Launch new spacecraft designs with the digital twin
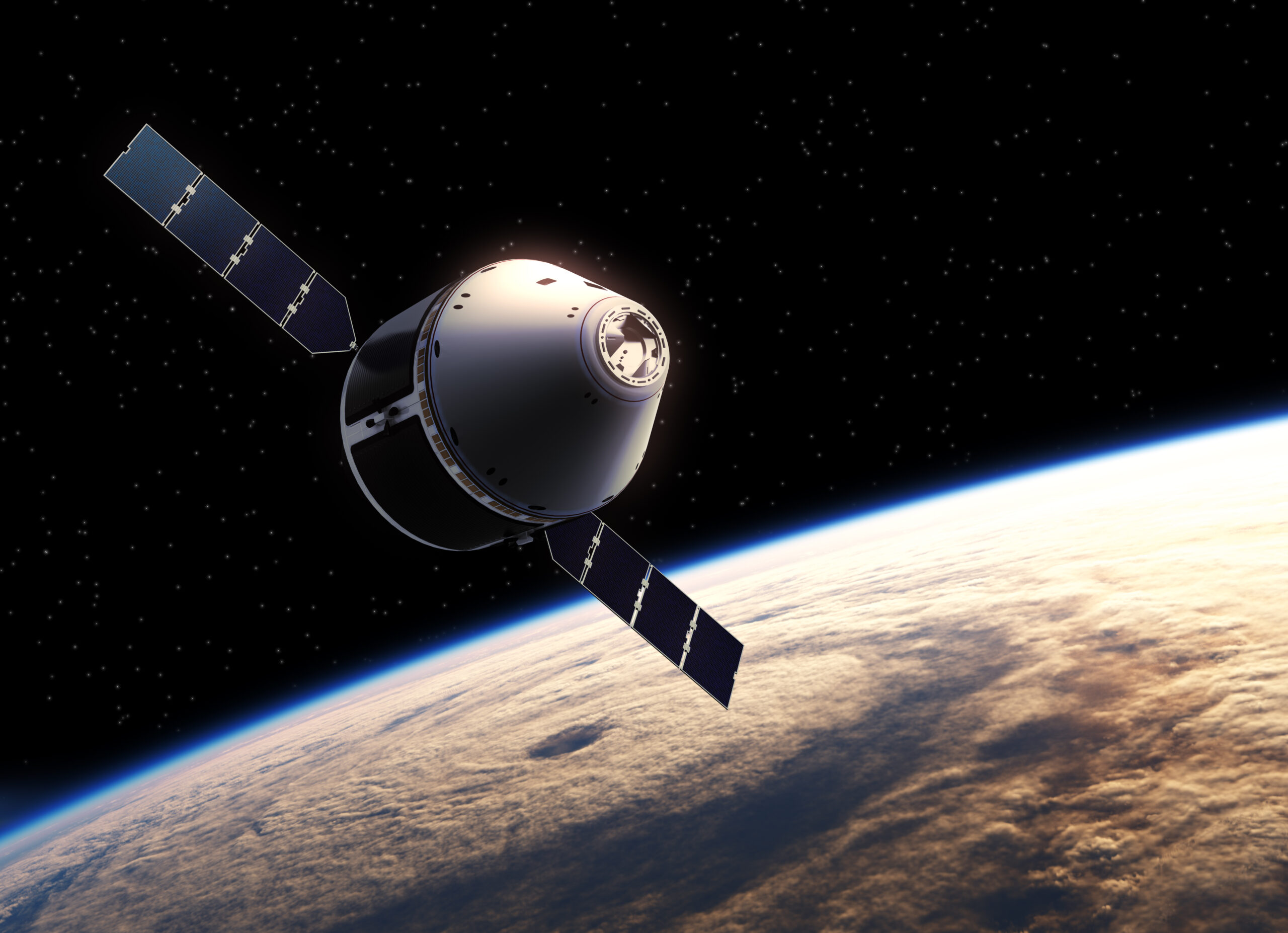
The world is drawing closer to a new space age day by day. Public and private initiatives have been making bold efforts to increase humanity’s reach beyond Earth’s gravity well, from NASA’s planned Artemis mission to the Moon to SpaceX’s colossal Starship. These missions are paving the way toward a more accessible future of space travel, opening new extraterrestrial ventures both exploratory and commercial.
