Manufacturing a better energy industry with additive
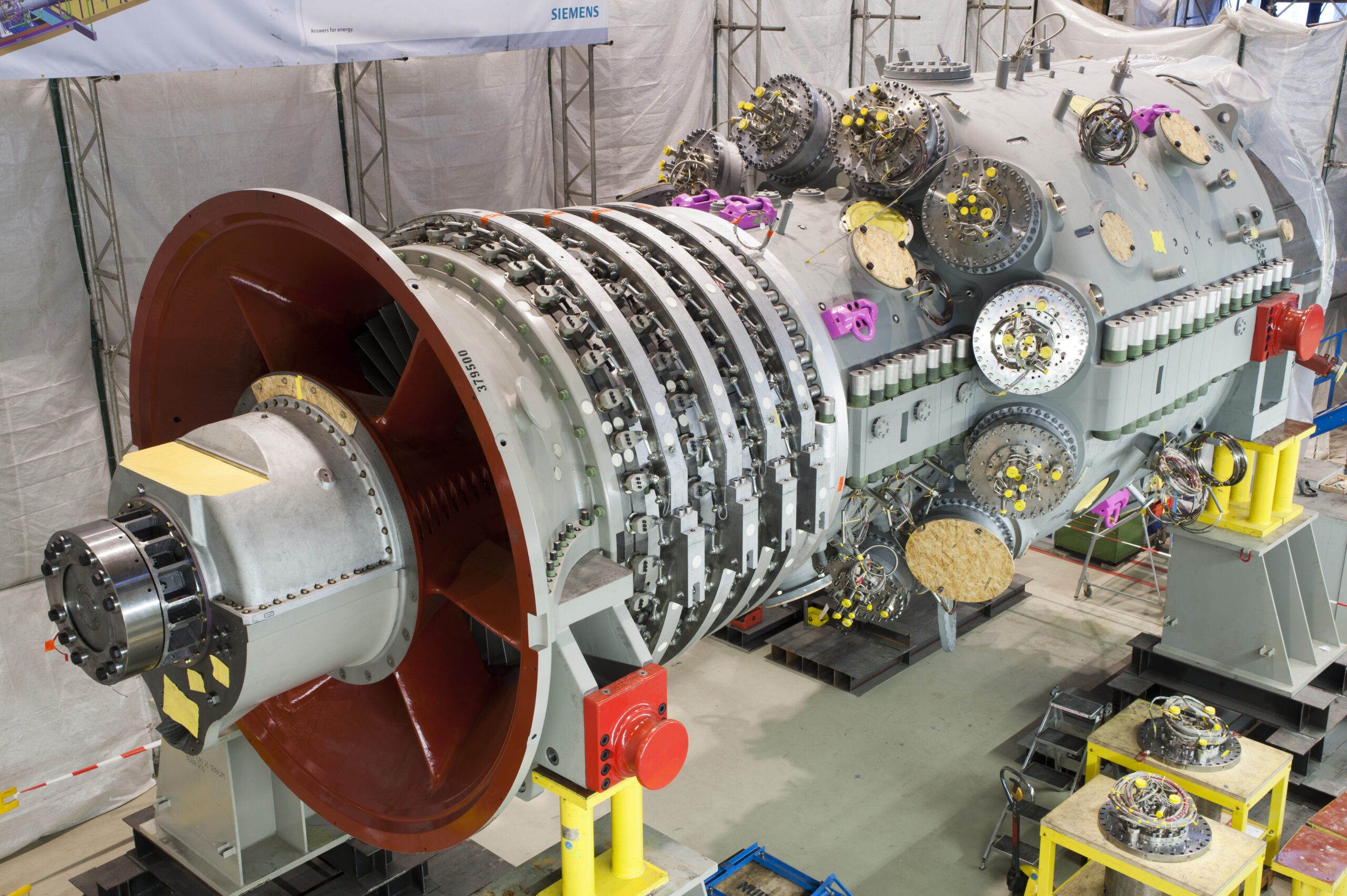
If you had a chance to listen in to episode six of this season of the Siemens Additive Manufacturing (AM) podcast, or read the summary, you would have heard about the journey Siemens Energy has taken in adopting AM. If you haven’t, it is a great discussion between Ashley Eckhoff and Kevin Sheehan, but essentially being an early adopter allowed Siemens Energy to establish their footing, reinvest in the technology, and even diversify with the acquisition of Material Solutions. But for the second half of their conversation Ashley and Kevin talk in greater detail about some of the innovative projects coming out of the partnership. Together they talk about remanufacturing wear-parts with AM, the role of software in the energy industry writ-large, and where Siemens Energy stands on their additive manufacturing journey.
