The future of 3D printing with additive manufacturing
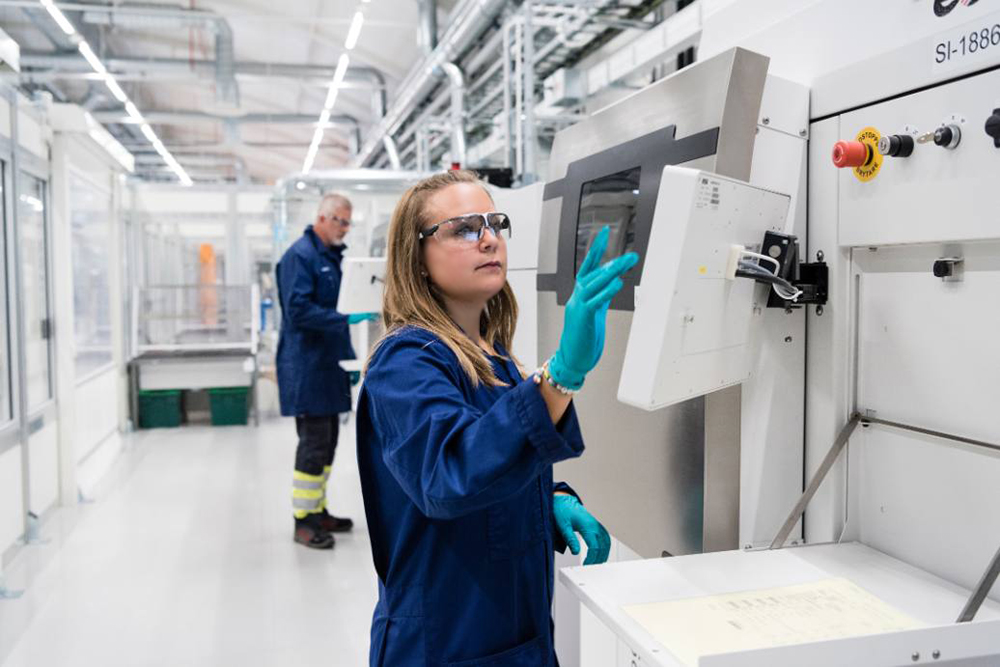
The future development of additive manufacturing for the process of 3D printing, including prototyping, and producing parts-on-demand to form three dimensional layers of materials via multiple techniques to create an object, is a growing phenomenon in manufacturing.
Moreover, factories like those in Finspång, Sweden are on the cutting-edge of this innovation, showcasing this amazing and developing technology in their factory. The future of additive manufacturing is onboard to grow exponentially as a standard piece of the process for all manufacturing.
The work that is ongoing at Finspång, and the additive manufacturing software Siemens offers, are just one part of a multistage approach to additive manufacturing. In 2016, Siemens purchased Materials Solutions, a world-class additive manufacturing contract manufacturer based in Worcester, United Kingdom, that manufactures extremely high-quality metal components for sectors such as aerospace, power generation and motor sports.
Furthermore, Siemens divisions outside of energy and software are working on projects that use additive manufacturing. This includes the mobility division, the corporate technology research division and the consulting division, all of which have ongoing additive manufacturing projects.
Another side of this multifaceted strategy is the recently announced Siemens Additive Manufacturing Network. This online network links part designers and additive manufacturing production service providers together, enabling online accessibility to additive manufacturing knowledge and distributed manufacturing for scaling up global industrial additive manufacturing.
In the near term, the Finspång facility will continue its serial production of turbine burners while moving on to the additive production of turbine vanes and blades.
Additive manufacturing matures to assist other manufacturers
Siemens is eager to assist the industry in its transformation from prototyping into serial production. With research and multiple products having successfully been built, and many more in the pipeline, the company has the capabilities to assist customers and original equipment manufacturers in maturing this technology.
The benefits of additive manufacturing are massive, and digitalization plays a critical role in ensuring success.
“Without digitalization or simulation of the process itself, you cannot industrialize on a large scale,” said Andreas Saar, vice president of manufacturing engineering solutions and additive manufacturing program lead for Siemens PLM Software. “Advancements in digital technology, simulation of processes, feedback loops and machine learning will be the core assets to make industrialization work.”
Visionaries at Finspång believe that Siemens’ turbines will eventually be able to connect to a diagnostic center where spare parts can be ordered and printed on-demand. Tracking each turbine will provide critical feedback, such as running hours and weather conditions, increasing the turbines’ efficiency and longevity while reducing costs. When a gas turbine can analyze its own health and signal in advance when it needs maintenance, components can be additively manufactured to minimize downtime.
Looking to the future
Technology is rapidly evolving and soon the additive manufacturing machines and processes of 2018 will be improved. Andreas Graichen, group manager for the Additive Manufacturing Centre of Competence at Finspång, believes that today’s additive manufacturing machines are like the cutting-edge technologies offered during the infancy of computing.
