The effects of COVID-19 on the automotive industry – The Future Car podcast transcript
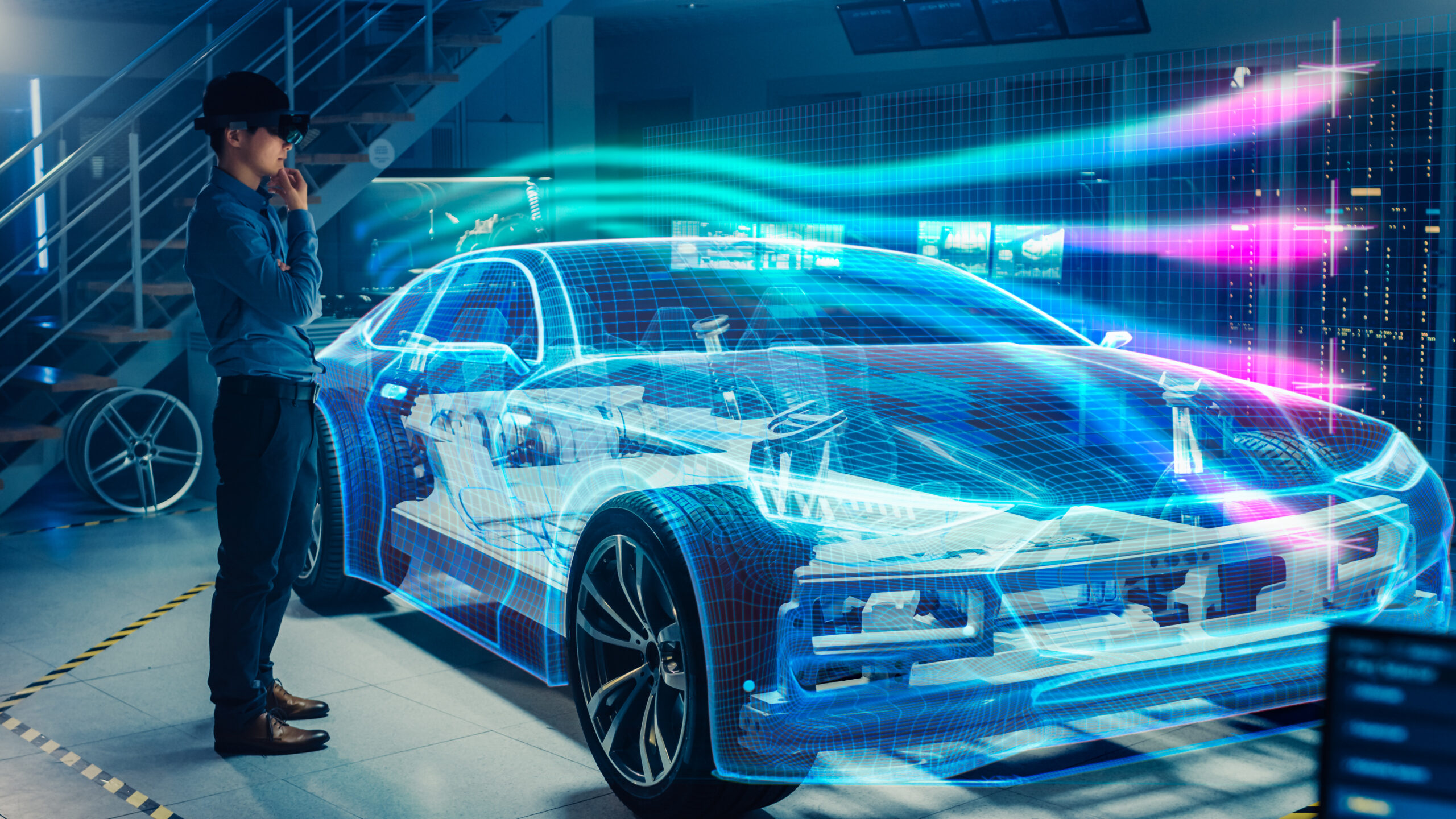
The entire automotive value chain has experienced immense pressure during the global COVID-19 pandemic. Automotive manufacturers have had to rethink how they design, verify and manufacture new vehicles. In particular, they have had to develop new ways of working while protecting the safety of their employees, families and communities.
