Where additive manufacturing meets tomorrow: challenges to industrializing 3D printing
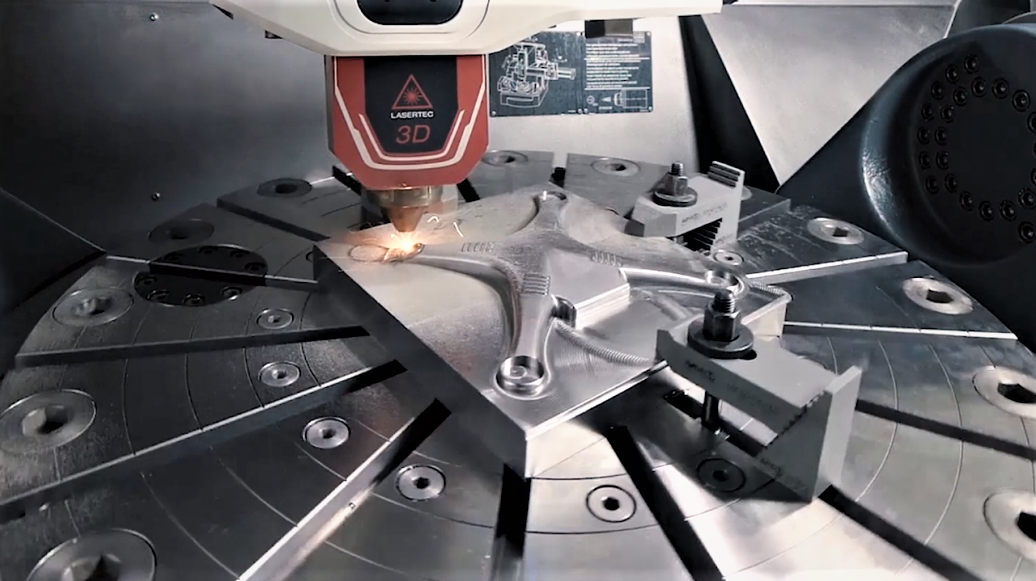
At the dawn of the 20th century, manufacturing was on the cusp of radical change, setting in motion a revolutionary dynamic in the automotive industry. Many players entered this arena, capturing a slice of innovative technological advancements in both combustible and electric engines.
However, one innovator named Henry Ford came to the forefront with the concept of mass manufacturing of the motor car, making it possible for the common man to purchase it. Because automobiles were once strictly an asset of the wealthy, Ford’s ingenuity catapulted them to become a ubiquitous commodity that many people could afford. Thus began a revolutionary change that has since become commonplace in mass production for developing an assembly line to create greater efficiency while reducing cost.
Industrializing additive manufacturing
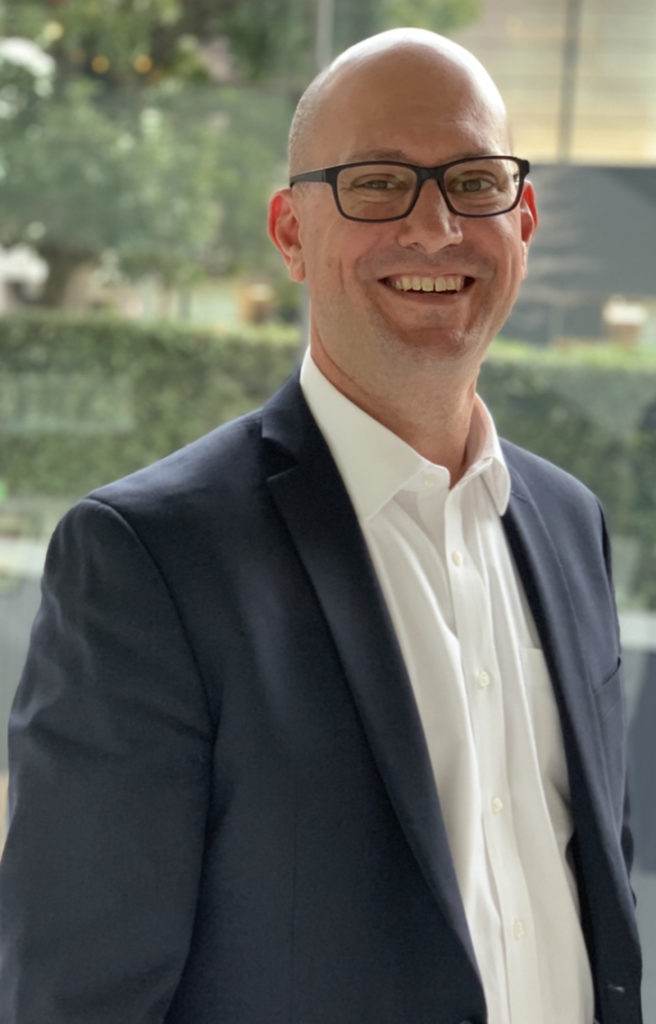
Fast forward more than a century later, and manufacturing is once again on the cusp of radical change to what some people call the fourth industrial revolution: new, innovative methods for manufacturing products and their processes. Cutting-edge technologies such as additive manufacturing (AM), or 3D printing, make it possible to print complex objects via a CAD simulation model, creating layer-by-layer using various types of materials with high precision and repeatable quality. Simulation and 3D modeling allow for advanced complexity of design and quality, ultimately resulting in fewer distortions and errors.
