Autonomous Vehicle Development from Chip to City (Part 1)
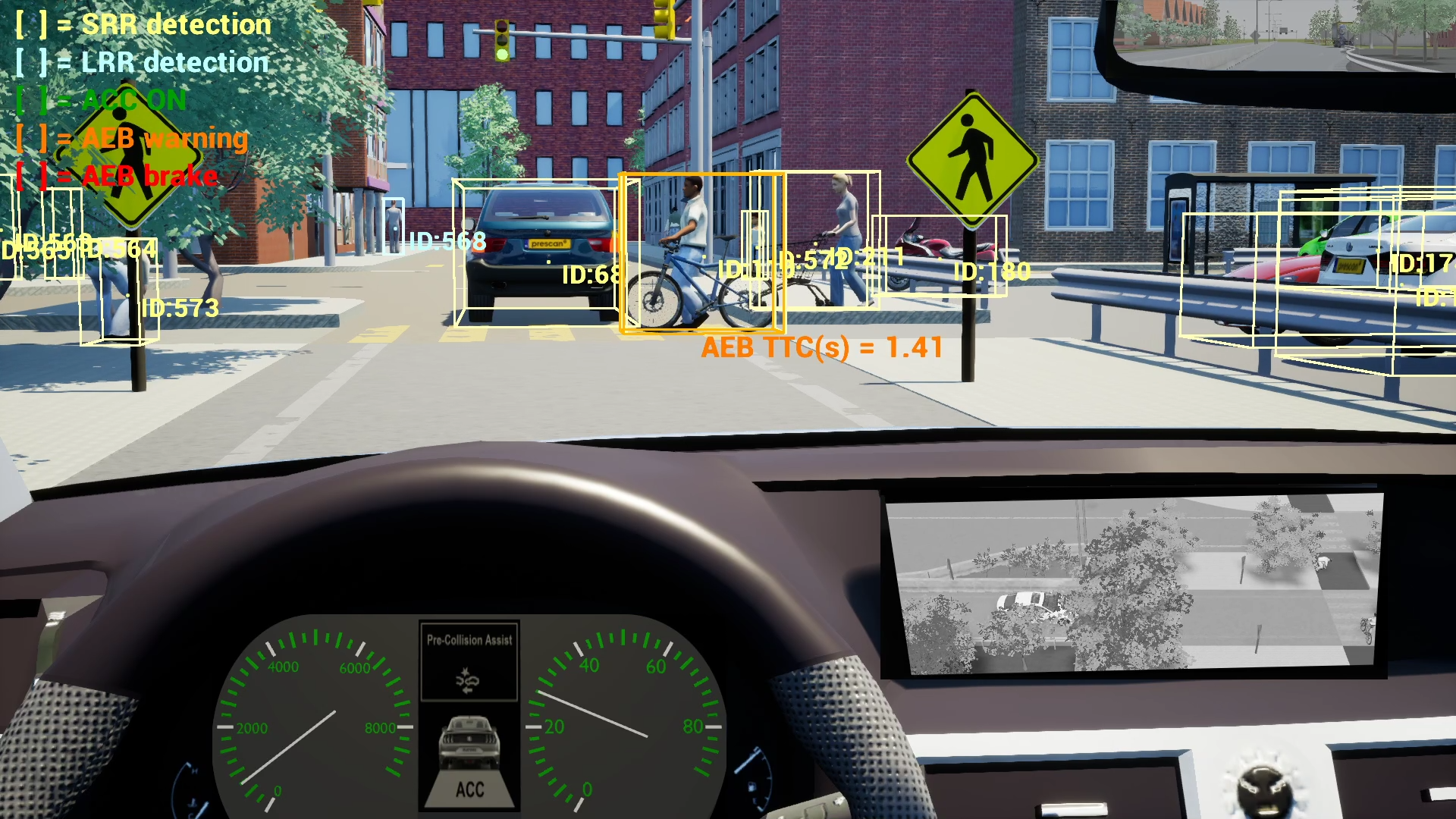