Last year, Nand Kochhar and I discussed the many ways in which automotive companies have responded to the challenges of operating during a global pandemic. The transcript of this episode follows:
Nand Kochhar: Yeah, of course! Good afternoon, first of all, The biggest challenge, of course, is around safety – the safety of our employees, the safety of our customers, and the safety of the community overall, as a goal. So, within the A&T industry, that gets into wherever there is a production environment where people are right next to each other, people in offices. So, that was the biggest challenge: how do we make sure that all our employees are safe, all our customers are safe and people that interacted with them, their families, everybody is safe. So, specific to the A&T industry, if you take an example of a manufacturing environment in a factory, that is a huge challenge, that you can’t be working in the same environment at the same line speeds, people standing next to each other. So, you can imagine that’s a big challenge. Also, you can imagine that, while there is room for a lot of digital work, some of the things like certification, homologations, those things are done in a lab environment and you have huge dynos and other test facilities. So, those facilities had to be taken care of and couldn’t be working in the same environment. So, those are specific to the A&T industry. Those things are a huge challenge.
Conor Peick: What has helped or hindered companies in addressing these challenges? And I’m also curious if you’ve seen any specific strategies that you found are interesting or innovative?
Nand Kochhar: Yeah, sure. So, again, first, what has helped us on the humanity side, whenever there’s a crisis like this, teams just come together. And that was a good observation because all of us have a common goal of fighting this pandemic and fighting the issue. So, the collaborations – teams coming together – and cooperation at all levels. That was a huge thing on the humanity side. What has helped on the specific action items is, again, the digitalization, doing work in a virtual environment – that has been the biggest savior, I should say; it helped handling the situation. Typically, we’ve had this in the IT information technology world. However, on the other side, even in a product development environment, there’s lack which can be done remotely. And that has really been a big savior for the A&T industry at all levels, both at the supplier level and at the OEM level. So, that has struck me as the most innovative – that some of the companies were ready. They were able to send their design and engineering staff back to their own homes and work in that safe environment, obviously, with some level of adjustments in order to handle volume; that was the biggest thing, that they were able to continue the work without any major hiccups in that arena. So, that has been a huge help and, of course, Siemens as a digital industry software, that is our business, and we were there in the support role helping our customers make it through that transition of working remotely.
Conor Peick: So, the critical thing here that you’ve seen is digitalization? Would you say that’s correct?
Nand Kochhar: That’s right! Digitalization which allowed to work remotely and get a lot of things done. Typically, you’ll assume anyone doing software development, Siemens employees themselves, okay, they can work from home, because it’s a software type of work. But now, imagine we’ve got software everywhere in the automotive industry and that is a big shift over the last few years. Even guys who are doing the calibration of a product – in this case, a car; it could be an electric car, or it could be a regular car – and there’s a lot of software involved in that. Those engineers from these auto companies can go home and still kind of work from their garage.
Conor Peick: Do you think maybe other departments have had a harder time making that transition? It seems to me that software engineers might be more used to the idea of working remotely, whereas, I don’t know, if like a mechanical engineer or maybe in the verification and test side, do you think they would have had a harder time making that transition
Nand Kochhar: Yeah, take a typical example of an automotive designer, they have been able to work from home or remotely in the same fashion as the IT engineers. a CAD designer is able to access the CAD data through our Teamcenter, and they’ve been pursuing their work just like they were working in the office. So, that part of the business is there. What has hindered is what I alluded in the opening, is the certification testing, where you need to put a vehicle on a dyno, and dyno is a huge facility. And then, you have to do the test and instrumentation of the vehicle. That’s the part that you have to be back in the office, back where those test facilities are, back where the test track is. That is the kind of work which went on the back burner a little bit.
Conor Peick: Okay, right. I see. That makes sense. Okay, so then, for the customers that have successfully made this transition and are really taking advantage of digitalization, I guess, how does that help them in coming out of this pandemic stronger – or at least as strong or stronger than before?
Nand Kochhar: I think it is going to teach us a lot of lessons. And necessity is the mother of invention. People are going to find after this a lot of different ways of doing things. So, if we were able to do these things in a virtual environment, and obviously there were a lot of pluses to it, and it will shift how work needs to get done. So, there has been a paradigm shift, and it has shown us the ways of doing those things. I’ll use a couple of specific examples. Traditionally, any auto OEM has been that we need to be around a clay model even today, and approving the final designs and things of that nature. So, that means physically a chief designer and the designer and the engineers and the body engineers and the others, they need to be around the property and they need to be approving and say, “Yep, this is good to go! Let’s go cut the metal to the specification!” It’s a very good example. A lot of that technology like virtual reality and augmented reality – VR/AR – has been around and every auto OEM has been using it but the pandemic has pushed that to a next level. I’ve seen several examples of major OEMs where their chief designers are in their living room, their IT people provided them with the equipment so they can have these devices on their heads and goggles, or whatever is needed based on whether they’re using VR/AR. And now, four or five people are collaborating from their own homes or living rooms, and still making the same decisions.
