Additive manufacturing processes – risks and opportunities
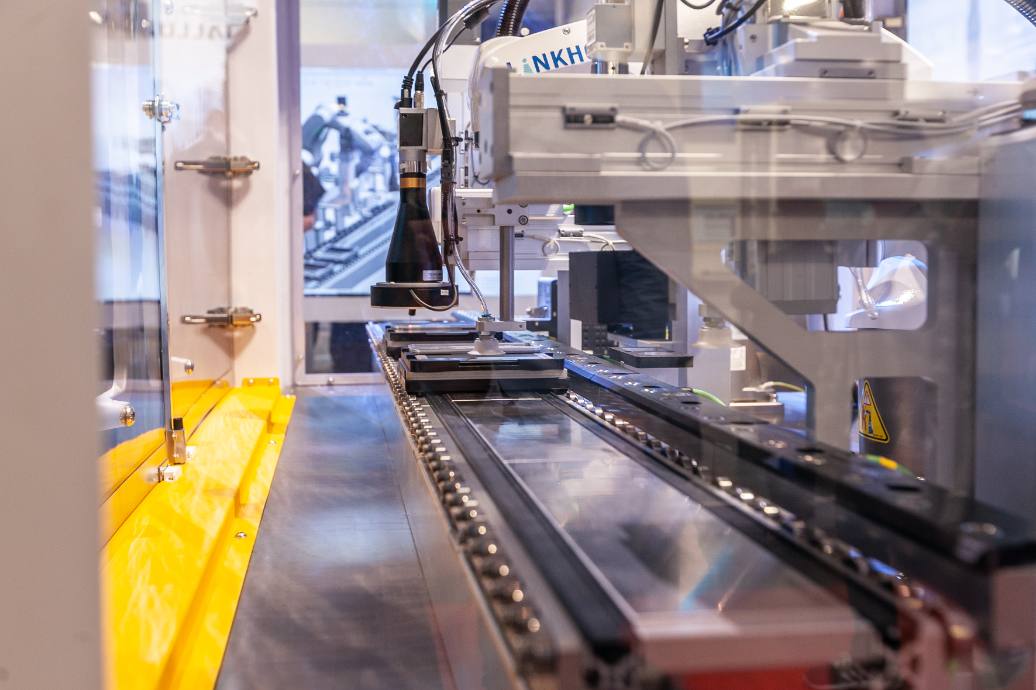
Industrial-scale additive manufacturing, also known as ISAM, brings both risks and opportunities. This growing technology will someday be a requirement for all manufacturers. Additive manufacturing has many benefits, with room for expansion. However, with its many rewards are also risks.
As a member of the Siemens PLM Thought Leadership team, it’s my privilege to reintroduce Robert Meshel, Siemens Director of the Additive Manufacturing Network Initiative, which is a new online collaborative platform designed to accelerate the use of additive manufacturing in the global manufacturing industry.
Here, we’ll address the opportunities and risks of additive manufacturing. To listen to the entire set of conversations via podcasts, you can follow us on Soundcloud, Stitcher and iTunes.
Dean Haehnel: What are the high-level opportunities with ISAM and where are organizations going to see its value?
Robert Meshel: There are multiple levels. First is the product. We can now reimagine new products that could not be produced with past standards of traditional manufacturing. These products incorporate both light-weighting and efficiency of parts, which are crucial elements to the aerospace industry.
For example, GE produces highly efficient parts for aircraft engines, with the ability to improve the engines’ efficiency by altering the parts and transitioning them into additive manufacturing production. With an improvement of only one percent in engine efficiency, this results in a substantial effect on the business value to GE and its engine operators.
There is also the ability to utilize new materials that were not previously available using previous manufacturing methods, for instance, printing human tissue or food.
At the industrial level, you can fully merge with new mechanical properties of metal production that is rapidly accelerating by using additive manufacturing.
We foresee a significant amount of changes in how products are designed and produced.
It is crucial to acclimate yourself to a strong market demand element via customization of parts. For several years we are seeing this trend of additive manufacturing accelerating individualization, producing part by part. Moreover, modification of one part to another does not promote more cost, versus the traditional manufacturing process of placing value on the standardization of parts. However, with additive manufacturing, you can reimagine anything for new parts with no risk of extra cost.
