Smart manufacturing with sustainability improves all areas of machine design and manufacturing
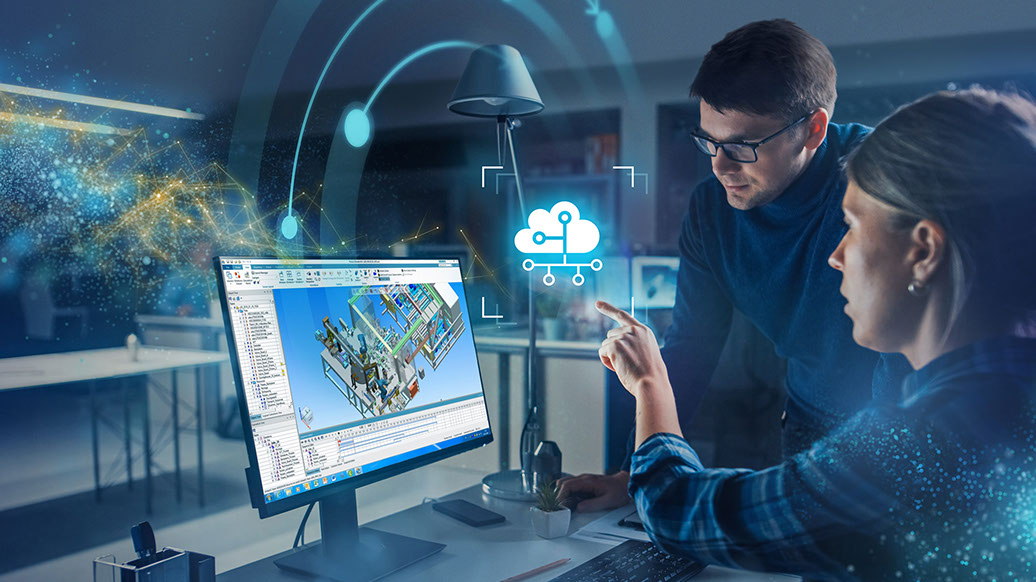
Sustainability is a crucial global topic in multiple industries. So let’s begin by asking how it relates to industries globally. And how is sustainability affecting the global environment and its contributing factors?
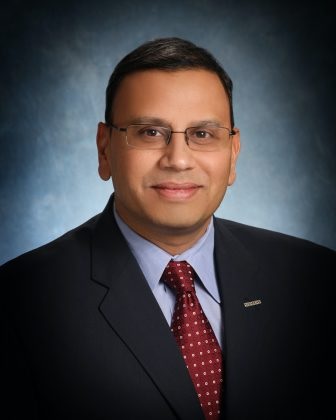
This summary blog will help to answer these questions, based on a
recent podcast with Chris Pennington, Global Industry Marketing Leader for Industrial Machinery at Siemens Digital Industries Software, and Rahul Garg, the Vice President of the Industrial Machinery and Mid-market Program at Siemens Digital Industries Software.
Sustainability considers our industry’s impact on the world and finds that impact minimizes adverse effects by taking actions that contribute to the business to improve the industry’s impact on the environment.
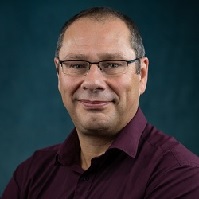
Around one-third of the energy we produce is consumed by the industrial sector, with manufacturing being the majority, providing potential for a significant impact.
Manufacturing sustainability
Sustainability in manufacturing involves some key areas:
- Energy usage is predominantly from use in the production process, which includes carbon production. Carbon production naturally has a negative impact on the environment.
- There is a deliberate effort to ensure outputs in manufacturing are reusable instead of polluting landfills in our oceans. Of course, this includes recycling the product and the machinery used to produce it.
- Sustainability can have a significant positive impact on the manufacturing business. For example, increasing energy efficiency results in lower energy costs and lower carbon production, thus benefiting both the company and the environment with lower energy costs, directly impacting the bottom line.
- Recycling raw materials such as metal scrap wood pallets (bright products) have value in the marketplace, and recycling them improves company financials, reducing any negative environmental impact. These things seem insignificant, but they can have a potent effect. For example, even a five percent reduction in the electrical power requirements of a motor running in a factory can significantly impact the environment.
In considering sustainability and industrial machinery, there is an obvious focus on machine design and energy efficiency to optimize energy usage. Secondly, supply chain elements relative to energy consumption and recyclability practices ensure that machine parts can be recycled and not discarded for the end of the machine’s life.
Thirdly, reporting practices are essential as financial markets, customers, employees, and communities are concerned about sustainable industrial practices. Hence, a company must ensure communication of capabilities that focus on the rest of the world.
