How Virtual Reality is Making Mobility Accessible for Everyone: Part 2 Podcast Transcript
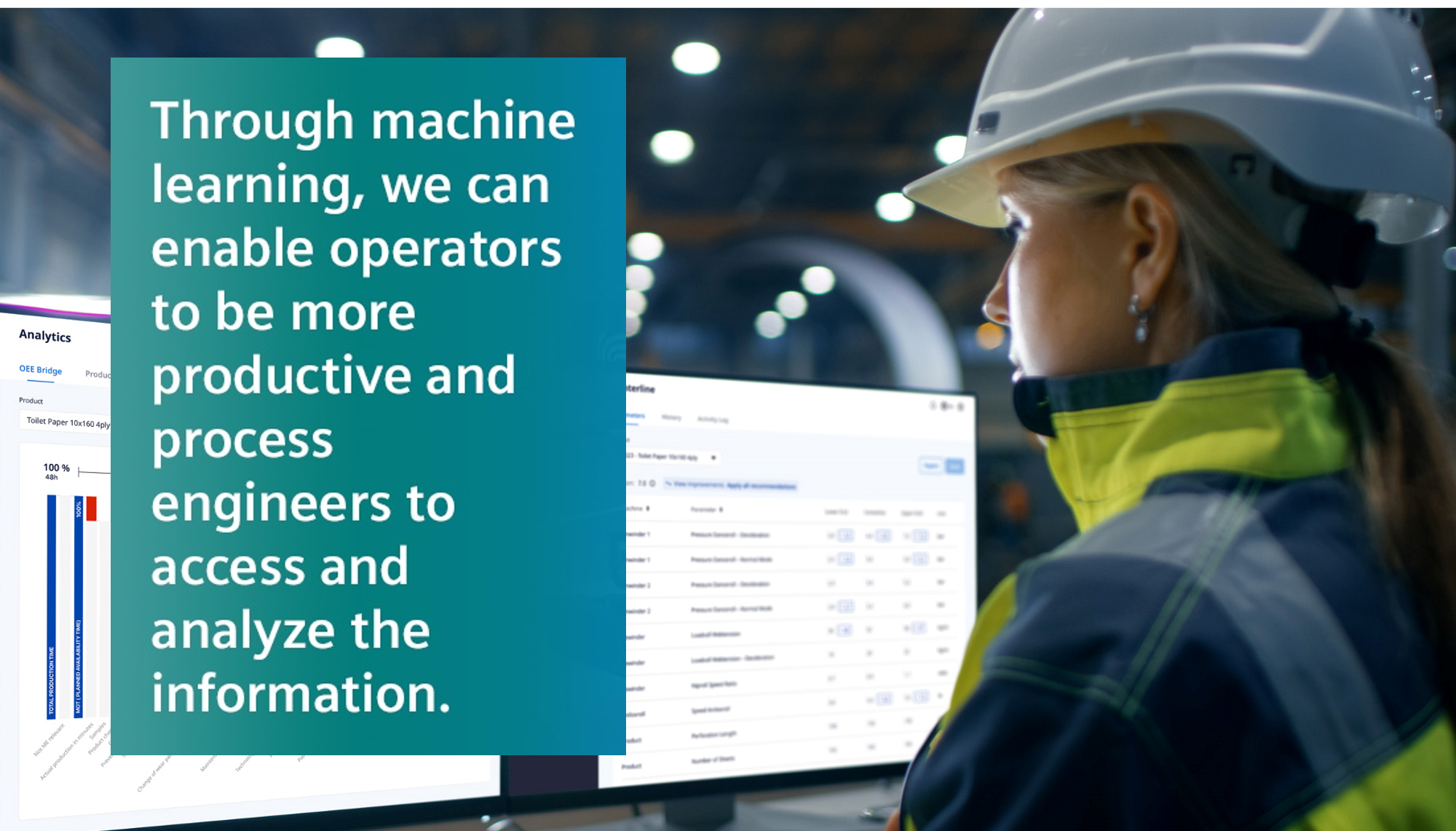
As we continue to steer towards a more mobility-inclusive future, there’s a restructuring that needs to take place. This goes for our perceptions of what is possible in terms of automated transportation, and how we make sure that this technology wave is being executed in terms of production. You might say it’s a restructuring from the factory floor up.