As we view the operations and efficiency of new parts and design, we see significant value for operators who no longer need to store large amounts of in-process materials. We can print specific parts on-demand, as required, with much less tooling than standard manufacturing.
Lastly, is the ability to produce and bring to market new iterations rapidly without adding to the cost associated with traditional manufacturing. In most cases, you design the product and then set up the manufacturing facility to support it. Then you promote this product to the market, and if a problem occurs, like the need to add an element, this requires rebuilding your manufacturing process to make several changes which could be costly to implement. The result is a product that is not modified.
With the additive manufacturing process, you can perform multiple iterations at no extra cost.
So, the products will be different; the process is different, your ability to go to market faster is unusual – with a very significant value that manufacturers are going to see.
Dean Haehnel: With the value-add of industrial manufacturing, why are industrial manufacturers not being proactive about implementing industrial-scale additive manufacturing?
Robert Meshel: One reason – lack of competency. To produce more products via additive manufacturing, you need to generate more demand for these kinds of products, meaning you need more experienced engineers capable of designing products for additive manufacturing. Moreover, additive manufacturing is not sufficiently available to the market. Even companies like Siemens and GE, who promote it vigorously to the market, have engineers involved only at a segregated level to specific business units versus having enough knowledge to spread throughout the organization.
Also, even companies that move beyond the point of specific areas of operation and understand the importance of additive manufacturing to the destiny of their company and process have questions as to whether they have the infrastructure to support a full-scale initiative.
Questions to ask:
- Who is going to be my supplier when other suppliers have not worked?
- What kind of materials?
- What kind of processes?
- What parts are going to be relevant for additive manufacturing?
A complete set of elements need consideration to proceed with the additive manufacturing processes, and this road is not entirely paved.
One crucial element is security. Because additive manufacturing is a digital process, there is a threat of an IP address security breach, leaving you open to vital information being stolen and used for production. Highly regulated industries like aerospace, medical and automotive are very cognizant about maintaining their IP, and specialized technologies need to address and aleve these concerns.
Another element is monitoring and tracking production, making it visible to areas outside of the core factory, where another associated tool production resides. Everything related to the product needs supervision. Providing competent support is vital to the success of additive manufacturing.
Lastly, in the goal to mature this technology, there are issues with cost, application quality and creating a repeatable process. All the players in additive manufacturing are diligently working to improve progress in these areas, and we are seeing improvement, with the plan to have these issues behind us in a few years.
Manufacturers cannot solve this problem by themselves. Moreover, not all manufacturers possess the abundant capacity and financial backing to address these concerns. Therefore, to harness this technology, we need the collaboration of knowledge-sharing to accelerate its advancement.
Dean Haehnel: In talking with several companies who have concerns about the rapid pace of change in the industry with 3D printing, including costs and printers becoming obsolete, is there a way to alleviate these worries?
Robert Meshel: This is typical of every new emerging domain where technology changes rapidly, like that of additive manufacturing. Begin by utilizing service bureaus because they have already made the investments in machinery and possess significant amounts of knowledge you can leverage. Also, they have associations with an extensive list of partners in software solutions, materials, engineering and consulting – already beginning the process and gathering knowledge. Leveraging their expertise, and their overall ecosystem is an excellent advantage for newcomers to the industry.
Also, there are machine companies that allow you to upgrade your machines. You can buy local machines for prototyping and start to experiment – it’s crucial to have immediate experience in additive manufacturing because it’s challenging to gain the knowledge required to master this domain.
Dean Haehnel: I hear there is a steep learning curve with this technology. How can a company gain the knowledge to produce additive parts at an industrial-scale without it taking years?
Robert Meshel: It would be the same steps I mentioned, above: to build partnerships via a complete ecosystem – leveraging the knowledge that exists. The problem with this domain is not a lack of knowledge but that this information is in silos and not accessible. This hinders the market from progressing more rapidly.
Leveraging the entire ecosystem significantly accelerates your ability in additive manufacturing to contribute to the ecosystem. This kind of business model of co-creating and collaborating fosters an elevation of the entire additive manufacturing industry.