Nand Kochhar: You will see that shift, the technology has been there, but we still had the mindset that it can’t be taken that far to make a final decision. And that, I’m sure, over the last couple of months has pushed people to go ahead and not delay things and make those decisions. I’m sure they are going to sit back after this, do lessons learned – hopefully, everything worked. And even if some things didn’t work to some extent, they’ll tweak that and that will allow digitalization to go at the next level.
Conor Peick: Yeah, and following on from that point, that discussion, I’m curious if you foresee a regression to kind of old ways of doing things, or do you think this change is gonna be relatively permanent?
Nand Kochhar: Yeah, I think it’s not going back to the old ways of doing things the way we were doing. 100%. As I said, everyone is going to take a look at the opportunity. So, there’s going to be a shift and it’s going to be a mix, right?
Conor Peick: Do you see these moves towards digitalization as a key part of automakers becoming more resilient to any sort of interruptions like COVID, for example, moving forward?
Nand Kochhar: Yeah of course. There are several factors to improve the resilient part of the automotive industry. Digitalization or virtual stuff is obviously one big contributor, but they’ll also be looking into a lot of other factors around the supply chain at deeper levels of the supply chain from a single source to a dual source for every commodity, and also the supply chain not only at a tier-one level, but all the way at tier two and in some cases even going where the raw materials are coming from. So, there is a lot of commonality with other industries. For example, for a pandemic type of scenario, you need to be prepared and companies will take that into account. Most companies have what they call ‘disaster recovery plan’. We have that today. I think wherever we have worked, companies have had that. Some call it ‘business continuity plan’ or a ‘disaster recovery plan’. I think those things will take a new shape and a new form because, even though we all have that and we all reacted to that, but these lessons earned from pandemic will take those to the next level.
Conor Peick: Will they become more detailed or just more extensive?
Nand Kochhar: They’ll become, I would say, more real. Some details might already be there, but I think this has, at least for me, and I’m sure most of us taught that lesson – anything could happen. So you don’t play scenarios just for the Wargaming side of it. You play scenarios of what really we would do, right? We are told, “Okay, store food for X number of days in case there is a supply chain break in the food supply.” So, this makes it more real. Hey, we rarely go and buy some canned food and keep it at home. So that’s what I mean by real. And the same thing is in the business world. What is critical in running the operations and what is the real plan for that? And I think that’s the change it’ll bring.
Conor Peick: Right. Okay, so it’s gonna force companies to really take a very considered look at the plans that they had come up with to see, “Well, were these actually effective in the case of this very unforeseeable, you could argue, situation?” And so then, from there they can mold and update their plans to hopefully better cope with something like this in the future?
Nand Kochhar: That’s right, yeah!
Conor Peick: Okay, great. Okay, so I guess, I think, we can maybe move on to taking a look at countries and how they’re trying to reopen their economies and getting manufacturing back online? So, just to start off, I’m wondering what you see as the key steps to getting manufacturing up and running again to getting it back online?
Nand Kochhar: Again, it’s going back to the safety – the safety of employees, the safety of people working, and the supply base. So, what does that really mean? That means, if social distance guidance is still there, obviously you’re going to continue to work with the local governments and CDC guidelines. Now, imagine in your plant, which was up and running and producing a car or a truck – every 58 seconds a truck was coming off line – that there’s going to be challenges. So, your stations, which are set up for assembly operations from point A to point B, they need to be changed for multiple reasons. One is the separation. So, there might be partitions between two stations as an example; you might have an optimization, that today you have a single part being shared by two workers, but you won’t be able to do that today in the going forward environment, at least till the pandemic thing is fully resolved.
Nand Kochhar: It’s also important not only on the assembly operations, but workers coming in, workers going out, shift change, there’s gonna be precautions. Coming on the technical side of the things for Siemens, our manufacturing side of the business, you do whole shaft road planning. So, that’s where Siemens can come in with that side of the shop. People need to work through their plants all the assembly operations on the manufacturing side. So, that needs to happen before you can open up your factories with safety. Also, as you said, the huge challenge for… Some plants are running three shifts. So with this change in speed and change in setup, would they be able to run all three shifts? Probably not. And that’s the kind of the lessons learned coming from China as well. Some of those plants are running fewer shifts, some of them are skipping a step within the assembly – like skipping a vehicle and producing a lesser number of vehicles in the same shift, etc. So, all those changes need to go through in the plant at the manufacturing site of the things.
