Integrating industrial custom 3D printing
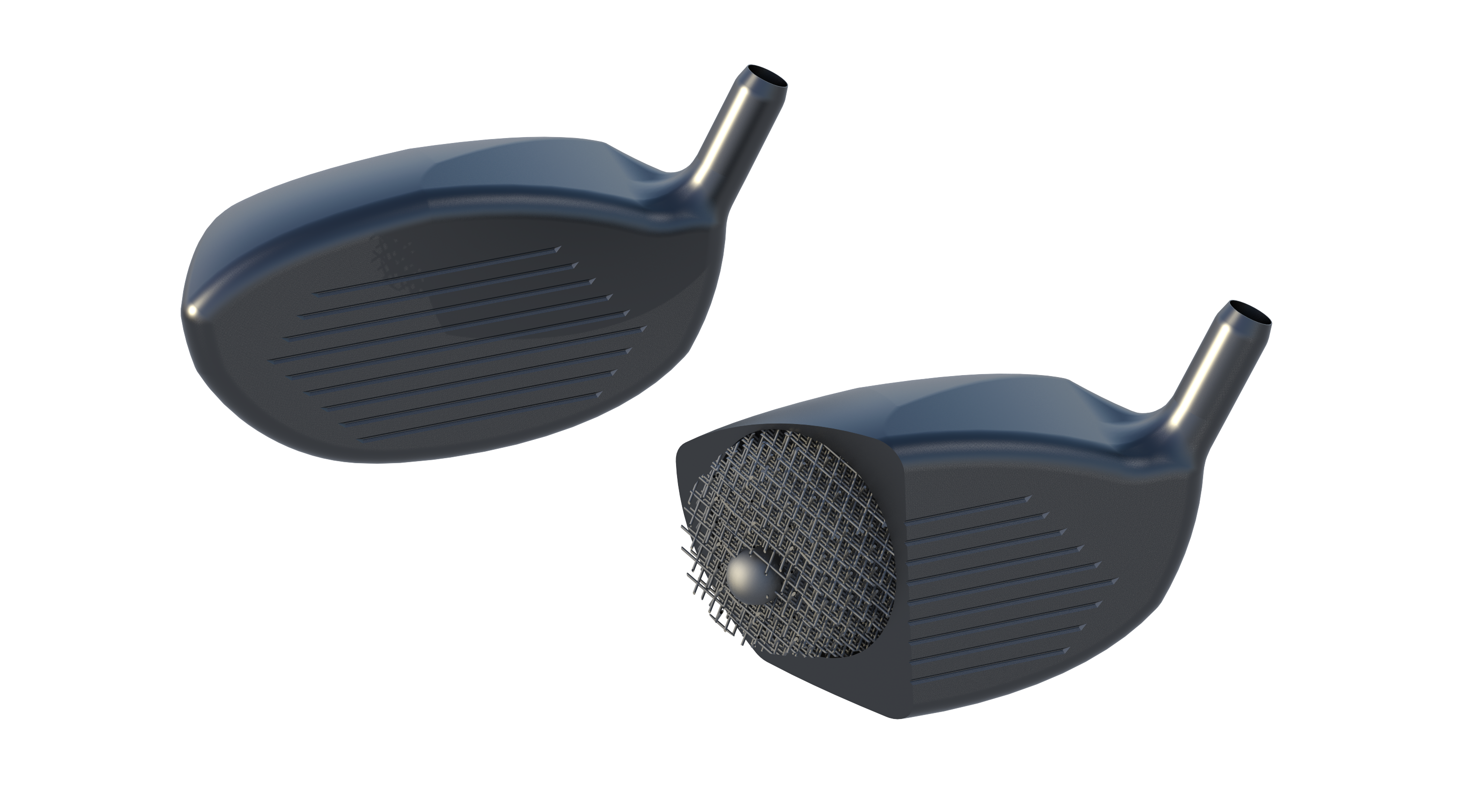
With enough time, money and ingenuity pretty much anything can with the handfuls of manufacturing process humans have developed over our time here. It is not the most effective way to create a product, but it can be done with sheer willpower. Instead the variety of manufacturing methods has evolved to do specific tasks very efficiently. Injection molding can create thousand of identical parts in a minute, metal stamping machines can form perfect doors panel for years and CNC machining can create the most precise metal parts for ultra-high performance applications, but the growth of fast and custom manufacturing has forced many to reevaluate the possibilities. Additive manufacturing and 3D printing deliver many of the benefits product developers are searching for, but the changes to production also come with changes to the entire enterprise. Two very important changes are simulation and traceability, but they should be implemented with informed intent.