Therefore, we are beginning to build our Additive Manufacturing Network Solutions for Siemens. We recognize the fact that if you want to accelerate the adoption of additive manufacturing, you need to ensure that knowledge is accessible to everyone – collecting experiences to deliver to everyone needing it.
You benefit newcomers to the market from those that gather experiences, which moves them through the learning curve more rapidly. However, this is also true for incumbent players like machine vendors, material vendors or software developers. Even they do not have all the information accessible to them; however, having a central place to collect data and share this knowledge internally to the ecosystem also provides value to accelerate additive manufacturing to the market.
Dean Haehnel: Earlier, you mentioned the Siemens’ Additive Manufacturing Network. What is that?
Robert Meshel: This is a new cloud-based solution we’re about to launch which connects the entire network of players within the additive manufacturing domain.
These players first include those who require parts and deliver them via internal or external service bureaus. This includes machine vendors who possess significant amounts of knowledge to upgrade their machines. Moreover, they need to learn if they can leverage the information available in the market to improve their machines and better their service to customers.
Secondly, it includes materials vendors who possess the know-how and the best method for delivering their material that is needed by the market and how to access that market easily – leveraging the network.
Thirdly, are organizations such as engineering and consulting, because we are seeing additive manufacturing processes leveraging the knowledge that exists from engineering firms. There is a need to facilitate the overall co-creation process that takes place between these manufacturers and the engineering entities.
Additive manufacturing processes
Lastly, it is for industry software solutions to have market access to ensure their solutions are fully integrated into the overall set of processes within additive manufacturing.
All these players in the industry need the ability to co-create, collaborate, build knowledge, build the IP and the tools necessary to deliver correctly for those who need it. This is the foundation of additive manufacturing and what it delivers: helping engineers to design for additive manufacturing (DfAM) to validate that their design works in fully digitalizing the process for additive manufacturing.
However, today, there are many digital tools like PowerPoint or Word within the engineering processes, but the process itself is not digitalized because these tools cannot trace, manage or check the overall engineering process.
However, within the Additive Manufacturing Network, we are including how we digitalize the entire set of activity and processes that occur between multiple players. We help companies and service bureaus to scale their production, meaning we allow them to go and run a broader set of activities. For instance, we are working with companies that are producing 100,000 parts a year but desire to produce 250,000 parts a year – exponential growth is expected.
We need tools to manage this volume of data that includes the number of parts and data to be delivered and produced. We will provide the capabilities to scale their production to higher levels of production and support digital warehousing, which is storing inventory digitally versus physically – saving enormous amounts of money.
Again, manufacturers cannot do additive manufacturing by themselves. The new business model for this industry is cross-leveraging, co-creating and co-generating with other partners. The Additive Manufacturing Network allows you to implement that model and provides the infrastructure to better collaborate with partners and other players.
Dean Haehnel: Thank you, Robert, for providing insights into the opportunity and value of ISAM, the changes in the industry and the Siemens Additive Manufacturing Network.
To listen to our entire series, find the episodes on Soundcloud, Stitcher and iTunes.
This concludes our second in a four-part series of blogs taken from a transcribed podcast on industrial-scale additive manufacturing. In our third blog, we discuss jump-starting industrial-scale additive manufacturing.
About the author:
Blake Snodgrass is a writer for the Thought Leadership team in Siemens PLM Software, which supports several venues, including the Thought Leadership blog for the company. He speaks with experts in their field who provide compelling insight into innovative technologies affecting industries and how this can impact the future. Blake has a Bachelor of Arts degree in Mass Communications and more than 25 years of experience working for IT companies, with roles in technical writing, marketing communications, user-experience design and content development.
Robert Meshel, Director of Additive Manufacturing Network, Siemens PLM Software
Robert Meshel is the Director of the Siemens additive manufacturing network, an online collaborative platform designed to accelerate the use of additive manufacturing in the global manufacturing industry. This initiative was born under his previous role, where he re-joined Siemens PLM as the director of strategy for the manufacturing Engineering Software unit. Driven by the passion for innovation in technology and business models, Robert was relentlessly pursuing new strategic opportunities developed within the organization or by partnering with ambitious external startups that are seeking to make a significant impact.
Robert originally joined Tecnomatix in 1996, where he served in various technical management capacities, including head of portfolio management, director of product management and business consulting.