Solutions for a new age of automotive regulatory compliance (pt. 4)
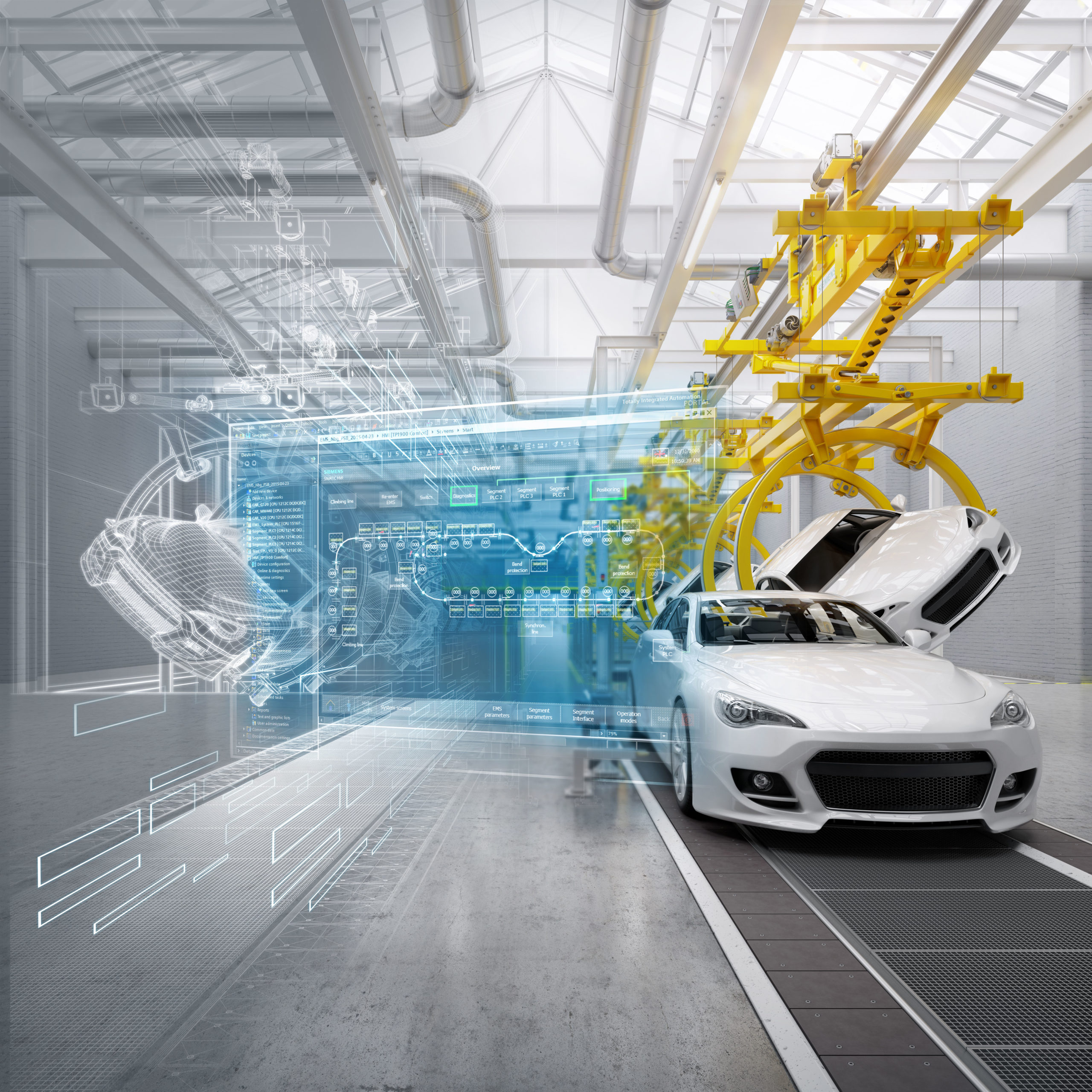
In the last post of our series exploring the landscape of automotive verification, we established three core questions engineers must ask themselves before executing the required verification processes on a design. Where are the relevant files? Are these files and dimensions up-to-date? And, have all these metrics been verified? These questions are simple in wording, but as we saw in blog #3 getting them wrong can be a very costly endeavor, leading to longer development times, reduced customer trust and even criminal charges. The continued rise in complexity due to electrification, autonomous drive, ADAS, emissions reduction, and vehicle connectivity mega-trends will only intensify the need to manage the verification process to ensure all the new requirements are met.
To avoid wasted time and cost and to deliver the right product efficiently there are three main areas that should be addressed: enabling an end-to-end automated workflow, establishing consistent activity notices/updates and providing all this information as a single source of truth.
End-To-End Automation
Verification management is far more than requirements management. Verification processes encompass everything from requirements and planning to CAD models and simulation along with all process request documentation, test requests and related results. Integration of these workflows, along with other things like engineering bills-of-materials management and revision control, is critical in delivering a modern and state-of-the-art verification management process. Incorporating automation is not only necessary for automotive manufacturers to keep pace within the industry, but also provides access to higher-level process planning.
