Hydrogen in sustainable aerospace design
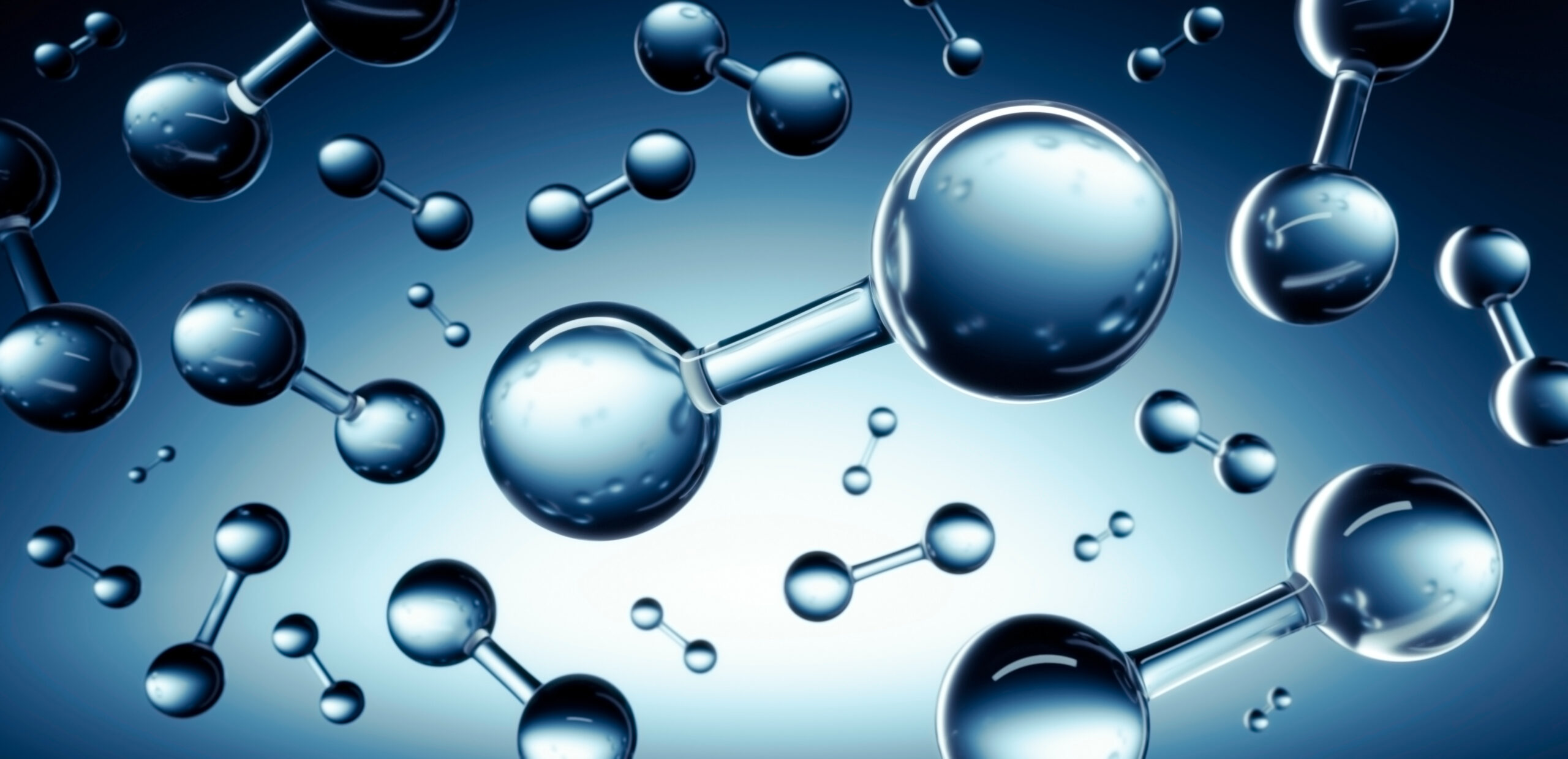
Zero emission aircraft need to be the future of the aerospace industry. Global carbon dioxide (CO2) emissions from planes peaked at 1Gt in 2019 according to the International Energy Agency (IEA). While that is only about five percent of all global emissions of that year, it is still a substantial contributor to climate change. Zero emission aircraft provide the image change for an evolving worldview on travel and a means to meet mounting regulation around the world to decarbonize.
