Digitalization and the design challenges of autonomous vehicles
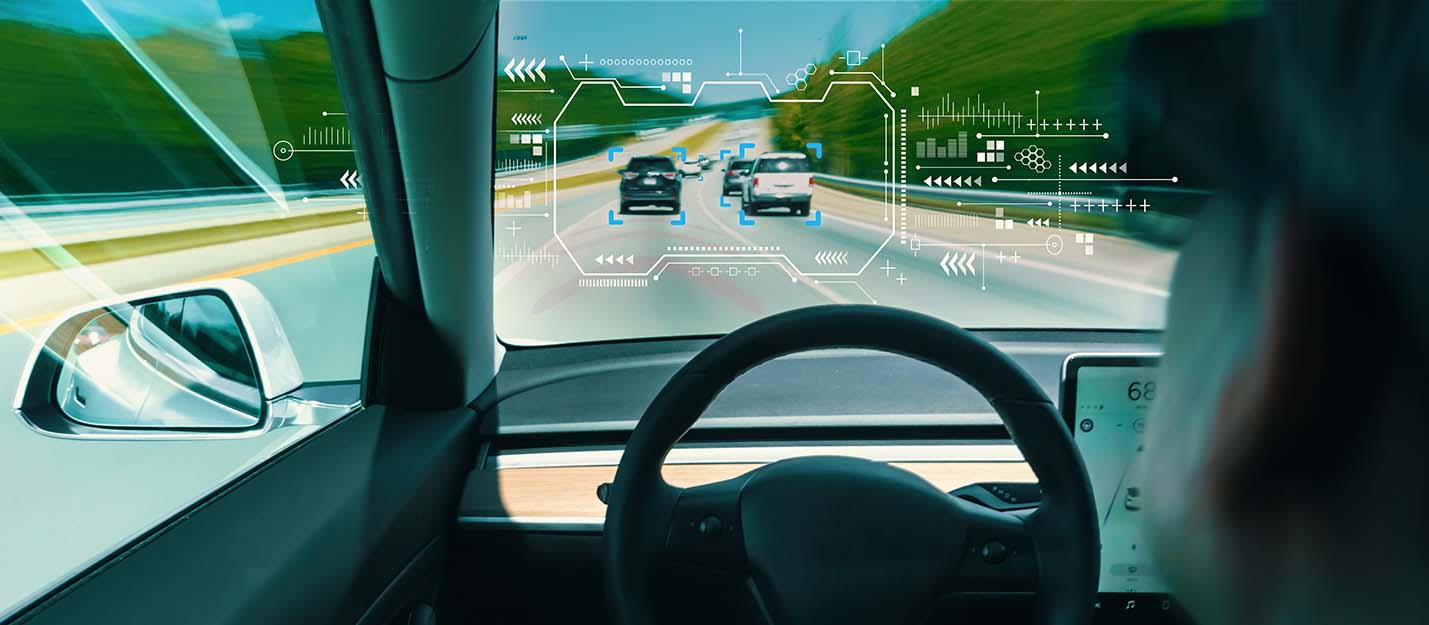
A widespread transformation is taking place in the automotive industry. Changes in technology, societal pressures, and environmental regulations are all pushing vehicles to become more sustainable, safe, accessible, and smart. In response to these trends and pressures, automakers are doubling down on electrification and continuing to invest in the development of automated driving features and autonomous vehicles (AV).
AV development will only become more important in the marketplace as the competition to produce new and advanced vehicle features continues to mount. Automakers today must focus on the development of advanced features and functions to stand out in a competitive landscape. As the emphasis on advanced self-driving vehicle features continues to grow, so too does the design challenge for the engineers.
Automakers will be required to transform fundamental aspects of their businesses and organizations to meet the needs of the future of mobility. Years of development in advanced driver assistance systems (ADAS), vehicle electrification, software, electronics, and other technologies are coming to fruition, driving a massive shift in the composition of the automotive market.

