The digital transformation behind the James Webb Space Telescope
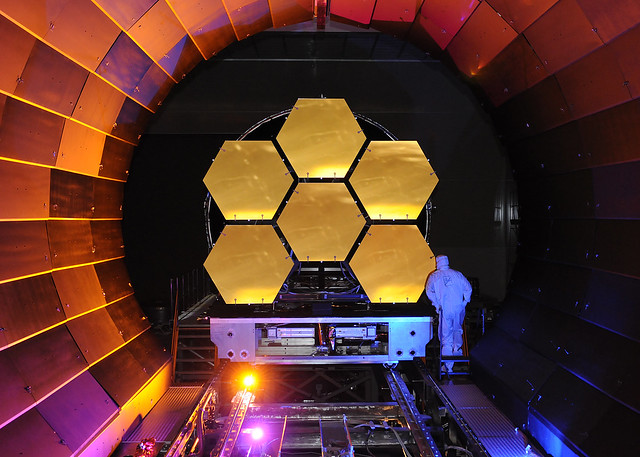
The James Webb Space Telescope (JWST) is one of the most cutting-edge scientific marvels of our time, capturing the beauty of the cosmos and probing celestial mysteries that have eluded us for millennia. The images it has sent back to us are nothing short of breathtaking, some of the most mesmerizing pictures of our universe to date. However, what is not immediately visible is the comprehensive infrastructure of digital software key to creating the James Webb in the first place. The myriad government organizations and private partners who came together in the construction of the JWST utilized a broad scope of digital tools to design, simulate and test the telescopes key components. Many of those tools were provided by Siemens and were instrumental in developing the JWST’s Integrated Science Instrument Module (ISIM), the very eye of the telescope. We at Siemens are proud not only to have contributed to the JWST in a critical way, but also to be part of the digital transformation that will serve as a model for future space missions.
Bracing for space
When it comes to constructing and operating spacecraft as complex and expensive as the JWST, there is only one shot to get it right. Spacecraft experience some of the most dangerous conditions imaginable throughout their mission, from intense vibrations during launch to extreme temperature disparities when in the vacuum of space. On top of that, they will be well out of human reach, meaning there will be no way to maintain or repair them should something go wrong. This goes double for the JWST, which orbits the sun approximately 1,500,000 kilometers away from Earth. With that in mind, the JWST had to be designed to withstand these conditions for its planned decade of operation from the very beginning.
Designing the eye
Digitalization was greatly beneficial for designing the ISIM in particular, as it is a collection of advanced scientific instruments that must work in tandem for the telescope to function. Three out of four of the ISIM’s instruments, the Near-Infrared Camera (NIRCam), Near-Infrared Spectrograph (NIRSpec), and Fine Guidance Sensor/Near-Infrared Imager and Slitless Spectrograph (FGS/NIRISS), all utilize a critical analog-to-digital converter (ADC) to change video and images captured by the JWST into a digital format. The ADC must provide for all these tools while enduring the harsh conditions of deep space for the telescope’s decade-long mission. To ensure this could be done, the engineers at Teledyne Technologies and Lewyn Consulting Incorporated used a suite of electronic design software, now part of Siemens EDA, to simulate the custom ICs central to the ADCs operation. As demonstrated by the incredible images transmitted from the JWST, this strategy worked perfectly.
Other aspects of JWST also benefitted from utilizing digital tools in their development. The Mid-Infrared Instrument (MIRI) was created by engineers at the University of Leicester Space Research Centre, who used the NX and Teamcenter software suites to design, simulate, and manufacture the scientific module. The ability to design and simulate the MIRI virtually before creating a physical model proved to be a very cost-efficient solution. It provided valuable observations not just about the MIRI itself, but also its tool access and the ground support equipment used to transport the instrument to NASA. Additionally, Northrup Grumman utilized a comprehensive E/E systems development software to design the wiring between all the ISIM instruments, while NASA used Simcenter Femap to perform thermal and structural analyses on the fully assembled instrument modules. All the design and simulation tools together form a comprehensive suite of digital tools that readied the ISIM and JWST for their long voyage.
Looking beyond
We at Siemens are proud to have our software serve such a key role in the creation of the James Webb Space Telescope, as well as showcasing the advantages and successes that comes with digitalizing the space industry. The simulation of everything from circuit boards and wiring to mechanical structures and operating conditions improves the chances of successful launches and better prepares spacecraft for extended missions in the most hostile and unreachable environments of our solar system. Further advancing digitization in the space industry will open a path to develop even more advanced spacecraft, granting us the ability to peer deeper into both the mystery and majesty of our vast, uncharted universe.
Siemens Digital Industries Software is driving transformation to enable a digital enterprise where engineering, manufacturing and electronics design meet tomorrow. Xcelerator, the comprehensive and integrated portfolio of software and services from Siemens Digital Industries Software, helps companies of all sizes create and leverage a comprehensive digital twin that provides organizations with new insights, opportunities and levels of automation to drive innovation.
For more information on Siemens Digital Industries Software products and services, visit siemens.com/software or follow us on LinkedIn, Twitter, Facebook and Instagram.
Siemens Digital Industries Software – Where today meets tomorrow