Additive manufacturing goal and challenges
While there are numerous examples of additive manufacturing in its prototype stage, the goal is to propel it into the mainstream. Though it may not replace all conventional manufacturing methods, it will serve as an invaluable add-on for adopting innovative technology because it allows users to re-imagine products, reinvent manufacturing and even rethink business models. In order to get there, the industry still has to overcome some challenges – after all, 3D printing is an extremely complicated process.
Just think about how complex this concept is: Driving a laser beam no bigger than the tip of a pen, at a speed of six feet per second, melting metal powder at more than 3000 degrees Fahrenheit over a course of about 25 miles, to create a product about 18 inches high with a 10 inch circumference, and never once deviating from the planned path. This is the additive manufacturing challenge, and its complexities continue throughout several stages.
First, find the ideal materials. Secondly, create a perfect design. Lastly, qualify the process to be able to produce that design. Then production needs to execute flawlessly, and when the part comes out of the factory, it needs to be certified. The full AM challenge covers the entire value chain: from product design to the production process all the way to its performance, including:
- assessing opportunities
- optimizing designs
- using materials
- qualifying parts
- avoiding print failures
- optimizing efficiency
- orchestrating production
- monitoring issues
- automating production
- providing trace-ability
- gaining insight into information from the manufacturer
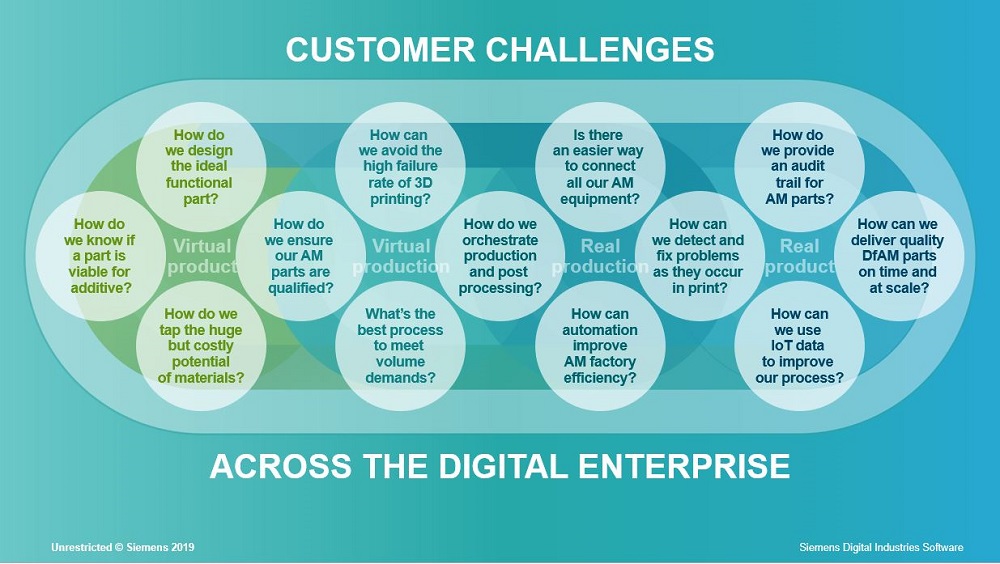
All of these assist in achieving the production of quality parts, on time and at scale.
Let us focus on some of the most significant challenges.
1) How can we tap into the huge but costly potential of materials?
Audi recently published a paper about a metal additive manufacturing part that unexpectedly failed in an unpredicted location on the part. So, how can additive manufacturing help to tap into the complexities of the part, process and materials to avoid these failures?
It can take up to five iterations to get a print correct. How can this high failure rate be avoided?
Siemens is working on two solutions to assist designers and engineers:
- automating the discovery of optimal lattice structures and
- predicting part fatigue and durability.