End-to-end automated workflows can manage and control the entire development operation. For each step in a process, the system can manage the current tasks, trigger the next event as well as provide all the data objects required for the task. This can include previous results, status updates or any other relevant data for the process. For something as complex as a modern vehicle, this interoperation would be nearly impossible without automation to streamline the workflow, and track all of the relevant parts of the development process.
Development Updates
Automotive engineering programs are inherently chaotic due to the complexity of creating a modern car with dozens of mechanical subsystems, hundreds of electronic control units, and millions of lines of software code. The goal is to deliver the most well-balanced product to fulfil regulatory requirements and meet the needs of customers and cost on behalf of the business. That means many factors are subject to a state of constant flux while engineers optimize and refine the design to meet evolving consumer or regulatory needs. To manage this welter of ideas, data and designs requires a powerful, accurate, and real-time solution. Navigating the complex budgets, resource allocation, equipment and delivery milestones of an engineering program has traditionally required direct communication with the chief engineer who then communicates with other engineering teams to resolve a request. Best case, this takes a couple hours to get the response to the program manager requesting the information. In the worst case, it can take days. If the program manager needs more information on the topic, more communication and possibly even face-to-face meetings will be necessary given a complex issue.
Instead of a needlessly time consuming back-and-forth to get the answer, a real-time status dashboard can supply the needed information at a glance. Providing every development team with access to a dashboard that provides the status of various verification activities greatly reduces the time required to communicate these updates across the organization.

With a robust digital thread underlying the verification management process, even highly specialized data that is inappropriate for a high-level summary can be accessed through the dashboard. For instance, the dashboard may show that new results from a noise, vibration and harshness (NVH) study are available for the rear brake calipers. An engineer can interact with the dashboard to learn more information about this study, such as the design revision used, the parameters of the test and the results. Giving everyone access to this data streamlines future development by reducing the reliance on ad-hoc information requests.
Single source of truth
Now that information is up-to-date and in the right location, how can an engineer be sure the data is correct? In fast-pace automotive development environments, it is not unusual to have undocumented or un-validated changes, new targets and requirements. Lack of direct access to the approved and correct information exacerbates this situation. Working from incorrect data can yield disastrous and often costly results that may not surface before the release. By maintaining a single source of truth for all development information and test data, an organization can work to eliminate the acceptance of rumor, hear say or gossip as the truth. Avoiding this means providing direct access to correct and approved information through the digital thread.
A verification management process with a digital thread ensures that the entire product development eco-system has access to the approved and validated information, data. If a piece of information is not in the system, then it isn’t a valid piece of information. It also means nothing can be accidently added or modified in the system. Gone are the email, voice mail, text messages, missed meetings, that inhibited the relay of changes and updates. Everything from requirements to CAE simulation procedures need to be a part of the digital thread to be considered valid results.
Automotive designs today are far too complicated to be discussed in-depth at the water-cooler or through emails. Imagine trying to discuss the intricacies of the following in such interactions:
- Requirements revisions
- Design targets
- CAD models
- Sensor calibration information
- Test procedures
- CAE simulation procedures.
The scope of many of these topics is far too broad to discuss easily. But more importantly, any decisions and agreements must be captured in the digital thread as the new source of truth – that everyone can be informed of and have access.
In it for the long haul
Ideally this would be the end of our discussion, the data has been found, it’s up-to-date and by all accounts it represents the physical product and how it will function, allowing comprehensive verification of the vehicle. Unfortunately, mistakes and errors can still occur in the real-world. It may have been an unforeseen operating situation, a faulty part from a supplier or just regular maintenance of the vehicle that the customer missed. Regardless, the vehicle manufacturer must review the situation, finding the source of the problem to avoid repeat problems.

For such situations, including recalls and legal procedures where millions of dollars are on the line, it’s crucial to know what was verified and tested, what were the results, what test equipment was used, were the sensors and equipment calibrated. The verification management process stores all data and information digitally and provides a thread to all the relevant information, instead of the disparate laptops, network storage devices and odd paper documents of verification processes in the past. So as memories start to fade over time, these digital links are maintained and provide direct access to all information as needed.
Where today meets tomorrow
Everyone who develops and engineers a product goes through a verification process. As new engineering challenges present themselves in the automotive and transportation industry—including electrification, autonomous drive, ADAS and vehicle connectivity—traditional practices and processes cannot keep pace. These new challenges are far too unforgiving. Vehicles must be developed quickly while meeting all requirements to ensure safety, durability and performance. This is especially true as vehicles incorporate more assisted drive capabilities and the move towards electric cars.
The industry can no longer afford to let the market discover problems that could be identified earlier, through other means. Fortunately, new, digital thread-based verification management processes provide the necessary structure to manage product verification process as never before. Siemens Xcelerator portfolio offers such a solution, providing an efficient, powerful and stable verification management solution with high fidelity and integrity. In the next part of this blog series we will take a deeper look at Siemens’ verification management solution and highlight the value it can deliver to automotive companies as they adapt to a new regulatory and technological environment. This truly is technology of tomorrow, available today!