Powering off-highway vehicles through electrification
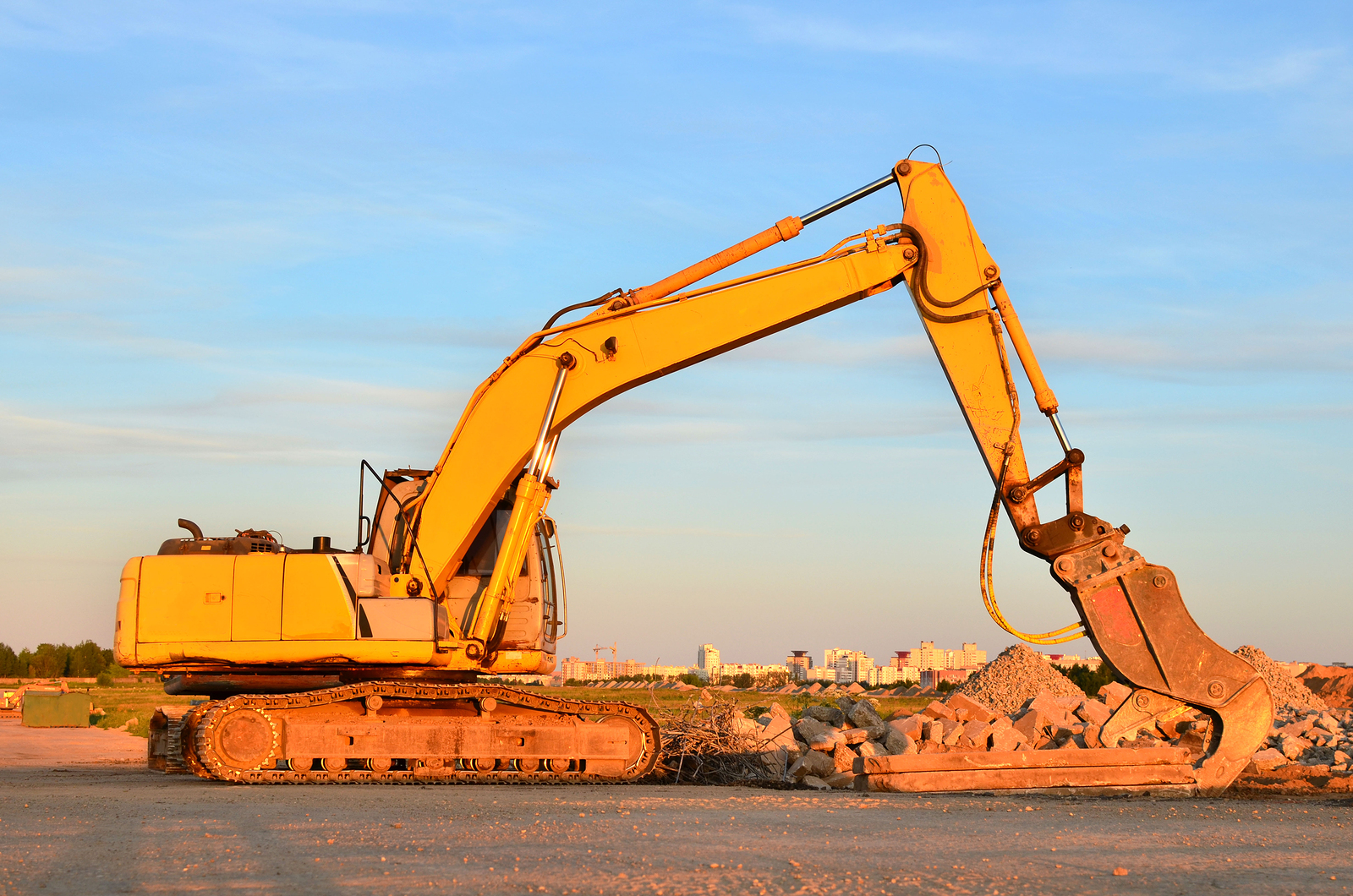
Modern priorities, such as sustainability and clean transportation are steering automotive companies away from fossil-fueled vehicles and toward an electrified future. Over the last decade, the electrification of cars has made significant progress due to improvements in battery life, motor function and overall public interest, particularly as electric vehicles (EVs) have come to rival the performance and capabilities of internal combustion vehicles. The advancement of electrified mobility in the consumer space is opening new opportunities for the electrification of other types of vehicles. This includes the field of off-highway vehicles (OHVs), which we rely on in construction, agriculture, mining, and even for recreation.
