Closed-loop quality integrates quality and manufacturing to meet expectations
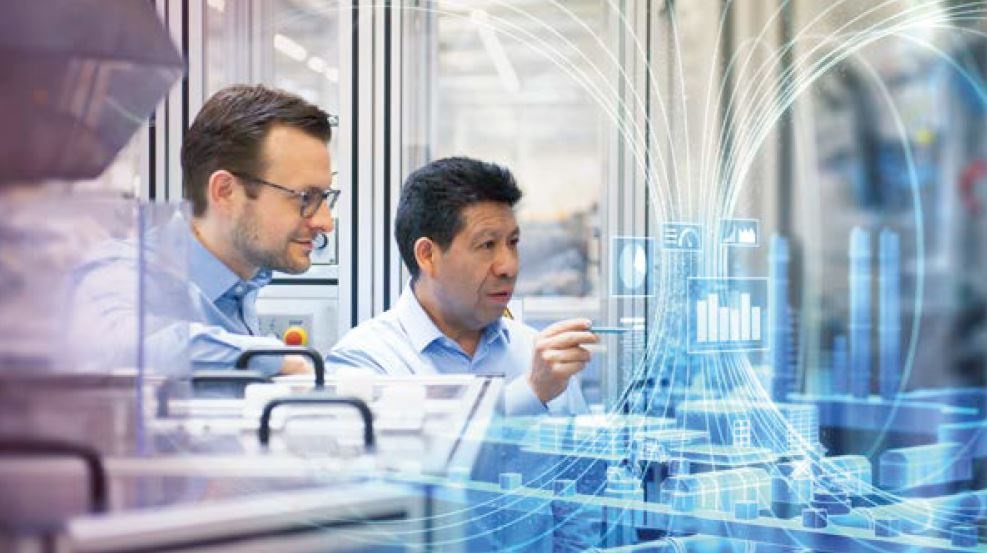
One of the most critical aspects of utilizing smart manufacturing is ensuring products and parts are delivered correctly the first time through closed-loop quality (CLM). Closed-loop quality moves to the next level of details which whole digitalization concept companies are exploring.
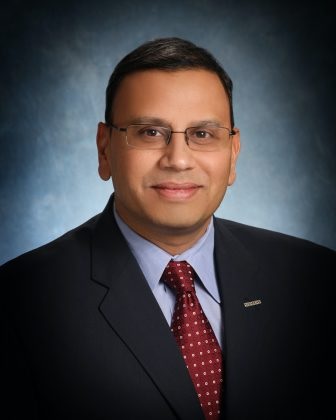
Rahul Garg, vice-president of the market program at Siemens Digital Industries Software, discusses how closed-loop quality can utilize automation and digitalization to significantly reduce factory flow disruptions via design changes, supply chain issues and changing requirements by integrating essential quality into the manufacturing process. When viewing quality and the manufacturing process, one cannot exist without the other, as it’s vital to ensure manufacturing has the correct quality. Also, it confirms that products and parts are delivered on time and to the correct specifications.
Take quality to the next level with digitalization
A company or factory takes advantage of digitalization by taking quality to the next level by integrating quality and manufacturing. Quality ensures that the product outcome meets the original expectations. Closed-loop quality aims to optimize the manufacturing process by identifying and correcting nonconformance early to minimize scrap and rework to improve the overall product to market.
Manufacturers can accomplish these goals by accounting for quality in phases. Therefore, writing a quality plan early in the process is crucial, examining all requirements for quality before building anything and checking it against well-defined capabilities and product expectations, defining where failures might exist.
This process helps find additional details like how a machine operates, defining the environment and conditions that impact overall product quality. These conditions include vibrations, temperature tolerances, and machine conditions, monitoring these closely to ensure that the final product delivers customers’ expectations through upfront planning.
Secondly, monitor quality through this process by capturing output parameters, looking at as-built conditions against requirements, and ensuring that you’re closing the loop on the source of the parameters needed. Then if there are deviations in monitoring the production process, it’s essential to take advantage of IoT, providing an uninterrupted, unhindered data collection mechanism to monitor what’s going on and provide closed-loop feedback to the manufacturing process. Combining these pieces optimizes critical quality requirements and characteristics.
The current environment possesses significant challenges with disrupted supplier issues and the supply chain, monitoring and tracking where supplier parts are coming in, thus significantly impacting the overall quality processes.
Closed-loop quality helps meet customers’ expectations
Lastly, companies implementing closed-loop quality processes achieve a median product compliance rate of 99 percent, with the majority performing between 97 and 100 percent. Conversely, organizations without this capability have significantly more variability in performance, with the majority performing between 90 and 98 percent.
Examining the disparity in performance could mean the difference between being first or second to market, thus avoiding a significant product recall and winning future contracts. Even an insignificant difference can substantially impact an overall business by implementing closed-loop quality.
Closed-loop quality closes the gap to final customer expectations. It shifts quality-related concerns to the entire organization, making it a shared responsibility instead of a disconnected or isolated end process. Therefore, people early in the design and engineering process are looking at the manufacturing and closed-loop processes.
Siemens Digital Industries Software helps organizations of all sizes digitally transform using software, hardware and services from the Siemens Xcelerator business platform. Siemens’ software and the comprehensive digital twin enable companies to optimize their design, engineering and manufacturing processes to turn today’s ideas into the sustainable products of the future. From chips to entire systems, from product to process, across all industries, Siemens Digital Industries Software is where today meets tomorrow
For more information on Siemens Digital Industries Software products and services, visit siemens.com/software or follow us on LinkedIn, Twitter, Facebook and Instagram.