings of the tool. In other words, the customer brought the tool back to life by scanning its surface and creating a digitized copy of it. Now, if the tool breaks again, the company can easily recreate it using the digital twin—avoiding costly downtime and responding to customer needs quickly.
Securing intellectual capital for future value
Another potential benefit of 3D scanning is the ability to preserve years of knowledge about products. Business strategies change over time, and the company may want to consider selling the product line. Or, the company may want to position itself as an acquisition target. If critical product information isn’t readily available or lost over time, the manufacturer may struggle to attract investors.
A digital scan can serve as a type of archive for intellectual capital. It provides potential suitors with confidence that they can manufacture the part with minimal guesswork or extensive design planning to begin production. 3D scanning software also helps manufacturers preserve the knowledge they often lose when experienced workers retire. New employees may require significant training to build an existing product, especially if it’s a complex design; but the digital twin provides new employees with the tools they need to build quality parts without extensive onboarding.
3D scanning and reverse engineering help manufacturers remain agile in an increasingly competitive market. Whether it’s resolving quality issues, resurrecting older product lines or securing tribal knowledge, the digital twin is already proving to be a game-changing technology for manufacturers’ peace of mind and competitive advantage.
This concludes our series on the key roles 3D scanning software can play in your business.
About the authors
Ryan Haylock is an NX design specialist on the Americas channel enablement team and is focused on assisting partners in learning, communicating, and demonstrating the Siemens PLM product suite. Prior to joining Siemens in 2007, Ryan held positions in the semiconductor capital equipment industry supporting corporate initiatives around design reuse & automation, commodity cost reduction, engineering process methodologies & tools, and business readiness. His experiences have helped him learn about the complexity of implementing corporate wide processes, executing against milestones and achieving bottom line results in complex machine design. Since joining Siemens a decade ago, he has continued to focus his efforts on helping customers achieve the value from our products and realize the true potential of PLM. Ryan has a bachelor’s in engineering from Michigan State University and is located in Michigan.
Chris Himburg is CAM Logic’s business development director for additive manufacturing and is a partner of Siemens PLM Software. His focus is on solving real-world manufacturing challenges by pushing 3D printing and 3D scanning technologies to their limits. After running a home theater and IT business, then committing to IT full-time, he followed his heart back to the engineering field where he has helped CAM Logic grow the additive manufacturing and 3D scanning portion of the business. He is a DIY enthusiast who enjoys tinkering and is excited about the future of the manufacturing industry. Chris is based in Michigan.