Artificial Intelligence is entering our workspace in subtle ways already, but the future is proving bright for AI in more direct operations too. It’s being used as a training tool for machine operators, and it’s providing valuable information that operators, designers, and managers can use to change how we do things, improving training access and efficiency along the way.
In this episode of the Women Driving the Future series, Ed Bernardon continues his conversation with Sofia Lewandowski. As a Senior UX Researcher, IoT & Industry 4.0 at FactoryPal, her work happens directly on the factory floor where she can help shape both the design and assembly process. The virtual environment she’s created has paved the way for accessible mobility for the masses.
In this follow-up episode, we’ll learn the different mindset around creating vehicles versus establishing the groundwork for building better, more accessible vehicles. She’ll share what she’s learned from working remotely during the pandemic, and how it may be shifting the future of how we work. You’ll also hear her perspective on women working in the software and automotive industries.
This is the transcript of the episode.
Ed Bernardon: Welcome to the Future Car Podcast. I’m your host Ed Bernardon, from Siemens Digital Industry Software.In many ways you can think of city streets to be much like a factory. But instead of moving parts around to different factory workstations, we’re moving people and packages around from place to place.” There are a lot of commonalities between what happens on the automated factory floor, and what happens with autonomous vehicles on city streets.
In part one of our interview with our guest Sofia Lewandowski we discussed her past work at HFM designing autonomous vehicles and making them better suited for the disabled. She now works for FactoryPal, where they are digitizing the factory floor. In this follow-up episode we shift gears from city streets to factory aisles as we learn about the mindset when utilizing AI on the factory floor. Sofia also shares what she’s learned from working remotely during the pandemic as well as her perspective on women working in the software and automotive industries.
Sofia, welcome back to the Future Car Podcast.
Sofia Lewandowski: Hello, Edward. Thanks for having me. (insert from interview part 1)
Ed Bernardon: Well, let’s move from autonomous vehicles to the factory floor and talk a little bit about what you’re doing now at FactoryPal. I looked at their vision, FactoryPal’s vision, and it’s “To revolutionize manufacturing by synergizing human expertise and digital intelligence.” What does that mean “to synergize human expertise and digital intelligence”?

Sofia Lewandowski: Basically, the concept of FactoryPal is to enable machine operators on the shop floor to be more productive and to achieve improvement in efficiency by using our recommendations in the app for the machine settings. So, basically, we would recommend, in the app, what machine settings they would need to use to optimize the workflow of the machines so that they have less downtime, less speed losses, and can just do the right settings to the machine. We actually also have a couple of apps that we are working with. It’s not just this app that gives the recommendations but also an app where operators document losses, such as downtimes and speed losses, and with the input of the users, we can enable operators to be more productive and also for process engineers to have this access to the information from their machine operators and analyze and optimize the machines. So, we work with the input from machine operators and through machine learning. We give them every time recommendations for the right machine settings.
Ed Bernardon: What kind of machines are we talking about here?
Sofia Lewandowski: Production machines. So, we are working with our customer, the customer produces a specific product, and we have their lines, production lines with different areas. On these lines, sometimes what happens is that there are a lot of different products that have been created on these lines, each product would slightly differ from the previous one, operators would need to try out different settings. It will be try-and-fail but with our recommendations for every run, they are getting optimized, and give the best recommendations for the operators.
Ed Bernardon: So, AI and machine learning is applied in trying to achieve these goals to optimize the interaction of the human and their production machines. How is AI used in this application?
Sofia Lewandowski: At FactoryPal we utilize machine learning, which is the first milestone that gives us an output recommendation for the machine settings, as I said, and the algorithm continuously improves with next runs. So, it’s difficult for machine operators to figure out all the machine settings for the products, we provide recommendations to a piece, and the piece can apply or decline this by giving their feedback. The machine learns best settings for the next time.
Ed Bernardon: And then the human or the operator will give feedback and say, “Ah! These settings were better, they weren’t,” or it actually monitors the equipment and actually tells the operator if it’s operating better or worse.
