Optimizing manufacturing capacity
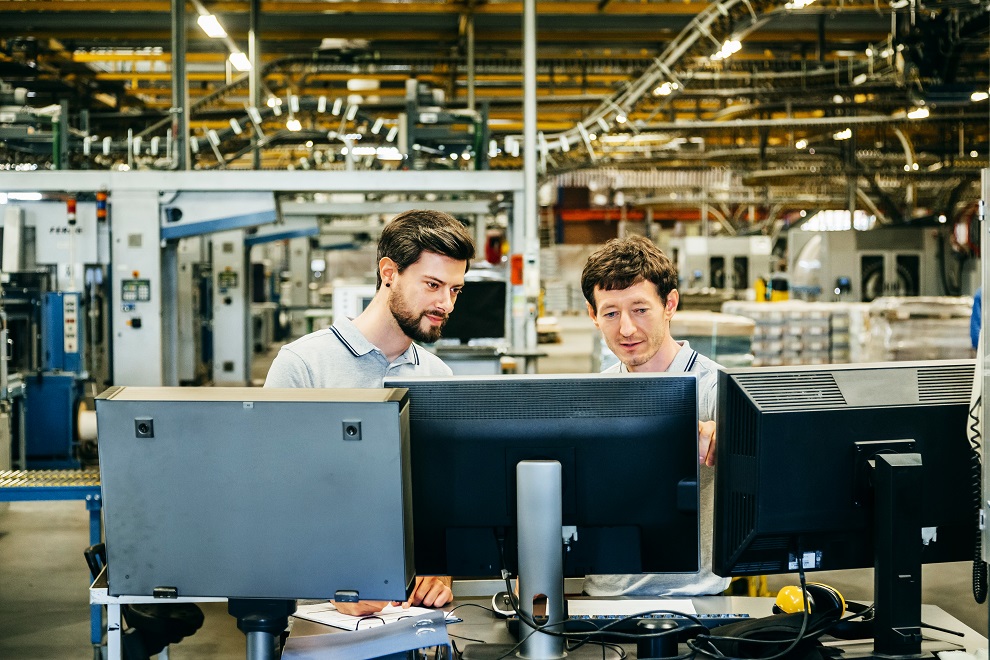
In a recent article in Digital Engineering 24/7, Tom Kevan, writer/editor specializing in engineering and communications, interviews Rahul Garg, VP of industry machinery at Siemens Digital Industries Software, and two other industry experts discussing optimizing manufacturing capacity.
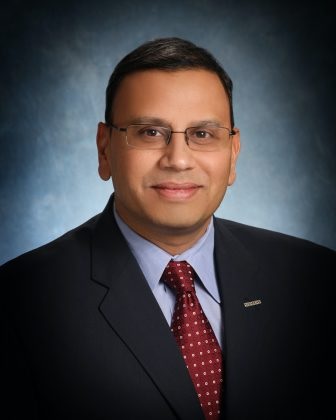
There is an increasing need for shorter order-completion cycles, and more customization with smaller batch options, thus compromising small and medium-sized manufacturers’ abilities to accept production orders. To maintain competitiveness and profitability, companies must adopt a strategy through virtual manufacturing networks typically used by more prominent, established industries like automotive, aerospace, semiconductor, and electronics.
>Read the article.
This change is spurred by economic reasons and robust digital platforms, tools and practices that bring granular visibility throughout the lifecycles of machines and processes across the supply chain. Innovative technologies support small to mid-sized businesses (SMBs) to implement networks and to adapt to a new manufacturing landscape with significant agility and resilience.
Collaborative alliances
Virtual manufacturing networks aim to unite manufacturing enterprises in collaborative alliances so each company can leverage the other enterprises’ free production capacity.
Therefore, companies must identify each network constituent’s core competencies and capacity. A company can then arrange for alliance members to take over the parts of the manufacturing process that are not viable for the larger company. This flexibility allows manufacturers to manage workloads by radically transforming traditional infrastructure in a scalable manner.
The distributed production processes perform simultaneously. Then, the manufacturer that took the original order brings the pieces together at the prescribed time. This method makes it faster to build the entire product than a linear process in a single facility. Also, it reduces network constituents’ costs.
“You’re trying to improve your capacity,” says Rahul Garg, vice president of industry machinery and the SMB program at Siemens Digital Industries Software. “You’re trying to offload some of your capital expenses onto those factories.”
This strategy is gaining popularity among small and medium-sized manufacturers because of being proven for larger companies.
“We are seeing more complex and virtualized manufacturing networks as manufacturers look to increasingly optimize production while balancing their response to demand fluctuations, supply interruptions and rapid onshoring of manufacturing capacity post-COVID,” says Keith Chambers, vice president of management software at AVEVA.
A manufacturer encounters new challenges. So, implementing these collaborative practices increases complexity for manufacturers with integrated business planning and running plants that serve multiple producers simultaneously. Thus, the need for digital tools and practices.
The planning stage
Getting the correct data at the right time while dealing with more complexity and using a virtual manufacturing network requires a bill of process (BOP) describing the product build, its tools and required resources.
The bill of process requires tight collaboration between engineering, manufacturing, and network constituents. Manufacturing process planning software achieves this within the companies’ product lifecycle management (PLM) systems. Basically, the PLM’s workflow, change management and configuration capabilities create the BOP.
Having the BOP data, a company assigns individual manufacturing tasks to identify manufacturers in the network to build the outsourced parts. Also, plant-specific BOPs can be created to accommodate special requirements.
“Siemens can make BOPs specific to different assemblies, different product configurations and different regional needs,” says Siemens’ Garg. ”…An enterprise BOP will be able to easily see what the different variants are, and it becomes a lot more efficient for the company to track the manufacturing process and the throughput of your different plans as well.”
With increasing product complexity and decreasing batch size, integrated BOPs are essential for cost-competitive manufacturing operations.
When the bill of the process is complete, the production plan is communicated to collaborating companies’ primary manufacturing systems—so their manufacturing operations management system and the manufacturing execution systems (MES) implement the final plan.
Siemens Digital Industries Software helps organizations of all sizes digitally transform using software, hardware and services from the Siemens Xcelerator business platform. Siemens’ software and the comprehensive digital twin enable companies to optimize their design, engineering and manufacturing processes to turn today’s ideas into the sustainable products of the future. From chips to entire systems, from product to process, across all industries, Siemens Digital Industries Software is where today meets tomorrow