The benefits of electrifying OHVs
Building a sustainable future for transportation will require a combination of technologies applied at scale across all forms of powered mobility. So far, the consumer side of the automotive and transportation business has been at the front of electrification. 2024 looks to continue this trend as several dozen new EVs are expected to hit the market from both startup companies and major automotive brands. As the consumer space takes the lead it also demonstrates the real-world viability and benefits of modern battery and electric motor technology.
EVs now offer competitive driving ranges between charges, compelling performance and driving characteristics, and produce much less noise and no emissions as they drive. Through electrification, OHVs can harness these and other benefits. In a recent article, EDAC Inc., a maker of electrical connectors, posited a number of additional advantages to the electrification of OHVs.
First, electrified powertrains contain fewer mechanical failure points than internal combustion engines and associated transmissions and drive linkages. Electric motors feature essentially one moving part, that being the rotor which is spun by magnetic forces to deliver power to the wheel. Modern EVs also place electric motors directly at each driven wheel, virtually eliminating the mechanical linkages present in a traditional drivetrain, and do not require a multi-speed gearbox to deliver maximum torque to the wheels. On the whole, this means electrified transportation should have fewer mechanical failures that can be difficult and costly to repair in the field.
EDAC also suggests that the precise torque control of electric motors can help reduce wear and optimize the expenditure of energy to complete a task. As mentioned above, and electrified OHV will likely also have independent motors at each driven wheel or actuation point. This arraignment enables precise control over where and how power is delivered throughout the vehicle. When coupled with advanced control systems, this can give operators greater control over the vehicle, making it easier to complete their jobs efficiently and safely.
Finally, the lack of tailpipe emissions from an electrified OHV can contribute to both a reduction in the overall environmental footprint of our transportation systems and to safer and healthier environments for operators, workers, and other people in the immediate vicinity. This may be particularly beneficial in enclosed environments like underground mines, where air quality can be a major challenge.
Some challenges OHVs face
The conditions in which OHVs often operate also make electrification difficult. Creating EVs for standard road use is already a formidable challenge, and this complexity is only magnified when engineering vehicles to operate reliably in extreme environments. EDAC identifies a few key challenges created by the often dirty, hot, wet, and remote operational conditions experienced by OHVs:
- OHVs are expected to operate reliably and efficiently in a wide range of temperatures, from the dry heat of the desert to the humidity of swamps and jungles, to the bitter cold and everything in between. Extreme temperatures can reduce the state of charge of a vehicle battery as more energy is diverted to keep both the battery and human occupants at comfortable temperatures.
- OHVs frequently encounter intense shocks and vibrations from uneven driving surfaces and the nature of their tasks. Vibrations and shocks can pry components loose or cause other damage to components both electrical and mechanical.
- Finally, these vehicles must meet even higher standards of reliability and longevity than consumer EVs. Many OHVs are used in commercial applications where breakdowns are uniquely costly due to the downtime of critical equipment that can lead to further delays and cost overruns. These vehicles are also expected to remain in service for decades to deliver sufficient value to their owners and operators.
The electrification of OHVs aims to expand the future of a more connected, optimized and sustainable approach to mobility across a wider range of vehicle types. But challenges abound in electrifying OHVs due in large part to the rugged operating conditions in which they are used. Engineers will need to tackle familiar challenges, such as heat management and reliability, in new ways due to the extreme operating conditions common for OHVs. While these obstacles are considerable, overcoming them will play a crucial role in shaping a smarter and more sustainable future for the automotive industry.