Uncovering smart manufacturing – Transcript 1
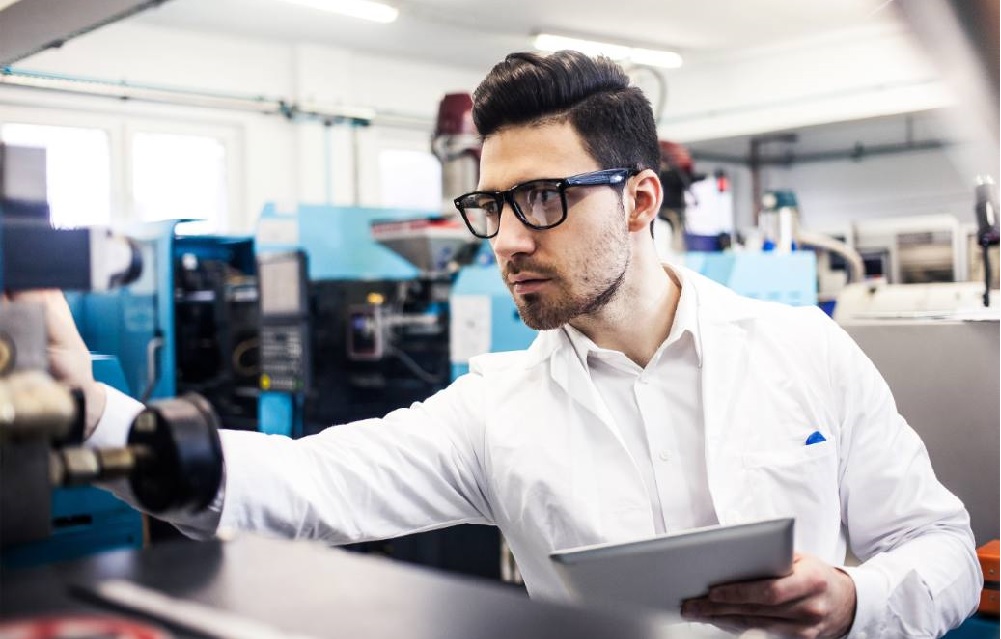
We kick off our new season of the smart manufacturing podcast series with Conor Peick, technical writer for global marketing at Siemens, speaking with Dale Tutt, VP of the Industry Strategy Team at Siemens, and our resident expert on smart manufacturing, Rahul Garg, VP of Industrial Machinery and SMB Industries at Siemens.
The focus of this podcast discussion is from an industrial machinery perspective, discussing the impact of customization and customer demand on manufacturing while also considering supply chain issues and competing globally. Join us as we dive into this compelling topic. Please read the transcript below or listen to the audio podcast on Acast.
Read the transcript
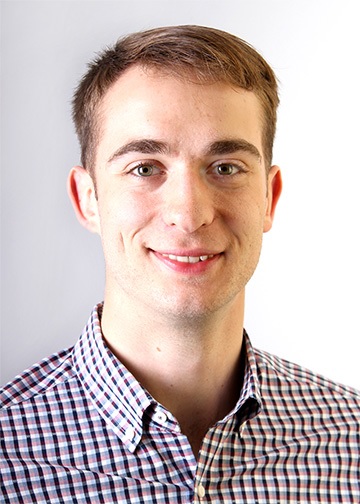
Conor Peick: Hello, my name is Conor Pieck, one of your co-hosts for this podcast today, and I’m a writer for Siemens Digital Industries Software’s Thought Leadership team.
Dale Tutt: And I’m Dale Tutt, Vice President of the Industry Strategy team at Siemens Digital Industries Software.
Conor Peick: So, in a new series of podcasts, Dale and I are going to be joined by seasoned experts from around Siemens Digital Industries Software to discuss the trends, technologies and opportunities affecting some of the largest and most important industries today. So, today, we’re going to be joined by Rahul Garg, Vice President of the Industrial Machinery, and the SMB Program at Siemens Digital Industries Software – going to be saying that name a lot.
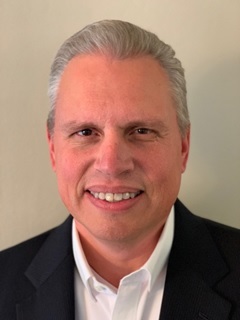
We’re going to discuss the trend towards smart manufacturing systems and how it is enabling companies to overcome the challenges of product complexity, sustainability and a whole lot more. So, welcome, Rahul. Thanks for joining us today. We’re really excited to have you. So, just to get started, maybe you could give us a brief introduction of yourself, your experience and what you’ve been doing in this fascinating industry.
