Accelerating tomorrow’s machine shop with additive
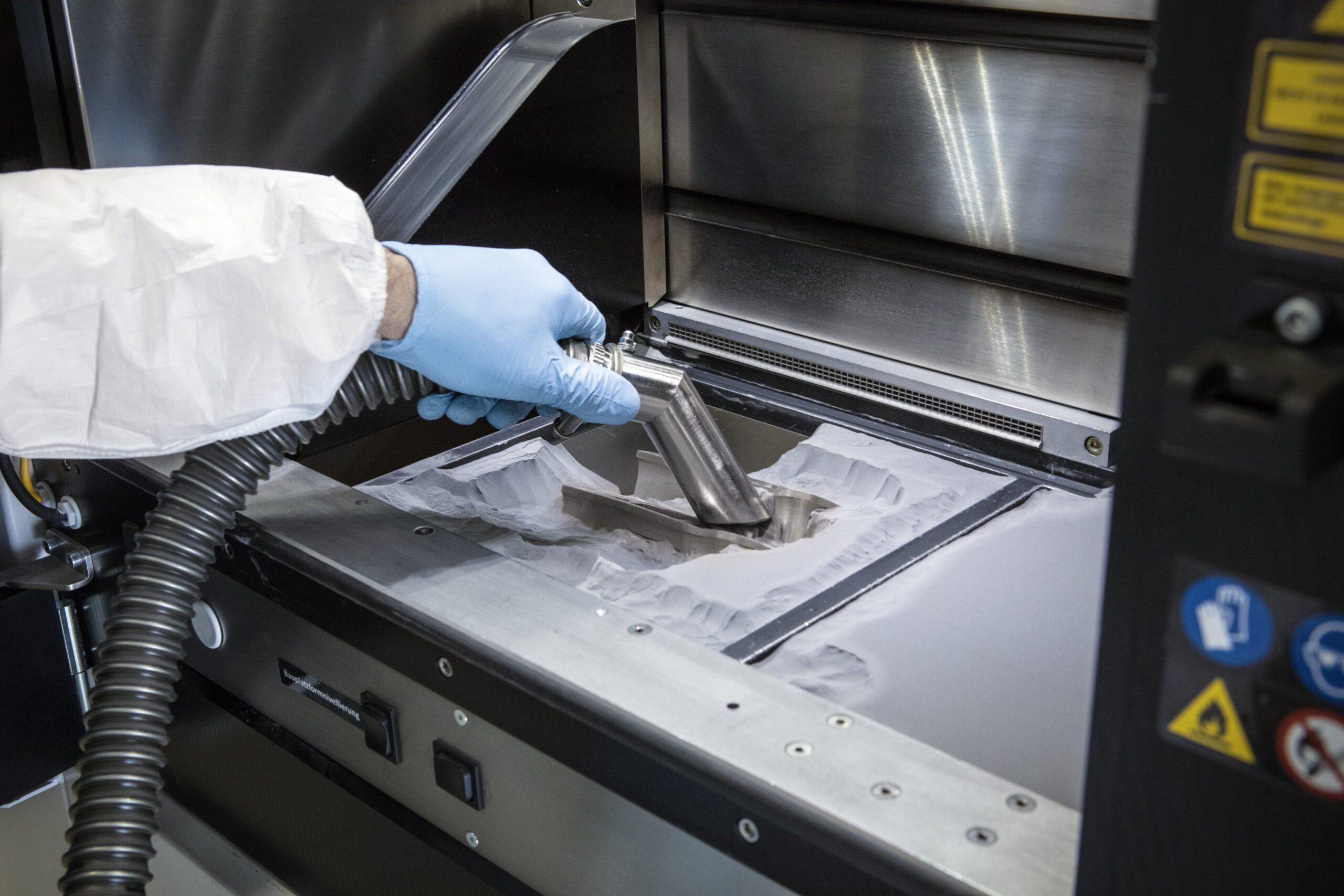
The machine shop is the most important stop on a component’s journey from concept to usage, and unfortunately it is one of the departments most often overlooked when talking about additive manufacturing (AM). AM technologies are regularly positioned as replacements to the machine shop – if I can make any part with one machine, why wouldn’t I simplify the process to do so? The problem with this thought process comes from the technology itself, AM devices are not capable of everything a machine shop does to produce valuable products. This could be precision features to join AM parts with existing assemblies or surfacing techniques for a mirror finish on an otherwise dull part.
