Going digital and the wealth of opportunity in sustainable production
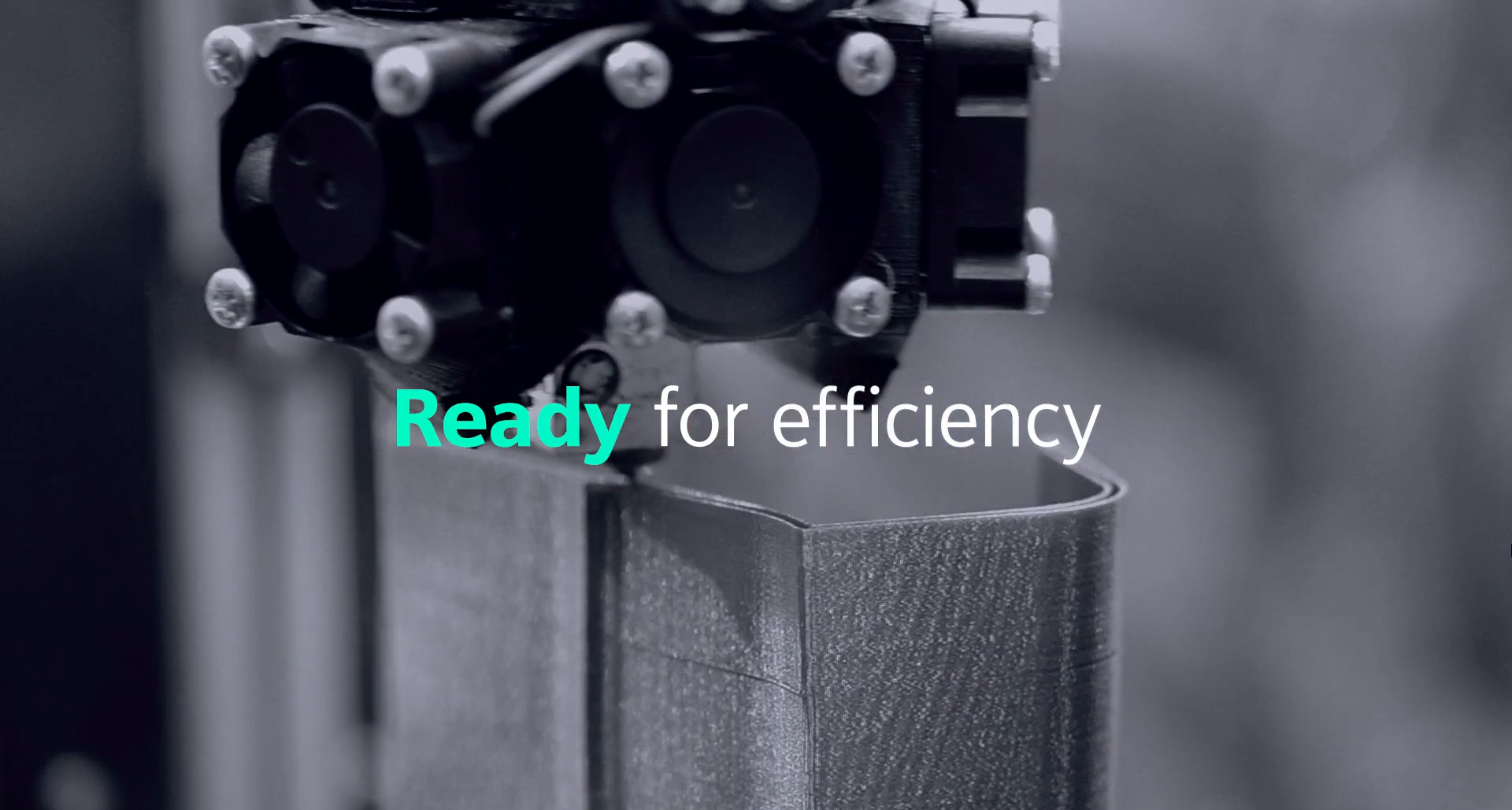
Efficiency and cost savings are nothing new to successful industrial production business, making something faster, with fewer materials, and at a lower cost is a large part of how then find their success. But the market is shifting for industries and business around the world to also account for the sustainability of their processes. Some see newly introduced regulation as a stick of sorts, others are chasing a changing value system of their customers, and more still see sustainability as a profit center in the years and decades to come.
