Adapt to complexity with the Product Definition
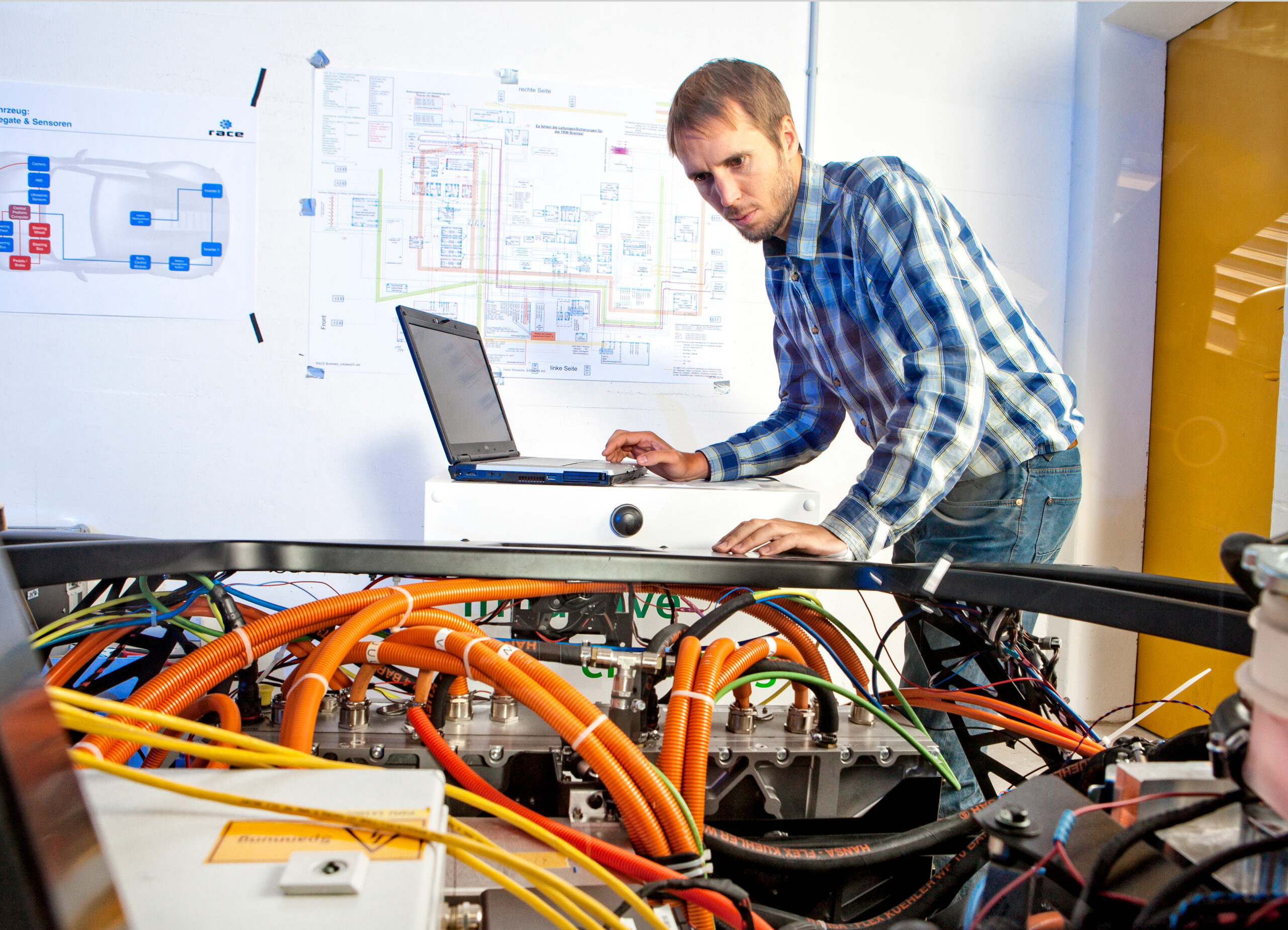
One of the major pillars of a model-based systems engineering (MBSE) approach, and more specifically Software and Systems Engineering (SSE) for the automotive industry, is the Product Definition. In the first episode of the MBSE miniseries on The Future Car podcast, our resident expert on the automotive market – Nand Kochhar – briefly explained how this process is meant to capture design concepts as well as project requirements to then guide development. But the complete scope of what the Product Definition entails is covered in episode two. While most of the discussion is framed around the newfound complexity in electrification, comprehensive solutions to complex problems are needed across the industry.