Rahul Garg: Thank you, Conor and Dale. Very excited to be joining you all on this very important and emerging topic. I’ve been in this industry for the last 30 years, helping customers leverage key technologies in their growth processes, and having been part of many startups, having faced many small and medium-sized companies, that is a part of the role I play. So, having worked very closely with the larger manufacturing companies building their own equipment and small manufacturing companies supplying to larger companies; it’s been a very interesting journey for me, getting these companies to take advantage of new and emerging technologies in their growth processes.
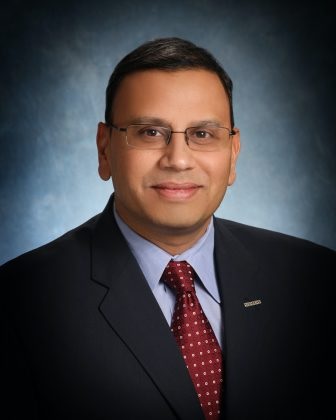
Conor Peick: So, I think we’ve got the right guy to cover this topic. That’s what it sounds like. Rahul, what do you see as the major challenges in the industrial machinery and manufacturing industry today?
Rahul Garg: If you look at it from an Industrial Machinery perspective, Industrial Machinery is a very broad group of companies when I look at the customer base or the companies that I work with. They are the companies that provide the equipment that goes into a larger manufacturing company, and into a larger manufacturing organization. For example, the equipment that goes into the factory shop floor of General Motors or Lockheed where they are building the parts or assembling the equipment or their products. So, the companies that I typically work with are faced with pretty complex issues all the way from their end customers, demanding a lot of customization for their specific shop floor needs, making sure that the products that can be built from those machines can be done at the fastest possible time. Significant supply chain issues that most companies are facing today, even the key labor shortages. One of our customers I was just talking to yesterday in Germany, has openings for 350 engineers to keep up with the demand, so the backlog of orders that they have gotten, they cannot find enough people. It’s definitely becoming a big issue. And then, obviously, meeting all of the needs of what their end customers are looking for, in terms of using less energy, less resources and making sure that their equipment is performing at the highest possible rates.
Dale Tutt: A lot of these challenges that you talk about are really common in a lot of our industries. I think, across the board, you see more and more demand for these highly customized products. And, of course, every company is dealing with supply chain problems right now. And I just think about some of the challenges that I’ve seen throughout my career with the workforce and just getting enough people of the right skill sets to work on some of these areas. So, I’m curious, how have you seen the Industrial Machinery industry and manufacturing companies really trying to tackle some of these challenges? What are the strategies that they’ve been using?
Rahul Garg: One of the things that have happened is it started, perhaps pre-COVID, the pre-pandemic era where companies were overlooking as to how to take advantage of technologies – digitalization being one of those key enablers – to really bring their design manufacturing processes to the next level. The pandemic has hyper-propelled that process where these companies are now needing it and see it as a necessity to drive digitalization into their businesses. And as part of that process of driving is how they will build these machines to become smarter, and obviously, enable their end customers to make their manufacturing processes smart as well.
The whole concept of smart factories leads the equipment manufacturers to create and build those smart factories or smart machines. So, I definitely see digitalization as a very important enabler that is going to necessitate companies to start doing things differently and continue to strive in this highly competitive market. And as part of that process of digitalization, there are some key capabilities that they are beginning to think about. One is this whole concept of OT and IT convergence. This is a very important area for the equipment manufacturers, as they look at how their end customers will be using their technology or using their equipment or their machines or their products. Looking at closed-loop manufacturing and execution; how the actual process is going to be delivered; how the customer orders will be delivered in the fastest possible way. And then looking at closed-loop quality, ensuring that the products and the parts are delivered right the first time. So, these are some next-level details in terms of the whole digitalization concept that companies are looking at.
Conor Peick: I’m glad that you brought some of those things up. And I think before we get into the idea of smart machines and smart manufacturing, Rahul, I’d like to dive a bit more into those topics you just mentioned; the idea of OT/IT convergence and closed-loop manufacturing and things like that.
Dale Tutt: Rahul has really made some good points on these topics. And I’m excited about what we’re seeing with the convergence of some of these operations. The factory operations are now starting to become more holistic with facility operations. So, can you elaborate on some of those things that you’ve mentioned? How are these manufacturers really leveraging this digitalization manager, or to improve the processes and their facilities across all their operations?