Simulated customization
AM provides the greatest benefit to those looking for low volume and high customization in manufacturing work. That can stem from rapid prototyping, one of the first reason for the adoption of the technology, but it is increasingly adopted to manufacture personalized products for customers. It is much faster and cheaper to print a component than to create molding for an individual part, but it is a doubled edged sword because each iteration must be qualified for the manufacturing process. The technology is less mature than other forms of manufacturing and there are few who understand the intricacies of the process as with other methods like casting or forging. And if an individual does have this deep knowledge it is likely very narrow in focus – changing the material, the printer or even the printer’s software can have drastic effects on the quality of the product. This is where simulation plays a huge role in 3D printing.
Simulation tools fill in the knowledge gaps of users to create the right product the first time, through optimizations of the tooling path to minimize overheating the metal or orienting the part in the print tray to prevent deformation. But it is also important to remember that simulation still has a cost and as users begin to understand the intricacies of the process it can be beneficial to reduce the number of simulations being run. It can almost be thought of as guardrails, they’re great in difficult road conditions to prevent the worst but are only in extra cost on easy sections. There are many ways to optimize the use of simulation in your manufacturing process and Ashley Eckhoff makes a few great points in his article in Metal AM magazine. One example is to simulate a representative sample of custom parts, such that simulation is only required for edge cases.
Tracking every part
Custom printing also impacts how components are tracking through manufacturing. Large batch printing is comparatively minimal, you know when a group of parts was made and what the manufacturing parameters were. For custom AM, every individual part needs to be traceable. A custom golf club for example, is designed for a specific user getting the part to the wrong individual could not only hurt their play but company reputation if the customer assumes the technology is ineffective. For more critical components for aerospace applications, the process itself needs to be traceable on top of the product. It would be important to know if a specific printer is creating parts with a higher than normal porosity.
Just as with simulation there are a variety of paths to applying traceability to 3D printing operations – serialization is one of the more traditional while sinter boxes are specialized for the additive manufacturing process. If you’ve ever constructed a plastic model, from the breakaway “sheets” you have dealt with a precursor to the sinter box. One of the main purposes of the technique is to print related parts such that they can be dealt with as a lot. This can be similar parts that need to undergo the same post-processing or grouping the parts that connect so they serialization isn’t necessarily required for the individual parts.
Selecting your perfect solution
There are a variety of process possibilities stemming from just two points in additive manufacturing, but it should not be a fear. There are software solutions to help guide the decision process, whether in early stages of development deciding how to print the parts to manufacturing planning of specific variables to use in the process and with a digital enterprise the decisions could even be made based on cost models. For a more in-depth understanding of not just the possibilities in simulation and traceability, but how they are being implemented for custom printing Forging a process for mass customization via metal Additive Manufacturing is a great start. And if you are looking for more resources on AM, our website has topics across the supply chain.
Siemens Digital Industries Software is driving transformation to enable a digital enterprise where engineering, manufacturing and electronics design meet tomorrow. Xcelerator, the comprehensive and integrated portfolio of software and services from Siemens Digital Industries Software, helps companies of all sizes create and leverage a comprehensive digital twin that provides organizations with new insights, opportunities and levels of automation to drive innovation.
For more information on Siemens Digital Industries Software products and services, visit siemens.com/software or follow us on LinkedIn, Twitter, Facebook and Instagram.
Siemens Digital Industries Software – Where today meets tomorrow