Podcast Transcript: Additive manufacturing – an industrial revolution (Part 4) – materials solutions
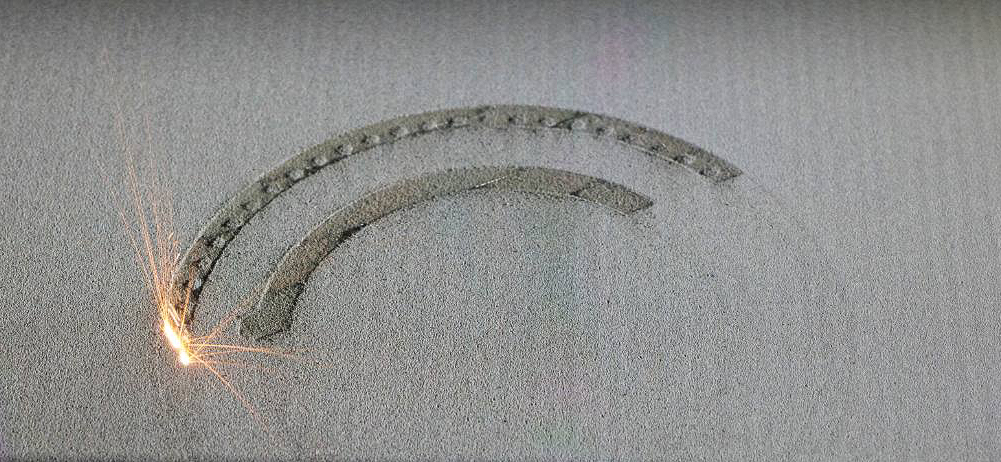
In our recently published fourth podcast of our new additive manufacturing podcast series, we are joined again by Tad Steinberg, manager of Siemens Energy’s Additive Manufacturing (AM) business development, and Trevor Illston, Chief Technical Officer for Materials Solutions Ltd, a print service shop that Siemens acquired in 2016.
Read the transcript
Ashley Eckhoff – Welcome everyone to Episode 4 of the Siemens AM Podcast. This podcast is sponsored by the Thought Leadership team here at Siemens. As you may know by now, my name is Ashley Eckhoff and I’m a member of the AM software team here at Siemens.
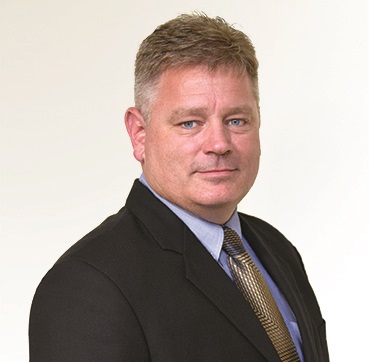
Today we are continuing our conversation with Tad Steinberg and Trevor Illston from Materials Solutions. If you haven’t yet listened to episode 3, I encourage you to seek that out as we began our conversation with Tad and Trevor. But for those who are coming in cold, Materials Solutions is a print service shop for whom Siemens acquired a majority stake in 2016.
Trevor is the Chief Technical Officer for Materials Solutions Ltd. and was one of the three founding members of the company, and Tad is the manager of Siemens Energy’s Additive Manufacturing (AM) business development, marketing and sales.
Welcome back, Tad and Trevor. Just to review where we left off in our last episode, we talked about the history of Materials Solutions and what services you provide. Then we got into what your customers are doing with additive, how you document your process for your customers and eventually a discussion about the future at Materials Solutions.
I’d like to start today by expanding upon that last subject. You guys mentioned in episode three, that one of the reasons for your expansion is the desire to add new materials or capabilities to your services. How difficult do you find it to add a new machine from a different vendor or new materials to your process? I hear from other companies that it’s a pretty arduous thing in having to go through the whole learning process again to figure out how to make that new material or machine function. Do you guys find that same thing? Is it difficult for you, or do you have it well down?
