Quality parts on demand with additive manufacturing
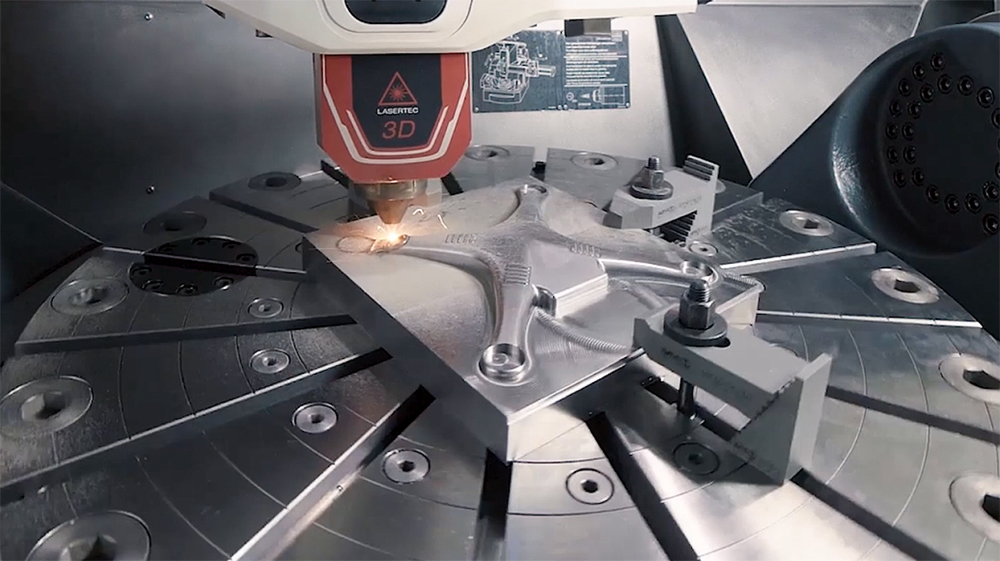
Is your company taking advantage of the many benefits of additive manufacturing to improve your system production and product quality to stay competitive?
Additive manufacturing (AM), also known as 3D printing, uses a process to create a three-dimensional part where layers of material are formed using numerous techniques and methods to create an object. Objects can be of almost any shape or geometry as defined in a 3D model.
Technology and expertise are necessary to bring all the pieces of your manufacturing workflow together for additive manufacturing. For example, design tools to optimize the geometry of each part might be necessary.
When designing a part for additive manufacturing, you need the ability to verify and simulate the print before committing to manufacturing the part. The medical industry is very familiar with this, being an early adopter of 3D printing to create medical devices such as replacement joints. As part of this process, designers rely on specialized tools for simulating the metal printing process. For example, printing a hip joint in titanium can take up to 32 hours; and if a problem occurs mid-way through your print job, it could cost up to $50K in wasted time and materials. Therefore, simulation before physically printing saves both time and money.
Simulation is the key to success with additive manufacturing
So what investment are you willing to make in using process simulation to improve your product?
Whatever your business size, from small to medium or at the higher-end enterprise level, the cost of simulation is always a consideration. However, process simulation can ensure you’re pushing the edge of technology to stay ahead of the game, ensuring you get the best bang-for-your-buck. So, it’s crucial to be willing to gather your brain trust and invest in the technological tools necessary to get ahead.
With process simulation, you can simulate the entire process—including all the parts in the print trays, support structures and even the thermal effects of residual powder in the tray. Also, you resolve problems before committing to the actual print process ‒ saving both time and money by minimizing errors. Using tools like these can help boost final product quality.
Printing unique parts on demand
Serious, real-world metal parts require premium quality, unlike the plastic prototype parts used in initial printing. A change in manufacturing standards requires companies to have connections to the broadest breadth of printing possible for many materials, including plastic and metal. New systems continually come on the market providing new methods and ways for users to print unique, one-of-a-kind parts on demand. Manufacturers need expert technical support to manage these new systems.
Industrialization of additive manufacturing requires the ability to:
• print securely to multiple printers with multiple materials,
• repeat that process possibly thousands of times over, and
• ensure consistent quality throughout the process.
To achieve these aggressive goals, manufacturers need to simulate every step of the printing process with a world-class CAD system and validation to deliver the total package.
This process can start at a minimal level. There are automotive companies in Germany experimenting with a combination approach by using both additive manufacturing and off-the-shelf software to create structurally sound pieces of a car frame. They may not be printing an entire car, but they are taking extruded hollow beams, like those used in traditional automobile manufacturing, and printing nodes to connect those beams together. These nodes also include a printed lattice structure on the interior to generate the required structural rigidity with little weight penalty. These nodes and beams are put through a series of physical impact tests for verification of the final structure. By starting small and focusing on an achievable goal, they’re printing durable, efficient parts that may change future automobile manufacturing.
Additive manufacturing ‒ its effect and potential to 3D printing
Additive manufacturing has the potential to disrupt business in most any industry. However, it also offers an enormous potential to create and expand new business opportunities. The result is the ability to create parts on demand and products that were inconceivable only a few years ago. Moreover, one can see how future manufacturing of these parts and products will be a comparable level of quality and quantity as traditional manufacturing.
According to Goldman Sachs, by 2025 additive manufacturing and 3D printing will have an estimated annual economic impact of $550 billion. Additive manufacturing will be a $140 billion market opportunity if it penetrates just 1 percent of the manufacturing market. Furthermore, ING says that 40 percent of trade could be wiped out by 2025 due to 3D printing at local manufacturing facilities.
These staggering figures should prompt every manufacturer to rethink their business model to increase personalization, offer on-demand printing, provide design/print anywhere and improve their overall competitiveness in their industry via additive manufacturing.
This concludes part one in a series on additive manufacturing and its impact on the manufacturing industry. Future articles in this series will forecast the future of additive manufacturing and its possible impact on other industries – where today meets tomorrow. In the meantime, please visit our additive manufacturing Thought Leadership hub.
About the author
Ashley Eckhoff has a background in engineering and has been with Siemens for over 20 years in various capacities. He has spent the past few years deep-diving into additive manufacturing in both product design and marketing roles.