Uncovering smart manufacturing – summary blog
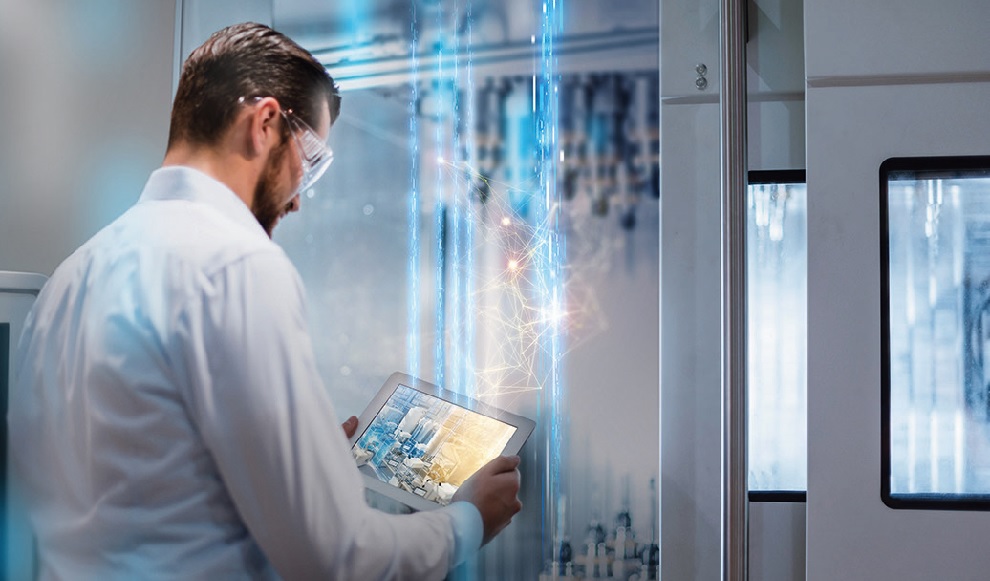
The trend toward smart manufacturing systems enables companies to overcome the challenges of product complexity, sustainability, and much more. Therefore, there are significant challenges in the industrial machinery and manufacturing industry.
A broad group of companies provides the equipment that goes into larger manufacturing companies and a larger manufacturing organization. An example of this would be the equipment that goes into the factory shop floor of General Motors or Lockheed, where they are building the parts or assembling the equipment or their products. So, there are complex issues causing end customers to demand customization for their specific shop floor needs to ensure that products be built from those machines quickly. Other issues like the supply chain and critical labor shortages only further complicate all companies.
So, it is essential to meet all customers’ needs using less energy and resources and ensure that equipment performs at optimum levels. Our experts, Conor Peick, technical writer for global marketing at Siemens, speaks with Dale Tutt, VP of the Industry Strategy Team at Siemens, and our smart manufacturing expert, Rahul Garg, VP of Industrial Machinery and SMB Industries at Siemens Digital Industries Software.
Listen to the Uncovering Smart Manufacturing podcast.
Some of these issues began pre-COVID when companies were overlooking how to take advantage of technologies – such as digitalization – to bring their design manufacturing processes to the next level. Furthermore, the pandemic hyper-propelled this process with companies needing to drive digitalization into their businesses. Also, there was the issue of how they would build these machines to become smarter and enable their end customers to implement smart manufacturing.
Smart factories lead equipment manufacturers to create and build smart machines. Digitalization is a crucial enabler that necessitates companies to do things differently while striving in a highly competitive market. Digitalization requires vital capabilities:
OT and IT convergence looks at how end customers will use their technology, equipment, machines or products. It also considers how the process of closed-loop manufacturing and execution is delivered; and how the customer orders will be delivered quickly. Additionally, it considers closed-loop quality, ensuring that the products and the parts are provided right the first time.
Factory and operations are becoming more holistic, coinciding with the concept of OT and IT convergence. This convergence is becoming essential to drive the production and operational efficiencies that companies vitally need. Using OT (Operation Technology capabilities) allows a company to monitor the operations occurring on the factory floor. And with IT, it manages the business operations and business systems. So, the whole concept of OT and IT convergence enables real-time process capabilities that monitor what’s occurring on the shop floor and the business impact.
Simultaneously, the shop floor can react expeditiously to requirements from the business systems. Customer orders are dynamic, requiring more flexibility in manufacturing operations to drive customized orders. It is promoted through a business operating system to ensure production shop floor systems can react to changing demands quickly and flexibly. This aspect is the principal value that OT/IT convergence provides extreme flexibility and visibility to drive necessary changes.
Closed-loop manufacturing and execution is another critical attribute. This technology allows a company to move to the next level of detail and provide better controls throughout the manufacturing operations to maximize production throughput. Every company must establish how to yield maximum benefits from the assets used in the factory. The entire closed-loop manufacturing process ensures that customer orders are coming in as scheduled; tracked correctly; and billed to the correct designs that engineering systems created for them. When orders go through the execution process after the orders are fulfilled, and products are delivered, there is the ability to provide feedback on the order and engineering systems. Issues can arise during the manufacturing process that may have not been captured or have not been thought about in the engineering systems. Therefore, having a closed-loop manufacturing execution system provides the ability to bring some diverse organizations in a typical company together to make it easier to have constant monitoring.
Sustainability-related impact globally on the environment, with several contributing factors, is another critical factor. One is gasoline, vehicle movements, passenger cars, and trucks. Also, there are contributing factors to energy consumption via factories. They are the engines of the world producing goods, and to run those engines, you need energy; to get energy, one must rely on some fossil fuel or some other mechanism to drive the factory’s electricity requirements. So, of course, these are huge contributors to the environment. When you think about a five percent reduction change in the electrical power requirements of a motor – this is typically the equipment that’s “running the factory” – it equates to a considerable impact. So, sustainability and factory manufacturing machines have a strong relationship and a strong potential for a significant impact on what kind of an effect it has on the planet.
Learn more in the full audio podcast about other attributes that uncover the benefits of Smart Manufacturing.
Xcelerator, the comprehensive and integrated portfolio of software and services from Siemens Digital Industries Software, helps companies of all sizes create and leverage a comprehensive digital twin that provides organizations with new insights, opportunities and levels of automation to drive innovation.
For more information on Siemens Digital Industries Software products and services, visit siemens.com/software or follow us on LinkedIn, Twitter, Facebook and Instagram. Siemens Digital Industries Software – where today meets tomorrow.