Lastly, the development of workflows and productivity, supply chain, carbon neutrality, traceability in the supply chain and the circular economy – tracking the identifying recyclable, remanufactured parts to make it easier to close the loop and ensure what design gets used and when it’s used. Then it can be recirculated back into the design or engineering process or the development process at the end of life. Therefore, it’s vital to tie in the various digital technologies that address these challenges.
Optimizing energy efficiency is needed to reduce energy consumption; therefore, carbon production will be the most significant factor and potential for impacting business profitability and the environment. The result is a win/win.
Energy efficiency
The operations of an industrial machinery company need to manage the sustainability of the operating systems and working practices to be energy efficient. Also, there is the issue of the customers and their machines. Customers desire energy-efficient machines to lower operational costs and increase sustainability.
The result is to produce and sell more energy-efficient machines, creating significant differentiation that provides the machine builder with a competitive advantage in the marketplace.
The most significant goal is to leverage digitalization to optimize the energy efficiency of your whole system. For example, several motors combine to make up part of a line and part of a plant. This links energy and production data to optimize the energy efficiency of machines or motors and the energy productivity of the entire plant. When piecing these together, ensuring complete visibility into the whole production line and evaluating it for optimizing, the production process and energy efficiency is essential. This is where digitalization helps during the usage and front end stages when designing and building machines.
A digitalization systems approach drives intelligence across a digital twin’s entire product life cycle to continuously learn and drive more sustainable industrial innovation. In addition, there is the ability to leverage the digital twin to know a machine is getting used, providing valuable knowledge and feedback on designing and driving more sustainable innovation inside a product and the machines.
Also, carbon neutrality is undoubtedly an essential piece from an environmental and reporting perspective. It requires connecting and collaborating with the industrial ecosystems, including suppliers, distributors, energy producers, and recyclers. They exchange information to enrich the digital twin to identify new option keys to partner and create a sustainable growth plan together.
A comprehensive view lets you define indicators that balance multiple considerations like carbon footprint, performance, and profitability and optimize these in real time. This process ensures you have the mechanism to drive sustainability across a company in the long term.
Machine efficiency
A company making the machines has its own sustainability goals and targets to ensure energy usage, carbon requirements, and recycling requirements are met to the highest standards. Then the machines delivered to the end customers will meet these high energy standards.
The machines are made efficient while selling to the end users and machine operators, ensuring usage perspectives with an ongoing sustainable way of getting consumed. Therefore, a company buying a milling machine from company A or B; might be 20 percent more efficient. So, they are willing to pay extra for that energy-efficient machine. Thus sustainability impacts both the machine operators and the machine builders.
Advanced simulations are performed on the machines to improve energy efficiency. These simulations could include the entire line, like at the operating line to produce a fixed amount of goods, not just the energy usage, but potentially the production line amount.
Also, the material is a factor of energy use – the grade of steel used to minimize the amount of energy while cutting that steel and the movements impacting the production process. Therefore, it’s essential to know how to optimize the material flow inside the operation plan for that energy usage to optimize the machine.
There are several ways to evaluate machine usage and the ability to monitor how a machine is getting used and then make changes based on the usage.
There are various tools to help with this process. The first is the CAM solutions and CAM software. Using a toolpath optimization software can optimize the time required to do a machine part and the energy utilization. Also, a CNC machine that’s cutting tools can simulate the CNC machine usage to reduce energy during the milling or turning operations and provide front-end solutions for the machine design process that can include natural gas or fuel oil burning machines and the combustion analyzer software that can be utilized to increase the energy efficiency of burning those so that less fuel is used in the flow term software. Many industrial processes utilize heat exchanges around and on mechanical refrigeration processes in the form of chillers and coolers. The software can optimize heat exchange design relative to the machine size, cost, and energy consumption.
There are also other tools like optimizing hydraulic systems, along with motors, being some of the highest power users. For example, optimizing all hydraulics usage can reduce the total energy consumed, resulting in improved startup power for various motors and reducing the energy consumed during startup time. These are all examples of leverageable capabilities for any company.
In looking to the future, all companies are trying to get to zero downtime, zero harm and zero waste – the eventual goal of sustainability. We can evaluate how companies are doing against these triple zeros and then see what they can do to improve in the future.
Siemens Digital Industries Software helps organizations of all sizes digitally transform using software, hardware and services from the Siemens Xcelerator business platform. Siemens’ software and the comprehensive digital twin enable companies to optimize their design, engineering and manufacturing processes to turn today’s ideas into the sustainable products of the future. From chips to entire systems, from product to process, across all industries, Siemens Digital Industries Software is where today meets tomorrow