Sofia Lewandowski: I would say two different kinds of operators, very experienced ones that already worked in the production from 15 to 30 years. They have all these settings in their mind but still have to try out a lot of times. And there are also inexperienced, new machine operators, younger ones, new generation, next generation that we are trying to support. And of course, without the help of experienced OPs, for them, it’s a little challenging, especially in the beginning to set up the right settings. That’s where we use the input from experienced operators who would decline some of the recommendations and provide feedback, and our software would learn the best settings for the next round from the feedback.
Ed Bernardon: Well, let’s imagine you have a new operator, a younger operator, hasn’t had too much experience running a particular machine, and you have two choices: you could get someone with 30 years experience to help them, or you could have let’s call it an AI assistant. How would you compare those two? Because having someone that’s very experienced help them, that’s the traditional way. You think they’re equal, same speed, slower speed?
Sofia Lewandowski: Even experienced operators, they still need to try settings out and see what works best. Sometimes, of course, it happens that new OPs don’t always have the supervisor on their side, and they need to contact shift leads maybe or ask any other operators who are on another line. So, it actually would save time to work with the app to look up the recommendations there to also have more precise, over the time the recommendations, of course, will get better and better, and where they will not have to try out a lot but really will be able to rely on these recommendations.
Ed Bernardon: So, do you think if the experienced operator was available, probably you could learn at a more rapid rate? Because it sounds like one of the advantages is the AI assistant is always available, where the experienced operator might not be. But if they are available, is it still a better way to go if you can get someone that’s experienced, rather than relying on AI and machine learning?
Sofia Lewandowski: Well, we consider a lot of different aspects that we use for machine learning for our algorithms. So, I would say there are a lot of different experience operators, but still they might not consider some of the aspects at the same time. So, that’s why they will still try out until the right setting will be found, and the AI will make sure that it will happen faster so that the recommendation is already there without trying out a lot.
Ed Bernardon: I suppose with the experienced operator, though, once your break comes along, you could go and have a cup of coffee with him. We haven’t perfected the AI assistant yet to do that have we.
Sofia Lewandowski: No, you cannot get the coffee with.
Ed Bernardon: You never know what you might learn on that conversation over a cup of coffee. That could be for the next version, version two. Now, how do you compare the difference in the goals you have at work at HFM with autonomous vehicles to what you’re doing now working in factories here using artificial intelligence to improve and digitize the factory floor? How do you compare these two working environments and what your goals are?
Sofia Lewandowski: At the FactoryPal, I’m actually working as a UX researcher, and here I’m more specified. So, basically, I have the expertise in one area, I’m testing the prototypes that were created by designers, also test the features and different ideas with the users on the shop floor. And this is really more about UX methods. I apply a lot of methods, such as interviews with the users, I observed the users on the shop floor, I also create for them diary studies. I’m just basically using a lot of methods only for UX research. And here I also worked in the software area. So, with HFM. was more working on the physical level for physical motion work platform, I created these 3D designs in different 3D software, using VRED,using VR. And also was not just responsible for design but really, for a lot of different things at the same time. So, basically, designed the 3D models but also reached out to the community, represented the company, and so on. So, it’s a completely different area, I would say.
Ed Bernardon: When you say it’s completely different. Is it completely different in terms of the final application or more the difference in your role?
Sofia Lewandowski: Both. So, different in my role? Yes. I mean, I used to work, of course, with the customers and users as well, but it was more spread out. I really was responsible for a lot of different things in a, let’s say, smaller startup, and now in this corporate startup with FactoryPal, I’m more focused. In terms of the company goals and also the product, we are comparing automotive industry with Software as a Service, let’s say, with a software solution where we don’t create a physical product but we create the software piece that we use at customer side and help them to improve their efficiency.
Ed Bernardon: So, in one case, you’re creating a vehicle, and in the other case, you’re actually trying to, in a way, providing a service. Well, you’re providing a product, but ultimately, it’s to make what they have better. The whole idea of AI coming into a factory and helping people gain experience or improve, I would imagine, there may be some people that are excited about that, maybe others that are scared about it. How do you see people in factories or even people that are going to take a ride in an autonomous vehicle, how do you think they feel about artificial intelligence?
