Model-based product development
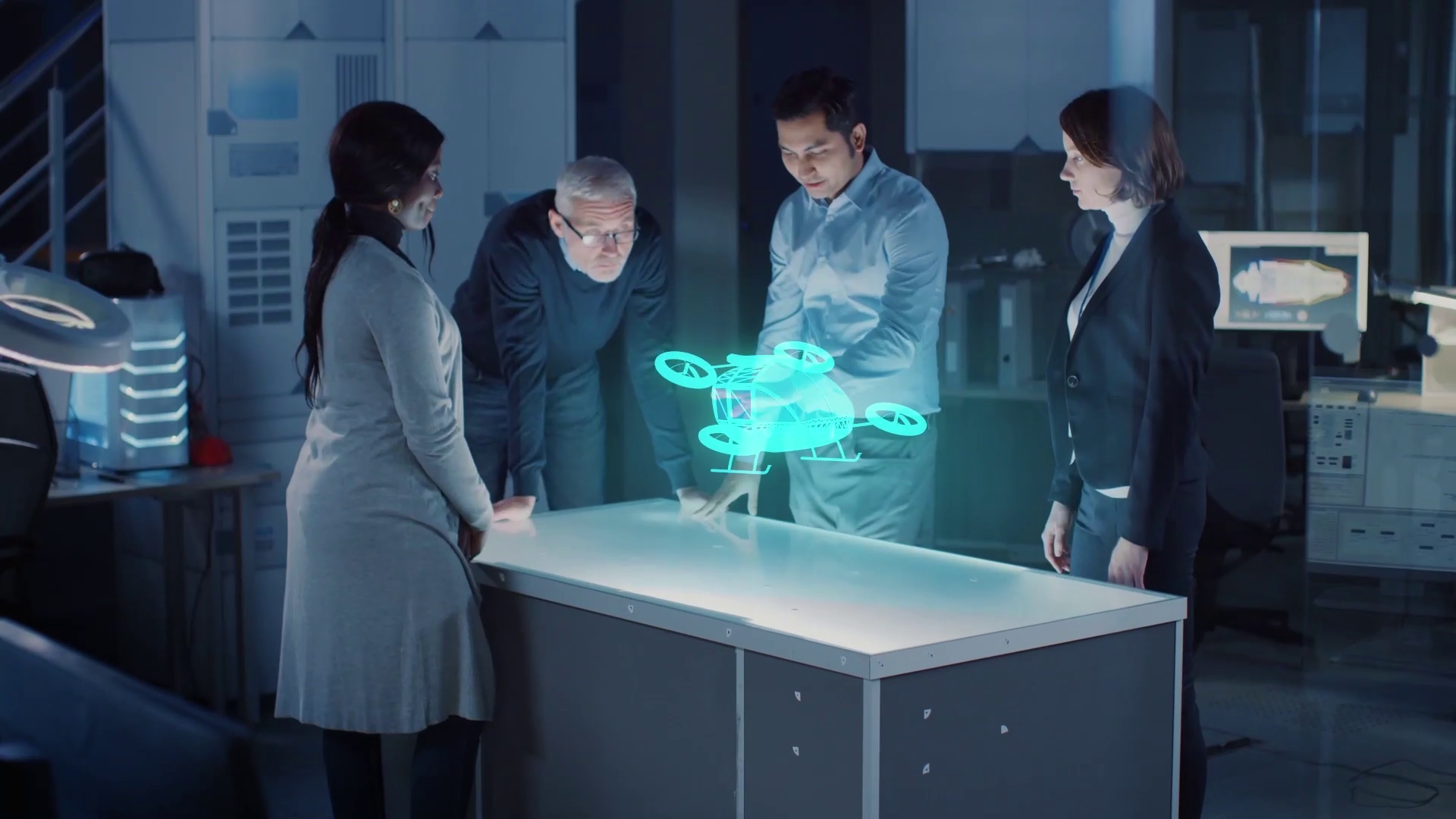
Model-based is a very muddied term in industry today, and it is most notable when looking at the digital twin of a given product. Of those that claim a model-based approach to designing their products, only about 15 percent truly use the model for development processes. The most common misunderstanding creating this divide between claimed and actual usage is that using a digital design tool – think CAD or CAE – is equivalent to model-based development. While they are creating a model of the physical product, downstream practices are often conducted based on drawings of the original model which negates any benefits of a model-based approach. The confusion is understandable, but it is important to understand what model-based development truly is to harness the complexity of today’s smart products.
Complex products constitute many systems of systems, from mechanical to electronic and even software in many cases, which is why model-based systems engineering (MBSE) is so important for products like automobiles and aircraft. The beginning of any product starts with the concept – what does this product need to do? What are the safety requires? Are there any production limitations? What features are customers asking for in the next model? All of the questions begin to form the product architecture in the abstract, but every piece of information is retained and tracked to understand the development decisions for regulatory reasons and future development processes.
The system architecture is then presented to the relevant engineering and development domains to classify and design the features within the requirements. Something as straight forward as a push-button start function would require input from the mechanical design group, electronics, and even software to deliver a more refined representation of the feature for use later in development. And communicating these decisions and requirements in a reliable and understandable format is why MBSE is so important – interpretation only enables opportunities to mis-interpret whereas specific definitions produce repeatable activities.
But the single source of truth for MBSE is not limited to the product design, it extends into the manufacturing and value chains, it even covers the future service capabilities around a product. Say your company is looking to lightweight a component for an aerospace application with additive manufacturing (AM). To understand the possible design envelope, you need to understand the manufacturing capabilities of the system, would it be more effective to use a combination of AM and more traditional techniques to create the bulk of a component and then print on top of the component? Or within the factory itself, if there is some flexibility to the process paths one could increase output as demand for one product raises by reassigning machine capacity on the fly.
And by using a model as a single source of truth from design, through manufacturing, and into service there is a greater understanding of the impact from certain activities. Is a certain machine producing components with a shorter useable life? Maybe you are collecting performance information on the product as it is being used out in the real world, that information can be used to refine any simulation models you have for the digital workflow, but it can also provide valuable feedback on the initial requirements of the system architecture. A system expected to be very important may e over-engineered for it’s actual usage cases or a component expected as non-essential has a greater impact than expected during development.
Few of the problems are novel, but they have become more complex with the introduction of more systems within an individual product. An inefficient engine could stem from poor tolerances within the cylinders, improper tuning of the firing times in the electronic control unit, or even a length of wire being longer than designed creating a signaling error. In effect one system could be designed perfectly, but if a system it relies on is not, problems are bound to crop up. But to learn more about the role of model-based – whether it is MBSE, the model-based enterprise, or model-based engineering – this discussion between Brian Meeker and Del Costy, of Deloitte and Siemens respectively is a great introduction.
Siemens Digital Industries Software is driving transformation to enable a digital enterprise where engineering, manufacturing and electronics design meet tomorrow. Xcelerator, the comprehensive and integrated portfolio of software and services from Siemens Digital Industries Software, helps companies of all sizes create and leverage a comprehensive digital twin that provides organizations with new insights, opportunities and levels of automation to drive innovation.
For more information on Siemens Digital Industries Software products and services, visit siemens.com/software or follow us on LinkedIn, Twitter, Facebook and Instagram.
Siemens Digital Industries Software – Where today meets tomorrow