The problem for aerospace companies is finding the right technologies to meet these new sustainability requirements. The automotive and energy industries are facing similar challenges and are deploying battery technology today to meet some of the demand. But aerospace necessitates a far lighter solution than what is possible with battery tech available now. Some small aircraft with short ranges can be battery electric but scaling to large international planes is essentially impossible. If it can be made sustainable, hydrogen might just be the solution the industry needs.
Hydrogen as energy storage
Hydrogen already has applications today, even as a fuel for transportation. One problem with deploying it in aerospace as a replacement for kerosene is the volume at which it can be produced sustainably. Green hydrogen is possible through electrolysis powered by renewable energy, but most of the world’s supply comes from steam methane reformation – essentially pulling free hydrogen from natural gas. Another major hurdle, for aerospace specifically is the storage and transportation of green hydrogen after it is produced. While it has an gravimetric energy density three times that of kerosene, the volumetric energy density requires high pressures and low temperatures to be feasible.
Engineering new aircraft for H2
Deploying hydrogen in aircraft presents myriad engineering challenges to aircraft design in addition to storage solutions, the most notable being propulsion systems and aircraft shape. Fortunately, digital solutions are making the resolution of the challenges easier to find. Propulsion for example, there are two general technologies a design could employ to convert the chemical potential energy of hydrogen into kinetic energy for flight – combustion or fuel cells. Combustion with H2 is similar to traditional kerosene, converting more energy rapidly but fuel cells can provide some of the flexibility of electric engines with their low weight and small size. Simulating many different propulsion configurations early on in development gives engineers a better understanding of the benefits and costs while committing far fewer resources than physical prototyping would.
The same goes for the overall shape of the aircraft in the shift to hydrogen. Traditionally, aircraft follow a tube and wing design where the liquid kerosene fuel is held in tanks throughout the aircraft. Unfortunately, the storage vessels for hydrogen can not fit in these same spaces as effectively – they are too large. Fitting enough H2 in a tube and wing design would require placing the storage vessel when passengers usually sit, but this reduces the effective carrying capacity and also throws off the center of gravity of the aircraft throughout the flight as fuel is depleted. The other option is to rethink the shape of an aircraft. Flying wings have been around in the experimental and military sectors for a while and may hold the key to commercial hydrogen aircraft, but finding the right balance requires rigorous testing just like for propulsion systems.
A product is not sustainable on its own
Even if an aircraft is zero emission from takeoff to landing, there are many other avenues for carbon emissions and environmental impact. As discussed at the top, the hydrogen fuel needs to be made sustainably or else the benefits of using a zero-emission fuel are negated even before the plane takes off. But there are also the material impacts of constructing and decommissioning an aircraft. Can the components be easily maintained to extend the life of the aircraft? Can the materials be recycled at the end of life? Are the environmental impacts from manufacturing verifiable from within the digital twin of the aircraft? These kinds of questions will be important to characterize in building the next generation of aircraft to be truly zero-emission.
To learn more about how Siemens is helping aerospace companies design the future of aviation, you may want to check out a recent article from Thierry Olbrechts, our Director of Simcenter Aerospace Industry Solutions at Siemens Digital Industries Software in Aerospace Manufacturing and Design
Siemens Digital Industries Software helps organizations of all sizes digitally transform using software, hardware and services from the Siemens Xcelerator business platform. Siemens’ software and the comprehensive digital twin enable companies to optimize their design, engineering and manufacturing processes to turn today’s ideas into the sustainable products of the future. From chips to entire systems, from product to process, across all industries. Siemens Digital Industries Software – Accelerating transformation.
For more information on Siemens Digital Industries Software products and services, follow us on LinkedIn, Twitter, Facebook and Instagram.