Smart manufacturing key to tomorrow’s advanced vehicles
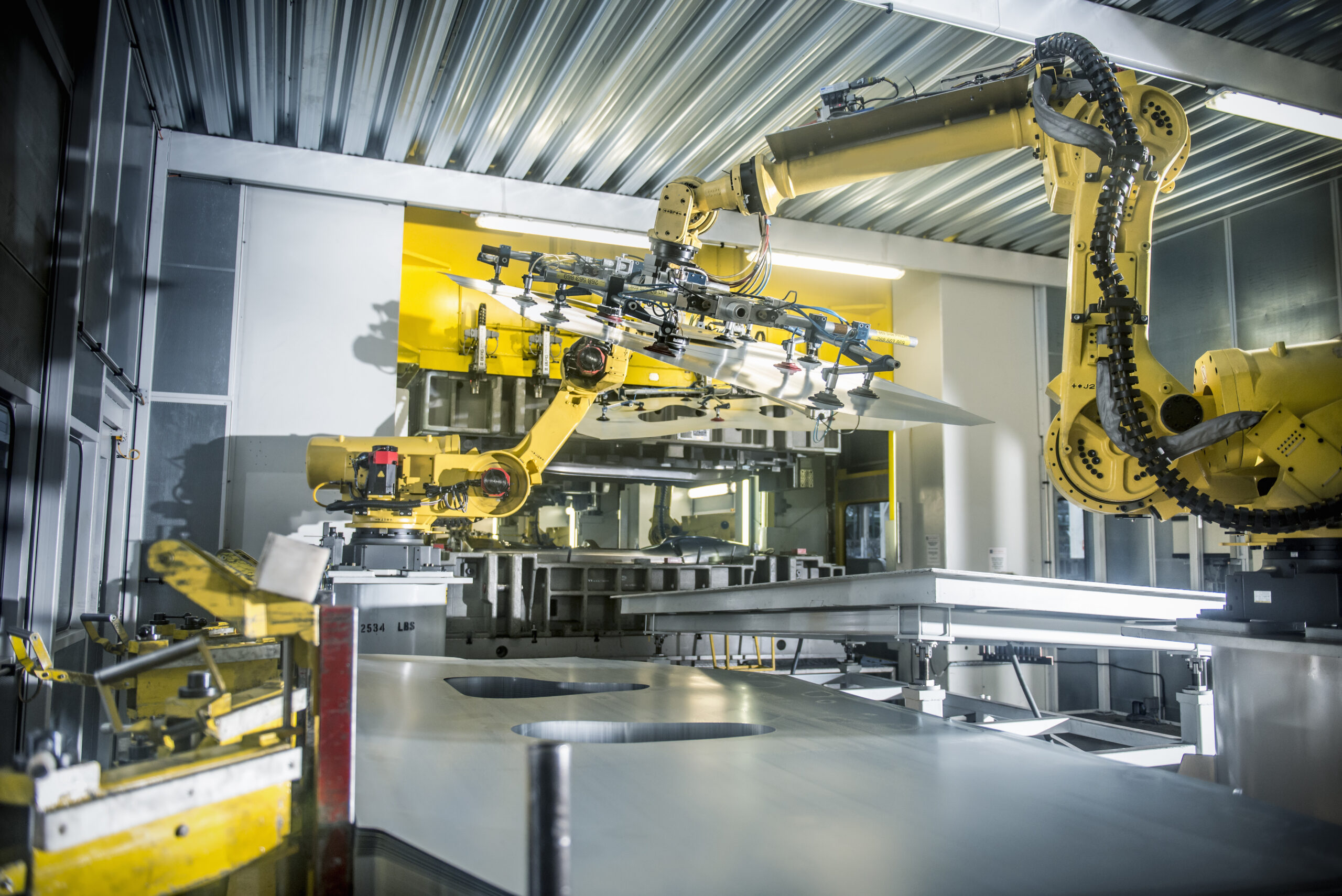
Automakers are under more pressure than ever as the automotive and transportation industries continue to transform at a rapid pace. Technology advancements, such as automated driving systems, 5G connectivity, and electrified powertrains, are transforming the cars we know into more sustainable, accessible, and convenient transportation machines. At the same time, increasingly strong emissions and sustainability directives for vehicles and the production facilities in which they are made are coming into effect around the world. Finally, a rash of new entrants to the automotive market are driving up competition, putting pressure on product development and introduction cycle as both startups and legacy automakers compete to bring the vehicles of tomorrow to market today.
This disruption and transformation in the automotive industry is having wide-spread effects on vehicle design, development, testing, and manufacturing. In this blog we will take a brief look at how the changes in the automotive industry are impacting the production of vehicles, and why increasingly smart manufacturing solutions will be critical to the future of mobility.

The risks of existing processes
Most established automotive factories today are brownfield facilities, meaning that they contain a blend of older and newer equipment. Newer machines are built to share data across a network, whereas older machines are typically data islands. As a result, traditional manufacturing approaches are not able to leverage data in an intelligent way. Especially in today’s market, this can jeopardize an automaker’s business in multiple ways, including production line disruptions, a lack of flexibility in production facilities, and an inability to meet new regulations.
Today, companies must be able to quickly relocate, or duplicate production lines globally as regional politics and economies dictate. They must also deal with increasing pressure to innovate and bring new features to market faster, increasing complexity and decreasing launch timelines, and comply with new sustainability requirements and regulations. Overall, traditional manufacturing processes are falling behind, exposing companies to significant production challenges that may result in a loss of reputation, competitive position and even business.
The advantage of smart manufacturing
Automakers can modernize their manufacturing process by connecting the data of all engineering disciplines to the knowledge of their shop floor. This includes incorporating new machines, that have built-in sensors and processing capabilities, and integrating sensors and processing power into legacy equipment. The integration of sensors and intelligence into production facilities will enable companies to build a closed-loop of engineering and manufacturing data, helping them to monitor and improve manufacturing performance and product quality. This closed-loop of data can also enable companies to predict operational issues in real-time.

So how do they get there? Digitalizing the manufacturing planning, design, and commissioning is the key. Digitalization enables automotive manufacturers to design, test, and commission production machines, lines, and even entire facilities quickly and with minimal risk. In addition, digitalization helps create a continuous flow of information throughout the manufacturing lifecycle, from engineering to the production floor. This digital backbone enables companies to make the most of connected machines by gathering valuable data from the shop floor for use in multiple processes, such as advanced analytics or predictive maintenance programs. With these capabilities, automakers will be able to implement a complete smart manufacturing approach that connects engineering, information technologies, operational technologies, and the shop floor. As a result, these companies will be more adaptive and resilient to market changes while also supporting future product innovation through manufacturing flexibility.
Once the production line has been designed, commissioned, and installed, the automaker can begin production while capturing valuable data from the shop floor. With real-time access to operational data, companies can easily manage and adjust the manufacturing environment as needed. For example, real-time manufacturing data can help identify bottlenecks or pinpoint the source of quality issues on the production line. As this information feeds into the data backbone, it creates a closed loop of manufacturing planning, engineering, and actual operation. In addition, the production data being captured on the line feeds AI, machine learning, and simulation platforms. These can help companies perform predictive maintenance on machinery, prevent quality failures, and initiate corrective actions through the entire production lifecycle.
To learn more, read our article on engineering.com, Smart Manufacturing Drives the Future of Mobility.