Trevor Illston: It’s a mixed bag, in a sense. Bringing in a new material of the same type – obviously depending on the alloy – can be more straightforward. So, we’ve processed a lot of nickel superalloys and, depending on the alloy, adding another nickel superalloy can be relatively straightforward. But if you’re doing titanium or aluminum, it’s a very different process.
They’ve got very diverse characteristics when they’re in the additive machine. So, you’ve got to learn how they respond to the additive process to optimize your process specifically to suit those material types. And, in terms of machines, moving from one machine vendor to another machine vendor does take a lot of learning. You get to learn the characteristics, challenges and the good aspects of each machine type. And for a new one, it will probably take six months to a year to understand how that machine works, even when using the same material characteristics.
Ashley Eckhoff: Have you found a lot of variation between machines of the same type and from the same vendor? I know in the early days, I’d hear people say, you know, “We got this new machine from so-and-so. It’s supposed to be exactly like our old one, but the firmware is different and now we have to go relearn everything all over again.” Is that still the way things are, or are you guys finding it to be a little easier now?
Trevor Illston: You still have that process. So, you must make sure that you’ve got your machines to a consistent standard going forward, be it the software, the setup and the calibration to guarantee that you’re getting consistent results out of the machines. So, if you’re not careful, you can find it a problem. But we do take that into account when we’re setting up any new capability.
Ashley Eckhoff: Do you guys have a consistent recalibration process time period?
Trevor Illston: Yes. So, we’ve got a preventative maintenance process in place. We do regular checks on some of the key process variables and get the machine checked on a consistent basis from the OEMs as well to ensure that they’re performing as we expect.
Ashley Eckhoff: Okay. You know, on the software side, we talk much about industrialization of additive. It sounds like what you guys have done is taken the additive process and made it into an industrial process where you can print quality parts repeatedly. Can you give us a little bit more insight as to what it took for you as a company to get to that point, to where you could do serial production?
Trevor Illston: I suppose it took many years of hard work and lots of learning to get to that point where you’re doing serial production, but it’s putting in place a series of software tools to control and manage the manufacturing of the process and to record the output. So, it’s all done in a controlled and repeatable fashion. And I suppose the new part of the journey that we are on is trying to simplify those software processes. In the early days, the software processes were all independent. They didn’t talk to each other and you spent a lot of time transferring your information between one tool and the next tool. Then, as the technology progressed, the software has moved forward considerably, and we’re getting to the point where we’re trying to simplify the software tools and packages that we use so it’s very simple to transfer it from one part of the process through to the next part of the process. You get a seamless transition and you don’t get all the translation errors or problems that that can cause.
Ashley Eckhoff: Yeah. That’s something we’re working hard on, on the software side. We’d love to see a world where STL files are never, ever seen again.
You talked about materials earlier. In the early days, one of the knocks against additive was that there was a very limited set of materials. But, you know, over the last couple of years, it seems like I keep seeing more and more materials being added to the set of available materials to use. Are you guys keyed into what’s going on in the materials world? Are you keeping an eye on the development process and research? And, how do you deal with new materials when a customer asks you to print something you maybe haven’t dealt with before?
Trevor Illston: Yes, we very much do keep an eye on it. I suppose one of the unique things about Material Solutions – certainly when we started – is that we identified that there was a very limited palette of materials. So, we quickly got into developing materials to suit the customers’ needs. That is one of the bases that the company was founded on, and we continue to do that today. There is a massive explosion in the range of materials that are being developed out on the market, which is great for the technology, but it can also be very difficult to keep up with it. Therefore, we are targeting our resources on materials that suit our customers’ needs, because it requires time and resources to take a new material and get it working well on the machine and qualify it for customer acceptance. So, we have to be very selective about which ones we do choose in moving forward.
Ashley Eckhoff: Have you guys seen much about digital materials? I hear about that periodically, where people are talking about using a base material but altering the behavior of the material through printed structures. Do you guys see that sort of thing yet or is that still kind of on the horizon?
Trevor Illston: That’s still really on the horizon for us. The industries that we work with are generally relatively conservative, so it’s standard materials that they understand now. But that sort of thing is interesting for the future. Yes, definitely.
