Convergence enables smart manufacturing and a digital twin for actionable data and performance
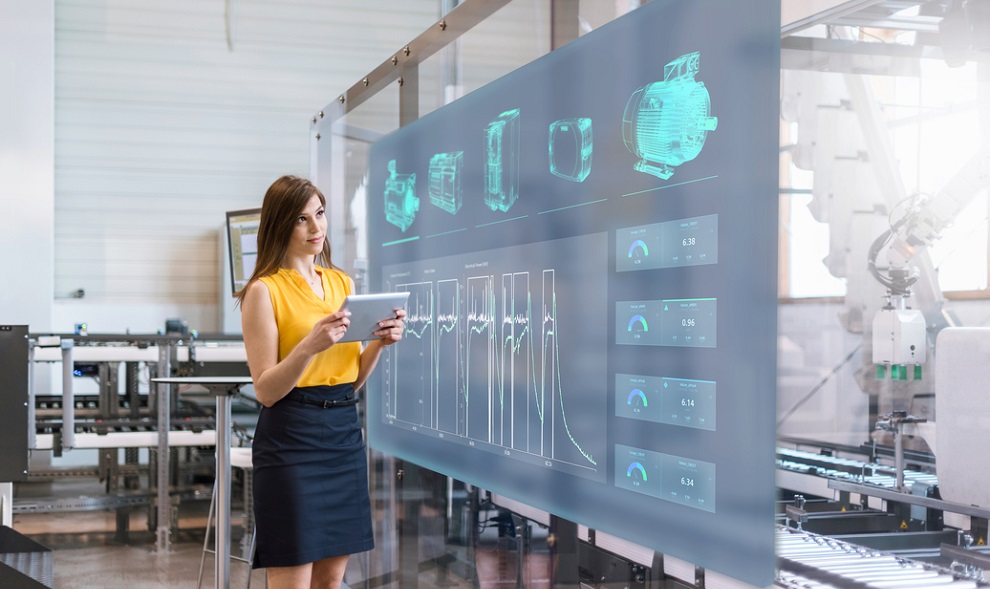
The industrial machinery industry faces several market hurdles, including global competition, low-cost providers, and customization. Additionally, other pertinent issues like disruption to the supply chain and labor shortages broadly impact the industry.
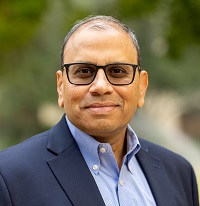
One of our experts in this industry, Rahul Garg, VP of Industrial Machinery and SMB Business Program at Siemens Digital Industries Software, in a podcast episode discusses the blurring lines of IT and OT technologies in a that is driving smart manufacturing.
Rahul elaborates on how manufacturers are overcoming these challenges in the industry by using the convergence of IT and OT to create a digital twin to address relevant issues, in addition to using the Siemens Industrial Edge initiative.
Operational efficiency in manufacturing
Improving operational efficiencies is essential to addressing current issues while finding alternative suppliers to determine the best way to set up products and manufacturing correctly and efficiently with operators. And remember that data is driving higher throughput and operating efficiencies. So, in most factory environments, it’s common to have a combination of older and newer equipment – the newer smart machines share data with a network while older machines are in silos. Subsequently, a network of sensors provides the data and brings it together cohesively.
Converging OT and IT
Information technology and operational technology are converging. So, operation technology (OT) is the factory’s capability or the operation’s software, physical equipment and the controls or technology driving the machines and PLCs. This software instructs the machine and ensures the hardware’s proficiencies. Information technology (IT) is the organization’s computer technology to store, retrieve, process, analyze, and act on the electronic information inside the operations.
Therefore, IT allows management to make decisions, while OT drives the actions in the factory. And they collaborate to achieve significant operational efficiencies. The result is the information flows more seamlessly – which is essential.
Operational technology capabilities monitor the factory floor operations, and capabilities like edge sensors stream data with a range of measurements that provides a sound knowledge of how the equipment performs. This information is captured on the factory floor during operations and fed into the IP systems. The result is the IP systems digitally optimize business decisions, analyzing data from the edge sensors on smart machines.
This environment creates an optimum view of equipment operations to make real-time decisions. Then these decisions assist in optimizing and maximizing throughput completed in the factories. Additionally, it provides knowledge of where machine parts might fail, run out of stock, or have issues that may hinder factory operations. This real-time knowledge allows for solid decision-making on rescheduling the shop floor, applying new support capabilities, or service technicians before the equipment fails. Thus, it creates an excellent environment to maximize and utilize factory operations effectively.
Convergence enables a digital twin
Subsequently, this data provides a valuable digital twin. And the digital twin (a virtual digital replica of physical objects, machines, manufacturing systems, or the entire shop floor) provides a virtual duplication of each machine while the factory operates. In turn, the IT and OT convergence offer real-time data and real-time information in the digital factory. So, the operational data ensures a higher fidelity virtual digital twin, equating to higher visibility of real-world operations. Therefore, it is possible to see how the digital twin performs while the real twin is doing its work.
OT/IT convergence and a digital twin provide access to actionable data. This data empowers improved decisions in an integrated manner to collaborate the planning, scheduling, and research regarding equipment performance. Additionally, it enables exceptional flexibility and visibility into operations, driving the ability to respond quickly to customer requirements and proactively understand and respond to customer needs. The result improves efficiency and ensures our goal: zero downtime, zero waste, and zero operational issues – the triple zero. Moreover, it maximizes throughputs to lower the global competition cost, improve sustainability, and minimize resource usage, electricity, and water waste.
Siemens Industrial Edge
Siemens Industrial Edge initiative is an essential ingredient in convergence, containing the following elements:
- Edge sensors are available to a broad group of users.
- Open ecosystems allow integration, networking with manufacturers, and information from other manufacturing environments.
- Security and policy management using edge systems, open ecosystem, and policy support.
Learn more in the audio podcast.
Software solutions
Siemens Digital Industries Software helps organizations of all sizes digitally transform using software, hardware and services from the Siemens Xcelerator business platform. Siemens’ software and the comprehensive digital twin enable companies to optimize their design, engineering and manufacturing processes to turn today’s ideas into the sustainable products of the future. From chips to entire systems, from product to process, across all industries. Siemens Digital Industries Software – Accelerating transformation.