Building reliable EV power delivery packages
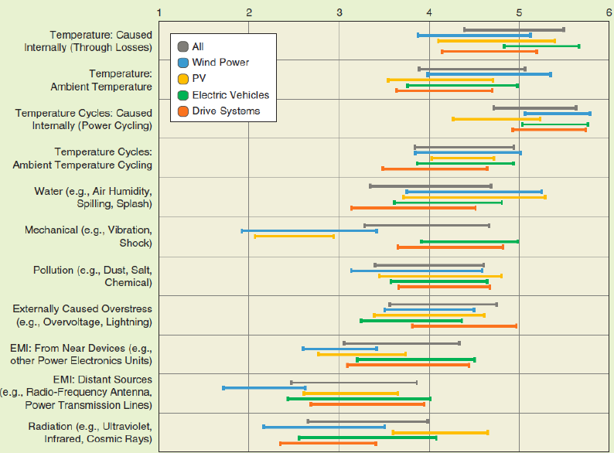
Electric vehicles (EV) may be as old as internal combustion engine (ICE) powered vehicles, but due to the superior energy density of petroleum products over electrical storage at the time, ICE development substantially outpaced EVs. But EVs are beginning to gain substantial ground on ICEs. In 2018, worldwide sales of electrified vehicles grew over 70 percent and by 2040 they are expected to contribute to 57 percent of all passenger vehicle sales according to Bloomberg New Energy Finance.
The growing adoption of EVs is pulling the technology out of the early adopter phase and niche markets into the mainstream, but this brings higher scrutiny and reliability requirements. And with more and more companies investing in EVs, differentiation is key. Some are incorporating greater feature sets, while others concentrate on higher efficiencies. Regardless of the focus, electronics play a key role in EV performance and differentiation. But all of these improvements need time testing, refining and re-testing to establish predictability across the lifetime of the final designs. This is especially true for automotive semiconductor suppliers who must adhere to strict quality and reliability requirements set by vehicle OEMS and Tier-1 suppliers.

J. Falck, C. Felgemacher, A. Rojko, M. Liserre and P. Zacharias, “Reliability of Power Electronic Systems: An Industry Perspective,” in IEEE Industrial Electronics Magazine, vol. 12, no. 2, pp. 24-35, June 2018.
One of the crucial areas of reliability in any EV is the power electronics. To compete with ICEs, EVs need to use high quality components and increasingly efficient silicon for controlling the power delivery and features throughout the vehicle. The single most important factor affecting reliability is temperature, as seen in figure 1. During design stages of power electronics modules, thermal performance and reliability data is important for development and verification. For production, vehicle OEMs often request vendors provide quality test data for batches of components or each component.
Temperature is important, but how is it tested?
Physical temperature measurements are traditionally taken via two methods, thermocouples and infrared (IR) cameras. Unfortunately, these methods only capture surface temperatures of the components being inspected. Moreover, these methods are not completely accurate: thermocouples can affect the surface temperatures through the additional conduction path whereas IR cameras are hindered by changes in emissivity and absorption on the component surface. Even after accounting for these effects, the real junction temperature (Tj) within the electronic circuitry remains unknown, hampering the design team’s ability to assess the true reliability of the design.
The real Tj can be calculated using the forward voltage of a PN junction under a forced current condition. After calibrating the forward voltage (or temperature sensitive parameter – TSP) against the change in temperature according to JEDEC, JESD51-1 or MIL-STD-750D standards, this can produce highly accurate readings.
This temperature data is still not actionable, however. One last step is needed to be able to analyze the power electronics – power stepping. Increasing delivered power to a device while recording the voltage (analogous to temperature using TSP calibration) will deliver a structure function representing the resistance/capacitance map along the heat flow path from the source to the ambient environment.

From the capacitance/resistance plot, physical objects and structures can be determined as seen in figure 3. At this point, much of the data collected could be analyzed manually, but doing so prevents truly deep insights.

Upgraded thermal testing and simulation
Fortunately, advanced testing hardware in Siemens Digital Industries Software Xcelerator platform is now available that accurately measures power electronic component thermal metrics. Using a combination of Simcenter™ T3STER™ hardware and the Simcenter ™ software enables accurate and highly detailed thermal metrics for components, as well as reliability, quality and calibration metrics using the following methodologies:
- Reliability is established by quantitatively measuring changes in the component structure through extensive power cycling
- Quality can be identified by comparing incoming and outgoing devices, this could be a change to die size or thermal interface material
- Combining test measurements and simulation data, temperature profiles can be calibrated to create extremely accurate thermal models
The most important capability of this setup when optimizing for EVs is the ability to refine simulations of these same processes. By continually adding test data to the digital twin of the vehicle, the time required to validate and optimize the designs is dramatically reduced. Physical testing is still required, of course, but not on the same scale.
This blog only scratches the surface of what can be achieved by thorough characterization of thermal behavior within EV power electronics. For an in-depth look at the process, check out Andras Vass-Varnai’s webinar simulating and testing the latest technology for EV power electronics. For ideas on how to implement the technologies to best optimize your workflow, check out one of the many case studies from our customers;