Ashley Eckhoff: So, in discussing the evolution of the industry as we have here, what do you think are the catalysts that are driving the adoption of additive manufacturing? And maybe even what do you think are the impediments? What do you think needs to happen to really make this thing production-ready for the world as opposed to unique companies like you guys that have done all the hard work?
Trevor Illston: I suppose one of the catalysts we’ve found comes back to climate change and the need for more efficient processes, especially for industrial gas turbine and narrow engines, or aerospace in general. So, it was the need by regulation to reduce emissions and fuel burns, and things like that were pushing people towards more innovative ways of designing their components. Therefore, additive was an enabler to allow them to come up with designs they couldn’t manufacture conventionally. That was one of our first main drivers.
I suppose the continued reduction in cost of the process has allowed that to accelerate because it opens a broader range of components that additive could be applied to.
Tad Steinberg: So, just to add to that, one of the hurdles that I am seeing – both internal and external – is the mindset of taking on a new technology and the unknown as well. I think additive will continue to develop and define through attrition, by the retirement of the folks that approve the designs or approve of the manufacturer, going towards CDR – whatever that might be. And I’m finding that they don’t like the way that something looks, so therefore they do not pass it. So, I think those are some hurdles that we must get through from a traditional mindset to continue to advance additive to make it global.
Ashley Eckhoff: Yeah. I think that kind of goes into confidence. Right? I think we’re still in this place where a lot of people don’t quite have confidence in the things they’re seeing because they’re so unique and different. From what we’re seeing, the more proof points we get in the market to show that these things are working in the way they’re intended and delivering the benefits expected, it helps in that regard.
Tad Steinberg: Yes.
Trevor Illston: Yes.
Ashley Eckhoff: So, we kind of talked about this earlier, but to circle back around to it, I had a conversation with Aaron Frankel about how hard it is for the companies we talk to, to get good, quality output from their additive processes. You guys seem to have a pretty good handle on that. Is quality something that you’ve sort of baked into your process at different steps? What do you do to make sure that the prints you’re making and delivering to your customers have the quality that you and they need?
Trevor Illston: I suppose quality has been very important from the early days of Material Solutions. Our initial customers were aerospace focused. So, over the years, we have built our quality system to meet with the intention of meeting their requirements. We started from the point that you won’t naturally get quality out of these machines; learning the characteristics of the machines. You’ve got to control them well. You’ve got to put all the monitoring and checks in place, including preventative maintenance of the machines, as well as the complete manufacturing process to get to a point where you’re consistently and reliably delivering quality parts.
Ashley Eckhoff: Have you found that software plays a role in that?
Trevor Illston: Yes, very much. The software has got to be providing a good input to the machines. In the early days of additive manufacturing, the slighting software and the checking software through the machines and the actual algorithms in the machines were not as good. So, you had to spend more time checking those before printing anything. Now, the software has moved on and is very critical when it comes to the production for collecting the data and monitoring the process to make sure that you’re achieving what you expect in the process.
Ashley Eckhoff: I’m pretty sure I heard you say earlier that you guys do things like non-destructive testing and quality assurance at the end of the process.
Trevor Illston: Yes.
Ashley Eckhoff: And then there are certifications, right? Can you describe to us the certifications Materials Solutions has and what those mean for your customers?
Trevor Illston: We have a range of certifications. We started out with ISO 9001 and quickly got the aerospace AS9100 approval, which we have been developing over the years. Also, very recently we’ve got the NADCAP AM approval. So, we’re one of a handful of companies in the world that has that, and we’re continuing to expand our approvals, including customer-based approvals.
Tad Steinberg: To add to that, if you think about some of the other industrial additive manufacturing specifications that are out there, such as AMS7003, and other additive-specific safety specs, we keep abreast of all of those and we understand what they are asking. We understand how they apply to us, and where we are in the journey in regard to things like statistical process control and things that AMS7003 asks for. Yet, there isn’t enough data to be able to actually adhere or abide by those particular requirements.
