Developing AM orthopedics faster than ever
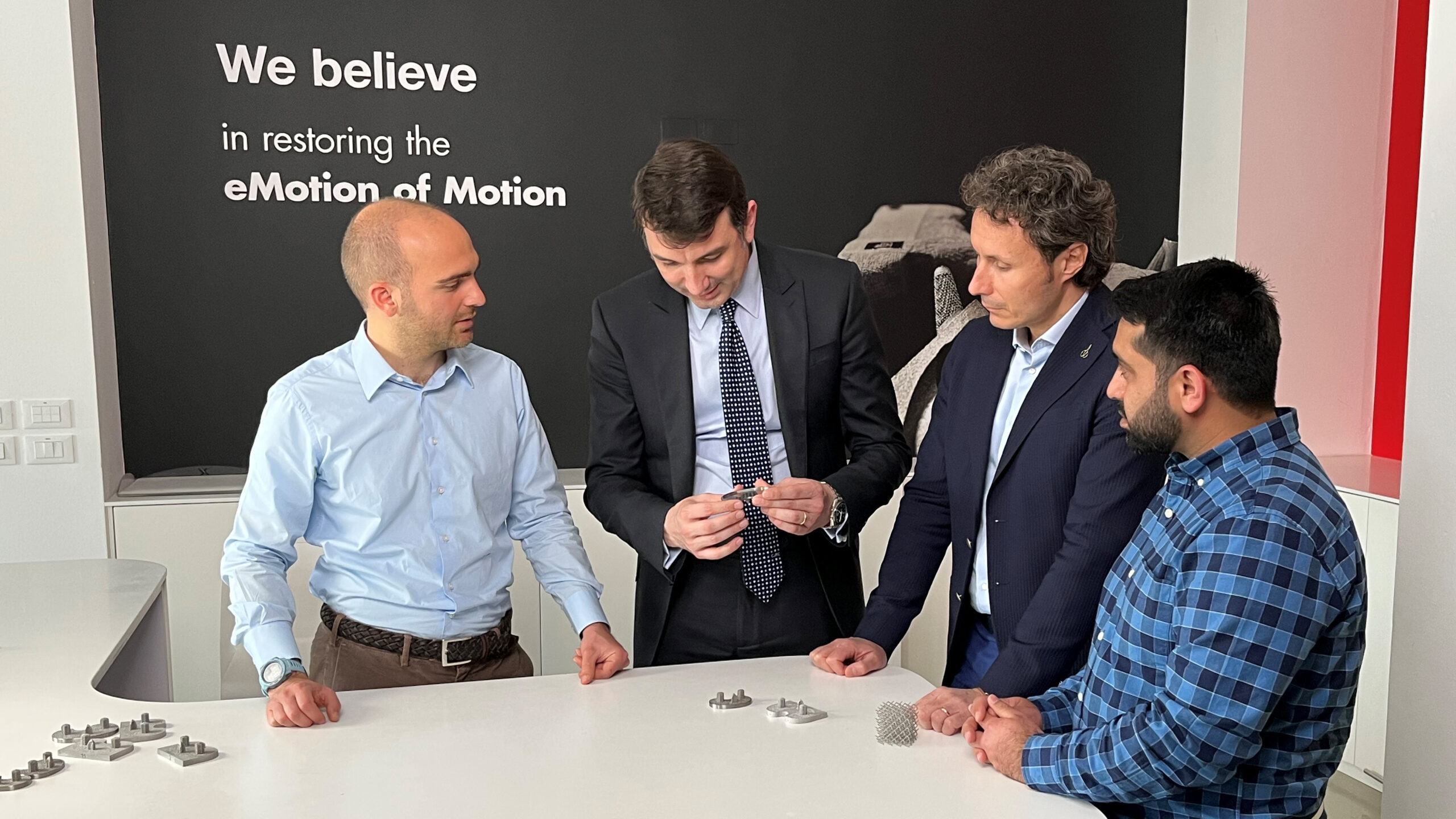
The strengths of additive manufacturing (AM) are well suited to the field of medical technology, for many of the same reasons as it is for aerospace. High customizability is not a hindrance to manufacturing as it is with more traditional manufacturing methods, and the advantages of complex geometry add more performance in the same design envelopes. LimaCorporate saw these advantages early on for their implants. The technology and methods were not well-established, however. When Lima first embarked on printing in titanium, nearly half its builds had to be scrapped. But this small company’s big bet on AM helped them beat competitors to major orthopedic innovations. And now LimaCorporate is set to disrupt the industry again with a revolutionary knee implant.