Rahul Garg: Let’s just take one at a time. So, the whole concept of OT and IT convergence. This topic is something that’s been spoken about, to be honest, for quite a few years now. But it’s coming to a head where companies are recognizing that they must look at this very seriously, because this convergence is becoming real as possible now. It’s something that is necessary to drive the production efficiencies that they’re looking for; and to drive the operational efficiencies that companies desire. What this whole process allows you to do is, through the whole OT (Operation Technology capabilities) you are able to monitor very closely what’s happening on the factory floor, and the operations that are occurring on the factory floor. And with IT, you are managing the business operations and the business systems. So, this whole idea of OT and IT convergence, what you’re enabling is real-time process capabilities that can monitor what’s happening on the shop floor, and the business impact that is happening with the work going on the shop floor. And at the same time it is enabling the shop floor to react in a more expedited manner to requirements that may be coming from the business systems. Customer orders changing, providing more flexibility into your manufacturing operations; we spoke about the ability to drive more customized orders. So, all of that is driven through a business operation system, and ensuring that the production shop floor systems can react to those changing demands in a very quick, flexible way. So, that’s the whole value that OT/IT convergence is going to provide that extreme flexibility and extreme visibility to driver changes as necessary. That’s one key topic, Dale, as you were just talking about.
The other big area is around this whole concept of closed-loop manufacturing and execution. This is where you’re trying to get to the next level of detail and providing better controls throughout your manufacturing operations to effectively maximize your production throughput. Every factory is trying to figure out how to get the maximum out of the assets that have been used in the factory. So, this whole closed-loop manufacturing process ensures that the customer orders that are coming in are scheduled in the right way; tracked in the right way; and that they are being billed to the right designs that they were created for by engineering systems. And once the orders go through the execution process, once the orders are being fulfilled, once the products are being delivered; you then have the ability to provide feedback into your order systems and into your engineering systems. Because as you typically go along, there are issues that you may encounter during the manufacturing process that may have not been captured or have not been thought about in your engineering systems. So, having that closed-loop manufacturing execution system allows you to bring some diverse organizations in a typical company together to make it very easy to have that constant monitoring.
Conor Peick: What about automating facilities and some of the processes that go on within there? Does digitalization help manufacturers increase the amount of automation in a facility?
Rahul Garg: Oh, for sure. To me, I think of digitalization or automation as the new equalizer. In the past, automation was caught off as something that’s going to help reduce your cost. But now, it’s really helping you go to the next level of ensuring high availability, helping you manage your supply chain in a much better way, and most importantly, improving your time-to-market. That’s one of the big challenges that most companies are facing today because of supply chain issues and other challenges like labor shortages. So, that whole time-to-market can be significantly improved taking advantage of automation. That’s something I really see as a big advantage going forward.
Dale Tutt: Excellent points. I was excited about the automation that you can put into the factories now, and how much has changed over the years in so many industries. We’ve been talking about flexibility for a long time. But it really seems that as companies start to adopt automation, they go through a lot of work: designing, and then testing, and then verifying that the robots and the automation that they’re adding, that it works properly. And a lot of times they become these big monolithic structures within their facilities. But obviously, robots are still very valuable to the manufacturing industry, but how can you adapt them that they become much more flexible so that they’re more in line with the needs of modern manufacturing as opposed to being these large, monolithic structures within a manufacturing facility?
Rahul Garg: That’s a great point and great question there, Dale. The way I look at it is with the challenges of today around supply chain global uncertainty; many companies are looking to bring their manufacturing facilities back onshore. And that is becoming a big driver, in terms of them looking to change the way they do their manufacturing and making sure that it is competitive with what was there before, and making sure that it gives them the ability to remain competitive going forward as well. So, automation, robotics, is something that’s going to become very, very key, and then this move-forward; even helping you all the way from reducing the effort to even including robots in your manufacturing process. But they are working together with the humans, becoming a “cobot,” as one would call it; helping the human being lift heavy objects, move sensitive objects around as necessary, and being more agile and flexible in that process as well. So, this is something that’s really going to be driving a lot of changes in the way companies take advantage of automation and robotics, for sure. And a lot of that being driven by a need to have manufacturing facilities as close as possible to where the products are going to be used and not relying on some offshore capabilities.