Sofia Lewandowski: For example, at FactoryPal, on the shop floor, there is fear on the shop floor level from, let’s say, machine operators. On the management level, there is an excitement. So, basically, the same company, the same customer, but different levels of this excitement and fear. So, the management level understands the benefits, what it will be doing for the production, how the production will benefit from it. And they also know where it comes from and how it works. I would compare this with [ inaudible] where you have two phases, it’s not separate. There’s not either fear or excitement but there’s both in the same person, or in the same company. I would say, also on the shop floor level, there is also both, the young OPs – so basically the next generation – they are excited about the technology, and they also support, they can work easily with smartphones, with tablets, with MacBooks where we have our apps. And they also are very familiar with all the usability aspects. They play around with the app and are really excited that they actually can use this knowledge base. So, basically, they can use these apps to optimize their processes to have easier life, easier workflow. But elderly, more experienced OPs, they are non-digital natives, and for them, it’s a little scared because they maybe feel that they might be replaced in the future and they might not be needed, or they just don’t know how it works and where it comes from. With automated vehicle, it’s similar, there is also an excitement and fear, there’s both. And I think because people are curious, but a lot of people don’t want to be the first who would try out the new technology, there will always be these early adopters who will just jump on an autonomous vehicle, try it out, and see that it actually works well, that is not dangerous. I think we just need to go step-by-step by losing this fear to show that it’s actually exciting and it will be beneficial for people.
Ed Bernardon: In an autonomous vehicle the fear is almost understandable. You get into it, “Oh, there’s no driver!” And certainly, there are the early adopters that say, “Oh, no problem. I’ll give it a try.” On the factory floor though, when you say there’s fear of AI, what’s it fear based on?
Sofia Lewandowski: People don’t understand where it comes from; how the AI works? And also a lot of, let’s say, experienced OPsif they don’t know what it will be good for, and how it will help them in the future; they might become fearful that they will be not needed in the future if the AI will know better.
Ed Bernardon: Yeah, “The AI is going to replace me.” So, how do you go about when you encounter someone like that? Because if you have a user-centric product that’s supposed to help the user, yet they’re afraid of the very thing that’s going to help them? How do you create the trust around the product that’s AI-based so that they can get the benefits that it can provide to them? How do you do that?
Sofia Lewandowski: We don’t actually aim for lifeless factories, the customers will always need the operators there. But this support from the AI will enable them to have more time for other things, to maybe oversee not just one line, but two lines, not being in a noisy environment but being in their cabin and monitor everything from there. So, to let them kind of understand and help them to understand what is the value, we need to show them where it comes from, and that they are still in charge, and that AI just supports them, these recommendations are actually originally coming from them. Shopfloor consultants, we do have shopfloor consultants on the customer side, who are companions to machine operators, they are assistance in the transformation process. So basically, they support them to learn how to work with the app and to understand where everything comes from. I think this is how we can gain trust.
Ed Bernardon: When you’re doing these types of interactions, certainly being face to face has to make it a lot easier, especially if you’re trying to build trust. But with COVID, over the past year, I would imagine a lot of your work, if not almost all of those, probably been done remotely, how has your role and what you’ve done changed because of COVID in trying to achieve the goals that you’ve achieved in the past when you were working face to face?
Sofia Lewandowski: I actually started during the pandemic and was even onboarded online. I still don’t really know my colleagues in person, a lot of them, a couple of them I met in the office sometimes as I went there. But especially in the beginning, I went to the customer side to the shop floor, in the beginning, a lot. So, I was traveling to different locations in Germany. But now because of the restrictions, I cannot go there anymore or not that often. We created a remote setup to interview the users online. And, of course, there is a big disadvantage because I cannot be there and observe them, I cannot, let’s say, bother them with questions and just figure out things I would like to figure out, and just I think observation is really important in this case. And I used to talk to a lot of different operators during the day, and now we schedule, let’s say, maybe a couple of interviews a week, which is sometimes not enough input, but we figured out it actually works pretty well, I would say. Now, because of the pandemic, it’s more accepted that people cannot be there and accept the remote environment and the remote installation, and are more ready to actually sit down in front of the computer and talk to me via Lookback, Teams, or Zoom. So, we do still have our shopfloor consultants, not all of them at the same time, but they help us with the installation. They have helped us with the installation in the beginning, and now they just look if they can get us some users, let’s say, to invite for a remote interview. And if they are not there and they are not allowed to go there because of the pandemic, then we just have our person of contact, which is a process engineer at one of the locations, and he tries to organize the interviews with us
Ed Bernardon: Did it surprise you how well you’re able to work remotely?
