The additive manufacturing workshop for automotive
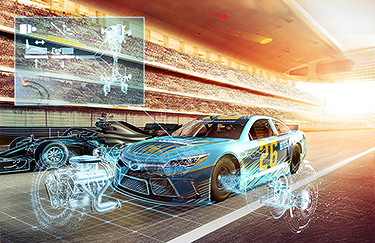
A common misconception in the automotive industry is that additive manufacturing (AM) is only for prototyping of small volume production in motorsports. While this is a piece of what additive contributes to the automotive arena, it’s exclusive to the phenomenal impact additive manufacturing is making globally with implementing innovative technologies on automotive factory floors.
The positive impact that additive manufacturing is making to the auto industry must not ignore the contribution of engineers, designers and executives in creating and extending digital workflows with generative design, additive manufacturing and simulation in the production of crucial parts.
Positive examples to the impact of additive manufacturing were presented at the introductory Additive Manufacturing Workshop for Automotive (AMWA), held at Detroit’s 2019 North American International Auto Show on January 16th, displaying the integration of 3D printing in revolutionizing the design and production of automobiles.
To have this workshop held at such a renowned forum, attended by hundreds, represented a substantial interest in how OEMs are employing additive manufacturing to further its advancement in the automotive sector. The initial presentation at the AM Workshop showcased Ford Motor company’s polymer parts: lever arm, auxiliary plugs and electric parking brake brackets.
These parts, using Ford’s qualified epoxy materials, are made via Carbon’s digital light synthesis technology, amazingly surpass stringent performance testing and crucial requirements like interior weathering, heat exposures UV stability, fluid and chemical resistance, flammability and fogging.
The benefits of these parts go beyond the concept of new technology – displaying notable improvements:
- Reducing leading time of new lever arm by 50 percent, dispelling inventory and warehouse requirements.
- Light-weighting of electric parking brake bracket by 60 percent versus using old-school, stamped steel.
- Simplified brake bracket production process via 3D printing, reducing the complex requirement of two components for both sides with a streamlined mono design.
Ford’s presentation, led by Ellen Lee, Ph.D., Additive Manufacturing Technical Leader, Ford Motor Company and Paul Dilaura, Vice President, Enterprise Partnerships, Carbon, forecasted additive manufacturing playing an active role in the automotive industry in specified areas of:
- service parts,
- low-volume production,
- series production,
- mass customization and
- distributed manufacturing.
All of these will focus on new materials, software and design tools with end-to-end manufacturing processes, interfacing with automated factories.
Additive manufacturing – the hype is gone
“Additive manufacturing started with all hype,” says Kevin Brigden, Additive Manufacturing Advanced Concepts, Renishaw. However, this is changing rapidly with leveraging metrology, calibration and performance testing technologies that define Renishaw’s CMM inspection equipment. Their well-established industrial metrology, process control and automation technologies display their innovative approach in the additive space: Renishaw’s Additive Manufacturing Solution Centers – where engineers guide customers through the design process via additive manufacturing to validate production deployment.
Brigden emphasized the four-laser powder-bed metal printer and one of the greatest opportunities in additive today — for which Renishaw is a pioneer — in-process control and capturing of data during the build process.
Additive manufacturing – mold tool applications
In discussing the latest in innovative hybrid metal 3D printers, Evan Syverson, the Additive Manufacturing Business Development Manager of Sodick, stated that mold tool applications require a quick turnaround and shorter injection cycle time. “Throughout the cycle of a plastic part — which includes mold open time, mold closed time, filling stage and packing stage — the biggest time waste is cooling time, which can represent 60 to 70 percent of the entire cycle time,” he said.
The most significant opportunity to reduce overall cycle time is through conformal cooling — an opportunity ideally suited for hybrid manufacturing.
Combine Sodick’s powder-bed printers and laser technology with a linear motor spindle, and it performs mill operations during pauses in the printing process that allow access to internal features when the part is finished. This capability, correlated with conformal cooling channels, allows for the building of printed lines that match the part shape, eliminate hot spots, reduce cooling and cycle time and result in almost no defect. Other hybrid manufacturing molds, such as beryllium copper, have a 17 percent longer cooling time with reduced tool life.
Industrializing additive manufacturing – design and produce parts at scale
“This is the most exciting time in my career of 30 years,” says Chris Weber, the Director of AM Portfolio Development, Siemens PLM Software.
Siemens participated in the additive manufacturing development of the hydraulically-powered spoiler which helps control the Bugatti Chiron sports car, stabilizing it at speeds of 240 mph. “The end result was an innovation process that was accelerated tenfold: reduced aerodynamic drag and light-weighted the system by 50 percent,” says Weber.
Douglas Ramsey, Chief Development Officer of Hackrod, also highlighted the La Bandita speedster – “the first car designed in virtual reality with a chassis and other large structural components being 100 percent 3D printed,” says Ramsey.
A combination of artificial intelligence and large-scale metal deposition printing, the La Bandita is generatively designed critical components — a technology process that Ramsey says, “will someday be achievable while playing a video game.”
Technologies are encompassing additive manufacturing: generative design, material characterization and machine learning.
“Manufacturing is getting back to an artisanal world. The engineering knowledge is locked in our heads. I think we’re about to democratize the information,” says Ramsey.
Additive manufacturing trends and technologies
“As we approach the 2020s and beyond, the desire for mass customization and light-weighting will increase the ubiquity of generative design. This, in turn, ensures that parts will become too complex to manufacture via traditional methods,” says Rick Fulop, CEO and Founder of Desktop Metal.
However, he went further to explain how the powder-bed fusion process raises issues that need addressing, including slow printing speeds, limited build space, arduous postprocessing, limited material choices, hampered geometrical resolution and few automation capacities.
To learn more, read Brent Donaldson’s recap of the Additive Manufacturing Workshop for Automotive.