But how does the Product Definition change development, automobiles were already complex pieces of machinery with a variety of mechanical domains? Engineers and designers often already know the requirements to the system, so what’s different? Well, the Product Definition can be thought of as the explicit aggregation of these requirements. That may be the limitations that the engineers has previously experienced in manufacturing processes, it might include business targets on limiting wasted material and most importantly for the more integrated electric vehicles (EVs) those requirements will cover mechanical, electrical and software demands in one definition
The product Definition phase of development also acts as a catalyst to establish the physical and system architectures for the product. For example a vehicle that will function as an electric fleet vehicle in a city has drastically different requirements from an electric pickup used by a construction crew. The fleet vehicle can prioritize low weight and highly efficient engines with its minimal load and travel distance while the truck needs to travel longer distances and carry far more weight to get supplies to the job site. And speaking to the system architecture, the fleet vehicles are far more likely to be integrated into a larger system like smart cities to optimize the charging of vehicles at off peak times or even control city-wide traffic patterns through autonomy systems linked to the city infrastructure.
These are examples of the high-level decisions that guide development, but making, tracking and verifying them requires a digital enterprise. While many of the workflows of MBSE and SSE are hold overs from their predecessor – systems engineering – those that document centric approach cannot handle the complexity of today’s automobiles, let alone tomorrow’s. With the Product Definition guiding future development processes like design, simulation and validation it is important that the exact requirements and portrayed throughout the development cycle and not just end-to-end, but across every engineering domain (mechanical, electrical, software, etc.).
The actual sharing of the Product Definition across the enterprise is Connected Engineering as Nand also discussed in episode one of the MBSE miniseries, and for the full story you’ll have to listen to episode three, but it is important that every engineering or even business team working on the product has access to the definitions within the context of their development activities. As an example, a mechanical engineer working on frame design needs to know where electrical systems will be in the vehicle and how large they are, but they would not need to know what data they carry necessarily. The flip side of that example, the electrical engineer would not need to know the manufacturing process for the frame, but they would need to understand how the placement of sensors impacts their effectiveness.
But neither of these examples really captures the interconnectivity of todays manufacturing process, they only begin to uncover the vast web in complex systems of systems. And all of this becomes even more complicated when looking into the future with the possibility of electric cars functioning as a collective load balancing device for city infrastructure in the transition to renewable energy systems. Having a comprehensive solution not only in your toolbelt but using it every day will be the key to tomorrow’s successes. For the full story of how SSE and the Product Definition guide that change, listen to the complete second episode with Nand Kochhar and Conor Peick.
Siemens Digital Industries Software is driving transformation to enable a digital enterprise where engineering, manufacturing and electronics design meet tomorrow.
Xcelerator, the comprehensive and integrated portfolio of software and services from Siemens Digital Industries Software, helps companies of all sizes create and leverage a comprehensive digital twin that provides organizations with new insights, opportunities and levels of automation to drive innovation.
For more information on Siemens Digital Industries Software products and services, visit siemens.com/software or follow us on LinkedIn, Twitter, Facebook and Instagram.
Siemens Digital Industries Software – Where today meets tomorrow
Nand Kochhar is the vice president of Automotive and Transportation Industry Strategy for Siemens Digital Industries Software. He joined Siemens in 2020 after nearly 30 years with Ford Motor Company, where he most recently served as Global Safety Systems Chief Engineer. In this capacity, Kochhar was responsible for vehicle safety performance of all Ford and Lincoln brand products globally. He also served as Executive Technical Leader, CAE, and as a member of Ford’s Technology Advisory Board. Kochhar’s tenure at Ford also included executive engineering leadership across a range of disciplines including in product development, manufacturing, digitalization, simulation technology development and implementation.
Kochhar has additionally been active in SAE International, where he has served as Chairman of the Executive standards committee, leader of a cross-industry group focused on driving standards for mobility, autonomous vehicle development, electrification and connectivity. Kochhar also served as Chairman of SAE’s Motor Vehicle Council for 2015-16 terms, after which he was named the Vice Chair of Technical Standards Board (TSB) in 2017 and then TSB Chair in 2018 and 2019.
Kochhar graduated from Missouri University of Science and Technology (Missouri S&T) with a master’s degree in Engineering Mechanics. He was inducted as a member of the Academy of Mechanical and Aerospace Engineers at Missouri S&T in 2005. He lives in Northville, Michigan with his wife and two kids.
Conor Peick works as a writer covering Automotive and Transportation topics for Siemens Digital Industries Software. In this role, he has helped produce a variety of materials including blogs, articles and whitepapers on automotive topics ranging from wire harness design and manufacturing to embedded software development and overall industry trends.