Dale Tutt: It’s very exciting that the automation and digitalization, it’s going to give a lot of flexibility. And it can really go a long way toward reducing some of the disruptions that we see on the factory floor, whether it’s design changes, you’re able to adapt a little bit more quickly, or closing some of the gaps on the labor shortages that we see in so many locations nowadays. And it is a great opportunity, as companies start to restore some of their factories, and they’re maybe setting up more greenfields that they look more at automation and robotics. And with the digital twin in play now, you can certainly stand up these facilities a lot faster. It’s hard to imagine you’re working side by side with a robot, that’s probably something we would not have thought about 10 or 15 years ago. But they’re probably going to be a lot quieter, won’t tell bad jokes, so that’s okay. So, anyway, moving on. You also mentioned closed-loop manufacturing, which is really a key part to really making sure that your processes are working as intended and you can optimize them. So, you mentioned closed loop quality as part of that. What do you mean by closed-loop quality?
Rahul Garg: To me, quality is, obviously, a well-defined term: You have some expectations and you’re making sure that your product outcome is meeting those expectations. So, closed-loop quality is basically ensuring that you are optimizing, and then having complete visibility all the way from planning to quality, to delivering on the quality, and then, obviously, minimizing scrap rework and improving the overall product that’s taken to market. As part of that whole process, what customers need to do is plan for the quality upfront and develop well-defined capabilities and expectations, define failure modes right up front so you know what to expect and how to address those issues, and even look at environmental conditions that may impact your quality and your overall production processes to make sure of the way you are going to be resolving those kinds of environmental condition changes. And that’s where even better definitions become more critical. And then, based on those issues and ensuring that as you’re assembling your parts, your systems, you check against those engineering requirements or the quality requirements that have been set up upfront. And most importantly, monitoring through that process, capturing requirements, or the as-built conditions, doing a check against the closed process. It is data collection, and then feeding it back to your front-end design process and looking for non-conformance and compliance.
Conor Peick: So, Rahul, that sounds a bit like MBSE to me, that idea of collecting requirements and making sure that you’re tracking data throughout the lifecycle. Is that something that manufacturers are looking into or something that they’re dealing with?
Rahul Garg: That’s a very interesting comment. MBSE, Model-Based Systems Engineering, is not exactly a term, Conor, that most manufacturers would use in the concept of manufacturing. It’s, typically, as a concept thought of as something that’s most relevant and useful for the front-end design and engineering processes. Just based on the question, and if we take a step back; conceptually, MBSE actually makes a lot of sense. Having a requirements-driven process to drive your production and drive your quality, certainly is part of your closed-loop quality process. So, this probably needs some more discussion; it maybe a topic for us to further deep dive into in the next conversation.
Conor Peick: Well, hopefully, I haven’t started any internal fires or anything with that question.
Dale Tutt: As we look forward, you realize the closed-loop quality and whatever we’re going to call our MBSE process. All this will require machines that have intelligence and connectivity to be able to really maximize the opportunity for data to be gathered, and then really processed to get the insights that you need by pulling this data from the edge and feeding it back into the digital twin so that you can use that information and optimize your processes. So, my question then is what’s involved in the creation of these smart machines to help realize this future vision of work in our factories?
Rahul Garg: The whole concept of smart machines is twofold. One is ensuring that as you’re designing the machines, as you’re building the machines; you can capture information about how the machine is performing. So, it’s that front-end design engineering process, making sure that you’re capturing all the right relevant information from the machine. It could be something as simple as a temperature on a motor to the vibration on a spindle unit. All of these are very critical pieces that feed a lot of intelligence into how the machine is performing. And that’s where the smartness comes in, as now you can capture the usage of the of the machine and how it’s being leveraged on the floor. And being smart enough to recognize any issues that may come down the road. Typically, any heat or electrical spikes are indications of something going wrong. So, being able to monitor that information and saying, “Okay, hey, wait a second, I’m sensing a lot of heat in this area.” Typically, if there’s heat going in there, maybe there’s a bearing that’s potentially going to be breaking. If the bearing is going to be breaking some critical part of your machine is going to break down. So, before you have that breakdown, you recognize that upfront heat moment and use that intelligence to create some proactive action. So, that’s where many of the smart machine design processes are coming into the picture, which are going to lead to the smart manufacturing processes. So, really making it easy for customers to have a more agile and adaptable manufacturing process, so that they can ensure, eventually, what companies are looking for. The Triple Zero concept: Zero downtime, zero defect and zero harm. So, that’s where the whole concept of smart machines can really be leveraged by manufacturing companies.