“Some may have thought at the time that what had been achieved was enough, but to stop innovation at that point would have eliminated the natural progression of better computers, the internet and the cloud,” said Graichen.
Siemens’ plan to exploit this potential relies upon new technology as it aims to design a state-of-the-art production facility. Robotics, data security, artificial intelligence and analytics all have a role in the intelligent facility the company envisions. The intention is for Finspång to serve as a model facility, with industry leaders visiting to see what the next generation of industrial production will look like.
Within the context of traditional production facilities, Siemens has already reduced repair times and increased production. But the company now wants to leverage a fully-connected production facility to boost its additive manufacturing capabilities. By connecting equipment to the digital chain, from design through serial production and quality control, the production process can run smoother and more efficiently, errors can be identified sooner, and time-to-market decreased.
Big data analytics and machine learning make this facility a “learning” facility. Production machines and printers will communicate with each other and use machine learning to capture data for later use. Components and products will be manufactured to exact specifications as build jobs take place on-demand and improvements to the process are made based on the machines’ feedback. As complexity grows and more data needs to be scrutinized, the human capacity to monitor changes becomes nearly impossible. These future machines will be able to track, open and print files while providing real-time feedback and adjusting the process on the fly.
Future vision of additive manufacturing
Siemens also envisions a facility one level above the learning facility. This will be an intelligent production facility, which brings artificial intelligence and virtual and augmented reality into play.
For example, powders and microparticles used or left over from a part build are unsafe for workers, and the labor-intensive cleaning process involves dressing in safety equipment and manually cleaning the build chamber. As machines take on more dangerous jobs, the work environment will need to be safer and healthier. The facility will use autonomous robotics and advanced machinery to manage the process and to do this cleaning, ensuring people onsite are not exposed to dangerous materials.
Since its initial investment in this technology, Finspång has already built a robot arm capable of extracting powder from the current M280 machines where burner repairs are performed, relieving employees of this potentially dangerous task.
Along with human safety, Siemens wants to lead the way with environmental safety. As additive manufacturing technology evolves, fewer resources are needed to complete production of a component. Using additive manufacturing can result in reduced final product weight, power consumption and material usage. Costs and environmental impact are minimized as fewer materials are needed for production.
The vision at Finspång is to have a semi-autonomous production facility for rapid manufacturing, repair or prototyping, with service technicians on hand to manage the factory and capacity. In the field, remote monitoring of gas turbines, for instance, will detect problems, alerting the facility to the need for spare parts and components where they can be ordered automatically via the cloud.
This semi-autonomous, connected factory will need systems such as in-line and off-line monitoring, robotic cleaning of additive manufacturing machinery, automated 3D scanning and validation, self-healing processes and systems that can handle and react to the data created as the process executes. This vision places Siemens on the cutting edge of advancing additive manufacturing with no other companies laying out specific plans.
As additive manufacturing technology evolves, fewer resources are needed to complete production of a component. Additive manufacturing provides results that relate to most industries and processes by reducing final product weight, power consumption and material usage. Also, costs and environmental impact are minimized via fewer materials needed for production ‒ substantial benefits that any manufacturing company would welcome.
However, in the near term, Siemens anticipates increasing the number of additive manufacturing production machines in Finspång, creating spare parts on demand, printing parts for new turbines and harnessing printing and job execution via the cloud and digital twins. Autonomy will allow sensors to monitor work as printing occurs, ensuring the right parameters are met and that the output will be of the required quality.
Designing and producing useful parts at scale
Moving forward often requires a look at the past. Finspång has a long history of manufacturing with metal, and this continues today with additive manufacturing at Siemens. This technology presents a tremendous opportunity to look back and see how current products can be improved by making them more cost-effective to produce and less expensive to the end user.
As with the gas burner, what started small as a tool for the prototyping and repair of a legacy design, evolved into the consolidation of 13 components into a single part that is now produced at scale via additive manufacturing. However, this is only one application and the potential for further innovation is immense.
The people at Siemens are working hard to help industries across the world take advantage of this exponentially growing technology. Their ability to design and produce useful parts at scale with additive manufacturing is a proven example for the industry to follow, providing solutions for where today meets tomorrow.
This concludes the final part in this series on the industrialization of additive manufacturing at the factory in Finspång, Sweden. View the overview of this series along with the subsequent second and third blogs.
About the authors
Ashley Eckhoff has a background in engineering and has been with Siemens for over 20 years in various capacities. He has spent the past few years deep-diving into additive manufacturing in both product design and marketing roles.
Aaron Frankel is with the marketing team at Siemens PLM Software and focuses on part manufacturing solutions. He has been in the PLM industry for over 15 years and enjoys helping companies apply innovative technology solutions to design and manufacturing challenges.