Intentional design with additive manufacturing
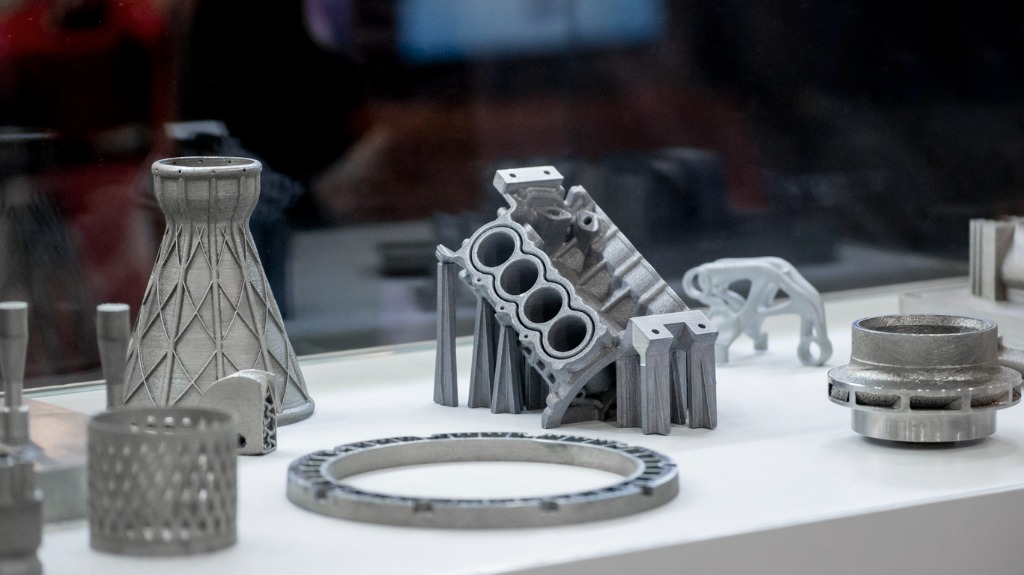
While additive manufacturing (AM) is a relatively new and highly regarded technology for the future of production it is important to understand that it is another tool. It has very unique benefits compared to more traditional manufacturing methods, but it is not the best solution for every application. Designing a product for AM requires more intentional design than other manufacturing processes because it is so versatile in the geometries it can create. This is very important to understand as more businesses apply sustainability as a new driver in their business models, it is easy to see the reduced material waste associated with AM but the energy usage can be far higher depending on the geometries being created. Designing intentionally for additive manufacturing means understanding the other product requirements beyond geometry, what are the performance gains over the lifecycle? Is AM a energy and material efficient option for the given part’s complexity? And is the product complex enough to make AM an economically viable choice compared to higher volume production methods?
One of the most important questions to ask in deciding whether to use AM for a given product is around the benefits to performance over the product’s lifetime. Depending on the product category, the greatest environmental impact is either the production itself or in the usage of the product. Vehicles, for example, have their greatest impact from usage – they directly consume energy at a system level. Reducing weight has a direct effect on energy consumed per unit traveled. This case is best exemplified in the aerospace industry, where every pound matters and the production volume is low enough to not benefit from the efficiencies of scale. Rather than producing solid components, lattice structures are printed into the parts to maximize strength and minimize weight. For more information on how these structures are created please read the whitepaper on the subject, but in effect it is like a honeycomb where the internal geometry reinforces the macro-geometry. These structures are very important to the sustainability of AM and not just for the performance benefits the product will gain.
There are many methods for AM, with plastics, metals, composites, and even ceramics across a variety of adhesion methods, but many of them require high energy inputs to form the material into the desired shape. Laser sintering is one of the most energy intensive operations, lasers require such large amounts of electricity that for mostly solid components it is far more sustainable to employ more traditional subtractive manufacturing processes. The processes for making large volumes of say aluminum billet and cutting some of it away for recycling is less energy intensive than creating fine aluminum powder and re-melting it with high-energy lasers. As parts move towards mostly hollow geometries there is a break-even point when the impact of either process is comparable. Instead, AM is most beneficial environmentally when the material structure is minimized which reinforces the goal highlighted for the performance of a component through AM.
A third important question to answer before planning a program around AM is the economic viability of the process. Because business decisions are so reliant on a balance of competing requirements, the value of AM must be weighed against its costs and I mean that in the literal sense. Unless you are building highly unique or highly complex components where a higher associated price is tolerable AM might not be the best option for a given operation. While aerospace applications can handle the higher cost for an individual component because of the astronomical cost incentives when it comes to weight, automotive applications may shy away because of the volumes needed. Injection molding, casting, and other high-volume processes will remain in markets where economy is crucial. But in these scenarios, AM will not disappear, only take on a new form. Rather than directly printing the product, AM may be used to create the tooling. There is a fantastic example of this within the whitepaper referenced earlier, where AM is used to create the mold for injection printing.
Creating the tooling for manufacturing with additive reduces development time from the more rapid production of low-volume components compared to traditional methods, but it also increases the performance of the tools. Integrated cooling channels in a mold can increase production yields through reductions in mistakes and even faster cooling times from more efficient coolant paths in the mold. Using optimized lattice structures for heat transfer can also improve process manufacturing by improving the efficiency of heat exchangers, but this application is still in infancy.
Additive manufacturing can be very exciting, there are so many possibilities. But designing a part for AM because it can be done is not a successful strategy. Intentional design is very important for AM workflows, without it the efficiencies of performance will be neglected, the process may be less environmentally sustainable than using more traditional methods, the project can become more expensive without tangible benefit to the component or customer. Simulation is often a great tool for understanding, defining, and qualifying the intent of a new design, but it is important to understand that AM is a new way to manufacture and should be handled as such instead of as a replacement for machining, casting, or molding. For more information on how simulation helps to design with intent please refer to the whitepaper on the topic. And stay tuned for more content of the sustainability of AM processes, I recently sat down with the AMGTA and will be publishing some great information on their early results from examining the AM value chain.
Siemens Digital Industries Software is driving transformation to enable a digital enterprise where engineering, manufacturing and electronics design meet tomorrow. Xcelerator, the comprehensive and integrated portfolio of software and services from Siemens Digital Industries Software, helps companies of all sizes create and leverage a comprehensive digital twin that provides organizations with new insights, opportunities and levels of automation to drive innovation.
For more information on Siemens Digital Industries Software products and services, visit siemens.com/software or follow us on LinkedIn, Twitter, Facebook and Instagram.
Siemens Digital Industries Software – Where today meets tomorrow