Sofia Lewandowski: Yes, actually, it was very surprising, I didn’t imagine it will work that well. As I said, there are a couple of challenges because our users are non-digital natives, a lot of them. And they really don’t work a lot with online applications, not even sometimes with smartphones, and for them, it’s sometimes challenging. But I figured out for myself that it works better than I thought. I think it’s just because of this social acceptance because everyone knows that it cannot work differently, right now.
Ed Bernardon: We’ve gotten used to the new way. And do you think it’ll change the way you work in the future once COVID is over and we can work the way we used to, or maybe apply elements of what you’ve learned over the past year? Do you think it’ll be different when we’re back, shall we say, to the new normal?
Sofia Lewandowski: I think I just learned the advantages, actually, of the remote setup. I don’t have to travel a lot, that’s why I think in the future, it will be a mix of being at home and still interviewing users from Berlin and not having to travel to somewhere in Europe; it saves a lot of time, and a lot of energy. And I have free time to actually analyze the results, present the results to the team, being busy with other assignments, such as user journey maps, and so on. So, I think I’ve learned that it just really can work and it works well, and I can just save a lot of time on traveling, and in the future, I will be just mixing I think both.
Ed Bernardon: Yeah, I think we’re all going to have to explore and figure out what the right mix is but it’ll certainly be a mix. The other challenge is, obviously, you have a home office of some kind, what would you say your biggest challenge was to learn to work from home day after day after day, over the past year or so?
Sofia Lewandowski: I think it was missing exchange with the colleagues in real. Sometimes, as I was onboarded, I didn’t know actually not much about the company. And production is also, let’s say, very technical, so you need to really understand what happens in the production. Not being able to go to the shop floor that often and not being able to exchange any time with the colleagues, that was the biggest, I would say, challenge. Sometimes, if you work with your colleagues everyday, you just know you have a lunch break together, you do a coffee break and during this time, you also talk maybe about work and about features they are working on and so on. So, it’s not forced, it happens kind of intuitively. But in the remote office, you really need to schedule appointments if you want to figure out something and you need to know what you need to figure out. That’s why I think remote office is a challenge because you sometimes don’t get the information you would get if you would be in the office with 35 people that surround you.
Ed Bernardon: Well, and also if you have a pet – like a barking dog- you have to learn how to control them. Any challenges like that, that you encountered?
Sofia Lewandowski: No, actually, I’m pretty lucky, I would say. I mean, I can speak from my sister’s experience, she has two children at home and they couldn’t go to school during the pandemic, and still they are not able to go full time. So, for her, it’s a real challenge. And if I compare myself with her, I really have the best conditions; I’m at home, my partner is at home. I don’t still have children or dogs at home, so it’s really relaxing. I would say, for me, the setup works really well. But for some of the families, of course, it’s a struggle.
Ed Bernardon: I would ask you one last thing here. So, you’ve worked in the automotive industry, and now you’re in the software business. How do you think the role of women compares in these two different industries? You’ve experienced both, how are they the same and how are they different?
Sofia Lewandowski: Both areas actually are about technology but I feel that if I think about how many women we have at FactoryPal, this is 1/3 of all employees and in HFM I was only one woman after another one left for her maternity leave. This is a big difference. Also, I used to work in an automotive company, in a corporate company, and I was the only one girl at that time, and the department consisted out of 40 people. So, I mean, here I see at FactoryPal, we have way more women, just because I think it’s not that technical, it’s not that physical; it’s more about software consultancy, user experience, a lot about user experience and design. And I wish we would have even more women, of course, in both areas, in the automotive industry and in the software industry.
Ed Bernardon: Well, certainly women bring a different perspective.
Sofia Lewandowski: That’s true.
Ed Bernardon: Well, Sofia, thank you so much for joining us here today. I want to finish up with what we call rapid-fire: a series of questions that we ask. You can answer very quickly, short answer or long answer if you want, or even say pass if it’s a question you don’t want to answer. Are you ready?
Sofia Lewandowski: Yes.
Ed Bernardon: All right, here we go. What is the first car that you ever bought?
