The 3 trends that are challenging heavy equipment manufacturers
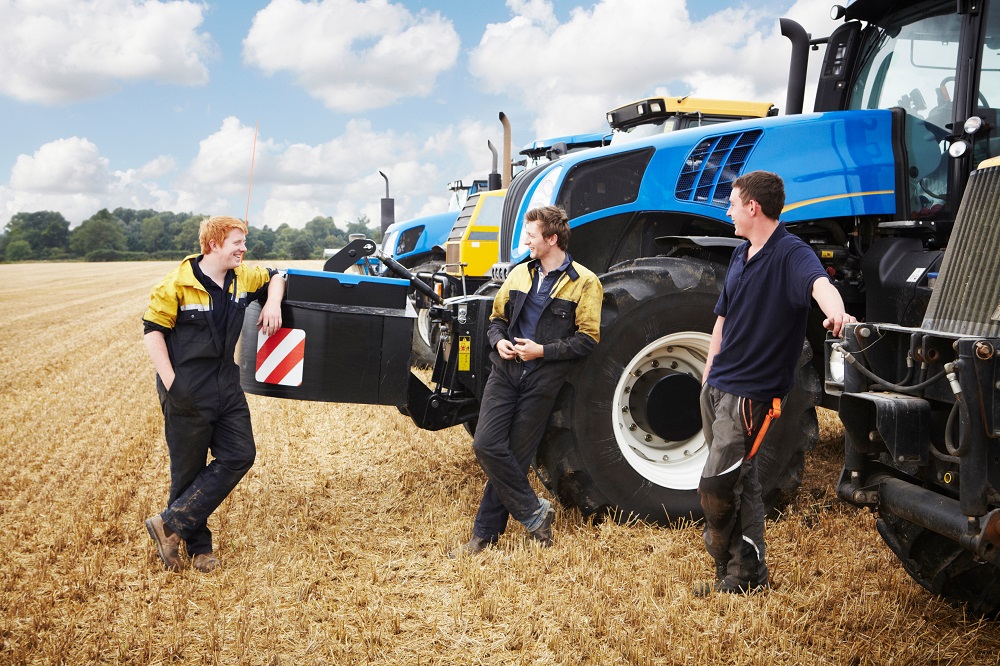
Heavy equipment manufacturers face no shortage of challenges. Everything from more stringent noise regulations to the need for localized customization, manufacturers are scrambling to keep up with ever changing laws, evolving technology and customer demands.
Challenges in the heavy equipment market include:
- Stricter noise regulations
- Increasing emission standards
- Higher safety requirements
- Stronger global competition
- Managing globalization versus local requirements
- Decentralized engineering practices
- Demanding customization and variants
- Growing rental businesses to reduce cost of ownership
- Better productivity
Of all the challenges, there are three key trends emerging:
Regulations. Government and safety regulations are becoming stricter as municipalities all over the world are determined to both achieve environmental targets that reduce CO2 emissions and protect workers and those in the surrounding area from bodily harm, which include noise levels, acoustic cabin levels, vibration levels and rollovers.
Globalization/localization. Regional original equipment manufacturers (OEMs) have the advantage of working locally to take advantage of customization opportunities. In Italy, there are many local crane manufacturers forging deep customer relationships that are actively competing against most OEMs. They survive through their flexibility and ability to manufacture and tailor machines to meet customer needs. Engineering know-how, OEMs that can focus on research-and-development at the local level, not only find this customization a key trait, but also helps build a rapport for after-market business.
Heavy equipment manufacturers must find ways to extend their distribution network. One way is to look for new partnerships. Consolidation whether it’s through new partnerships or acquiring expertise has shown to provide significant resources that bring innovation to the market.
Customer-centric trends. Rapidly changing technology and customer needs mean manufacturers and customers must work together to achieve success. Businesses that are agile are better aligned with helping customers by sharing operational best practices, building strategic R&D partnerships and addressing the cost of ownership.
Addressing the day-to-day needs and concerns such as fuel and maintenance costs, uptime performance and operational costs are critical before the product moves out of the development phase.
Closer interactions with customers is key to understanding what they need on a local level. The aftermarket business is highly profitable so honing machine performance and reducing cost of ownership are crucial.
How the digital twin helps heavy equipment manufacturers
The two main focuses on development must center on operability and user comfort. Operability addresses uptime performance, access to spare parts and oil and fuel consumption whereas user comfort involves everything around the cabin from ergonomic seats, interior and exterior noise, and vibration.
Multi-attribute performance engineering combining simulation and test must be present to optimize performance throughout the entire development process. The digital twin helps validate virtual performance during the product’s development cycle.
Take the idea of engine downsizing and all the big data that goes along with it. By adopting and deploying the digital twin to explore design space, engineers can transform their approach to performance to meet today’s engineering challenges.
Predictive engineering analytics within simulation helps predict real world behaviors down to a multi-physics, multi-disciplinary and even a component level while simultaneously addressing multi-domain system behavior. Predictive engineering analytics can combine 1D, 3D, Test and CFD to simulate a complete system as it operates throughout the product lifecycle. This brings realism to your simulation in each stage of the development from early planning to final design.
Heavy equipment manufacturers are using simulation technology to deliver multi-fidelity digital twins consisting of simulation and test models for rapid sign-off validating optimal systems architectures. With a digital thread of the product throughout development, engineers and designers address all critical system characteristics by integrating simulation disciplines and physics for balancing attributes. All the while, the varying models remain in sync with the product and its operating environment. Applying predictive engineering analytics and multidiscipline design exploration helps discover better designs faster and allows manufacturers to move forward with greater confidence.
Predictive engineering analytics also integrates simulation and tests together to quickly validate the simulation model you’re using. Digital twin technology can then combine historical and test data to calibrate simulation models providing information for different design parameters and limitations. This can improve accuracy of simulations and increase confidence when meeting customer requirements.
Multi-attribute simulation
Using multi-attribute simulation to optimize machine performance engineering allows increased efficiency and the enablement of new insights.
Fuel economy and energy management. Engineers can build to adhere to regulations surrounding emissions. Everything from fuel efficiency to thermal comfort can be tested and validated through simulation.
Structural integrity and durability. Part of customer expectations is guaranteeing the life of the machine under realistic loading. Simulation can test a variety of loads and in countless environmental scenarios to ensure the machine maintains integrity.
Operability and efficiency. Before delivery, manufacturers are often tasked with proving their products are reliable. If an OEM waits until the product is created before validating its efficiency and operability, changes are costly and delivery is delayed indefinitely.
Noise and vibration. Exterior and interior noise as well as the level of vibration that can affect the operator are subject to regulations and ISO certification because they directly impact safety. Not only can simulation prove the acoustics within the cabin are safe but can ensure the driver can operate the vehicle efficiently.
Controls integration. Balancing various subsystems and attributes amid complex systems is a challenge for manufacturers. As more software, mechatronics and electronics are built with increasing integration into machines, there is a greater need for ensuring all components work and evolve cohesively.
Bringing it all together with simulation tools
State of the art simulation tools are being used for component design to help balance the trade-offs between various systems. As the three key trends continue to challenge OEMs — regulations, globalization/localization and customer-centric trends — simulation can minimize costs as the various evolving needs change.
By incorporating multi-physics 1D and 3D simulation and other innovative tools, a digital twin of the heavy equipment can validate the impact of design changes, environmental conditions and other variables. This technology can help meet customer needs and expectations and prove safety and regulatory compliance while eliminating the need for costly physical prototypes.
Click here to learn more about the benefits of the digital twin for heavy equipment challenges.