Managing development with connected engineering
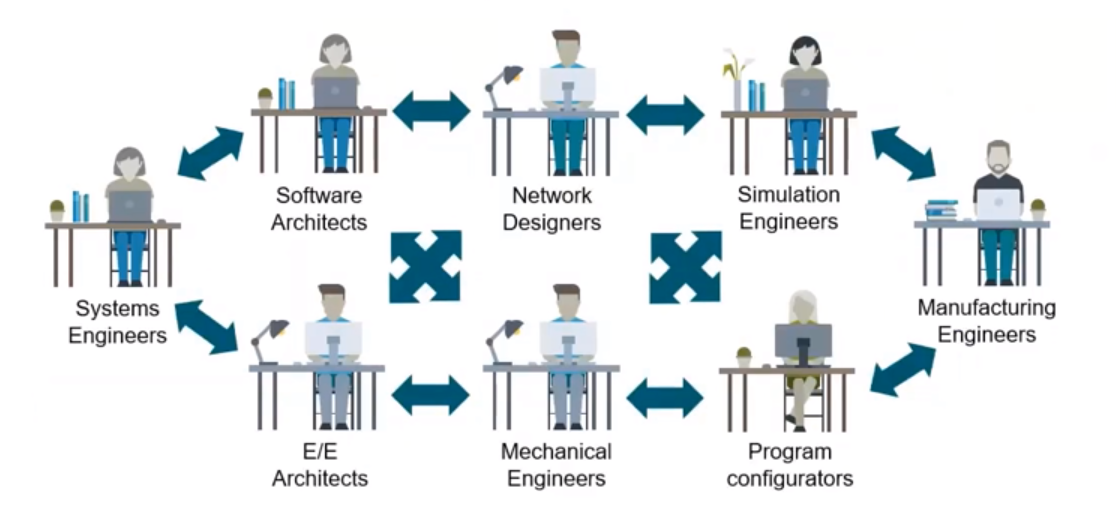
A central part of all of this complexity in the automotive market is the explosion of software. Start up companies are using more of it to punch above their weight and incumbents are adopting it to stay competitive. But it also goes into the systems being created due to greater reliance on electronic control systems and the connectivity features customers are requesting. Software even plays a role in environmental sustainability by refining designs with fewer physical tests and optimizing the vehicles for greater efficiency on the road. The reliance on software, both in the workflow and the product, is why model-based systems engineering (MBSE) and more specifically connected engineering are becoming crucial components of successfully managing the development of automotive project. These changes to the industry are covered in a recent webinar from Nand Kochhar – the VP of Automotive & Transportation at Siemens Software. The full presentation is highly recommended, but we’ll briefly go over a few of the major points here in case you are hesitant of the need.
Multiple domains
Pulling off a successful product while adhering to these new changes to industry norms requires the collaboration benefits of connected engineering. All stakeholders and development teams work from the same digital twin to maintain the single source of truth. This is highly important at the convergence of multiple systems. Mechanical, electrical and software engineers need to be able to work collaboratively in their respective tools. For example, electrical control units in a vehicle take up physical space and have material requirements to connect to the system from the mechanical group, they require circuit design and planning from the electrical group to minimize electrical interference, and the device needs to be able to communicate with the software systems in the vehicle.
Closed-loop verification
Also within the scope of connected engineering is the closed-loop verification and validation of systems. The chances of engineering a perfect component for a system on the first try are extremely low, but even in that reality it isn’t known to be perfect until it is verified or validated. And an important idea to remember is that none of these systems are isolated and independent. A component may meet the performance requirements of the greater system, but if it can’t communicate what it is doing to a controller or other system is it really perfect? Instead, systems are created iteratively to ensure each component in the system meshes while also providing the required system performance.
System re-use
A third important aspect of connected engineering has already been adopted heavily in the software world but is making headway in the remaining engineering and business domains – reuse. Given complex systems of systems rely on iteration to achieve highly-performant components, it would be a waste to only use that work on a singular product. And in the case of autonomous functions it could even impact overall system behavior to have redundant work. Take two functions that would be included in a modern autonomous vehicle – smart braking and anti-lock braking – both system likely rely on a similar set of information. Retaining multiple variables independently for these two systems increases the complexity of the code and if done across the thousand of systems can greatly impact the computation of the variables. This can either slow down under-powered processors or increase costs by purchasing over-powered ones. Re-use also has impact at the macroscopic scale, with entire systems being lifted into a new project which can drastically reduce engineering time for the new product.
Model mastery
Very few industries forego change and automotive is not one of these exceptions, in fact it might be one of the fastest moving industries right now with many changes in defining what a car is to the customer. The number and individuality of systems within a vehicle are expanding, along with an emphasis on connectivity and environmental sustainability. Traditional workflows are not able to keep up with traditional timelines with these inclusions, let along the start-ups and technology companies bringing advanced development practices for these complex products. Connected engineering is a critical step in creating the vehicles of tomorrow, and even today, for the collaboration it affords between teams working on what can seem very different goals. To learn more about the role of connected engineering in the future of the automotive and transportation industry Nand Kochhar’s webinar is a great place to start that journey, with success stories from Mazda and others.
For more information on MBSE in general, check out our podcast Model Based Matters.
Siemens Digital Industries Software is driving transformation to enable a digital enterprise where engineering, manufacturing and electronics design meet tomorrow. Xcelerator, the comprehensive and integrated portfolio of software and services from Siemens Digital Industries Software, helps companies of all sizes create and leverage a comprehensive digital twin that provides organizations with new insights, opportunities and levels of automation to drive innovation.
For more information on Siemens Digital Industries Software products and services, visit siemens.com/software or follow us on LinkedIn, Twitter, Facebook and Instagram.
Siemens Digital Industries Software – Where today meets tomorrow