Regardless of the reason, AM is not fit to replace the machine shop. But, AM can augment a machine shop. Much of the awe around additive comes from the flexibility of the solution. For traditional manufacturing methods, customization is unattainable for most and extremely expensive for a few, often requiring a high investment in new mounts, new molds or even a completely new machine. An integrated use of AM and traditional machining aims to solve this dilemma. But getting there will require a digital approach, to more easily understand the delineation between AM’s strengths and the strengths of traditional methods.

Digitalizing a machine shop workflow will be paramount as more design houses start implementing topology optimized components and organic geometries and not only because it will require optimizations for strictly additive process. Digitalization will enable streamlined production to make traditional manufacturing methods work in tandem with AM. A digitalized workshop enables hybrid printing – combining AM and CNC. It enables on-demand specialized components for complex processes. And it reduces the effects of shop downtime through greater machine management.
A hybrid printing approach (of AM and CNC) could be implemented to replace pure milling operations. Instead of needing to purchase solid blocks of material and creating undue scrap from material removal, the general shape could be formed through the AM process with traditional milling and surfacing to finish the part. Simulating this procedure before-hand also enables optimizing the tool paths for both processes – minimizing scrap and production times. Working from a digital environment requires less extensive knowledge than drawing from experts to understand how specific tools interact for a given component.
Or when specialized components are being produced in a small run, it is now profitable to commission a specialized bracket for standard machining. Required dimensions can be lifted from the final product for a perfect fitment. The required part can then be printed onsite and possibly used that day. Depending on the application it may also be important to use non-abrasive materials or plastics which also minimize weight if attached to moving systems.
Onsite AM limits the necessity of replacement invitatories, down machines are directly linked to lost revenue. That leaves many companies to hold inventories of replacement parts, even if they are bulky and rarely malfunction. Instead of relying on vast inventories, AM can be used to print the required part on the spot. That leaves more room on the shop floor while retaining uptime. A similar practice has been implemented by Airbus to service their older fleet instead of holding an expensive inventory.
The solutions for AM as a part of everyday manufacturing practices are numerous, but to get there machinists need the power to use these solutions. That is where Siemens’ Xcelerator portfolio comes into play. As an end-to-end solution from design to production, traceability is retained for the applications that need it – often aerospace and medical. It also means making manufacturing changes is even easier because the requirements created earlier in development are still bounding the design. For complicated AM designs, this can be invaluable for small revisions – especially when parts are delivered in facet-based geometry instead of precision CAD geometries.
We have only scratched the surface of additive manufacturing’s value to the machine shop of tomorrow. To gain a wider understanding of the journey, Ashley Eckhoff, Marketing Manager for Siemens Additive Manufacturing Engineering group, gives a great overview in the webinar – Transform your machine shop with industrial 3D printing. In the later half of the presentation, you will also hear from a 3D printing representative from HP on how their multi-jet fusion printers may integrate into the machine shop of tomorrow.
Siemens Digital Industries Software is driving transformation to enable a digital enterprise where engineering, manufacturing and electronics design meet tomorrow.
Xcelerator, the comprehensive and integrated portfolio of software and services from Siemens Digital Industries Software, helps companies of all sizes create and leverage a comprehensive digital twin that provides organizations with new insights, opportunities and levels of automation to drive innovation.
For more information on Siemens Digital Industries Software products and services, visit siemens.com/software or follow us on LinkedIn, Twitter, Facebook and Instagram.
Siemens Digital Industries Software
– Where today meets tomorrow.