Additive is industrializing behind the scenes
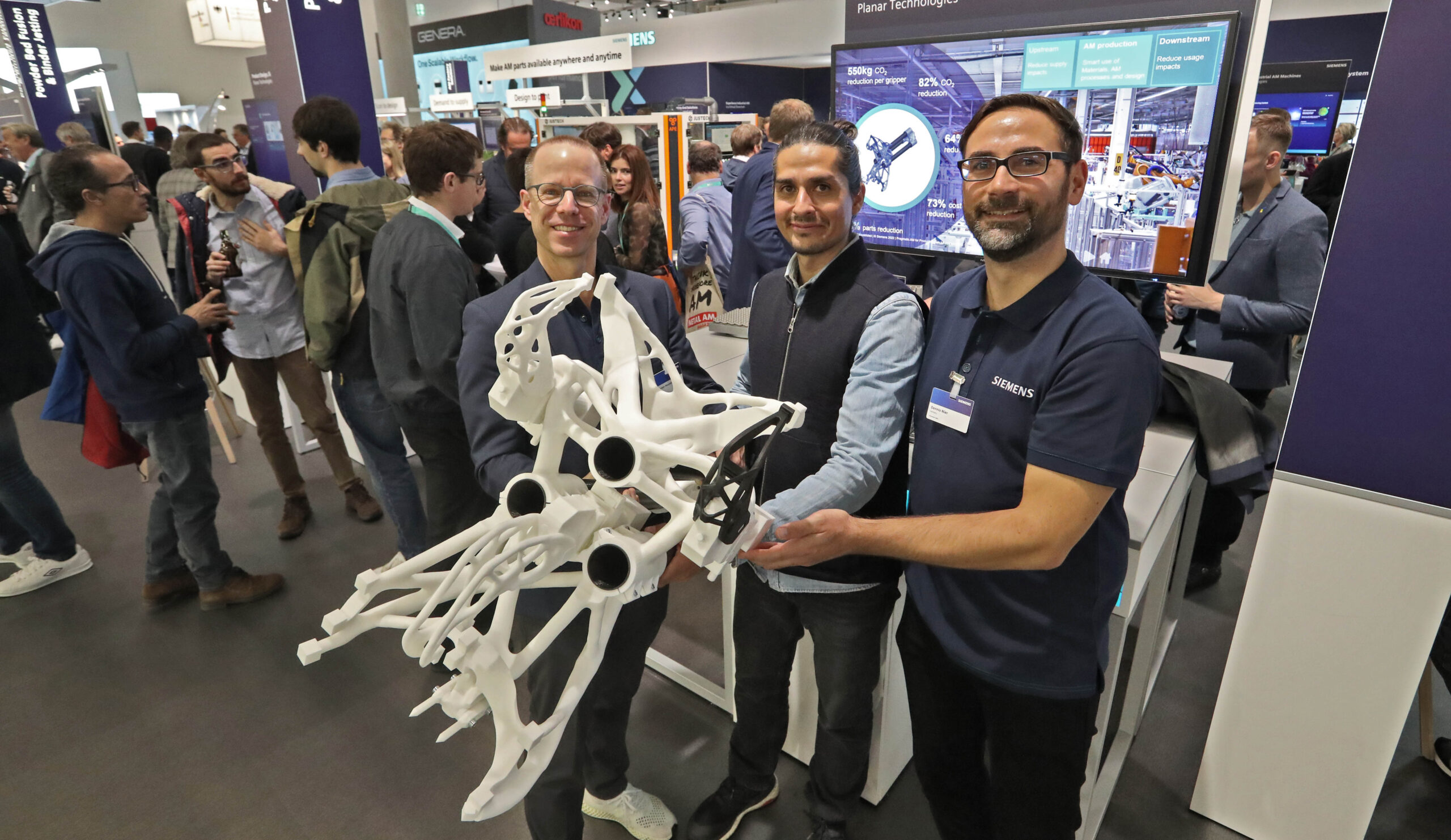
Manufacturing everything with a replicator is still a long way off, but additive manufacturing (AM) has come a long way from its roots as a design aid – coined rapid prototyping at the time. We are many generations past glued sheets of cardboard to get rough ideas of physical size for components. But there are still challenges to solve before AM gets deployed for consumer production and infinitely individualized products. However, that does not mean there is a lack of value in adopting the technologies today.
Cutting edge businesses selling high-performance products have some f the greatest incentives because of the performance benefits afford by the technology – auto racing is possibly the best example. But AM does not have to be seen as the final result of development. In fact, it is gaining a role in optimizing the manufacture of parts in many more industries through the creation of manufacturing aids. And the benefits seen here are helping cut the material, capital, and energy expenditures to make AM a sustainable technology when used effectively.
Compound curves and lightweight componentry are not exclusive to the needs of high-performance auto-sports or innovative medical implants, these shapes also emerge within manufacturing tools. AM can be deployed many different ways in a manufacturing environment to provide value to the complete process.
Hybrid printing machines are great for mold creation when constructing the intricate curves for aerodynamic features on automobiles and even small aircraft, today. Rather than machining down from a large solid block, a printing process can make nearly hollow molds to minimize the investment costs of new designs. That material savings has a direct association with environmental impact – less material is required, more energy is saved during manufacture, and the final product being made can further improve its operational efficiency. For the car example, a more aerodynamic shape means less air friction and drag which increases the effective efficiency of the vehicle – less energy consumption during usage.
Additive molds made in metal printers can also provide greater performance and efficiency to the molding process. By integrating cooling channels and lattices for light-weighting, to injection molding machines for mass production can become much more sustainable. The cooling channels improve the time to part ejection, allowing companies to create more per unit time. And light-weighting the molds reduces the inertial costs of moving the press. Less mass moving back and forth reduces the energy needed to operate these industrial processes – lowering the overall footprint of manufacturing.
Similar to molds, many manufacturing processes require jigs and fixtures to automate and streamline the manufacture of complex products. This is another area where AM can provide benefit today, even if AM is not mature enough for mass production. With the digital tools available today, it is nearly point and click to create custom jigs for production from the CAD models created in design. Say a part needs to be drilled and tapped before it can be assembled – taking the face of the part in your CAD software, like NX, a production engineer can create a custom fixture to hold the part stead for these operations and do so consistently for a run of parts. The part does not have to be perfect the first time nor 100 percent durable for the production lifetime of the product. These parts are typically treated as wear-components and will be replaced periodically, with AM they can be improved continuously to reduce material, improve longevity, and eliminate the reliance on external suppliers in the case of an unexpected failure. AM helps get these processes up and running in no time if printing is available on the shop floor.
There are so many companies applying additive manufacturing in innovative ways, it is just that so many see the value as their secret-sauce. Few consumer products are hitting the market to hint at what is happening behind the scenes, but that does not mean nothing is evolving in the space. Commercial products are only the tip of the iceberg and as more businesses look to optimize their material and energy uses there is no doubt that AM will play a role.
Siemens Xcelerator, the comprehensive and integrated portfolio of software and services from Siemens Digital Industries Software, helps companies of all sizes create and leverage a comprehensive digital twin that provides organizations with new insights, opportunities and levels of automation to drive innovation.
For more information on Siemens Digital Industries Software products and services, visit siemens.com/software or follow us on LinkedIn, Twitter, Facebook and Instagram. Siemens Digital Industries Software – where today meets tomorrow.
Stay up to date with the Siemens Software news you need the most.