FormNext presentation: How Siemens is converting the “black art” of metal AM to science
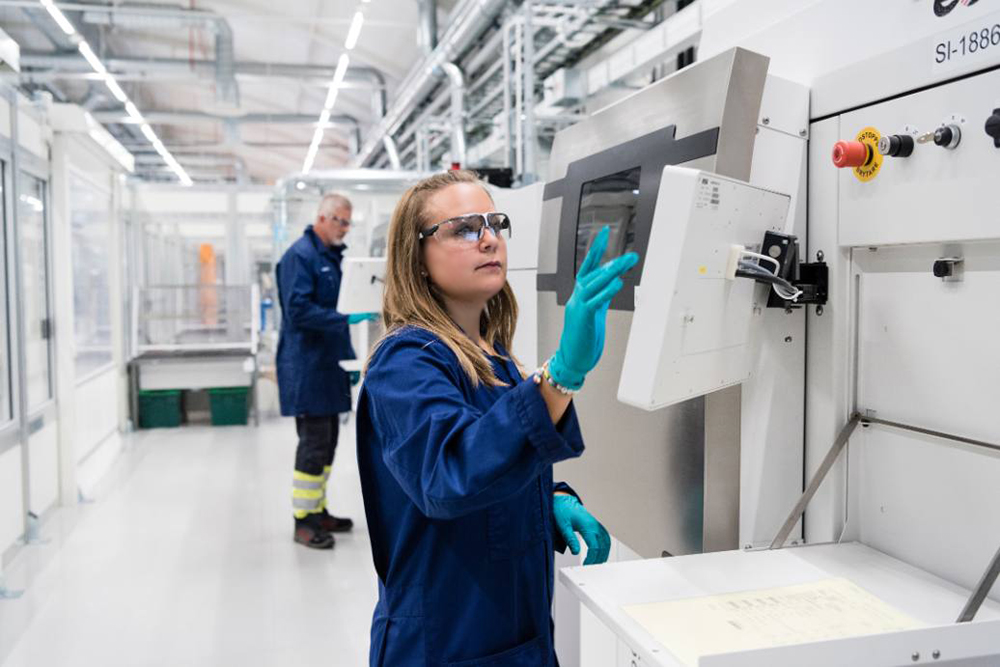
In 2020, Formnext Connect went entirely virtual, and leading this trade fair was additive manufacturing. In this context, Siemens also offered an exciting program – the Siemens Additive Manufacturing Summit – which shows how they transform the ecosystem together with their partners. This event is tailored to the respective industries’ requirements, presenting the Digital Enterprise Portfolio’s value, a holistic end-to-end solution covering the entire AM value chain.
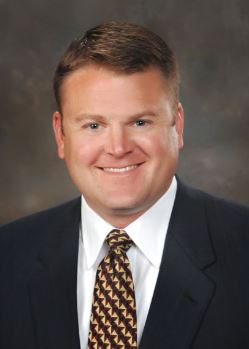
In a recent FormNext session, we have the privilege of learning from Chad Barden, the Product Portfolio Lead of Additive Manufacturing at Siemens Industry Software. He discusses Siemens AM Build Optimizer, which serially and intelligently selects one hundred unique orientations using a proprietary, direct simulation method to orient the part for maximum dimensional compliance while minimizing the chances for build failures.
Additive manufacturing (AM) engineers comprehend the challenges with printing parts using metal powder bed fusion. Process simulation identifies problem areas, while engineers will use a broad spectrum of parameters to battle common problems, with various success levels.
There’s pressure to reduce build failures in metal powder bed fusion. Also, there is a mastery of the black art of printing parts and metal. Siemens intelligent software solutions assist in reducing build failures to a science with a simple software-focused workflow. Therefore, it’s essential first to assess an engineer’s depth of AM knowledge.
Additive engineering knowledge and expertise
The additive engineer learning curve includes:
Master – They are beginning to use simulation to tune various process parameters to solve issues, including shrink lines, distortion and porosity surface quality. Their first article failure rate is less than 20 percent. They understand the additive process and appreciate the value of proper orientation as a crucial factor in mitigating thermally-induced distortion. They are typically heat-treating or stress-relieving parts while in the build plate to achieve improved results.
Journeyman – This engineer has less frequent article build failures but is still experiencing a 40 percent or less failure rate when building a part, or group of parts, for the first time. The journeyman is more advanced in nesting geometries together while concerned about the surface quality and post-processing management. They still largely use supports to fix build problems but are also adjusting z-orientation to alleviate recurrent crashes.
Apprentice – This engineer tends to have frequent build failures with first article printing, with a failure rate greater than 40 percent of the time. They use support strategies to try and solve these failures without much success.
The additive build preparation process
So, the process begins when designing the CAD part with AM in mind. When setting up and orienting the part, the engineers know it’s essential to invest in simulation software to identify build problems before spending valuable print time on a failed build. Unfortunately, accurate build simulation takes time. Therefore, sometimes it can be 24 hours later to receive information concerning a failed build, which means going back to the drawing board to reorient and resubmit the part and repeat the simulation process. Sometimes this cyclical process can take several iterations before the simulation communicates that the part will provide the results needed for a successful print.
Once the desired orientation and support are achieved, the engineers can optimize the scan path and machine parameters to increase print quality. Finally, everyone must submit all this information to the build processor, which translates the instructions into what the printer will understand, and the print begins. However, even utilizing all these tools can result in a high failure rate relative to other traditional manufacturing processes. Subsequently, this process may still result in reorientation and resubmitting of the part, which can even happen with master engineers.
Listen to Chad’s presentation to gain further knowledge of the manufacturing challenges in How Siemens is converting the “black art” of metal AM to science.
Siemens Digital Industries Software is driving transformation to enable a digital enterprise where engineering, manufacturing and electronics design meet tomorrow.
Xcelerator, the comprehensive and integrated portfolio of software and services from Siemens Digital Industries Software, helps companies of all sizes create and leverage a comprehensive digital twin that provides organizations with new insights, opportunities and levels of automation to drive innovation.
Also, for more information on Siemens Digital Industries Software products and services, visit siemens.com/software or follow us on LinkedIn, Twitter, Facebook and Instagram.
Siemens Digital Industries Software – where today meets tomorrow.
About our expert:
Chad Barden, Product Portfolio Lead of Additive Manufacturing at Siemens Industry Software, has a strong entrepreneurial bent, with a foundation in financial services. His analytical abilities, intuitive insight and excellent communication skills have been the cornerstone launching exciting companies. Strategic deal making has emerged as one of Chad’s core strengths and he is well versed in the art of conducting complex negotiations that result in lasting business relationships.