Remanufacturing renaissance
The industrialization of manufacturing has brought many improvements to life, within and outside of the factory. But the incentive to repair and maintain products was reduced, partially out of lower component costs but partially out of manufacturing specialization. The wheel might be a perfect example of this, moving from wood spokes to solid metal construction raised the minimum performance and reduced manufacturing complexity, but it made repair more difficult. Fortunately, the flexibility of AM as a manufacturing technique eschews the limitations of repairing wear components.
The first trial for Siemens Energy came with their burner tips for natural gas turbines. The harsh environment, historically, meant the tips need to be replaced every so often because the geometry was worn away in some area and deposits formed in others, reducing the efficiency of the system. But, by having AM as a part of operations and manufacturing the team could try repairing the tips rather than replace the entire component – much of which was undamaged. After grinding away the deformations in the component, the tips could be placed into custom jigs in the printer to print the parts back up to their original condition. With success in this application, there was an opportunity to expand the use case into the turbine blades as well, which can also benefit from the customization potential of AM, but that required a more integrated and digital workflow.
Going digital
While AM can provide complex geometries for optimized performance, getting a viable part can be just as complex. Beyond the complex geometries that need to be mapped into an appropriate tool path, there are material eccentricities that can impact part performance and strength, process optimizations to improve printing success, and comprehensive logistics for tracking custom parts from design to installation. The repair process outlined previously speaks to this need as well – the need for an end-to-end digital solution.
Data accuracy and continuity is vital to the Siemens Energy repair process, from the very beginning. The parts have to be machined to a workable state for remanufacture in the printers. Once there is a viable surface for printing, the parts must be placed in custom jigs which act to reposition the printing area to the tips of the burner. Part locations need to be validated with lasers to ensure component precision after remanufacturing. And the printing path needs to be designed to avoid print defects from overheating and collision. While more common for turbine blade repair, custom geometries need to be tracked through design, manufacturing, and delivery to ensure blades make it to the right locations inside the turbine – as they are optimized to the shape and speed of rotation at any given position.
A strong position
The early investment talked about in episode six is highly important to their success, but so are the innovative ideas being implemented, the adoption of digital solutions for the entire workflow, and their reinvestment in themselves through Material Solutions. All of these advantages has led them to over a hundred in-use additive parts for their products and the tipping point for serial production with AM. The internal part of the business is strong, especially compared to competitors in the industry looking at additive. But there is still room for growth on the external business – helping aerospace and automotive customers realize their potential with additively manufactured components. For a more complete analysis on where Siemens Energy stands in the industry and with additive manufacturing in general, episode seven is a great listen. Kevin Sheehan and Ashley Eckhoff share some great stories on how the process has developed and provide more detail on the value of repair to the energy business. If you’d lie to learn more about AM and the energy industry, you may want to check out the first part of this discussion or parts one and two of Ashley’s discussion with John Nixon and John Lusty of Siemens Software, who focus on the energy industry.
Siemens Digital Industries Software is driving transformation to enable a digital enterprise where engineering, manufacturing and electronics design meet tomorrow. Xcelerator, the comprehensive and integrated portfolio of software and services from Siemens Digital Industries Software, helps companies of all sizes create and leverage a comprehensive digital twin that provides organizations with new insights, opportunities and levels of automation to drive innovation.
For more information on Siemens Digital Industries Software products and services, visit siemens.com/software or follow us on LinkedIn, Twitter, Facebook and Instagram.
Siemens Digital Industries Software – Where today meets tomorrow