Parallels between the IC and computational fluid dynamics worlds
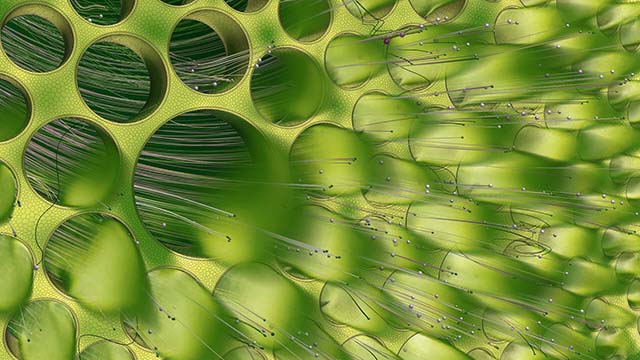
Development of a custom integrated circuit (IC) involves driving requirements through multiple model abstractions that feed over 20 design and analysis tools. This virtual environment results in a fully conceived and verified IC before the chip gets fabricated. This flow is called electronic design automation (EDA). Over the last several years, AI and machine learning (ML) techniques have been applied to improve this design flow. The virtual environment results in an IC with millions of transistors that can fit comfortably on the eraser at the top of a pencil. I have been involved in this custom IC methodology for my entire career. Knowing the process from the atomic level through creation, validation and fabrication, I am convinced that custom IC creation is one of the most complex processes on Earth. And, knowing all the things that can go wrong, I am amazed that any ICs work at the end of the day. But, they do, or else you would not be reading this blog on your phone, tablet, or computer.
Custom IC teams focus on getting that chip successfully out the door. They spend a fraction of their time making sure that the packaging around the chip meets requirements but otherwise do not focus much on how the chip is deployed on a printed circuit board. Their job is hard enough. Eventually though, another set of engineers place that IC on a board and surround it with other components and software to build a system, such as a sensor analyzer in a car. That team very much starts to worry about environmental conditions like heat dissipation and moving air over the board with cooling fans. These teams employ simulation tools that use computational fluid dynamics (CFD) methods.

Our CFD simulation definition:
“A CFD simulation involves the use of the fundamental laws of mechanics, governing equations of fluid dynamics and modeling to mathematically formulate a physical problem. Once formulated, computing resources use numerical methods to solve the equations using CFD software to obtain approximate solutions for the physical properties involved. CFD simulations are based on the Navier-Stokes equations used to describe the temperature, pressure, velocity, and density of a moving fluid.”
Siemens Digital Industries Software offers a comprehensive set of CFD tools within the Xcelerator portfolio. Because I like to learn new things, I was excited to read the blog “4 Myths about AI in CFD.” This blog walks though applying AI to CFD analysis in the context of automobile systems. It was time for me to discover what design and analysis techniques happen outside of the IC world.

Applying AI to CFD applications can be a strategic asset to companies, as it can help reduce costs and create new differentiated values. AI-driven smart solutions offer substantial benefits to CFD engineers and designers including:
- Reducing computational and operational costs by creating more designs per simulation faster.
- Enhancing the accuracy of simulations by flagging anomalies and providing knowledge base workflow assistance in the CFD process.
- Improving product performance and efficiency by creating an ecosystem to simulate, predict, and optimize the product in a seamless way.
I could swap the term CFD with EDA in the preceding benefit statement and make no other changes. The benefits are the same in both worlds. I got to thinking about some of the parallels between the IC and CFD analysis world:
- In the IC design world, temperature is a key parameter. The chip performance can degrade at temperatures that are too low or too high. Engineers run simulation on the IC at various temperature points to monitor performance. In the CFD world, AI convolutional neural network techniques can simulate and predict car cabin surface temperatures.
- In the IC world, tools employ ML techniques to spot potential problems in the design based on a dataset of real designs. In the CFD world, a history of simulation results (images) trains a convolutional neural network to identify any deviations from the normal state in simulation results. If an anomaly is detected, the neural network automatically flags the areas that should be inspected by engineers.
- In the IC world, techniques are used to simulate aging in chips to predict failure over time. In the CFD world, AI techniques can analyze simulation results from various operating conditions to predict part failure within an automotive system.
It has been my experience that the processes and techniques employed in the custom IC development flow have parallels to many engineering flows. All of these flows are now looking to employ AI to make improvements. I encourage you to take a look at AI in the CFD world by checking out this blog.
If you are interested in a sample of AI applications in the EDA world, check out my blog here.
I wanted to learn more about CFD and the use of AI within our CFD software. So I sat down for an interview with one of our experts. Listen to the podcast.