Digital transformation vital for building intelligent manufacturing in A&D
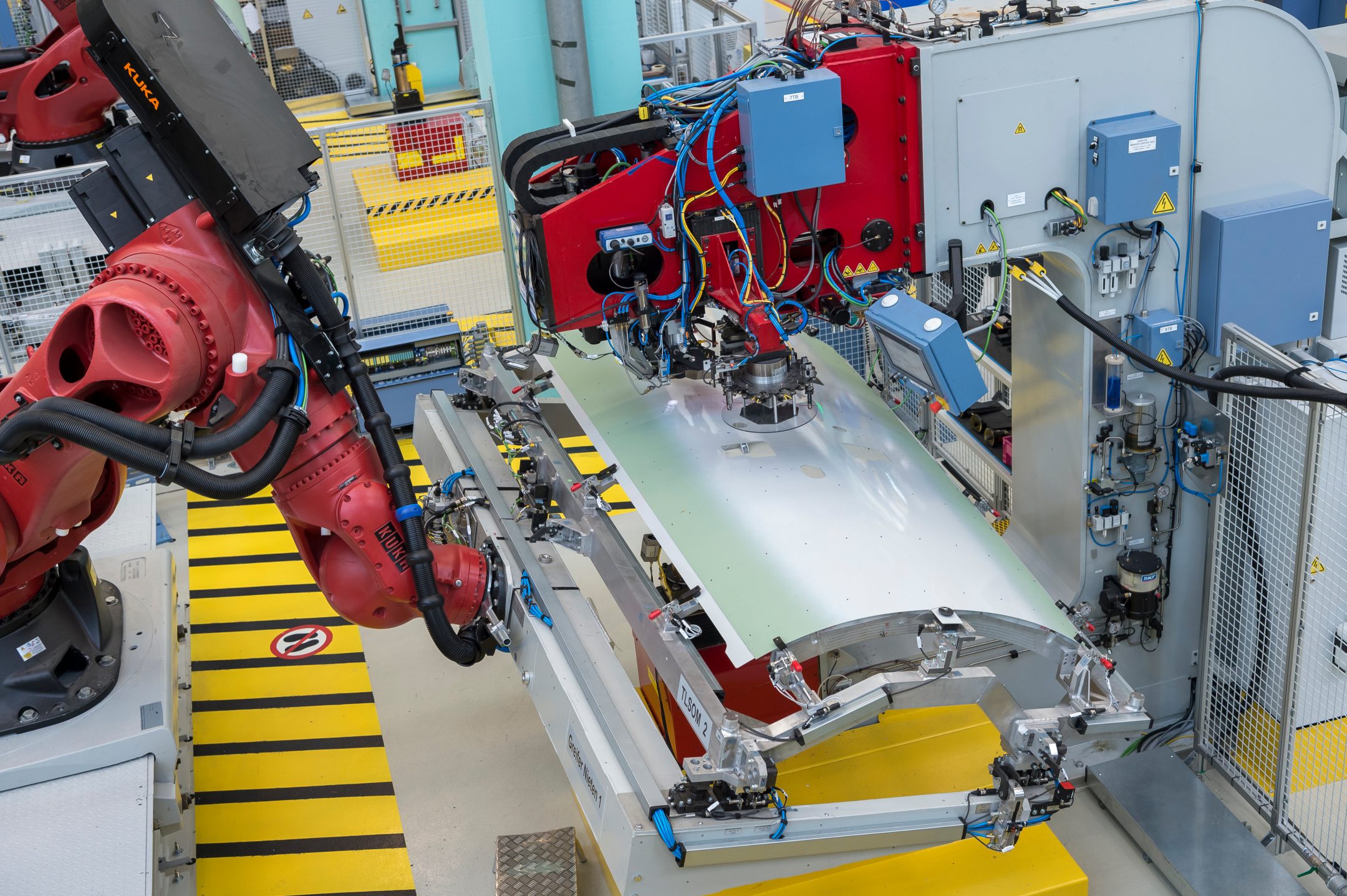
Multiple industries today have begun adopting intelligent manufacturing practices into their strategy, utilizing real-time data analysis to make informed manufacturing decisions. The aerospace & defense (A&D) industry, however, has been slower to adopt such changes compared to others despite industry demands pushing for faster, more efficient processes. This was the topic of a webinar hosted by Aviation Week back in November, where Todd Tuthill, Vice President for A&D Strategy and Marketing at Siemens Digital Industries Software, joined Jimmy Calas, Director in manufacturing engineering at Northrup Grumman, in a conversation about how intelligent manufacturing could help accelerate A&D programs. A critical takeaway from their discussion was that creating an intuitive intelligent manufacturing strategy will require a digital transformation that includes technologies like the digital twin and data-gathering algorithms, as well as innovative cultural shifts.
