Don’t replace it, repair it with AM
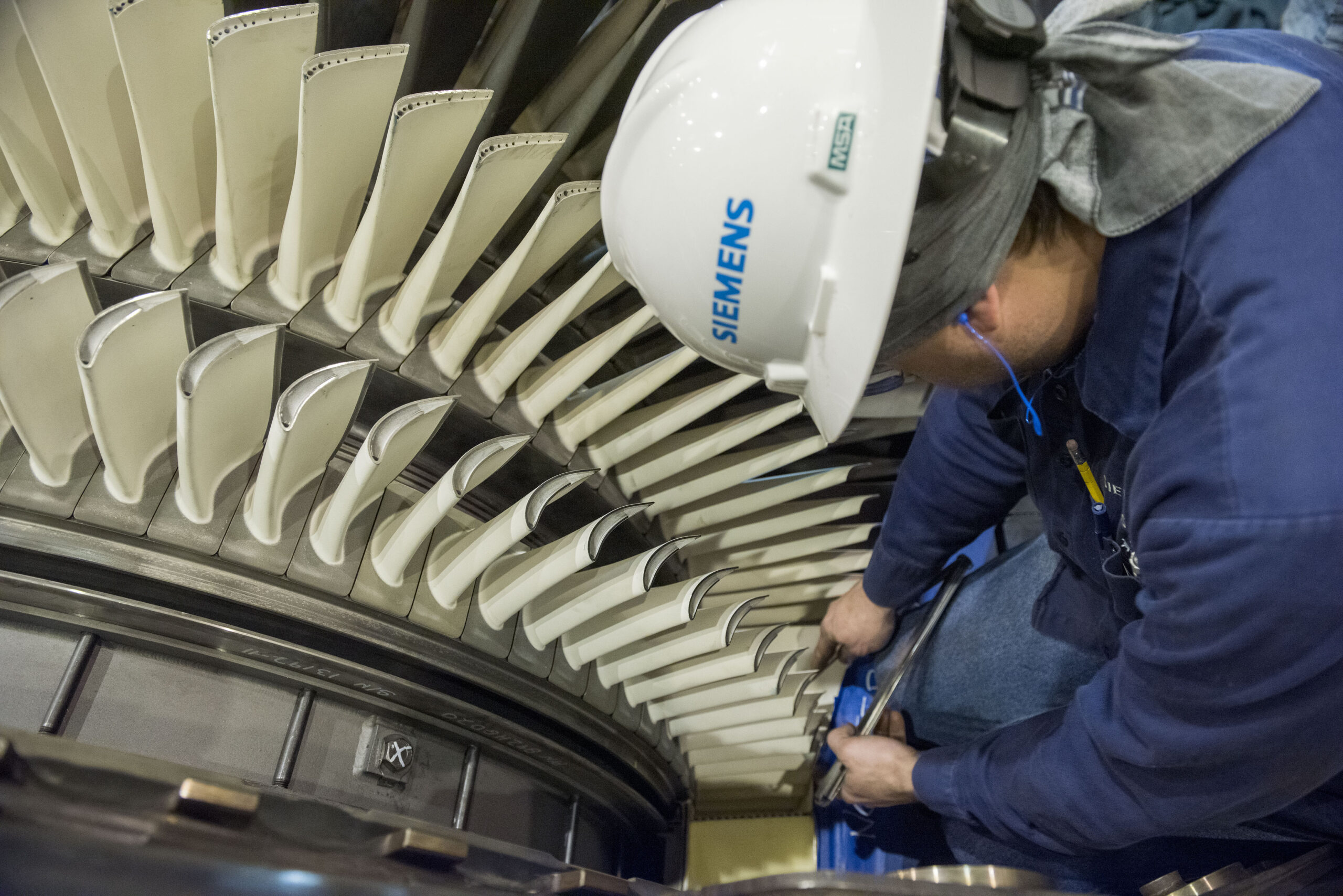
Many products around the world contain wearing parts that traditionally needed to be replaced on a continual basis to retain safety, performance or reliability. For automobiles the most common are the tires and brake pads, for consumer electronics it is often the internal battery and for the massive energy generating turbines the wearing parts were the individual blades. These components were designed to balance the replacement cost of each component against the performance of the system. Brake pads in a car represented a very efficient design compromise, they are easily replaceable, impact the performance of the system minimally compared to a non-replaceable caliper design and produce minimal wasted material during the replacement process. Turbine blades were on the inefficient end of the spectrum, at least until hybrid additive repair became a viable technology.
To ensure performance of each turbine blade in a generator, each blade had to be replaced when the wear on the it was too great. But because of the geometry required this meant when the top few millimeters of the blade’s tip wore away the entire blade with its mounting point had to be tossed out. Hybrid additive repair completely changed the maintenance process, now a blade could be removed, cleaned and built back up before being placed back in the turbine. This not only saved the users the cost of the wasted material in each replacement blade, it also provided an opportunity to optimize each part within the complete system.
Taking a turbine blade out, the first step is to strip the parts by mechanical and chemical means along with a visual inspection that there are no large deformities in the components. Then the part proceeds to fluorescent inspection to check for any cracks that were not visible in the visual inspection. Once the part has been classified as a candidate for repair it is mounted in a custom printing fixture with nine other blades to begin the repair process. In the fixture, the blades are set in a CNC milling machine to create a smooth and even surface across the entire lot for proper adhesion in later sets.
Now comes the additive manufacturing portion of the repair process, with smoothed printing surfaces the parts are scanned so that the geometry can be imported into NX for modeling. At this point, the repair geometry along with any optimizations are added to the tip of the blades in the modeling software so that each blade retains its customization for peak performance in the turbine. The geometry is then used to generate build job files for the laser powder bed fusion printer being used. With the right parts emerging from print, they can be post processed on-site by coating them in a protective layer and laser drilling any covered holes during the coating process.
Repair is one of the greatest tools to prolonging the use of high investment assets. It provides users with a sense of security that if something breaks it can be fixed on-site rather than waiting for a part shipment or a hired technician, at least in the industrial sector. And additive is growing the pool of components that can be repaired in any system to include wearing components. Being able to return material that is wore away in your own factory while also enabling further optimization to the technology with each repair is an amazing feat only possible with an advanced end-to-end process.
This end-to-end repair process highlights nearly every aspect of the additive manufacturing workflow available to customers with Siemens Software, from order management through post-processing and every step in between. But for the full story of how Siemens Energy implements this workflow or how anyone can adopt an end-to-end workflow for additive manufacturing, it is highly recommended to watch the Realize Live presentation on the topic before it goes away on June 25th. If you miss the deadline, check back in with us and we will be able to continue the discussion.
Siemens Digital Industries Software is driving transformation to enable a digital enterprise where engineering, manufacturing and electronics design meet tomorrow.
Xcelerator, the comprehensive and integrated portfolio of software and services from Siemens Digital Industries Software, helps companies of all sizes create and leverage a comprehensive digital twin that provides organizations with new insights, opportunities and levels of automation to drive innovation.
For more information on Siemens Digital Industries Software products and services, visit siemens.com/software or follow us on LinkedIn, Twitter, Facebook and Instagram. Siemens Digital Industries Software – Where today meets tomorrow.