Imagine using a smartphone app to scan your feet to create a pair of running shoes, creating a lattice structure tailored to your size and running style. Additive technology does this and much more, automating the discovery of the optimal lattice per the target performance of the part.
Siemens
performed design experiments
on 39 lattice structures to characterize the properties of each
one, followed by predicting the performance for various
cell sizes and strut diameters. Based on their findings, the software gives power to the designer to suggest the best-automated lattice design to
achieve a given part’s design performance specifications. Also,
artificial intelligence (AI) technology assists in automating the discovery of the optimal lattice structure for a design’s requirements.
So, as the Audi story conveyed, part failures can happen in unpredictable places. AM durability solver software rectifies this problem utilizing:
- Trained machine learning algorithms to predict fatigue properties for material data, print build orientations, heat treatments, support structures and porosities.
- Solvers that account for feature surface roughness, porosity and local material properties.
- Feature mapped results onto the basic finite element mesh model, allowing the ability to see where a part may fail for a given orientation. Users can then alter the geometry or explore new build orientations.
- Elements for assessing the impact of the melt pool and its effect on local material properties as a part is being built.
2) How can we avoid the high failure rate?
Compared to conventional manufacturing, it can take three times more iterations to validate an additive part design that will print repeatedly with quality. This means process inefficiencies are magnified three times. So, how can the process deliver quality parts efficiently when data is thrown over the wall?
Digitally defining a process for AM parts requires two technologies to solve this problem. Both rely on the power of simulation; one addresses macro-level defects in AM builds, the other addresses meso-level defects.
The macro-level 3D printing problems are overheating, residual stress, distortion, warping and re- coater collisions. These issues are addressed using an AM build simulation CAE-based solution, which predicts the thermal-mechanical distortion of the parts in the 3D print process, altering the original CAD to compensate for the problems it uncovers. This solution provides customers with significant improvement in their success rates to achieve first-time-right 3D printing.
However, this solution only analyzes the 3D print process from a Macro-level.
Path analysis
is a physics-based technology that
predicts meso-level defects due to overheating along the actual tool
path. Then it re-sequences the
vectors in the toolpath job file to correct the predicted
defects.
3) How do we deliver quality parts on time and at scale?
The most significant challenge that companies face pertaining to design is opportunity. Using a variety of materials in an infinite number of ways develops new dimensions to optimizing product performance. So, how do you work with this dynamic of choice?
Sintavia, one of the leading suppliers of AM parts to the aerospace industry, has dealt with the issue of how a disconnected digital thread impacts the ability to deliver AM parts on time and at scale. Siemens is working with them on several projects to achieve an integrated end-to-end process for industrializing additive manufacturing. These projects include streamlining the print process through simulation-driven design and optimizing shop floor operations.
Simulation-driven design
Simulation-driven design can have a significant impact on the quality and efficiency of the AM process. Siemens’solutions are tightly embedded into the simulation process, driving design without over-the-wall iterations.
This design method allows for the manufacturing engineer to be concurrently working on setting up the build job in parallel to the designer modifying the design, instantaneously updating the simulation model and rerunning the analysis. Then the manufacturing engineer can update the build job with the new part design all in one system.
While simulation-driven design for additive manufacturing (dfAM) streamlines the front of the process, factory communications connects the digital thread to the shopfloor. We’re working on a solution for automakers to securely connect all the software in the AM process to the physical world, orchestrating, executing and monitoring the entire 3D print operation.
Where challenges of today meet solutions for tomorrow
Besides the challenges mentioned, above, solutions are being developed to address all areas of the AM challenge as part of the technical vision to achieve industrialized additive manufacturing. Industrializing AM is only a matter of time. Just like the automobile, this technology will eventually take off and become a mainstream addition to all manufacturing. However, it will take collaboration, an ecosystem of partners and the right technogies to make this change happen.
”Be ready to revise any system, scrap any method, abandon any theory, if the success of the job requires it.” – Henry Ford
This concludes the first article in a blog series highlighting the challenges and steps to industrializing additive manufacturing.
Related Links:
Press Release – Siemens expands additive manufacturing portfolio through acquisition of Atlas 3D
Industrializing Additive Manufacturing 3D Printing through an Integrated, End-to-end Process
About the author:
Aaron Frankel is vice president of Siemens additive manufacturing software program. He has over 20 years of experience in the PLM software industry and has held various positions in engineering services, product management, and marketing – all focused on helping manufacturers take advantage of the latest digital design and manufacturing technology.