However, historical design methodologies will not be enough to keep space agencies ahead in the game. Spacecraft cost enormous amounts of money and time to construct, factors that can severely hinder an agency’s development processes and reputation. Furthermore, they are incredibly complex products, utilizing a multitude of cutting-edge systems that must operate in perhaps the most hostile environments known to humanity. To successfully carry out space ventures while navigating the demands of the growing space industry, the digital twin can be an invaluable tool.
The many parameters of spacecraft
To their credit, space agencies have decreased monetary costs of spacecraft in recent years, due in large part to innovative technologies such as reusable rockets. That said, rockets still cost tens of millions of dollars to build and can take years to go from design schematics to the launchpad. As more participants enter the race, they will need to offer the fastest times to market and the lowest costs if they want to stay ahead.
Much of these costs and delays come from the immense complexity of space-bound products. New technologies like reusable rockets present engineers with new design requirements, concepts, and system architectures to define and explore. Add those to the numerous systems, advanced materials, and physics that are already considered in current spacecraft, design parameters can grow beyond the point of being efficiently managed by humans.
Complexity in the design process
The significant complexity of spacecraft is made worse thanks to the disconnection between tools and data pervading the space industry. Most if not all space agencies utilize large suites of software tools, sometimes using a different tool to cover each individual spacecraft system. These tools are often a combination of in-house and commercially available tools, and thus cannot integrate and share data between each other. This is especially common in the space industry, as many projects are a collaboration between more than one organization, each using their own tool suites. In addition to managing complex products, space agencies will need to organize their design processes with a unified platform to ensure efficient design.
Of course, informing every design decision is the fact that once a spacecraft leaves Earth’s atmosphere, there will be no way to reach it should it experience failure. Space is home to numerous hazards such as vacuum, solar radiation, and dangerous temperatures ranging from extreme heat to near absolute zero. Ensuring spacecraft are built soundly enough to survive these hostile conditions before they launch is imperative, especially if manned missions are planned to increase in the coming years.
Designing with the digital twin
Thankfully, the digital twin offers solutions to many of these challenges with its simulative capabilities. As a virtual representative of a spacecraft, the digital twin allows engineers to replicate the conditions it will face during its mission, letting them better prepare their designs for the harsh conditions of space early in the design process. It can also act as a single source of truth, integrating data across different software tools and collaborating partners to provide engineers easy access to all data. This affords the additional ability to simulate a spacecraft as a whole product rather than individual systems, meaning engineers can predict how each system would operate with every other one during the actual mission. The digital twin gives engineers ample space to explore and optimize their designs more easily from the very beginning.
Another benefit of the digital twin is reducing time to market by shortening the decision-making process during design. Engineers can run multiple iterations using a virtual model of the spacecraft very early in the design process, giving them immense amounts of information early to inform design decisions later. These decisions can also factor in cost optimization, giving companies better insight into how they can lower the cost of a spacecraft while ensuring it will be operable and safe. Optimizing the decision-making process with the digital twin can give companies a critical edge to stay ahead in the race.
The recent rise in new space ventures is exciting, but participants will need new design methodologies to ensure their success. Fortunately, technologies like the digital twin can allow space agencies to simulate spacecraft virtually and optimize their numerous systems for the harshness of space, ensuring efficient design while lowering costs and deployment time. With the digital twin, companies can better navigate the competition and let the new space age take off quickly and safely.
Check out this white paper to learn more about the digital twin in spacecraft design.
Siemens Digital Industries Software helps organizations of all sizes digitally transform using software, hardware and services from the Siemens Xcelerator business platform. Siemens’ software and the comprehensive digital twin enable companies to optimize their design, engineering and manufacturing processes to turn today’s ideas into the sustainable products of the future. From chips to entire systems, from product to process, across all industries, Siemens Digital Industries Software is where today meets tomorrow.