Sofia Lewandowski: As I still was a student, I bought a new Hyundai I10. I had a couple of thoughts, why I would like to get a small car, it had to be small, good for parking in the city, but still have enough space inside to drive around with friends and family. It had to have a low fuel consumption to drive long distances so that I could afford as a student of course. And it shouldn’t have any issues, that’s why I got a new one. And I was super happy with actually this choice that time.
Ed Bernardon: Did you pass your driver’s test on the first try?
Sofia Lewandowski: Yes, I did for my car in Germany. But I had to repeat the driver’s test for my motorcycle in the US. But of course, I did it again in Germany I had to, and then I passed for the first time.
Ed Bernardon: Tell me have you ever gotten a speeding ticket? If you’re a motorcycle driver, you must have gotten a speeding ticket. What’s your best speeding ticket story?
Sofia Lewandowski: Actually, I’m not proud of my speeding tickets. And I’ve got a lot in Germany, seriously. Here are a lot of cameras installed everywhere so I regularly get them, unfortunately. But I also get pictures, so some of them looks fun. I’m very impatient and drive too fast, I think this is my problem. Last time I rented a car, Skoda Kodiaq, it has a great travel assistant, and the speed was automatically adjusted by speed limits. And the thing, automated cars will help impatient drivers in the future to keep the right speed. So, it helped a lot, me, to stay within the limits. And I think this is just a great solution. So, maybe I will improve in the future.
Ed Bernardon: Imagine, in the future – and actually probably not too distant in the future because HFM is doing it today – you could have your own living-room-on-wheels; an autonomous vehicle with whatever you want inside, you’re going to take it on a five-hour journey, what would you want in your living-room-on-wheels?
Sofia Lewandowski: I think I would like to be by myself. And since I will not have to drive, I would like to have a foldable desk and a big screen to cut videos; I like cutting videos in my free time. I would probably also learn singing; karaoke or something like that so that nobody can listen to how terrible it sounds. I would video chat with my maybe family and friends I haven’t seen for a long time. And once I will be done with all this, I would fold everything back and just relax and look out of the window.
Ed Bernardon: What person, living or not, would you want to spend that five-hour car ride with?
Sofia Lewandowski: I think I can think of two people. The first one would be Warren Buffett, I would love to learn about his investment strategies. And another one would be Elon Musk, I would like to ask him about his passions, his childhood, how he came to where he is right now, and what inspired him to do what he does today, and what are his further plans. I’m just really interested in people’s biographies and stories. And everywhere I try to talk to people first about how they came, where they are, and about their childhood, and inspire them to do what they do today.
Ed Bernardon: What do you wish you understood better?
Sofia Lewandowski: I would say these are investment strategies in startups; this is something I would be interested in. And also how to found a company and be successful; this is also something that would very much interest me.
Ed Bernardon: Well, we need to build you that living-room-on-wheels and get you with Elon and Warren, right?
Sofia Lewandowski: Right.
Ed Bernardon: Now, if you could have the answer to any question, what would that question be?
Sofia Lewandowski: How to make the world more accessible to everyone?
Ed Bernardon: All right, if you could un-invent one thing, what would it be?
Sofia Lewandowski: It’s difficult to say. I would say social media but not completely. I mean, I’m also spending a lot of time on social media. But only maybe partially, only the toxic part.
Ed Bernardon: It’s a love-hate relationship, right?
Sofia Lewandowski: Yes.
Ed Bernardon: And if you could magically invent anything, just one thing, what would that be?
Sofia Lewandowski: Since I used to travel a lot and I kind of wasted a lot of time by traveling, I would like to have something like people-beaming. So, I would like to save time on traveling and would like to appear in Stuttgart, or Portland, or Detroit just within seconds to go ahead and drink coffee with a friend, or go to a conference I want to go or do users interview somewhere in the middle of Germany so that I don’t have to travel down. So, I think that will be genius.
Ed Bernardon: The People Beamer, as you called it, is probably the thing that comes up the most when we ask that question, of one thing you could’ve done. Absolutely, so a lot of people looking for the People Beamer. So, hopefully, here it’ll be invented soon. Sofia, thank you so much for joining us on the Future Car Podcast.
Sofia Lewandowski: Thank you, Edward. It was really great talking to you.