The synergy of simulation and additive manufacturing
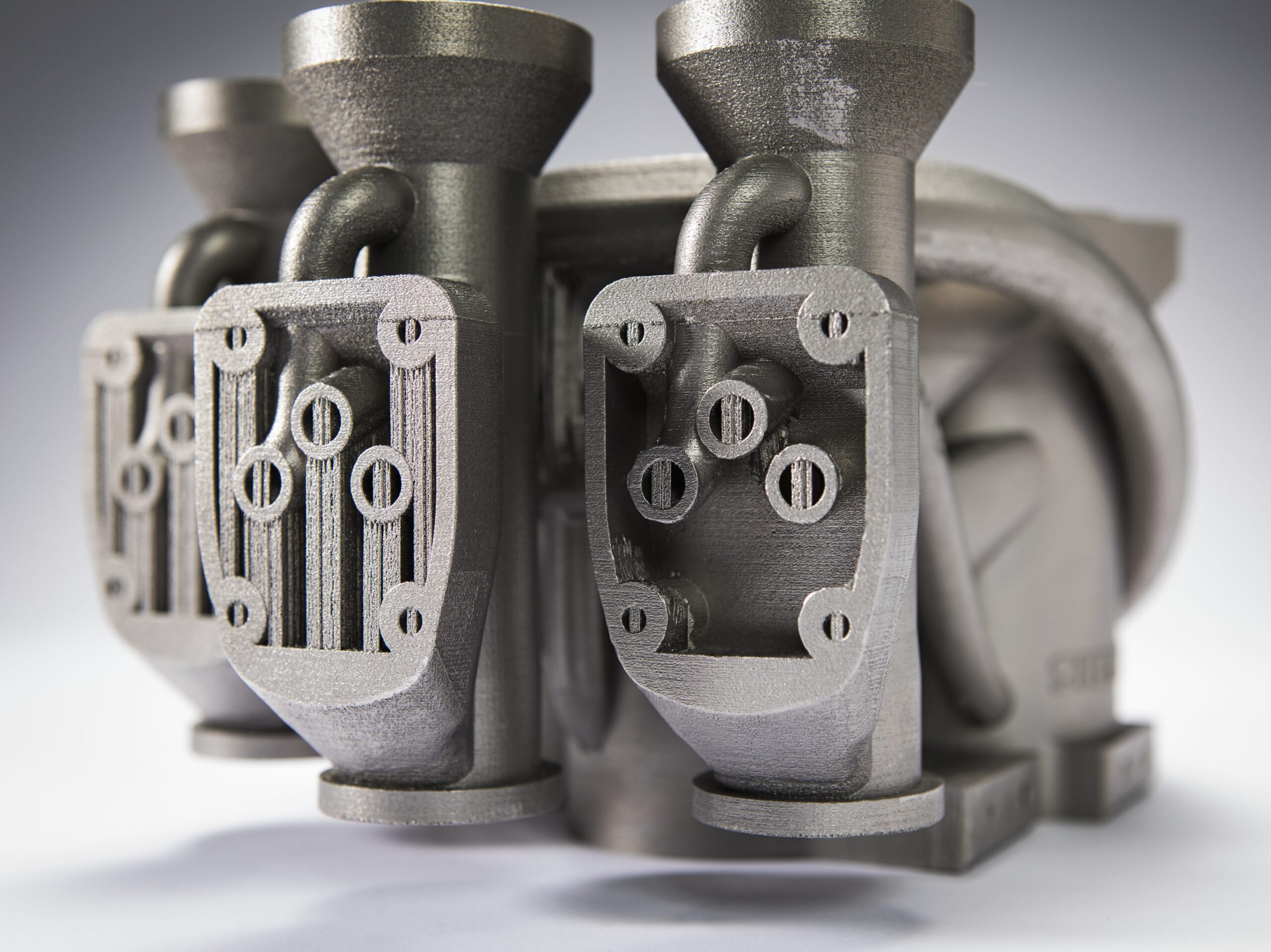
FormNext may have already passed, but with so much to learn about industrial additive manufacturing (AM) it might be time to revisit some of it or take a first look at what this manufacturing segment has to offer. Blake Snodgrass and myself will be highlighting some key presentations from Siemens Additive Manufacturing Summit at FormNext Connect, for those looking to learn how AM is changing industrial manufacturing.