Autonomous vehicle development cannot be successful without simulation. Digital twin capabilities ‘from Chip to City’ will make the difference in an efficient digitalization strategy. AV specific chips and accompanying core electronics and embedded software will proof to be the major differentiation between AV’s in the near future.
Where mobility meets tomorrow
Autonomous vehicles (AVs) are expected to be among the most complex technologies ever built. These vehicles will require state-of-the-art components from multiple domains including embedded software, semiconductor chips, sensors and electrical wiring. Additionally, extensive testing, verification and validation will be required to ensure the safety of these systems. Rand Corporation has calculated that it requires more than 17 billion kilometers of test driving to demonstrate a failure rate significantly better than humans. Finally, in autonomous vehicle development manufacturers will need to address AV deployment in mobility systems and connectivity with other vehicles (V2V) and infrastructure (V2I), such as traffic lights and management systems. Leveraging these connections will be critical to the successful implementation of AVs within the context of an entire mobility system.
AV manufacturers will need to alter the very structure of their design, engineering and verification methodologies to surmount the challenges created by the multi-domain and multi-level complexity of autonomous vehicle development. They will need to adopt a new level of digitalization, connecting vehicle engineering and verification to manufacturing and utilization in the field. These companies will need to build a portfolio of solutions that can cover every domain and development process, from the chip to the city. A holistic chip-to-city approach that encompasses software, services, application development and transportation solutions will enable closed-loop engineering, testing and deployment of AV platforms.
Digitalization is the key
In their pursuit of greater digitalization, AV manufacturers should seek to achieve three imperative characteristics. First is a comprehensive digital twin of their vehicles and production processes. The comprehensive digital twin comprises many digital threads at varying levels of abstraction from product design, manufacturing and in-field utilization data from the IoT, enabling greater efficiency and insight in vehicle development and deployment.
Next, these companies should seek to leverage and build adaptable solutions. No two companies are exactly the same, so no one set of software and services will fit the needs of each and every company. The same is true for cities as they plan for and deploy autonomous and shared mobility systems to fit their unique needs. Finally, in autonomous vehicle development manufacturers should seek to foster and participate in an open ecosystem of cities, suppliers and other manufacturers. The complexity of autonomous mobility demands collaboration, rather than separation.
In a pair of blogs, we will examine how Siemens’ advanced software solutions and experience with real-world AV implementations make it an ideal partner to drive digitalized semiconductor, vehicle and mobility system development, while achieving the three imperatives outlined above. Here in part one, we will focus on the electronics development, verification and validation capabilities that will be critical to AV platforms. In part two, we will look at the system- and city-level technologies that will help companies integrate these highly advanced electronics into vehicle platforms and mobility systems.
Designing and verifying AV semiconductors
The critical processors in an AV will be highly sophisticated system-on-chip (SoC) devices, that are built for artificial intelligence (AI). Today, car manufacturers usually source semiconductor chips for their vehicles from specialized suppliers. In an AV, however, these chips will represent a large portion of the value of the vehicle, as well as a critical brand differentiator in the market. As a result, automotive companies are investing in the creation of custom SoCs to power their future vehicle platforms. Automotive SoC development is intensely complex and evaluated under the strictest functional safety and reliability standards.
Siemens offers a full suite of integrated circuit (IC) and SoC design, functional verification, physical verification, and test solutions for both analog and digital chips. These solutions provide AV manufacturers with state-of-the-art capabilities needed to create powerful SoCs that are both energy efficient and near-flawlessly reliable over extended service lives in harsh conditions. Furthermore, a pre-silicon autonomous validation environment enables AV manufacturers to collaborate across the IC supply chain to develop and verify custom AV semiconductors. This environment, called PAVE360, uses a combined design, simulation, and emulation approach to simulate an entire platform for autonomous vehicle development, including decision algorithms. PAVE360 allows companies to virtually verify and validate the functionality of SoC designs within the context of the AV platform, including software and vehicle hardware (figure 1).

Integrating cross-domain electronics development
In addition, electronics content in AVs will be exponentially more complex than today’s human-driven vehicles. AVs will depend on an array of 30 or more sensors, such as radar and LIDAR, within the vehicle body to perceive the environment. Design goals for autonomous vehicle sensors are centered on reducing the size and cost of the sensor without sacrificing high resolution or range. Additionally, these sensors must function reliably when integrated into the vehicle structure and perform in all weather conditions. Engineers also must ensure the signal and power integrity of all on-board processors and electronic control units (ECUs) while balancing device cooling with power consumption.
To overcome these challenges, the industry needs an integrated electronics, thermal, electromagnetics and mechanical simulation workflow (figure 2). Siemens’ advanced 3D and 2D computational fluid dynamics (CFD) and system simulation software can integrate with both mechanical and printed circuit board design environments. This provides a seamless workflow that is adaptable to designers and analysts. Companies can leverage this software suite to create digital twins of sensors, ECUs and processors, ensuring optimal design, vehicle integration and reliability without sacrificing real-world performance.

New sensors and ECUs are driving a 40% increase in hardware content within the vehicle architecture. At the same time, network content is expanding, growing from megabits to gigabits and the safety and security of the architecture has become an absolute necessity. These factors are driving unprecedented complexity in AV electrical and electronics (E/E) systems. The complexity only continues to escalate as manufacturers integrate E/E systems with the rest of the vehicle, and each vehicle into larger mobility systems. We will continue in part two by examining E/E systems engineering, the virtual verification and validation of vehicle dynamics and integration into mobility systems.
About the author: Matthieu Worm drives the program for the ADAS and autonomous driving domain within the Simulation and Test Solutions group of Siemens Digital Industries Software. He has brought coherency and consistency in the Simcenter solution portfolio for the development of autonomous systems and continues to work on the integration, extension and deepening of the offering.