Ashley Eckhoff: When you guys approach a new requirement that you want to achieve – a certification – is that customer-driven or do you guys try to head those off at the pass? How do you handle picking out which ones you go after next?
Trevor Illston: It’s usually a bit of both. We’re looking at the landscape for the certificates and the approvals to see which ones are likely to be coming up and how they might be adopted by the industry. And if we think they’re going to be the ones that are relevant to us, then we’ll go through the process of doing a GAP analysis and see how it fits with our current quality systems. Then, we need to close those gaps and get us to the point where we’re fully compliant.
Tad Steinberg: And that also adds to our internal documents that we have that are set in place. They’re internal documents that we’ve generated to control our own products and process for those products. And those are all set and maintained and updated as it makes sense.
Ashley Eckhoff: All right. Very good. So, if we turn our attention to farther out in the future, where do you see the additive business going? What would you expect to see, and what would you put on your road map? Get out your crystal ball and give us a little idea of where you think we’re all going to be and where you’ll be five years from now.
Tad Steinberg: From a tactical perspective, in less than five years, I think it’s more of the same. It’s continuing to educate customers. It’s continuing to develop the additive mindset and capabilities throughout advanced manufacturers throughout the world. Strategically, as we move forward, I think Material Solutions will continue to grow and thrive. Part of the reason we built a facility in the UK was to expand, and we’re not quite at full capacity from a machine-perspective. The US will be somewhat similar. I think the strategic plan is to continue to grow. Again, that’s not short-term. I think five-plus years’ is a good number to say, strategically.
I do think we’ll grow, but we’ll only grow at a level in which industry and business will permit. What we would like to do is be able to see what customers are doing and where they’re going, and see if it makes sense and it fits into our portfolio to be able to service those customers from that perspective.
I don’t foresee – at least, short-term – for us to get into anything other than what we are currently doing: powder bed fusion. That’s what we know. That’s our core. And I don’t think we’ll get into other technologies such as a directed energy deposition. Maybe polymers, but I don’t foresee that in the near term. Trevor?
Trevor Illston: It’s the technologies that we are constantly evaluating and looking for business opportunities. But I agree. You know, in the near term, we’ll be sticking to our core, which is the powder bed laser fusion, and continuing to expand those sorts of the offerings and, hopefully, the markets that we offer it to as well.
Ashley Eckhoff: That sounds awesome and it’s a good note on which to end today’s episode.
We would like to thank both Tad and Trevor from Materials Solutions for joining us today. These two episodes have been very informative. I’ve enjoyed talking with you guys again. Of course, I’d also like to thank the Thought Leadership team here at Siemens who sponsors this podcast.
If you missed the previous episodes of our podcast, they are available for download wherever you found this one. And, if you like what you heard here, please leave us a comment or subscribe to the podcast. That tells us that you like what we’re doing and would like to hear more.
You’ve been listening to the Siemens Additive Manufacturing podcast. Thank you very much for joining us. I’m Ashley Eckhoff, and I’ll see you next time!
This is the fourth podcast transcript in this series on additive manufacturing. Look for more podcasts in the near future.
For more information:
Listen to the fourth podcast in this additive manufacturing series to learn more about the topics discussed in this blog, including designing for additive manufacturing (DfAM), the differentiation of internal and external customers, and the future of materials solutions.
You can also access this podcast via Apple, Stitcher, Spotify, Castbox, TuneIn or Google.
Also, listen to podcast01, podcast02, podcast03 and podcast04 in this series.
Siemens Digital Industries Solutions Software, through its Xcelerator portfolio, provides a breadth of simulation skills to help engineers with many capabilities, including simulation for build orientation, optimization and macro and mesoscale process simulation.
About our experts:
Tad Steinberg – Manager of Siemens Energy’s Additive Manufacturing (AM) business development team and more than 20 years of aerospace experience.
Trevor Illston – Chief Technical Officer for Materials Solutions Ltd