Intelligent Performance Engineering addresses machine complexity
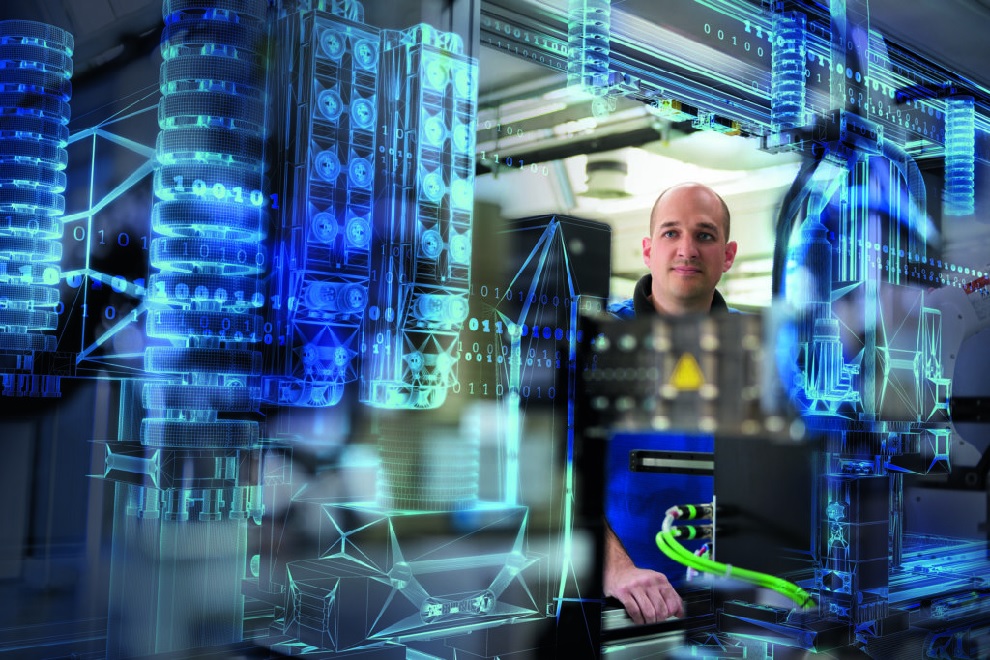
The foremost challenge for machine builders is addressing the customer demand for machine customization and associated complexities.
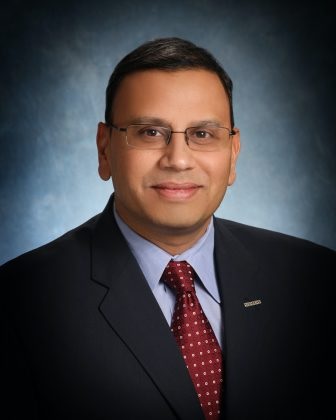
In an Industrial Machinery Digest article by Rahul Garg, Vice president for the industrial machinery and mid-market program at Siemens Digital Industries Software, he discusses how Intelligent Performance Engineering (IPE) unravels the challenges of new engineering development and staying ahead of complex machine introductions.
The most significant catalyst for change is technology and keeping pace with Industry 4.0 technologies with new machine introductions. Additionally, other challenging factors include meeting machine personalization via specifications and requirements. Consequently, machines much meet, exceed, and support the performance requirements of overt use cases. Therefore, it is necessary to distinguish a product from the competition globally by serving customers at a lower cost.
These objectives are the backbone of dynamic technologies, driving companies to consider and evaluate how to meet customers’ needs via digitalization. Therefore, with technological advancement expanding, it is essential to address the demand for flexibility and complexity. Meeting this objective requires machine behavior evaluation with subsequent data going back into the model.
IPE helps to ensure innovative machine designs are delivered as promised via a digital thread, supporting consistency and high performance. This improvement provides essential design parameters: personalization, global competition, and simulation. It also adopts IPE practices for ensuring safety, reliability, and cost-effectiveness.
Implementing IPE with a digital thread is critical as it balances a customer’s need to advance machine reliability and performance, including the ability to evaluate, verify, and test designs.
As corporations continue to provide machines with faster cycle rates, higher reliability, and constricted delivery schedules, simulation must be performed upfront instead of conventional testing of multiple physical prototypes. This change means that IPE simulation and testing can work together effectively to address the crucial needs of modern machines.
When designing new industrial equipment or altering existing ones, it is essential to verify, test and analyze its performance before reaching the customer. So, original equipment manufacturers (OEMs) can adopt an assortment of digital simulation and analysis tools to comprehend design choices that affect the performance and failure of a component, device, or machine. Subsequently, it costs less to address the design process issues than potential problems with machine design in the product development cycle.
Learn more in the article.
Xcelerator, the comprehensive and integrated portfolio of software and services from Siemens Digital Industries Software, helps companies of all sizes create and leverage a comprehensive digital twin that provides organizations with new insights, opportunities and levels of automation to drive innovation.
For more information on Siemens Digital Industries Software products and services, visit siemens.com/software or follow us on LinkedIn, Twitter, Facebook and Instagram. Siemens Digital Industries Software – where today meets tomorrow.
Related links:
Smart Manufacturing podcast 01 – Uncovering Smart Manufacturing
Smart Manufacturing podcast 02 – The Convergence of IT and OT in Digitalized Manufacturing
Smart Manufacturing podcast 03 – Uncovering Closed-Loop Manufacturing
About the author
Rahul Garg is vice president for the industrial machinery and mid-market program at Siemens Digital Industries Software, responsible for global business development. He and his team deliver strategic initiatives and develop solutions, working with industry-leading customers to provide thought leadership on new, emerging issues in the machinery industry. Rahul’s 25-year career includes delivering software-based solutions for product engineering and manufacturing innovation globally. He has held leadership positions in research and development, program management, sales and P&L management, focusing on industrial machinery and heavy equipment since 2007.