Dale Tutt: That’s very interesting. Let’s dive into that a bit more. As I think about factory environments, when you have a machine go down, obviously, you have an unscheduled downtime within the factory, and that’s a huge disruption for the factory and all the people around it and the other equipment, creating bottlenecks. But the other downside is that when those machines break down, there’s usually something being made on that machine. And it’s not uncommon for that part to get scrapped or require some serious rework because the machine didn’t do what it was supposed to do. So, it is vitally important for a lot of our customers and manufacturing companies around the world to help manage that process better and be more predictive. So, what kind of technologies are we talking about? Presumably, I guess this technology is being integrated both at the individual machines themselves, but then also being integrated at the factory level. Is that correct?
Rahul Garg: That’s pretty much right. Technology is enabling this kind of smartness to come into the whole manufacturing process. Some key capabilities are encompassing a few of them, I can mention IoT, which really allows you to capture real-time information around the performance of the machine. So, that’s where the IoT technologies come into picture. Secondly, Edge devices, which enable you to do a lot of processing right on the shop floor, where you don’t have to feed the information to some remote side to make any decisions. Thirdly, artificial intelligence and machine learning – again, another key capability that can be used to be more proactive in the way issues are identified; by collecting a lot of data, looking for non-conformance, non-regular data, and being able to quickly make decisions on that kind of information. Finally, the whole concept of the digital twin. To me, this is truly one of the most critical game-changers in terms of how companies can really set themselves up for the future; by having a digital twin of your machine, and being able to see how your machines in your factories are performing, and being able to evaluate the changes that may be necessary on a digital environment first before introducing it into your factory. A change in a digital environment doesn’t cost anything; it’s a zero cost. It makes it very easy for you to do many things differently, if you choose to, before you instantiated on your production floor or before instantiated in your mission. So, these are some unique capabilities that have come to bear over the last few years. And customers are slowly but surely recognizing it and starting to take advantage of this in a very aggressive manner.
Conor Peick: That’s really fascinating. Before we close out for the day, Dale, do you have any last questions or thoughts for Rahul? And Rahul if you have anything you’d like to address, here’s some space to do that as well.
Dale Tutt: Thank you, Conor, and Rahul, for this discussion today. But one of the things that I’ve been thinking about is how much this is going to change the future of work; how we work and how people work in these factories, and how they interact with the machines and the equipment around them, and how do we make parts. So, there’s pretty big element of changing the lives of the factory workers, and I think in a good way. But then there’s one other aspect that maybe we can touch on here as we wrap up. We’ve talked a lot about how we’re working in the factory, but we haven’t really talked too much about what’s the impact on sustainability and the energy usage within a factory, or the waste that’s maybe being created through some of these manufacturing processes. So, I think, there are some opportunities there as well. And maybe Rahul, I’d like to hear some of your thoughts on that as well as we look at what the future of work looks like for these factories.
Rahul Garg: If you look at the overall sustainability-related impact globally in the environment, there are two or three big contributing factors. One of them is what we typically think about in terms of gasoline, and vehicle movements, and passenger cars, and trucks and all that. But one of the biggest contributing factors to energy consumption are factories. They are the engines of the world producing goods; and to run those engines, you need energy; to get energy, you have to rely on some fossil fuel or some other mechanism to, eventually, drive the electricity requirements of factories. And those are, obviously, huge contributors to the environment. Anytime we can think about how to reduce a 5% change in electrical power requirements of a motor, which is typically the equipment that’s “running the factory,” having a huge impact. So, from my point of view, I think sustainability, and factories manufacturing machines, they have a very strong relationship, and a strong potential for a huge impact on what kind of an effect we have on our planet.
Dale Tutt: Excellent, great insight on that, Rahul. Thank you.
Conor Peick: Well, Dale and Rahul, thank you guys, again, for joining me today. And I really enjoyed having this discussion and getting to hear both of your expertise on some of these topics. So, just to wrap up, I would like to thank the listeners as well for coming in, and we’ll be back in the future with another expert from Siemens. So, until then, take care yourself, and we’ll see you soon.
Xcelerator, the comprehensive and integrated portfolio of software and services from Siemens Digital Industries Software, helps companies of all sizes create and leverage a comprehensive digital twin that provides organizations with new insights, opportunities and levels of automation to drive innovation.
For more information on Siemens Digital Industries Software products and services, visit siemens.com/software or follow us on LinkedIn, Twitter, Facebook and Instagram. Siemens Digital Industries Software – where today meets tomorrow.