Future of mobility full of design hurdles
The power of onboard processors and the sophistication of vehicle software will continue to grow as self-driving systems develop. Not only will AVs incorporate some of the most complex electronics devices ever produced, but they will also rely on complex software that incorporates machine learning and artificial intelligence. These advanced software systems will need to process sensor data, make decisions, and send instructions around the vehicle in real-time. As a result, the various sub-systems and domains that make up an AV, from the electronics and software to the mechanical systems, will need to interact continuously as the vehicle operates to support this movement of information around the vehicle.
Even as vehicle complexity grows, companies must integrate all the advanced components and sub-systems required for an autonomous driving system into an all-electric vehicle platform while preserving sufficient drive range and performance characteristics. Some estimates place the drive range penalty of a self-driving system at about 15% due to the electrical power demands of the various sensors, actuators, and processing devices. Additional integration challenges involve ensuring the vehicle networks can support the data requirements of an AV, and the creation of an attractive vehicle body that hides the presence of cameras and other sensors without impacting their performance.
How digitalization helps overcome challenges
So, how can companies overcome the design challenges introduced by AVs, accounting for the hundreds of thousands of interactions that can occur within the vehicle’s sub-systems? And how do they understand the potential impacts of a design change throughout the entire product lifecycle, including into the manufacturing and supply chain ecosystems? It starts with a digital transformation of the vehicle design process. Digital transformation enables companies to adopt a new approach to vehicle development and engineering, linking their entire lifecycle through a digital backbone that enables information to flow throughout the organization. Even partner companies can be incorporated securely into the digital backbone, ensuring faster and easier collaboration between organizations, and supporting accountability to overall goals.

Key to this approach is a comprehensive digital twin that captures every aspect of the vehicle design and production. Using such a digital twin, automotive companies can remove the barriers between engineering teams from across the electrical, electronic, software and mechanical domains. This not only helps companies overcome the complexity of AVs, but also fosters a new culture of collaboration and innovation in the company that will carry it through the challenges of tomorrow.
Understanding the big picture
The first step in the design of a new AV is to describe the intended vehicle behavior, operational environment, and performance targets. In other words, the engineers must capture how the AV will work, how it will interact with the outside world, and the ecosystem into which the vehicle will fit. This description includes how various sub-systems within the vehicle will interact as well as relevant regulations, manufacturing capabilities, and the supply chain. For an AV, this even stretches to smart infrastructure around the vehicle – smart stoplights, city traffic management systems, and more.

This process results in a system-of-systems picture of the vehicle and its operating environment. To begin the design, this picture must be translated into a set of requirements and constraints that outline the design space, the constraints, and the capabilities the vehicle will need. Traditionally, teams have attempted to describe, cascade, and decompose these requirements throughout the organization using a document-based approach. But this approach will not scale with to meet the complexity of AVs.
Through digitalization, these requirements that codify the big-picture understanding of the design space can be integrated with the product lifecycle, enabling a structured and traceable process of decomposing requirements throughout the organization. The result is a clearer, more detailed picture at the top level of what the vehicle needs to do, how it should behave, what size it should be, what kind of performance metrics it needs to meet, and how various systems will interact. As this high-level description is decomposed, engineering teams obtain specific targets and constraints to guide the development of each component and sub-system.
Building the future of mobility through digitalization
Overcoming the vast complexity involved in nearly every aspect of AV design is proving to be one of the great challenges of the future of mobility. Traditional automotive design methodologies that rely on document-based requirements tracking and siloed engineering domains have fundamental shortcomings when dealing with such complexity.
A new approach to vehicle development is necessary. At the heart of this transformation is the concept of a comprehensive digital twin of the vehicle, covering every aspect of the vehicle and its environment, over its entire lifecycle. Such a digital twin becomes the backbone of product development − capable of delivering greater insight, reducing development cycle time, improving efficiency, and increasing market agility.