One key presentation is Empowering generative engineering for AM through flow topology optimization, presented by Julian Gänz, from Simcenter STAR-CCM+ team at Siemens Software
Simulation and additive manufacturing, as concepts, have been tossed around in the engineering spaces for years. Simulation enables a manufacturer’s knowledge of how their products will perform in the real world or even how efficiently the production can happen. And additive manufacturing provides access to geometries once impossible, either completely or only with exorbitant investments of time and capital. Apart, each contributes to innovation, but together they become the innovation.
This synergy is exemplified by multiple design practices, some of the flashiest are within the design stage of development – topology optimization, generative engineering and bionics.
Topology optimization in its simplest form is the practice of shaping a predefined part into one that better fits the design requirements, this is most well-known for light-weighting parts. By stripping away material areas that do not contribute to the overall design requirements, mass can easily be dropped from the system. Today’s form of topology optimization is only available because of the integration of simulation and additive manufacturing – simulation handles the part requirements and AM enables the production, as many geometries found with topology optimization would be unproduceable with traditional manufacturing methods.
Generative engineering takes a step further from manual design than topology optimization, allowing simulation software and artificial intelligence to design a part based on the defined requirements. This process not only creates innovative geometries, it does so in far less time than asking an engineer to find a solution. For example, when EDAG was faced with solving cooling issues in their battery packs for an electric vehicle, instead of tasking an engineer to solve it with purely experience, generative engineering was proposed.
The inlet to the current battery cooling system split the airflow into three paths through the battery array to converge back into one outlet. The software was told how much space could be used by the design and that mass flow should be improved, as this directly impacts cooling performance. The result was a 6.9 percent increase in mass flow, but the optimized part came with other benefits as well. The pressure drop across the system fell 46 percent, leading to less strain and longer life of the cooling system and all of this was achieved in half the time it would have taken a specialized engineer to solve the problem.

Possibly the most influential change to come from the synergy of simulation and AM will be the application of Bionics. Though it has been practiced for years, using the innovations of nature’s much longer development times will be a wealth of knowledge as we solve larger and more complicated problems. Penguins have a body shape formed over millennia to provide them superior maneuverability in the water. Trees may take a whole lifetime to adapt perfectly to their environment balancing surface area between solar collection and biological costs of keeping limbs. Simulation lets engineers and designers attempt such refined designs through rapid iteration without material cost and additive manufacturing makes the unconventional geometries manufacturable.
These two technologies will be the great equalizer, both between human intelligence and nature’s variety and human experience vs. computational speed. Simulation combined with additive manufacturing can reduce development time, increase efficiency and provide innovation, as well as any combination of the three.
For more information on how these technologies are changing the manufacturing world, be sure to sign-up for the Siemens Additive Manufacturing Summit at FormNext Connect and watch Julian Gänz’s presentation on the topic. Or spend some time exploring other ways additive manufacturing is changing industrial manufacturing for the better. Additive manufacturing is where today meets tomorrow for industrial manufacturing and optimal part design.
Siemens Digital Industries Software is driving transformation to enable a digital enterprise where engineering, manufacturing and electronics design meet tomorrow.
Xcelerator, the comprehensive and integrated portfolio of software and services from Siemens Digital Industries Software, helps companies of all sizes create and leverage a comprehensive digital twin that provides organizations with new insights, opportunities and levels of automation to drive innovation.
Also, for more information on Siemens Digital Industries Software products and services, visit siemens.com/software or follow us on LinkedIn, Twitter, Facebook and Instagram.
Siemens Digital Industries Software – where today meets tomorrow.