Nand Kochhar: The second aspect is also on the supply chain of it. So, it’s not only at the OEM level. Just imagine the same thing, the same precautions have to be taken at a tier one or tier two supplier level and they need to be looking at their throughputs as well. And then, how does that feed into the OEM level? So that’s a huge transition to go through, and those are the steps people will have to follow in order to have a safe production up and running.
Conor Peick: Yeah, so that’s interesting. We’ve talked a lot about changing vehicle design and all that stuff, but for some reason, it had never occurred to me that manufacturing wouldn’t necessarily be able to return back to their operations pre-COVID. There’s gonna be lots of adaptations in that field as well. So, yeah, it strikes me that these manufacturers are gonna have to have a very considered and staged ramp-up of their capabilities to make sure that they are getting back to producing enough vehicles or parts if they’re a supplier, as you mentioned, while also ensuring safety as you’ve mentioned a couple of times.
Nand Kochhar: Yeah, that is going to be the reality, and every company is going to have unique situations. But that’s what they need to consider in the ramp-up curves – that’s what we call in A&T lingo. I’ll use an example: every 58 seconds or whatever that number might be for different OEMs, a car is coming off line. That number, at least, is going to change initially, or might change based on what different scenarios we’re talking about.
Conor Peick: Nand, I’m curious what new or sort of emerging technologies automotive companies might be looking into or that they could be developing that will make them more resilient going forward?
Nand Kochhar: Yeah, I think as we touched before, one is the overall automation in the automotive industry. That will come out and make it more resilient, both addressing the productivity as well as the safety side of the equation. Within automation, also, specific technologies like robotics and the assembly, and the shop floor operations. Additive manufacturing is another big one in making parts – in fact, designing and manufacturing parts. That’s a technology which can be very nimble for making prototype parts, which have been done for many many years now. But this offers opportunities to the automotive industry to take that technology to make production parts at a higher speed. Obviously, that additive is not something very new but it can be advanced. We’ve been using additive on certain materials – for example, the plastic parts or rubber parts or things of that nature and also some metals. That is the growing field that now we’ll be able to print a part, so to say a 3d printing of metallic parts, and then you can take those at a level that it could be used for the production run at rates and still be very cost-effective. So, that’s an example of additive manufacturing within the manufacturing domain, I think, will help companies to adapt and that is all in addition to overall digitalization in the product development side.
Conor Peick: Do you think this is going to push automation into test that it hasn’t really been used in before? Like, for example, I’m thinking, specifically in terms of wire harness manufacturing – I know that’s still largely a manual process for a lot of reasons, but do you think automation is gonna be given if not a first look, maybe a second look in some of these tasks?
Nand Kochhar: I think no. This is going to be the first look only, and that’s the permanent shift and the change. I used one example of virtual reality, augmented reality, which is already there. It’s not a new technology – the technology has been there – but the application of this will go to a different level, right? Because the circumstances did that. The same thing on automation, robotics, individual cell operations. I think a lot of the technology’s there, but this will push us to a different level of application of that, and it’ll again, also go back to the safety aspect of it. If workers don’t have to be standing next to each other, they have to be six feet apart, or they have to walk around a certain path, they can’t keep crossing the lines the way they were doing standing next to each other a sharing a bunch of parts – one guy was holding one side of the wire loom and the other person was doing that – that’s gonna bring all that innovation. My comment about ‘necessity is the mother of invention’, whether it’s more robotics, whether it’s more automation because that will address both things. That will address the safety aspect, also bringing the efficiency, also bringing the automation all into play, which has been out there. So, in a way, you could say it’s a huge opportunity for making that shift. But obviously, you’ve got to balance that with the overall cost and things of that nature.
Conor Peick: And speaking of opportunity – that kind of reminds me of the idea of making this new sort of complex situation and turning it into an advantage, which I know we talked a little bit about on the design side and, as you mentioned, using VR, AR things like that. Do you see an opportunity in terms of future-proofing supply chains or OEMs preparing themselves better in the future?
Nand Kochhar: Yes, definitely! I think this is going to be digitalization, virtualization at all levels. People will be taken into account. As you said, we quite often just talk about the product development side of the business. There are several examples, especially we try, as a company to address the complexity and not shy away from it. That’s our… To deliver, let’s say autonomous vehicles or electrification, complexity is multiplying or going up exponentially. So, all these approaches help us to address that complexity and make that an advantage rather than being scared of the complexity and not addressing it. I think the similar things will happen in the manufacturing operations side of the business and the supply chain side of the business. The whole huge connectivity of the data management – PLM world – into the ERP systems, having a single chain. That will be the examples of digitalization that will shift to the next level, so that we could streamline the operations without the human intervention, as much as possible.
