Functionality of a porous additive material
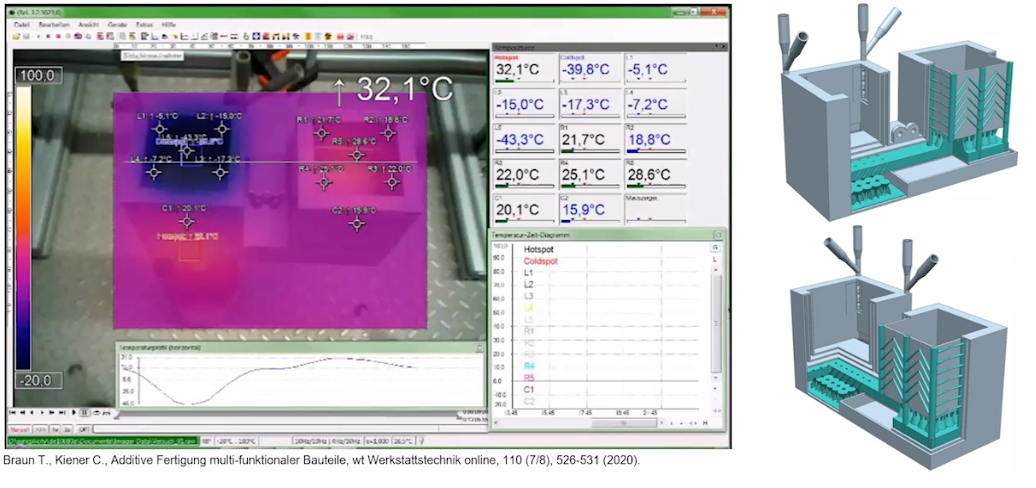
FormNext may have already passed, but with so much to learn about industrial additive manufacturing (AM) it might be time to revisit some of it or take a first look at what this manufacturing segment has to offer. Blake Snodgrass and myself will be highlighting some key presentations from Siemens Additive Manufacturing Summit at FormNext Connect, for those looking to learn how AM is changing industrial manufacturing.

In a previous installment of our FormNext review, we covered how intertwined simulation and additive manufacturing are expected to become as AM grows within the industrial manufacturing world. Without design traditions, a generatively design system can uncover solutions not easily available to the experienced engineer. And for parts with limited solution sets, the results can be reached more rapidly. But the innovative geometries available to AM practices, go well beyond the problems of today as you’ll see in Dr. Christoph Kiener’s presentation – Structural functionality pushes metal AM to a new application level, from his work as a principle expert on functional design at Siemens AG.
Many companies are looking to expand their capabilities with AM, some are doing so through expanded material sets, others through the printing technology, but one of the most interesting paths is the use of digital materials. Instead of using a multitude of materials to attain different material and structural properties, the structure of the material is altered with internal channels, lattices or increased porosity to produce different effects. This idea is already in use in some printing technology to account for the problems that come with layering a part, but Dr. Kiener’s proposition takes it even further with his example of a 3D printed heat pipe.
For the uninitiated, a heat pipe is typically a copper tube with an internal coating (the wick) used to move a working fluid via capillary action. While heat pipes are very effective, they are limited in size and thermal flux by the process for creating the porous internal structure. With AM practices, these hurdles can be avoided by altering the porosity of the wick and changing the speed at which the working fluid moves in the system. An example of the effect of porosity on capillary action can be seen below.

From there, a heat removal setup was designed to insulate one compartment while heating another. For an idea of what the internal structure would look like, please refer to Figure 2. The yellow portions of the model will be the porous metal to move the fluid through the structure while the empty spaces act as ducts for a vacuum insulation layer and to move the vapor created from the working fluid.

This design works very well through its combination of double-wall vacuum insulation and capillary action. So well in fact, ice can be stored in the compartment directly above the heating element while boiling water in the adjacent compartment as seen in Figure 3. But to really see the device in action, please visit the Siemens Additive Manufacturing Summit and watch the recording of Dr. Kiener’s presentation. There is much more to learn as well on the specifics of capillary action in digital materials as well.

Siemens Digital Industries Software is driving transformation to enable a digital enterprise where engineering, manufacturing and electronics design meet tomorrow.
Xcelerator, the comprehensive and integrated portfolio of software and services from Siemens Digital Industries Software, helps companies of all sizes create and leverage a comprehensive digital twin that provides organizations with new insights, opportunities and levels of automation to drive innovation.
Also, for more information on Siemens Digital Industries Software products and services, visit siemens.com/software or follow us on LinkedIn, Twitter, Facebook and Instagram.
Siemens Digital Industries Software – where today meets tomorrow.