Additive is design, not just manufacturing
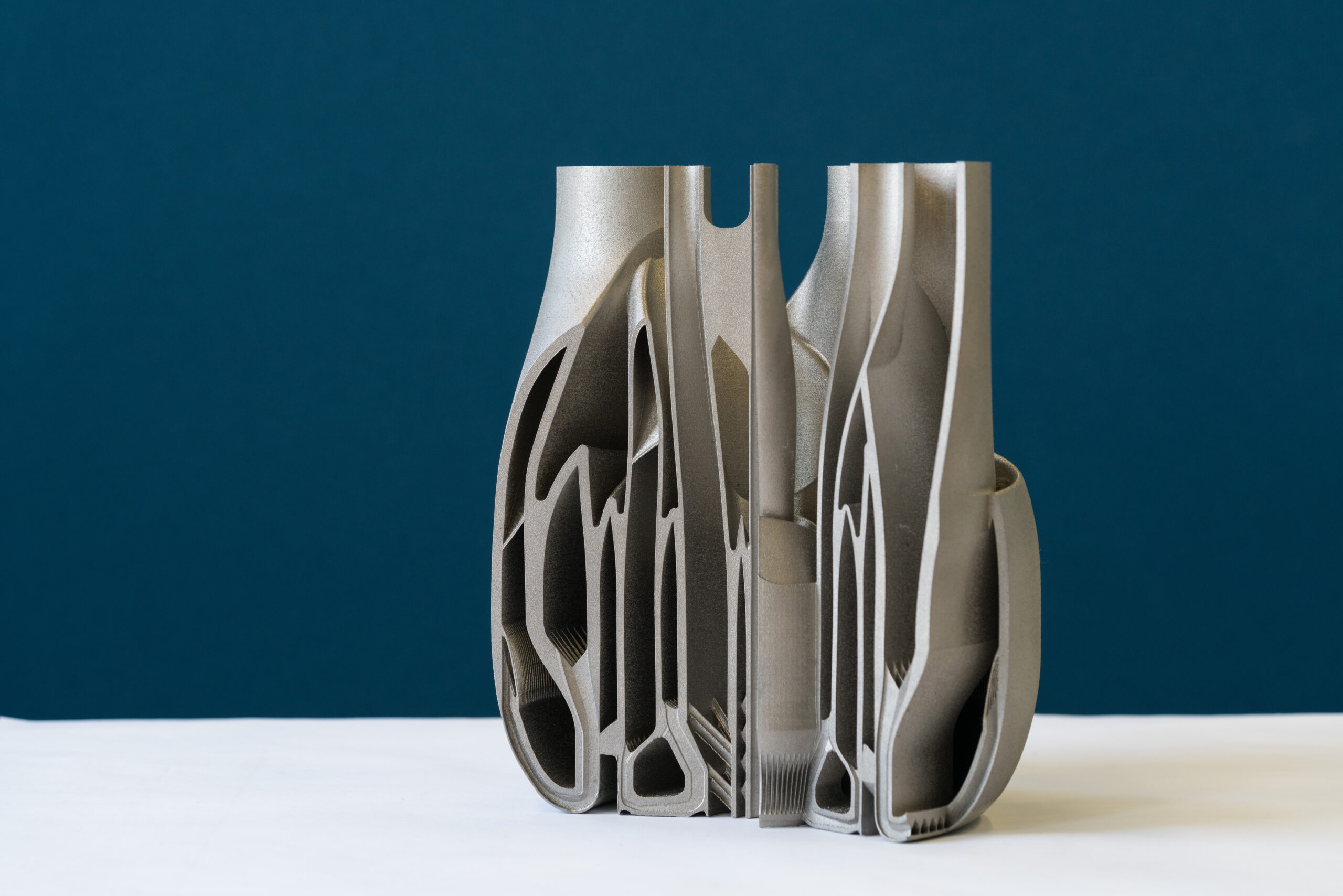
Often when additive manufacturing is discussed the immediate thought is of the final part. It often has lots of complex geometry and may even look alien because it forgoes the traditions of design. But that imaginary idea of what additive manufacturing (AM) resembles gets at the heart of the problem in widespread adoption of the technology – only focusing on the technology. Design plays a critical role in developing a 3D printed product. Granted, that can be said for every manufacturing technique, but the intent is because AM is so different from other manufacturing processes a new mindset must be employed to make the right product and make it right. To understand why this change is so important for the design of AM components, let’s look at a few common features to 3D printing and how they change the engineering framework.
Generative design and topology optimization
Perhaps the flashiest facet of additive manufacturing in discussions is implementing simulation to optimize the form and structure of a component. The biotic geometries are also likely what you thought of when 3D printing was first mentioned. These types of geometries are not entirely novel, however, they have been possible in the digital realm for years. Additive is merely the first manufacturing technology that could create these complex shapes at a reasonable cost. And could is the operative word, while nearly every geometry is theoretically possible with AM, there are physical limitations of the machines. This is why the design process is still so important, even when the optimal geometry stems from computer-generation. This might involve setting minimum thicknesses on parts so that there is no overheating during manufacture. Or if the goal is a sustainable product, the front-end design work may go deeper to understand the balance between the performance benefits of an exact biotic design vs. a truncated version that can be manufactured more traditionally at greater volumes.
Lattices and internal structures
The insides of AM components can also be drastically different from traditional designs, and for many applications they are the value differentiator from other manufacturing methods. Lattices are possibly the most common example of internal structures, allowing designers to shed excess mass from their products – saving material costs, manufacturing time, and improving part performance. Another application of these internal structures is internal fluid routing. That might be for directly cooling components, supplying lubricants, and even feeding a stock material more efficiently in a manufacturing process. All of these applications require concrete understanding of how the parts will be manufactured with AM, and to varying degrees. Many of the internal structures needs to be self-supporting within the greater part to prevent deformation and remove support structures which may not be removable after printing. In NX Design for Additive Manufacturing these tasks are aided by wide range of checkers to ensure the designs are compliant, as a way to expedite the learning process on these best practices.
Implicit modeling
The last technology is actually one of software rather than physical capabilities of additive and it makes the previous sets of geometry accessible in a CAD environment – implicit modeling. Most CAD applications require precision geomtery tow function correctly with the more traditional machining operations and geometry is modeled explicitly to meet those requirements. But with AM, the machine is already creating a digital approximation of the geometry and is not creating a part of a standardized block of material like one might find for CNC manufacturing processes. Implicit modeling enables working with the complex surfaces from topology optimization processes directly and better control of lattice structures by removing a need for hard-coding geometry.
Changing tomorrow’s products with AM
The opportunities available with additive manufacturing are expansive and will bring many innovations to a number of fields through performance increases, efficiency improvements, and greater sustainability. But getting there means learning the design process alongside the manufacturing process, especially for goals around sustainability which require far more context and a balance of competing requirements to solve. Siemens has the experience to help guide that learning as well as the infrastructure and tools to get it running in your business. To learn more about 3D modeling for additive manufacturing, check out some resources from NX and get ready for the upcoming product launch this year.
Siemens Digital Industries Software is driving transformation to enable a digital enterprise where engineering, manufacturing and electronics design meet tomorrow. Xcelerator, the comprehensive and integrated portfolio of software and services from Siemens Digital Industries Software, helps companies of all sizes create and leverage a comprehensive digital twin that provides organizations with new insights, opportunities and levels of automation to drive innovation.
For more information on Siemens Digital Industries Software products and services, visit siemens.com/software or follow us on LinkedIn, Twitter, Facebook and Instagram.
Siemens Digital Industries Software – Where today meets tomorrow