Conor Peick: So, following on that digitalization aspect, how has that really made a difference between the success or ability of companies to thrive? For example, if you look at Tesla, lately, has had really solid results despite the pandemic, whereas others maybe have struggled a bit more.
Nand Kochhar: Yeah. Obviously, in the overall success, there are several factors. Digitalization is a huge one. The capabilities, for example, Tesla has developed in the software world are a role model. So, their ability to do the over-the-air update, they can still continue to offer feature functions to customers and generate revenues with those kind of capability are pushing the limit of digitalization not only in the design phase of it, but also in the service phase and as well as in the sales and the execution phase of it. That’s an extreme level of digitalization in all aspects of automotive business and ideation. That’s when you have the concept and design and the realization and manufacturing side of it, and then going into the service side of the business. So, that is a good example that more and more companies will be adopting those technologies.
Conor Peick: Great! And then, I guess, kind of to wrap up, I’m curious if you see any lessons that auto suppliers were able to take from the Great Recession back in 2008, 2009 that they were able to apply in this situation that’s going on today?
Nand Kochhar: Yes, I’m sure there’s a lot of lessons all the suppliers are already using and, in fact, they will be using when we transition out of that. One of the big balance in the automotive world, you’ve seen, you know, every seven to 10 years there’s a recession and then the OEMs are pushing the metal, putting so to say, ‘money on the hood’. So, what does that really mean? That means that the balance of your production capacity to demand is the biggest challenge in the automotive industry. And that was big in 2008-2009. So, there were a lot of lessons learned. So, when we are back up and running, you have to balance that both ways. First, the supply chain is enough to get the production going. On the other hand, you don’t want the production capacity far exceeding the demand, because that puts another problem that creates in the marketplace, right? So, keeping that aligned is easy to say in words, but it’s a very difficult challenge for automotive industries – or, in fact, any production supplier. So, the lessons learned on how to deal with those uncertainties, how to keep that demand to production so that we don’t get into overcapacity issues. And now, multiply that. I’m using OEM as an example, but every supplier – tier one, tier two suppliers – they’re gonna have to balance that as well and match that to the demand coming from OEMs. So, that’s a huge one. So, in ’08-’09, sure, we saw it wasn’t an issue only at the OEM level, it was a bigger issue at a supplier level – a lot of them couldn’t even sustain that level of downturn. And that becomes very important. Demand, supply, balancing becomes a very important issue and lessons learned I’m sure is going to come up very handy for A&T or for any other manufacturing business in the world.
Conor Peick: It sounds like it’s gonna require some pretty frequent and intense collaboration up and down the supply chain, as you mentioned, OEMs and suppliers all trying to work together to balance out what they’re doing.
Nand Kochhar: Definitely. Collaboration is at all levels. That’s why I said this pandemic is a huge issue as humanity, everyone, so far what I’ve observed, have come together very well. One example, as you pointed out, of suppliers to OEMs, that collaboration. So, making sure there’s open communication from what the demand is to the supply base. That’s very, very important from a business dollar and cents standpoint. But even more important, everybody’s doing the same thing in restarting their operations. So there’s got to be communications. A) as an OEM this is my lessons learned, this is what I’m doing. I’m sure they will be sharing that with their supply base. And supply base, in turn, will be sharing back how they’re approaching this issue. So that’s a collaboration at that level. The same thing within guidelines. When there are things coming, the collaborations at the local government and the federal government level, that collaboration is key and getting the manufacturing operations collaborations with employees, whether it’s unions working on the line, or just the employees working in the offices. That’s going to be huge and critical. But what I see so far, everybody just pointing the same direction, since it’s a huge challenge for everyone. So, collaboration is key and it’s going to make a big difference about how we come out of this.
Conor Peick: And again, it seems to me that having a strong kind of digital thread or digitalized solutions is gonna be really helpful in supporting that collaboration, especially between an OEM and a supplier as they’re trying to get their manufacturing or their production back online, but doing so in a managed fashion? Is that correct?
Nand Kochhar: Yes. And from a technology standpoint, digitalization is the single biggest enabler which is going to help. But I wanted to touch on another aspect of teamwork and human interactions and communication. That’s equally important when you’re handling a big challenge of this magnitude. So, digitalization – digital thread you call it – and doing things more analytical, doing things in the simulation environment, whether it’s on the shop floor, whether it’s on the product side. So, those things are gonna play a big role from a technical standpoint, and then you still need open communications and collaborations as partners. That’s equally important as well, in my mind.