Digitally transforming factories
A digital transformation would give A&D companies the speed and efficiency necessary for successful intelligent manufacturing strategies, and a key tool that grants this is the digital twin. Companies can build a digital twin of an entire manufacturing facility down to individual assembly lines and machines, allowing engineers to analyze their processes for errors and any areas that could be optimized before operation. This fits into the “shift left” strategy of intelligent manufacturing, the idea of addressing manufacturing concerns well before the manufacturing stage begins. Shift left, especially when combined with the virtual testing capabilities from the digital twin, allows engineers to gather manufacturing data very early when creating a manufacturing plan, saving money, speeding up validation, and ultimately reducing the risk of operational failure. By utilizing the digital twin to virtually build and analyze manufacturing processes, A&D companies will find that they will be able to complete their projects faster, more efficiently, and at a higher quality.
Gather data automatically with IoT
Another beneficial element of digital transformation for intelligent manufacturing is the use of automated data-gathering algorithms. Today, most of an aerospace engineer’s time is spent combing through hundreds of documents containing the data they need, preventing them from performing any actual engineering. Automating this task with algorithms will cut down that spent time drastically, and it could be further enhanced with IoT sensors installed in manufacturing processes. These sensors monitor devices’ conditions in real-time, transmitting data back to the digital twin, where the algorithms can pull data from upon engineers’ requests. Engineers would then have more time to analyze how to improve their manufacturing processes, thereby making those processes more efficient. Thanks to algorithms and IoT sensors, companies will have constantly up-to-date information to better their engineers’ time working and optimize their manufacturing as a whole.
Tools, processes, and people
Of course, implementing digital transformation and intelligent manufacturing requires more than just technology, as Todd and his cohorts in the webinar emphasized how adopting intelligent manufacturing would also require cultural shifts in A&D companies. For decades, companies managed their data physically, using hundreds of paper documents to keep track of aircraft and spacecraft’s numerous complex components. There were no alternatives to this until digital technology became more widespread, and while companies have been making extensive use of digital documentation, some are still hesitant to go further and implement larger strategies like intelligent manufacturing. A&D companies will therefore need to transform their internal cultures to place heavy emphasis on pushing innovation and trusting technologies like the digital twin and IoT sensors. If companies wish to adapt to industry trends and adopt intelligent manufacturing, they will also have to get people on board, and building an innovative-driven company culture is the key to doing so.
A new strategy for A&D
Today’s industry and market trends are encouraging A&D companies to improve their timing, quality, and efficiency, and adopting an intelligent manufacturing strategy backed by digital transformation offers the means of doing so. The virtual testing capabilities of the digital twin and real-time data analysis provided by technologies like algorithms and IoT sensors are just some of the advantages included in such a strategy. Creating cultures that accept them will take some effort, but as with all technological innovations, any hesitancies can be overcome. With the adoption of intelligent manufacturing, A&D companies can improve their manufacturing to face the challenges of today and continue building the aircraft and spacecraft of tomorrow better.
To learn more about the relationship between intelligent manufacturing and digital transformation, you can register to watch the full webinar here.
Siemens Digital Industries Software helps organizations of all sizes digitally transform using software, hardware and services from the Siemens Xcelerator business platform. Siemens’ software and the comprehensive digital twin enable companies to optimize their design, engineering and manufacturing processes to turn today’s ideas into the sustainable products of the future. From chips to entire systems, from product to process, across all industries, Siemens Digital Industries Software is where today meets tomorrow.