However business are arriving at the decision to make production more sustainable, making it happen is a real challenge. They are adding a new set of metrics by which they optimize their processes, adding further complexity to already complicated workflows. Those additions could be expanded data sets on machine or process performance, plant-level optimizations to improve efficiency at scale, or supplier information to understand the extended scope of sustainability impacts. All of the businesses trying to tackle this new reality are turning to digitalization to help them streamline the process – with the digital twin and collective intelligence.
For a complete story on the value of the digital twin on sustainable production, our Head of Sustainability at Siemens Digital Industries – Eryn Devola – was recently published in Machine Design talking about this exact transition. But you can continue reading here for a quick overview of the four phases businesses are focusing on today:
- Energy use
- Flexible production and innovation
- Service engineering
- Production line planning and optimization
Each of these paths toward sustainability is important to a business, but possibly more important is to understand that they do not all have to be done at the same time. Some could be considered low hanging fruit because of the existing processes and engineering work established in previous projects while others might be great first steps for a company just starting out. It is a common idea in sustainability, regardless of the application, the best solution is really a set of possibilities and finding the right ones for your business is in itself a first step in the journey.
Energy use
But a fairly common first step for a manufacturer is to look at energy use in the factory. Because it already has a direct associated cost to operations, many businesses are already optimizing their energy use. Certain regions may feel this more pressure more than others depending on the reliability of power or growing costs associated with keeping it flowing. On top of the almost instant cost reductions in improving the energy efficiency of machines, it also reduces the associated carbon footprint of purchasing that energy.
Flexible production and innovation
For a company just starting off or pivoting to a new market and product category, flexible production might be the right first step to establish sustainable production processes. That might mean purchasing modular systems for production or going all the way to lot sizes of one with additive manufacturing. In either case, having a digital twin of the facility, product, and process will be important in optimizing the material and workflows of the facility while enabling change-overs first in the digital environment, then the physical.
Service engineering
Providing quality products from the factory is a long-held driver for many businesses, but making the established goals for a sustainable business will also require maintaining that quality for more of the product’s lifetime. That goes for both manufacturers and machine manufacturers. Replacing a product or machine can be an expensive proposition, both financially and materially. Offering preventative maintenance and replacement parts can create a longer lasting relationship between customer and manufacturer while also meeting sustainability targets because less material is being devoted to functioning systems.
Planning and optimizing production systems
The real bread and butter of sustainable production however is optimizing existing systems in the digital world, from data collected in simulation models and real-world data acquisition. The cost of machines, energy, and design changes are high, so making sure a factory floor is running as efficiently as possible is crucial in recuperating the improvement costs. The digital twin can help continuously improve existing systems with these data streams across manufacturing lines, factories, and entire enterprises.
Only the surface of sustainable production
Much like any competency, production sustainability is a deep well of knowledge and possibility and I have only pierced the surface of what can be learned and wielded. To learn more about how we have already helped some of our industrial customers start their sustainability journey, the Machine Design article provides a great high-level discussion. And to delve even deeper our website is a fantastic resource to research not only sustainable production, but also design processes, the role of logistics and supplier networks, the partnerships to make it all possible, and much more.
Siemens Digital Industries Software helps organizations of all sizes digitally transform using software, hardware and services from the Siemens Xcelerator business platform. Siemens’ software and the comprehensive digital twin enable companies to optimize their design, engineering and manufacturing processes to turn today’s ideas into the sustainable products of the future. From chips to entire systems, from product to process, across all industries. Siemens Digital Industries Software – Accelerating transformation.
For more information on Siemens Digital Industries Software products and services, follow us on LinkedIn, Twitter, Facebook and Instagram.
Comments
Leave a Reply
You must be logged in to post a comment.
According to my knowledge Digital technologies enable businesses to optimize processes, reduce waste, and minimize resource consumption. For instance, using data analytics can help identify inefficiencies in production, leading to better resource management and reduced greenhouse gas emissions. Companies that integrate sustainability into their core operations and leverage digital technologies to drive positive impact are better positioned to thrive in a rapidly evolving and environmentally conscious market.