The vision
LimaCorporate embraced additive manufacturing because they wanted to improve the osteointegration of its implants. By producing a cellular solid incorporating a lattice structure, the company could improve how the bone would grow around its implants. Traditionally, the joint replacement would rely on cemented arthroplasty to affix the implant to the bone and eventually some bone ingrowth to the surface, provided by plasma spray coatings for surface roughness. But this method results in limited osteointegration, so the implant is strongest on day one and degrades thereafter. Printing the implant with AM enables lattice structures on the implant surface to aid osteointegration from the much higher surface roughness and geometric variation. A few companies had achieved this with multi-material implants, but LimaCorporate saw the opportunity to combine the bulk material with a proprietary lattice structure. The result was Trabecular Titanium™ (TT).
Doubling down

Their first commercial release was an acetabular hip cup, using electron beam melting printers to manufacture the TT structure. But the innovation came with its own challenges. Beyond the material and geometric development, there were no international standards for printed implants. And once it was eventually certified by the regulatory bodies, demand outpaced expectations. The implants went on backorder, and LimaCorporate had to keep purchasing new printers and qualifying them to fulfill orders. Since the 2007 release, they have produced over 150,000 hip cups, with some of the highest patient ratings in the industry. But that success meant re-investing in TT-based implants and improving the development process. Their next challenge was developing a knee replacement. It entailed a massive increase in complexity to design. Hip ball joints are almost trivial compared to the wider range of motion and combination of forces required in a knee replacement. Making the more complex implant viable required a better development process, with fewer roadblocks.
Removing digital roadblocks

Communicating their needs to Siemens engineers, LimaCorporate began collaborating on how to improve the software workflow – reducing the dependence on STL files and enabling integrated design with the TT proprietary lattice. By having access to a broad software portfolio with NX AM, the team was able to further enhance the design of their tibial plate for knee replacements. The digital part was tested virtually to determine the perfect combination of peg locations based on the stresses identified in the walking studies. The software was able to calculate the optimal mix of solid and lattice Trabecular Titanium to guarantee the required strength and stability for patients.
With the new Siemens AM solution, design changes have become much easier to implement. Without relying on STL files, the team is able to edit most features of the tibial plate parametrically because they are mathematically linked to the geometry of the printed part. Better yet, those changes are associative through their PLM system to track specific implants throughout development and even delivery to surgeons. The shift to a more comprehensive digital approach increased the team’s confidence and reduced modeling and prep time by 50 percent. But the accomplishments are only the start. The team is continuing its collaboration with Siemens to further integrate the medical implant workflow into NX.
Defining pragmatic AM
The work being done by LimaCorporate is amazing, and their recent results with the knee implant hold great promise for their current and future endeavors. Now, the team is working on creating a pragmatic approach to its AM workflow and making it a more streamlined and profitable process. Their clear vision and willingness to collaborate on the entire development process bodes well for LimaCorporate as they bring more amazing implant to the market, faster than ever before.
To see how LimaCorporate designed the tibial component of its knee implant and hear from the doctor who performed the first surgery with the new technology, check out their full customer story here.
Siemens Digital Industries Software is driving transformation to enable a digital enterprise where engineering, manufacturing and electronics design meet tomorrow. Xcelerator, the comprehensive and integrated portfolio of software and services from Siemens Digital Industries Software, helps companies of all sizes create and leverage a comprehensive digital twin that provides organizations with new insights, opportunities and levels of automation to drive innovation.
For more information on Siemens Digital Industries Software products and services, visit siemens.com/software or follow us on LinkedIn, Twitter, Facebook and Instagram.
Siemens Digital Industries Software – Where today meets tomorrow